Die physikalische Gasphasenabscheidung (PVD) ist ein Beschichtungsverfahren, mit dem dünne Materialschichten auf ein Substrat aufgebracht werden.Die Kosten für PVD können je nach Art des PVD-Verfahrens, der verwendeten Materialien, des Produktionsumfangs und der Komplexität der zu beschichtenden Teile erheblich variieren.Nachstehend finden Sie eine detaillierte Aufschlüsselung der wichtigsten Faktoren, die die PVD-Kosten beeinflussen, sowie eine Erläuterung der einzelnen Faktoren.
Die wichtigsten Punkte werden erklärt:
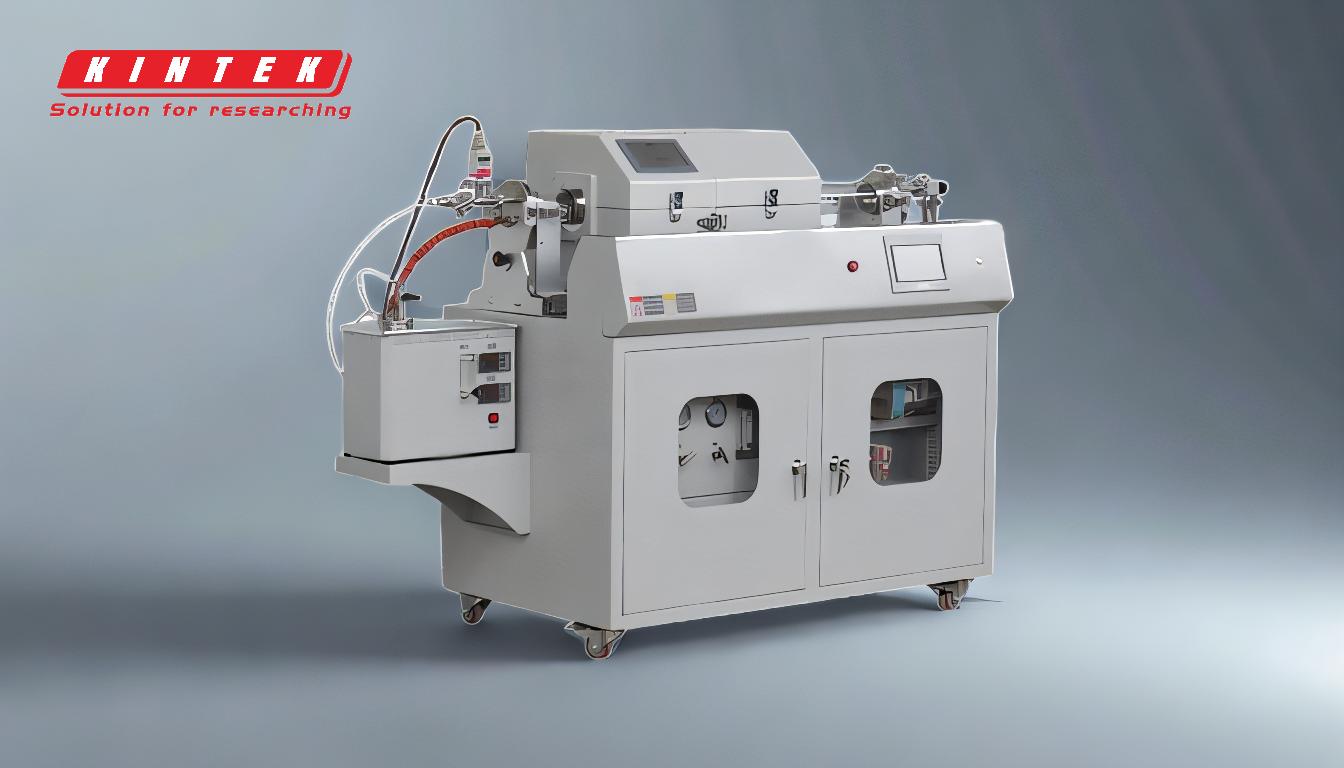
-
Art des PVD-Verfahrens:
- PVD umfasst verschiedene Techniken wie Sputtern, Verdampfen und Lichtbogenabscheidung.Jedes Verfahren hat unterschiedliche Anforderungen an die Ausrüstung, die Komplexität des Betriebs und die Effizienz der Materialnutzung, was sich direkt auf die Kosten auswirkt.
- So ist beispielsweise das Sputtern oft teurer, da Hochvakuumbedingungen und spezielle Targets erforderlich sind, während die Verdampfung zwar billiger, aber weniger vielseitig ist.
-
Verwendete Materialien:
- Die Kosten des Zielmaterials (z. B. Titan, Gold oder Aluminium) beeinflussen die PVD-Gesamtkosten erheblich.Edelmetalle wie Gold sind teurer, während gewöhnliche Metalle wie Aluminium relativ günstig sind.
- Auch der Reinheitsgrad und die Form des Materials (z. B. Pellets, Drähte oder Targets) können die Kosten beeinflussen.
-
Umfang der Produktion:
- Größenvorteile spielen eine entscheidende Rolle.Bei großen Produktionsläufen sinken die Kosten pro Stück, da sich die Fixkosten (z. B. für die Einrichtung und Wartung der Anlagen) über eine größere Anzahl von Teilen amortisieren.
- Kleinere oder kundenspezifische Aufträge hingegen sind aufgrund höherer Rüstkosten und eines geringeren Durchsatzes tendenziell teurer pro Stück.
-
Komplexität der Teile:
- Die Geometrie und Größe der zu beschichtenden Teile beeinflussen die Kosten.Komplexe Formen oder große Teile können spezielle Vorrichtungen, längere Bearbeitungszeiten oder mehrere Beschichtungszyklen erfordern, was die Kosten erhöht.
- Die Anforderungen an die Oberflächenvorbereitung (z. B. Reinigen, Polieren) erhöhen ebenfalls die Gesamtkosten.
-
Kosten für Ausrüstung und Wartung:
- PVD-Anlagen sind kapitalintensiv und haben hohe Anfangsinvestitionskosten.Die Wartung, einschließlich des regelmäßigen Austauschs von Verbrauchsmaterialien wie Targets und Vakuumpumpenölen, erhöht die Betriebskosten.
- Fortgeschrittene PVD-Systeme mit Automatisierung oder erweiterten Möglichkeiten (z. B. Mehrschichtbeschichtungen) sind im Betrieb teurer.
-
Energie- und Arbeitskosten:
- PVD-Verfahren erfordern einen beträchtlichen Energieaufwand, insbesondere für die Aufrechterhaltung von Hochvakuumbedingungen und die Versorgung der Abscheidungsquellen.Die Energiekosten variieren je nach Region und können sich auf die Gesamtkosten auswirken.
- Für den Betrieb, die Wartung und die Qualitätskontrolle sind qualifizierte Arbeitskräfte erforderlich, was zu den Arbeitskosten beiträgt.
-
Qualität und Schichtdicke der Beschichtung:
- Dickere oder mehrschichtige Beschichtungen erfordern mehr Material und längere Bearbeitungszeiten, was die Kosten erhöht.
- Hochwertige Beschichtungen mit strengen Leistungsanforderungen (z. B. Verschleißfestigkeit, Korrosionsbeständigkeit) können zusätzliche Schritte wie Vorbehandlung oder Nachbehandlung erfordern, was die Kosten weiter erhöht.
-
Markt und geografische Faktoren:
- Regionale Unterschiede bei den Lohnkosten, der Materialverfügbarkeit und den Energiekosten können die PVD-Preise beeinflussen.
- Auch die Marktnachfrage nach bestimmten PVD-Dienstleistungen oder -Materialien kann die Kosten nach oben oder unten treiben.
Zusammenfassend lässt sich sagen, dass die Kosten für PVD durch eine Kombination von Faktoren beeinflusst werden, darunter die Art des Verfahrens, die Materialien, der Produktionsumfang, die Komplexität der Teile, die Ausrüstung, die Arbeitskräfte und die Marktbedingungen.Das Verständnis dieser Faktoren kann Einkäufern helfen, fundierte Entscheidungen zu treffen und die Kosten für ihre spezifischen Anforderungen zu optimieren.
Zusammenfassende Tabelle:
Faktor | Einfluss auf die Kosten |
---|---|
Art des PVD-Verfahrens | Sputtern ist wegen des erforderlichen Hochvakuums kostspielig; Verdampfen ist billiger, aber weniger vielseitig. |
Verwendete Materialien | Edelmetalle (z. B. Gold) sind teuer, gewöhnliche Metalle (z. B. Aluminium) sind erschwinglich. |
Maßstab der Produktion | Ein großer Maßstab senkt die Kosten pro Einheit; ein kleiner Maßstab erhöht die Kosten pro Einheit. |
Komplexität der Teile | Komplexe Formen oder große Teile erfordern spezielle Vorrichtungen, was die Kosten erhöht. |
Ausrüstung und Wartung | Hohe Anfangsinvestitionen und laufende Wartungskosten. |
Energie- und Arbeitskosten | Ein erheblicher Energieaufwand und qualifizierte Arbeitskräfte tragen zu den Kosten bei. |
Qualität und Schichtdicke | Dickere oder mehrschichtige Beschichtungen erfordern mehr Material und Zeit, was die Kosten erhöht. |
Markt und geografische Faktoren | Regionale Lohnkosten, Materialverfügbarkeit und Energiekosten beeinflussen die Preisgestaltung. |
Sind Sie bereit, Ihre PVD-Beschichtungskosten zu optimieren? Kontaktieren Sie noch heute unsere Experten für maßgeschneiderte Lösungen!