CVD (Chemical Vapor Deposition) und PVD (Physical Vapor Deposition) sind zwei weit verbreitete Verfahren zur Abscheidung von Dünnschichten, die jeweils unterschiedliche Prozesse, Mechanismen und Anwendungen aufweisen.Der Hauptunterschied liegt darin, wie das Material auf das Substrat aufgebracht wird.CVD beruht auf chemischen Reaktionen zwischen gasförmigen Ausgangsstoffen und dem Substrat, was zu einer dichten, gleichmäßigen Beschichtung führt.Im Gegensatz dazu werden bei der PVD feste Materialien physikalisch verdampft und kondensieren dann auf dem Substrat in Sichtlinie.Diese Unterschiede führen zu Schwankungen bei den Betriebstemperaturen, den Abscheideraten, der Schichtqualität und der Eignung für bestimmte Anwendungen.CVD wird häufig für Hochtemperaturverfahren und Anwendungen bevorzugt, die dichte, gleichmäßige Schichten erfordern, während PVD für Niedrigtemperaturverfahren und Anwendungen, die glatte, gut haftende Schichten erfordern, bevorzugt wird.
Die wichtigsten Punkte erklärt:
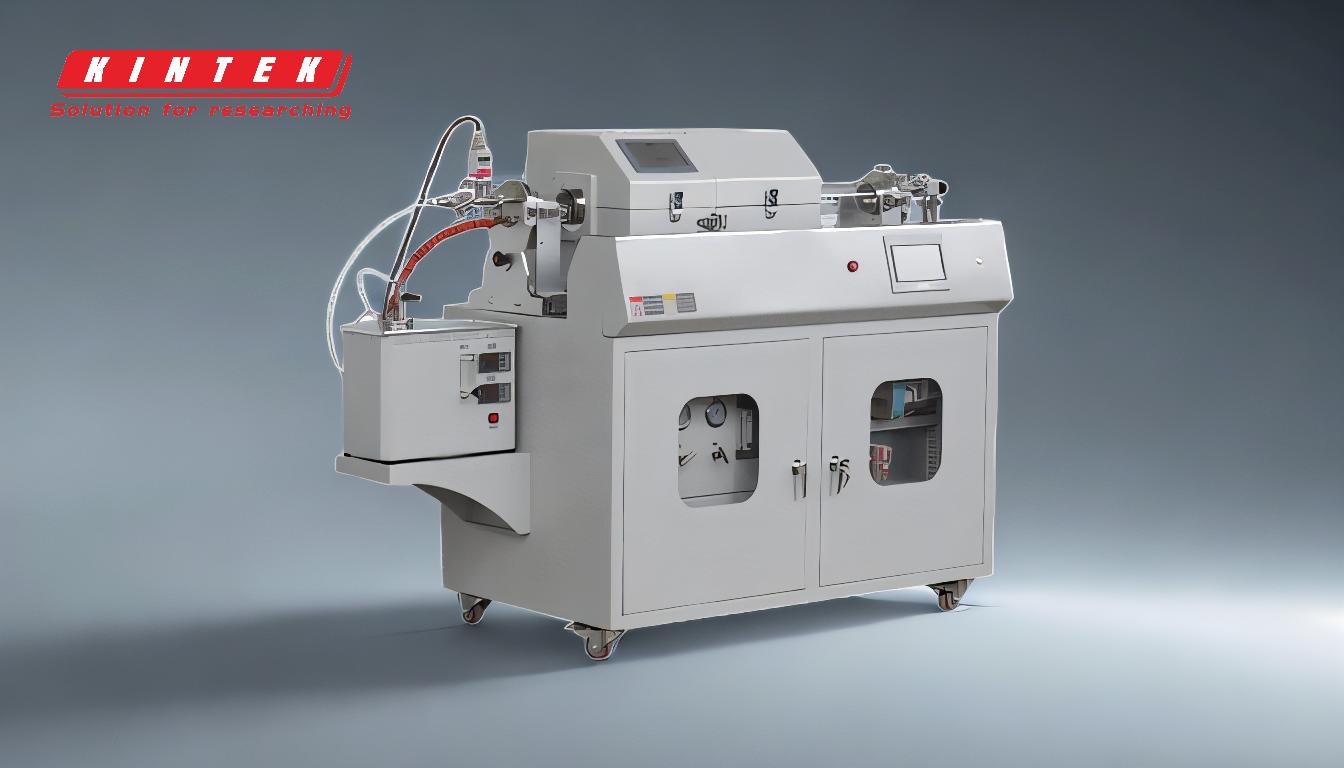
-
Mechanismus der Ablagerung:
- CVD:Es handelt sich um chemische Reaktionen zwischen gasförmigen Vorläufern und dem Substrat.Das Verfahren erfordert in der Regel hohe Temperaturen zur Aktivierung der chemischen Reaktionen, die zur Bildung einer festen Beschichtung führen.Die Abscheidung erfolgt multidirektional, so dass selbst bei komplexen Geometrien eine gleichmäßige Beschichtung möglich ist.
- PVD:Basiert auf physikalischen Prozessen wie Sputtern oder Verdampfen, um feste Materialien zu verdampfen.Das verdampfte Material kondensiert dann auf dem Substrat in der Sichtlinie.Dieses Verfahren kommt ohne chemische Reaktionen aus und arbeitet im Vergleich zur CVD oft mit niedrigeren Temperaturen.
-
Betriebstemperaturen:
- CVD:Erfordert im Allgemeinen hohe Temperaturen (450°C bis 1050°C), um chemische Reaktionen zu erleichtern.Dies kann die Arten von Substraten, die verwendet werden können, einschränken, da sich einige Materialien bei diesen Temperaturen zersetzen können.
- PVD:Funktioniert bei niedrigeren Temperaturen (250°C bis 450°C) und eignet sich daher für temperaturempfindliche Substrate.Dies ist ein bedeutender Vorteil für Anwendungen mit Materialien, die keine große Hitze vertragen.
-
Abscheidungsrate:
- CVD:Im Vergleich zum PVD-Verfahren werden in der Regel höhere Abscheideraten erzielt, was es für bestimmte Anwendungen effizienter macht.Allerdings kann das Verfahren langsamer sein, da chemische Reaktionen stattfinden müssen.
- PVD:Im Allgemeinen sind die Abscheideraten niedriger, aber durch Weiterentwicklungen wie EBPVD (Electron Beam Physical Vapor Deposition) können hohe Raten (0,1 bis 100 μm/min) bei relativ niedrigen Temperaturen erreicht werden.
-
Schichtqualität und Eigenschaften:
- CVD:Erzeugt dichte, gleichmäßige Beschichtungen mit hervorragender Deckkraft, auch auf komplexen Geometrien.Die Filme haben in der Regel eine hohe Dichte und gute Haftung, so dass sie sich für Anwendungen eignen, die robuste, langlebige Beschichtungen erfordern.
- PVD:Die Schichten können eine glattere Oberfläche und bessere Haftung aufweisen, sind aber im Vergleich zu CVD-Beschichtungen oft weniger dicht und gleichmäßig.PVD wird für Anwendungen bevorzugt, bei denen Oberflächengüte und Haftung entscheidend sind.
-
Material Bereich:
- CVD:Hauptsächlich für die Abscheidung von Metallen, Halbleitern und Keramiken verwendet.Das Verfahren eignet sich gut für die Herstellung hochreiner Schichten mit spezifischen chemischen Zusammensetzungen.
- PVD:Es kann ein breiteres Spektrum an Materialien abgeschieden werden, darunter Metalle, Legierungen und Keramiken.Diese Vielseitigkeit macht PVD für eine Vielzahl von Anwendungen geeignet.
-
Anwendungen:
- CVD:Wird in der Halbleiterindustrie häufig zur Herstellung dünner Schichten auf Siliziumwafern sowie zur Herstellung von Beschichtungen für Schneidwerkzeuge, verschleißfeste Oberflächen und optische Komponenten verwendet.
- PVD:Weit verbreitet bei der Herstellung von dekorativen Beschichtungen, harten Beschichtungen für Schneidwerkzeuge und dünnen Schichten für elektronische Geräte.Aufgrund der niedrigeren Betriebstemperatur ist es ideal für Beschichtungen auf Kunststoffen und anderen temperaturempfindlichen Materialien.
-
Produktions-Effizienz:
- CVD:Kann für die Produktion großer Mengen weniger effizient sein, da hohe Temperaturen und chemische Reaktionen erforderlich sind.Es ist jedoch sehr effektiv für Anwendungen, die eine genaue Kontrolle über die Filmzusammensetzung und -eigenschaften erfordern.
- PVD:Dieses Verfahren wird häufig für die Großserienproduktion bevorzugt, da es die Möglichkeit bietet, schnell Schichten auf große Substratflächen aufzubringen.Das Verfahren ist auch materialeffizienter und ermöglicht eine hohe Ausnutzung des Beschichtungsmaterials.
Zusammenfassend lässt sich sagen, dass die Wahl zwischen CVD und PVD von den spezifischen Anforderungen der Anwendung abhängt, einschließlich der gewünschten Schichteigenschaften, des Substratmaterials und des Produktionsvolumens.Jedes Verfahren hat seine Stärken und Grenzen und eignet sich daher für unterschiedliche industrielle und wissenschaftliche Anwendungen.
Zusammenfassende Tabelle:
Blickwinkel | CVD | PVD |
---|---|---|
Mechanismus der Abscheidung | Chemische Reaktionen zwischen gasförmigen Vorläufern und Substrat | Physikalische Verdampfung von Feststoffen, Kondensation auf dem Substrat |
Betriebstemperatur | Hoch (450°C bis 1050°C) | Niedrig (250°C bis 450°C) |
Abscheidungsrate | Höhere Raten, aber aufgrund von chemischen Reaktionen langsamer | Niedrigere Raten, aber Fortschritte wie EBPVD erreichen hohe Raten |
Filmqualität | Dichte, gleichmäßige Beschichtungen mit ausgezeichneter Deckkraft | Glattere Oberflächen, bessere Haftung, aber weniger dicht und gleichmäßig |
Material Bereich | Metalle, Halbleiter, Keramiken | Metalle, Legierungen, Keramiken |
Anwendungen | Halbleiter, Schneidwerkzeuge, verschleißfeste Oberflächen, optische Beschichtungen | Dekorative Beschichtungen, Hartbeschichtungen, dünne Schichten für die Elektronik |
Produktionseffizienz | Weniger effizient für die Großserienproduktion | Effizienter für die Großserienproduktion |
Benötigen Sie Hilfe bei der Entscheidung zwischen CVD und PVD für Ihre Anwendung? Kontaktieren Sie noch heute unsere Experten für maßgeschneiderte Lösungen!