Die Verweilzeit ist ein kritischer Faktor bei der Pyrolyse, der den Grad der thermischen Umwandlung, die Produktverteilung und die Zusammensetzung des entstehenden Bioöls, der Holzkohle und des Pyrolysegases erheblich beeinflusst. Längere Verweilzeiten verbessern im Allgemeinen den Abbau organischer Materialien, was zu einer vollständigeren thermischen Zersetzung und einer höheren Ausbeute an nicht kondensierbaren Gasen führt. Umgekehrt können kürzere Verweilzeiten die Produktion von hochwertigen festen Produkten wie Holzkohle begünstigen. Die optimale Verweilzeit hängt von den Eigenschaften des Ausgangsmaterials, dem Reaktortyp und den gewünschten Produktergebnissen ab. Das Verständnis und die Kontrolle der Verweilzeit sind für die Optimierung der Pyrolyseeffizienz und das Erreichen des gewünschten Gleichgewichts zwischen Produktausbeute und -qualität von entscheidender Bedeutung.
Die wichtigsten Punkte werden erklärt:
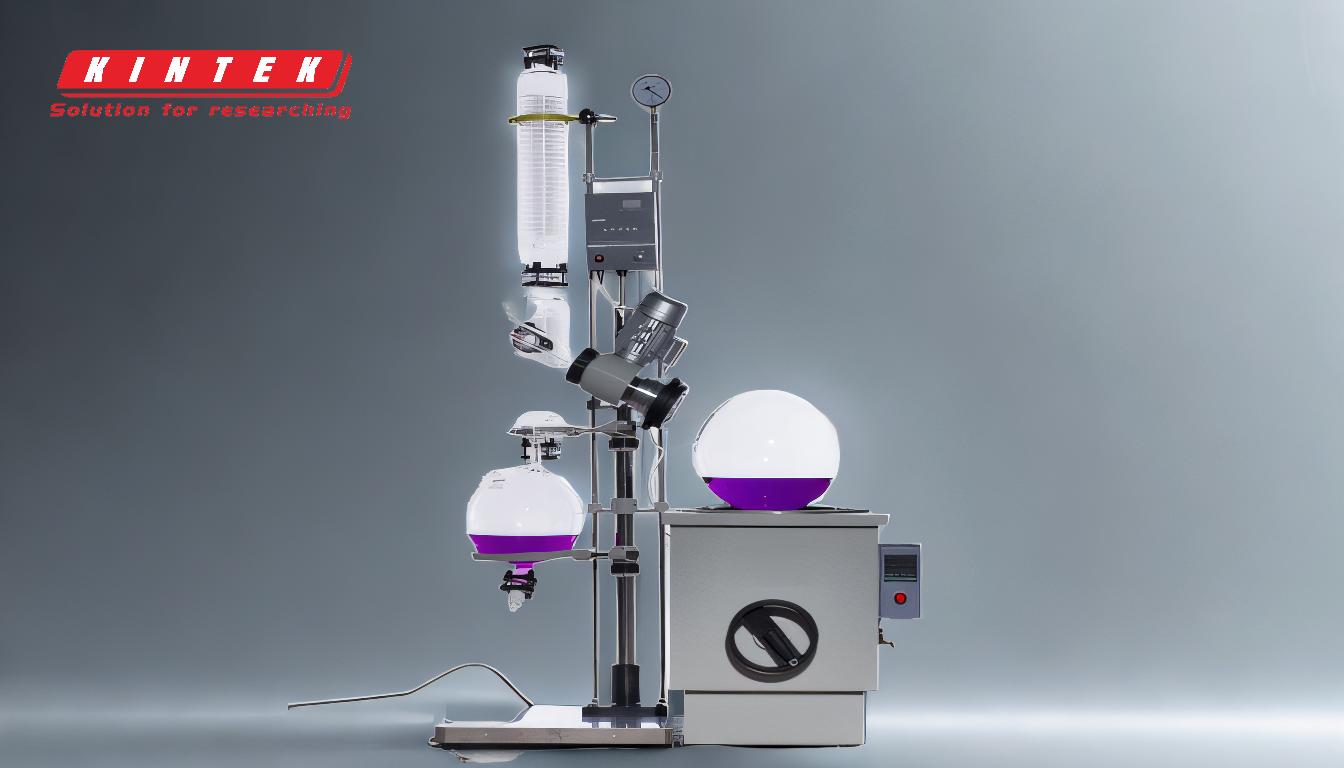
-
Definition und Bedeutung der Aufenthaltsdauer:
- Die Verweilzeit bezieht sich auf die Dauer des Verbleibs des Einsatzmaterials im Pyrolysereaktor unter thermischer Behandlung.
- Sie ist ein Schlüsselparameter, der sich direkt auf den Umfang der thermischen Zersetzung und die Verteilung der Pyrolyseprodukte (Bioöl, Holzkohle und Gas) auswirkt.
-
Auswirkungen auf die thermische Umwandlung:
- Längere Verweilzeiten ermöglichen eine vollständigere thermische Zersetzung des Ausgangsmaterials, was zu höheren Umwandlungsgraden führt.
- Dies führt zu einer erhöhten Produktion nicht kondensierbarer Gase, da organische Materialien mehr Zeit haben, sich in kleinere Moleküle zu zersetzen.
-
Auswirkungen auf den Produktvertrieb:
- Bio-Öl: Längere Verweilzeiten können die Ausbeute an Bioöl aufgrund von sekundären Crackreaktionen, die flüssige Produkte in Gase umwandeln, verringern.
- Char: Kürzere Verweilzeiten begünstigen die Bildung von Holzkohle, da sich das Einsatzmaterial nicht vollständig in Gase oder Flüssigkeiten zersetzt.
- Pyrolytisches Gas: Längere Verweilzeiten erhöhen die Gasausbeute, da mehr organisches Material in gasförmige Produkte umgewandelt wird.
-
Einfluss auf die Produktzusammensetzung:
- Die Verweilzeit beeinflusst die Zusammensetzung der Dämpfe und die Qualität der Endprodukte.
- Längere Verweilzeiten können beispielsweise zur Produktion leichterer Kohlenwasserstoffe und wasserstoffreicher Gase führen, während bei kürzeren Zeiten schwerere organische Verbindungen im Bioöl erhalten bleiben können.
-
Wechselwirkung mit anderen Pyrolyseparametern:
- Die Verweilzeit steht in Wechselwirkung mit Faktoren wie Temperatur, Heizrate und Eigenschaften des Ausgangsmaterials, um das Gesamtergebnis der Pyrolyse zu bestimmen.
- So können beispielsweise höhere Temperaturen in Verbindung mit längeren Verweilzeiten die Gasproduktion maximieren, während niedrigere Temperaturen mit kürzeren Verweilzeiten die Holzkohleausbeute optimieren können.
-
Abhängigkeit von Rohstoffen:
- Die optimale Verweilzeit hängt von der Art des Ausgangsmaterials (z. B. Biomasse, Reifen, Kunststoffe) und dessen Eigenschaften (z. B. Feuchtigkeitsgehalt, Partikelgröße) ab.
- So kann beispielsweise Biomasse mit hohem Feuchtigkeitsgehalt längere Verweilzeiten erfordern, um eine vollständige Trocknung und Zersetzung zu gewährleisten.
-
Überlegungen zur Reaktorkonstruktion:
- Verschiedene Reaktortypen (z. B. Wirbelschicht, Festbett) haben unterschiedliche Möglichkeiten zur Steuerung der Verweilzeit.
- Das Reaktordesign muss die gewünschte Verweilzeit berücksichtigen, um die angestrebte Produktverteilung und -qualität zu erreichen.
-
Praktische Auswirkungen für Käufer:
- Das Wissen um die Auswirkungen der Verweilzeit hilft den Käufern, die richtige Pyrolyseanlage und die richtigen Betriebsbedingungen für ihre spezifischen Anforderungen auszuwählen.
- Wenn beispielsweise das Ziel darin besteht, die Bioölproduktion zu maximieren, sind Anlagen mit einer präzisen Steuerung von Verweilzeit und Temperatur unerlässlich.
Durch eine sorgfältige Steuerung der Verweilzeit können die Betreiber der Pyrolyse den Prozess optimieren, um die gewünschte Ausgewogenheit von Produktausbeute und -qualität zu erreichen, was sie zu einem entscheidenden Faktor bei der Auswahl der Anlagen und der Prozessgestaltung macht.
Zusammenfassende Tabelle:
Aspekt | Auswirkungen der Aufenthaltsdauer |
---|---|
Thermische Umwandlung | Längere Zeiten verbessern die Zersetzung und erhöhen die Ausbeute an nicht kondensierbaren Gasen. |
Bio-Öl-Ausbeute | Längere Zeiten reduzieren das Bioöl aufgrund von sekundären Crackreaktionen. |
Saiblingsproduktion | Kürzere Zeiten begünstigen die Bildung von Holzkohle, da das Ausgangsmaterial nicht vollständig zersetzt wird. |
Pyrolytische Gasausbeute | Längere Zeiten erhöhen die Gasproduktion, da mehr organisches Material in Gas umgewandelt wird. |
Zusammensetzung des Produkts | Bei längeren Zeiten entstehen leichtere Kohlenwasserstoffe, bei kürzeren Zeiten bleiben schwerere Verbindungen erhalten. |
Abhängigkeit von Rohstoffen | Der optimale Zeitpunkt variiert je nach Art des Ausgangsmaterials (z. B. Biomasse, Kunststoffe) und dessen Eigenschaften. |
Reaktorentwurf | Der Reaktortyp (z. B. Wirbelschicht) muss auf die gewünschte Verweilzeit abgestimmt sein, um optimale Ergebnisse zu erzielen. |
Sind Sie bereit, Ihren Pyrolyseprozess zu optimieren? Kontaktieren Sie uns heute für fachkundige Beratung und maßgeschneiderte Lösungen!