Das Sintern von Keramik ist ein entscheidender Prozess bei der Herstellung von keramischen Gegenständen, bei dem pulverförmige Werkstoffe durch die Anwendung von Wärme und manchmal zusätzlichen Kräften wie Druck oder elektrischen Strömen in eine dichte, zusammenhängende Struktur umgewandelt werden.Das Verfahren umfasst in der Regel mehrere Stufen: Vorbereitung des Pulverpresslings, Erhitzen auf hohe Temperaturen, um die Partikel zu verbinden und zu verdichten, und Abkühlen, um das Material zu verfestigen.Dieses Verfahren verringert die Porosität, bewirkt eine Schrumpfung und verbessert die mechanischen Eigenschaften der Keramik.Der Sinterprozess kann je nach den spezifischen Materialien und den gewünschten Ergebnissen variieren, umfasst aber im Allgemeinen Schritte wie Pressen, Erhitzen und manchmal eine Bearbeitung oder Montage nach dem Sintern.
Die wichtigsten Punkte werden erklärt:
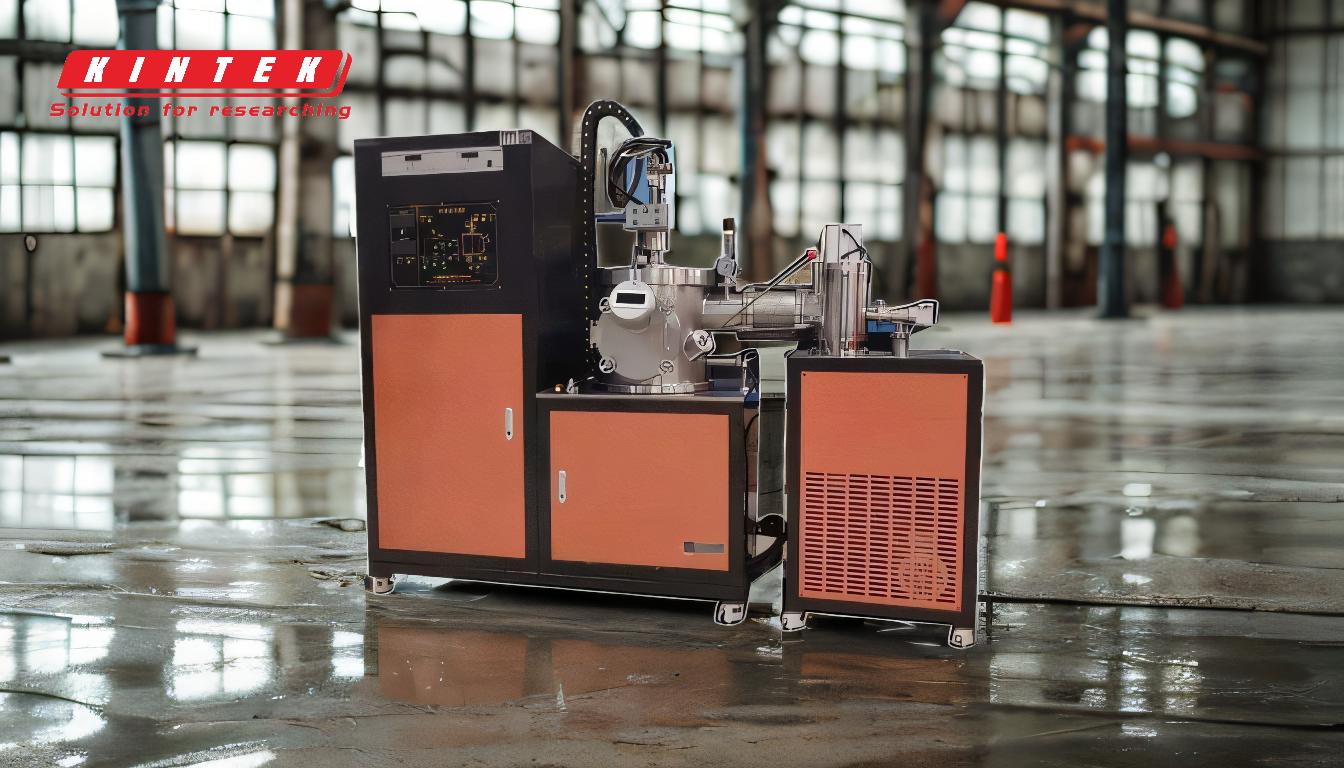
-
Vorbereitung des Pulvers Compact:
- Mischen und Komposition:Das Verfahren beginnt mit der Herstellung einer Pulvermischung, die keramische Primärmaterialien, Haftvermittler, Bindemittel und Entflockungsmittel enthält.Dieses Gemisch wird häufig mit Wasser zu einem Schlamm vermischt.
- Sprühtrocknung:Die Aufschlämmung wird anschließend sprühgetrocknet, um ein feines, frei fließendes Pulver zu erhalten, das sich leichter handhaben und pressen lässt.
- Pressen:Das Pulver wird mit Hilfe von Presswerkzeugen oder Formen in die gewünschte Form gepresst.Bei diesem Schritt entsteht ein "Grünling", eine kohärente, aber zerbrechliche Struktur, die die Form des Endprodukts beibehält.
-
Erhitzen und Sintern:
- Bindemittelentfernung (Entbindern):Der Grünling wird bei niedriger Temperatur erhitzt, um organische Bindemittel oder Haftvermittler auszubrennen.Dieser Schritt ist entscheidend, um Defekte während des Hochtemperatursinterns zu vermeiden.
-
Hochtemperatur-Sintern:Der Grünling wird dann auf eine Temperatur knapp unter dem Schmelzpunkt des keramischen Materials erhitzt.In dieser Phase laufen mehrere wichtige Prozesse ab:
- Partikelbindung:Die Pulverpartikel beginnen sich an ihren Kontaktpunkten zu verbinden, was zur Bildung von Korngrenzen führt.
- Materialwanderung:Die Atome wandern über die Korngrenzen, was zu einer Verdichtung und einer Verringerung der Porosität führt.
- Schrumpfung:Während sich die Partikel verbinden und das Material verdichtet, erfährt die Keramik eine erhebliche Schrumpfung, die sorgfältig kontrolliert werden muss, um die gewünschten Endmaße zu erreichen.
- Flüssigphasensintern (optional):In einigen Fällen wird eine flüssige Phase eingeführt, um den Verdichtungsprozess zu beschleunigen.Dabei werden Elemente wie Kupferpulver oder Hartmetalle hinzugefügt, die bei der Sintertemperatur schmelzen und in die verbleibenden Poren fließen, wodurch die Dichte des Materials weiter erhöht wird.
-
Abkühlung und Erstarrung:
- Nach dem Sinterprozess lässt man die Keramik langsam abkühlen.Diese Abkühlphase ist entscheidend dafür, dass das Material zu einer einheitlichen Masse mit den gewünschten mechanischen Eigenschaften wie Festigkeit und Härte erstarrt.
-
Verarbeitung nach dem Sintern:
- Bearbeitungen:Je nach Anwendung kann das gesinterte Keramikteil eine zusätzliche Bearbeitung erfordern.Dies geschieht häufig mit Diamantwerkzeugen oder durch Ultraschallbearbeitung, um präzise Abmessungen und Oberflächengüten zu erzielen.
- Montage:In einigen Fällen werden keramische Teile metallisiert und mit anderen Komponenten verlötet, insbesondere bei Anwendungen, bei denen Keramik in Verbindung mit Metallen verwendet wird.
-
Kontrollierte Parameter:
- Temperatur und Atmosphäre:Der Sinterprozess erfordert eine präzise Steuerung von Temperatur und Atmosphäre.Die Temperatur muss hoch genug sein, um eine Partikelbindung zu bewirken, darf aber nicht so hoch sein, dass es zum Schmelzen oder übermäßigen Kornwachstum kommt.Die Atmosphäre (z. B. reduzierend, oxidierend oder inert) ist ebenfalls entscheidend, um unerwünschte Reaktionen oder Oxidation zu verhindern.
- Schichtdicke und Geschwindigkeit:Bei kontinuierlichen Sinterprozessen müssen Parameter wie Schichtdicke, Geschwindigkeit und Endpunkt der Sinterung sorgfältig kontrolliert werden, um eine gleichmäßige Verdichtung zu gewährleisten und Defekte zu minimieren.
-
Anwendungen und Ergebnisse:
- Verringerung der Porosität:Eines der Hauptergebnisse des Sinterns ist die Verringerung der Porosität des Materials, wodurch die mechanische Festigkeit und Haltbarkeit der Keramik verbessert wird.
- Bildung eines Porzellankörpers:Im Laufe der Zeit verdichten sich die keramischen Materialien allmählich und bilden einen Porzellankörper mit einer gewissen Festigkeit, der sich für verschiedene Anwendungen wie Töpferwaren, industrielle Komponenten und Hochleistungskeramik eignet.
Zusammenfassend lässt sich sagen, dass das Sintern von Keramik ein mehrstufiger Prozess ist, der eine sorgfältige Vorbereitung, eine kontrollierte Erhitzung und eine präzise Nachsinterung erfordert, um ein dichtes, festes und haltbares Keramikprodukt zu erhalten.Der Prozess kann durch die Einstellung von Parametern wie Temperatur, Atmosphäre und die Verwendung von Zusatzstoffen wie Bindemitteln oder Flüssigphasen auf die jeweiligen Anforderungen zugeschnitten werden.
Zusammenfassende Tabelle:
Stufe | Wichtige Schritte | Ergebnis |
---|---|---|
Vorbereitung | Mischen, Sprühtrocknen, Pressen | Formung eines Grünlings mit gewünschter Form |
Erhitzen und Sintern | Bindemittelentfernung, Hochtemperatursintern, optional Flüssigphasensintern | Partikelbindung, Verdichtung und Schrumpfung |
Abkühlung | Allmähliche Abkühlung | Erstarrung zu einer einheitlichen Masse mit verbesserten mechanischen Eigenschaften |
Nach der Sinterung | Bearbeitung, Montage | Präzise Abmessungen, Oberflächenbeschaffenheit und Integration mit anderen Komponenten |
Kontrollierte Parameter | Temperatur, Atmosphäre, Schichtdicke, Geschwindigkeit | Gleichmäßige Verdichtung und minimierte Defekte |
Anwendungen | Töpferwaren, industrielle Komponenten, Hochleistungskeramik | Starke, haltbare und porenarme Keramikprodukte |
Sind Sie bereit, Ihren keramischen Herstellungsprozess zu optimieren? Kontaktieren Sie noch heute unsere Experten für maßgeschneiderte Lösungen!