Die chemische Gasphasenabscheidung (Chemical Vapor Deposition, CVD) ist eine in der Materialwissenschaft weit verbreitete Technik zur Abscheidung von dünnen Schichten, Beschichtungen und modernen Materialien auf Substraten.Es beinhaltet die chemische Reaktion von gasförmigen Vorläufern zur Bildung eines festen Materials auf einer Substratoberfläche.Der Prozess umfasst in der Regel Schritte wie den Transport der Reaktanten zum Substrat, die Adsorption und Reaktion auf der Oberfläche, die Filmbildung und die Entfernung von Nebenprodukten.CVD ist von entscheidender Bedeutung für die Halbleiterherstellung, die Nanotechnologie und für Schutzbeschichtungen.Im Folgenden werden die wichtigsten Schritte des CVD-Verfahrens im Detail erläutert.
Die wichtigsten Punkte werden erklärt:
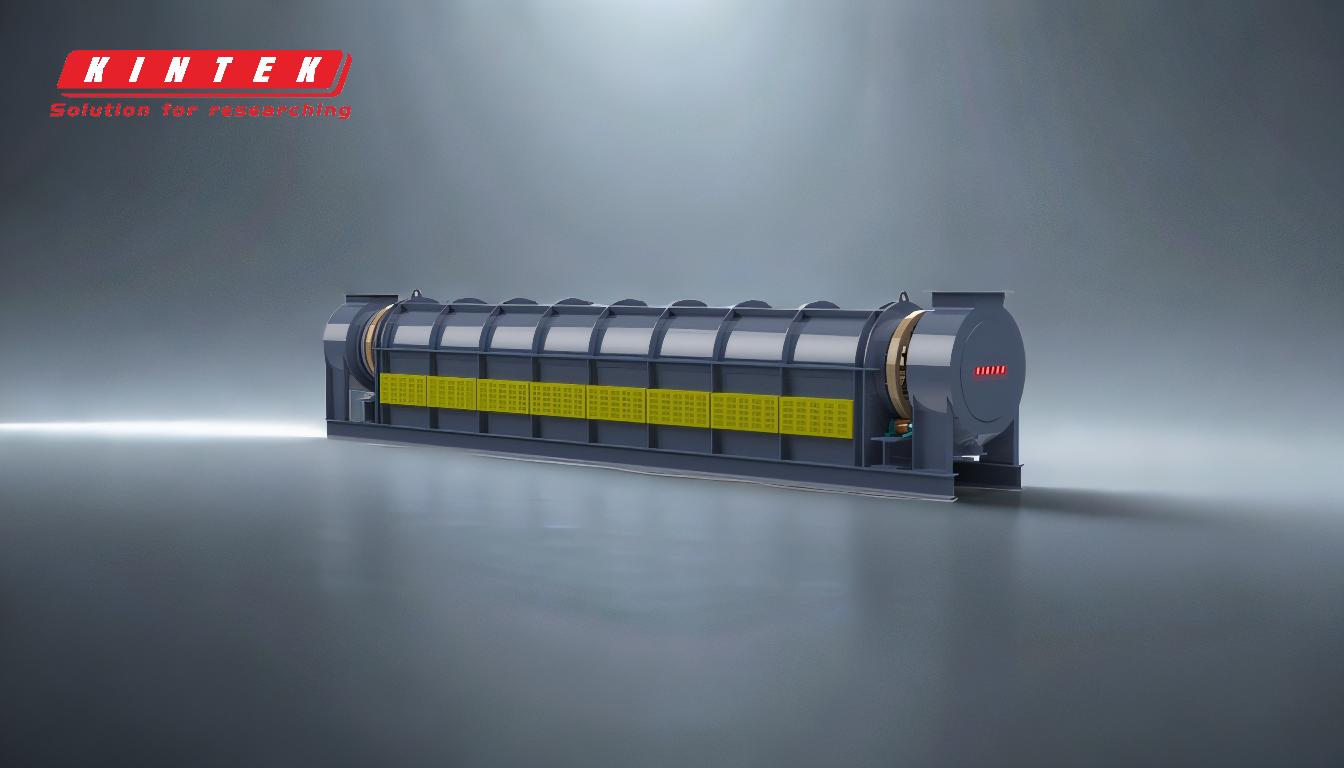
-
Einleitung von Reaktanten
- Gasförmige Vorläuferstoffe werden in eine Reaktionskammer eingeleitet, die das Substrat enthält.
- Die Reaktanten werden durch Konvektion oder Diffusion in die Reaktionszone transportiert.
- Dieser Schritt stellt sicher, dass die erforderlichen chemischen Stoffe für den Abscheidungsprozess zur Verfügung stehen.
-
Aktivierung der Reaktanten
- Die gasförmigen Ausgangsstoffe werden durch thermische Energie, Plasma oder Katalysatoren aktiviert.
- Durch die Aktivierung werden die Vorläufer in reaktive Spezies aufgespalten, so dass sie an der Abscheidungsreaktion teilnehmen können.
- Dieser Schritt ist entscheidend für die Einleitung der für die Filmbildung erforderlichen chemischen Reaktionen.
-
Transport der Reaktanten zur Substratoberfläche
- Die aktivierten Reaktanten diffundieren durch die Grenzschicht und erreichen die Substratoberfläche.
- Die Grenzschicht ist ein dünner Bereich in der Nähe des Substrats, in dem die Gasströmung langsamer ist, was einen effizienten Transport der Reaktanten ermöglicht.
- Ein ordnungsgemäßer Transport gewährleistet eine gleichmäßige Ablagerung auf dem Substrat.
-
Adsorption und Oberflächenreaktionen
- Die Reaktanten adsorbieren an der Substratoberfläche, wo sie chemische und physikalische Wechselwirkungen eingehen.
- Es kommt zu heterogenen Oberflächenreaktionen, die zur Bildung eines festen Films führen.
- Diese Reaktionen werden häufig durch das Substrat oder die Oberflächenbedingungen katalysiert.
-
Filmwachstum und Keimbildung
- Die adsorbierten Stoffe diffundieren zu den Wachstumsstellen auf dem Substrat, wo Keimbildung und Filmwachstum stattfinden.
- Der Film wächst Schicht für Schicht und bildet eine gleichmäßige und fest haftende Beschichtung.
- Dieser Schritt bestimmt die Qualität, die Dicke und die Eigenschaften des abgeschiedenen Materials.
-
Desorption von Nebenprodukten
- Flüchtige Nebenprodukte, die bei den Oberflächenreaktionen entstehen, werden vom Substrat desorbiert.
- Diese Nebenprodukte diffundieren durch die Grenzschicht und werden aus der Reaktionszone abtransportiert.
- Eine effiziente Entfernung der Nebenprodukte ist unerlässlich, um Verunreinigungen zu vermeiden und eine qualitativ hochwertige Abscheidung zu gewährleisten.
-
Beseitigung gasförmiger Nebenprodukte
- Die gasförmigen Nebenprodukte werden durch Konvektions- und Diffusionsprozesse aus der Reaktionskammer entfernt.
- Durch diesen Schritt wird die Reinheit der Reaktionsumgebung aufrechterhalten und unerwünschte Reaktionen verhindert.
- Die ordnungsgemäße Entfernung gewährleistet auch die Langlebigkeit der Abscheidungsanlagen.
-
Kühlung und Nachbearbeitung
- Nach der Abscheidung wird das Substrat unter kontrollierten Bedingungen abgekühlt, um die abgeschiedene Schicht zu stabilisieren.
- Nachbearbeitungsschritte, wie Glühen oder Ätzen, können durchgeführt werden, um die Eigenschaften der Schicht zu verbessern.
- Kühlung und Nachbearbeitung sind entscheidend für das Erreichen der gewünschten Materialeigenschaften.
Zusätzliche Überlegungen:
- Vorbereitung des Substrats:Das Substrat muss gereinigt und erhitzt werden, um Verunreinigungen zu entfernen und eine geeignete Oberfläche für die Abscheidung zu schaffen.
- Temperaturkontrolle:Die genaue Steuerung der Substrattemperatur ist entscheidend für die Optimierung des Abscheidungsprozesses und der Schichtqualität.
- Gasflussdynamik:Ein effizientes Gasfluss- und Druckmanagement gewährleistet eine gleichmäßige Verteilung der Reaktanten und die Entfernung von Nebenprodukten.
- Rolle des Katalysators:Bei Verfahren wie dem Graphenwachstum dient das Substrat (z. B. Kupfer) sowohl als Katalysator als auch als Oberfläche für die Keimbildung.
Durch die Einhaltung dieser Schritte ermöglicht das CVD-Verfahren die Herstellung hochwertiger dünner Schichten und Beschichtungen mit präziser Kontrolle der Materialeigenschaften.Dies macht es in Branchen wie der Elektronik, der Optik und der Werkstofftechnik unverzichtbar.
Zusammenfassende Tabelle:
Schritt | Beschreibung |
---|---|
1.Einführung der Reaktanten | Gasförmige Ausgangsstoffe werden in die Reaktionskammer eingeleitet. |
2.Aktivierung der Reaktanten | Die Vorläuferstoffe werden durch thermische Energie, Plasma oder Katalysatoren aktiviert. |
3.Transport zum Substrat | Die Reaktanten diffundieren durch die Grenzschicht und erreichen das Substrat. |
4.Adsorption und Oberflächenreaktionen | Reaktanten adsorbieren und reagieren an der Substratoberfläche. |
5.Filmwachstum und Keimbildung | Adsorbierte Arten bilden Schicht für Schicht einen gleichmäßigen Film. |
6.Desorption von Nebenprodukten | Flüchtige Nebenprodukte desorbieren und diffundieren weg. |
7.Beseitigung gasförmiger Nebenprodukte | Die Nebenprodukte werden aus der Reaktionskammer entfernt. |
8.Kühlung und Nachbearbeitung | Das Substrat wird gekühlt, und die Nachbearbeitung verbessert die Schichteigenschaften. |
Benötigen Sie fachkundige Beratung zu CVD-Verfahren? Kontaktieren Sie uns noch heute für maßgeschneiderte Lösungen!