Die Temperatur und die Haltezeit beim Sintern sind kritische Parameter, die von dem zu verarbeitenden Material, den gewünschten Eigenschaften des Endprodukts und der spezifischen Sintertechnik abhängen.Die Sintertemperaturen liegen in der Regel zwischen 70 % und 90 % des Schmelzpunkts des Materials, und die Haltezeit kann zwischen Millisekunden und über 24 Stunden variieren.Diese Parameter beeinflussen Porosität, Dichte, Festigkeit und Härte des gesinterten Körpers.Hohe Temperaturen und lange Haltezeiten können die Porosität verringern und die Dichte erhöhen, aber auch zu Defekten oder Kornwachstum führen, während eine unzureichende Sinterung die Materialeigenschaften verschlechtern kann.Bei der Wahl der Sinterbedingungen müssen diese Faktoren gegeneinander abgewogen werden, um die gewünschten Produkteigenschaften zu erzielen.
Die wichtigsten Punkte werden erklärt:
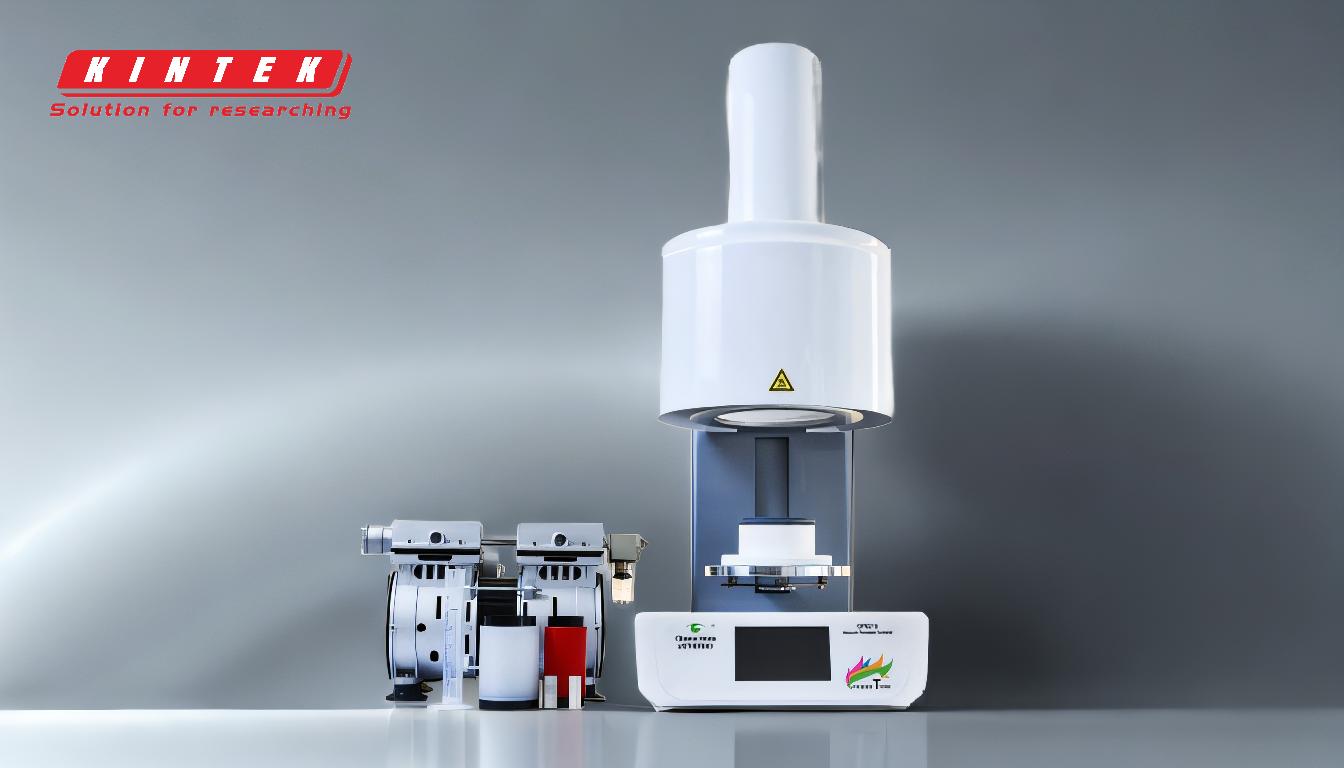
-
Abhängigkeit von Material und gewünschten Eigenschaften:
- Die Sintertemperatur und die Haltezeit werden auf das jeweilige Material und die erforderliche Dichte, Festigkeit und Härte des Endprodukts abgestimmt.
- Metalle wie Stahl oder Titan erfordern beispielsweise höhere Temperaturen (z. B. 1000°C bis 1400°C) als Keramik oder Polymere.
-
Typischer Temperaturbereich:
- Die Sintertemperaturen liegen im Allgemeinen bei 70 bis 90 % des Schmelzpunkts des Materials.
- Wenn ein Material beispielsweise einen Schmelzpunkt von 1500°C hat, kann die Sintertemperatur zwischen 1050°C und 1350°C liegen.
-
Variabilität der Haltezeit:
- Die Haltezeiten können von Millisekunden (bei Techniken wie dem Spark-Plasma-Sintern) bis zu mehreren Stunden (beim traditionellen Ofensintern) reichen.
- Längere Haltezeiten werden häufig für Werkstoffe verwendet, die eine hohe Verdichtung erfordern, während kürzere Zeiten für Werkstoffe mit niedrigerem Schmelzpunkt oder bei der Verwendung fortgeschrittener Techniken ausreichend sein können.
-
Einfluss auf die Materialeigenschaften:
- Hohe Temperatur und lange Haltezeit:Kann die Porosität verringern und die Dichte erhöhen, kann aber zu Kornwachstum, Defekten oder reduzierten mechanischen Eigenschaften führen.
- Niedrige Temperatur oder kurze Haltezeit:Kann zu einer unzureichenden Verdichtung führen, was zu schlechten mechanischen Eigenschaften und höherer Porosität führt.
-
Die Rolle der Sinteratmosphäre:
- Die Sinteratmosphäre (z. B. Luft, Vakuum, Argon oder Stickstoff) kann den Prozess beeinflussen, indem sie die Oxidation verhindert oder die Diffusionsraten steuert.
- So wird beispielsweise das Vakuumsintern häufig für oxidationsanfällige Materialien wie Titan verwendet.
-
Einfluss von Partikelgröße und -zusammensetzung:
- Kleinere Partikelgrößen und homogene Zusammensetzungen fördern eine bessere Verdichtung und schnellere Sinterung.
- Größere Partikel oder heterogene Zusammensetzungen können höhere Temperaturen oder längere Haltezeiten erfordern.
-
Fortgeschrittene Sintertechniken:
- Verfahren wie das selektive Lasersintern (SLS) oder das feldunterstützte Sintern (FAST) können die Sinterzeiten erheblich verkürzen.
- Mit FAST kann beispielsweise eine vollständige Verdichtung innerhalb von Minuten erreicht werden, verglichen mit Stunden in herkömmlichen Öfen.
-
Kompromisse bei den Sinterparametern:
- Eine Erhöhung der Temperatur oder der Haltezeit kann die Dichte und Festigkeit verbessern, kann aber auch das Risiko von Defekten oder Kornwachstum erhöhen.
- Schnellere Sintertechniken können die Verarbeitungszeit verkürzen, können aber zu Restporosität oder ungleichmäßiger Verdichtung führen.
-
Bedeutung der Abkühlgeschwindigkeit:
- Die Abkühlungsgeschwindigkeit nach dem Sintern kann das endgültige Mikrogefüge und die Eigenschaften beeinflussen.
- Eine kontrollierte Abkühlung wird häufig eingesetzt, um thermische Spannungen oder Phasenumwandlungen zu vermeiden, die die Leistungsfähigkeit des Materials beeinträchtigen könnten.
-
Optimierung für spezifische Anwendungen:
- Die Wahl der Sinterparameter hängt von den Anforderungen der Anwendung ab, wie etwa hohe Festigkeit, Verschleißfestigkeit oder Wärmeleitfähigkeit.
- So können beispielsweise die Sinterbedingungen für Bauteile in der Luft- und Raumfahrt vorrangig auf Festigkeit und Ermüdungsbeständigkeit ausgerichtet sein, während für biomedizinische Implantate Biokompatibilität und Korrosionsbeständigkeit im Vordergrund stehen.
Durch eine sorgfältige Abwägung dieser Faktoren können die Hersteller die gewünschten Eigenschaften der gesinterten Werkstoffe erzielen und gleichzeitig Fehler und Verarbeitungskosten minimieren.Der optimale Sinterprozess ist ein Kompromiss zwischen Materialeigenschaften, Verarbeitungstechniken und Anwendungsanforderungen.
Zusammenfassende Tabelle:
Faktor | Einfluss auf die Sinterung |
---|---|
Materialtyp | Bestimmt die erforderliche Temperatur und Haltezeit (z. B. Metalle vs. Keramik). |
Temperaturbereich | In der Regel 70-90 % des Schmelzpunkts des Materials. |
Haltezeit | reicht von Millisekunden (Funkenplasmasintern) bis zu Stunden (traditionelles Sintern). |
Sinter-Atmosphäre | Verhindert Oxidation oder kontrolliert die Diffusion (z. B. Vakuum für Titan). |
Partikelgröße | Kleinere Partikel sorgen für eine schnellere und bessere Verdichtung. |
Fortgeschrittene Techniken | FAST oder SLS verkürzt die Sinterzeit erheblich. |
Abkühlungsrate | Beeinflusst das Mikrogefüge und verhindert thermische Spannungen. |
Anforderungen an die Anwendung | Maßgeschneidert für Festigkeit, Verschleißfestigkeit oder Biokompatibilität (z. B. Luft- und Raumfahrt vs. Biomedizin). |
Benötigen Sie Hilfe bei der Optimierung Ihres Sinterprozesses? Kontaktieren Sie noch heute unsere Experten für maßgeschneiderte Lösungen!