Die Temperatur eines Pyrolysereaktors liegt in der Regel zwischen 350 und 400 °C für die Hochtemperaturpyrolyse, die für die Zerlegung von Abfallstoffen in wertvolle Nebenprodukte wie Pyrolyseöl, Ruß und Synthesegas unerlässlich ist. Die Mitteltemperaturpyrolyse kann jedoch auch bei höheren Temperaturen zwischen 600 und 700 °C stattfinden, je nach dem spezifischen Prozess und den zu behandelnden Materialien. Der Reaktor ist auf eine externe Wärmequelle angewiesen und arbeitet als geschlossenes System, das thermodynamischen Prinzipien folgt. Faktoren wie die Ofentemperatur, die Verweilzeit und der Innendruck haben einen erheblichen Einfluss auf die Effizienz und Leistung des Pyrolyseprozesses, so dass eine ordnungsgemäße Steuerung und Wartung für optimale Ergebnisse entscheidend ist.
Die wichtigsten Punkte werden erklärt:
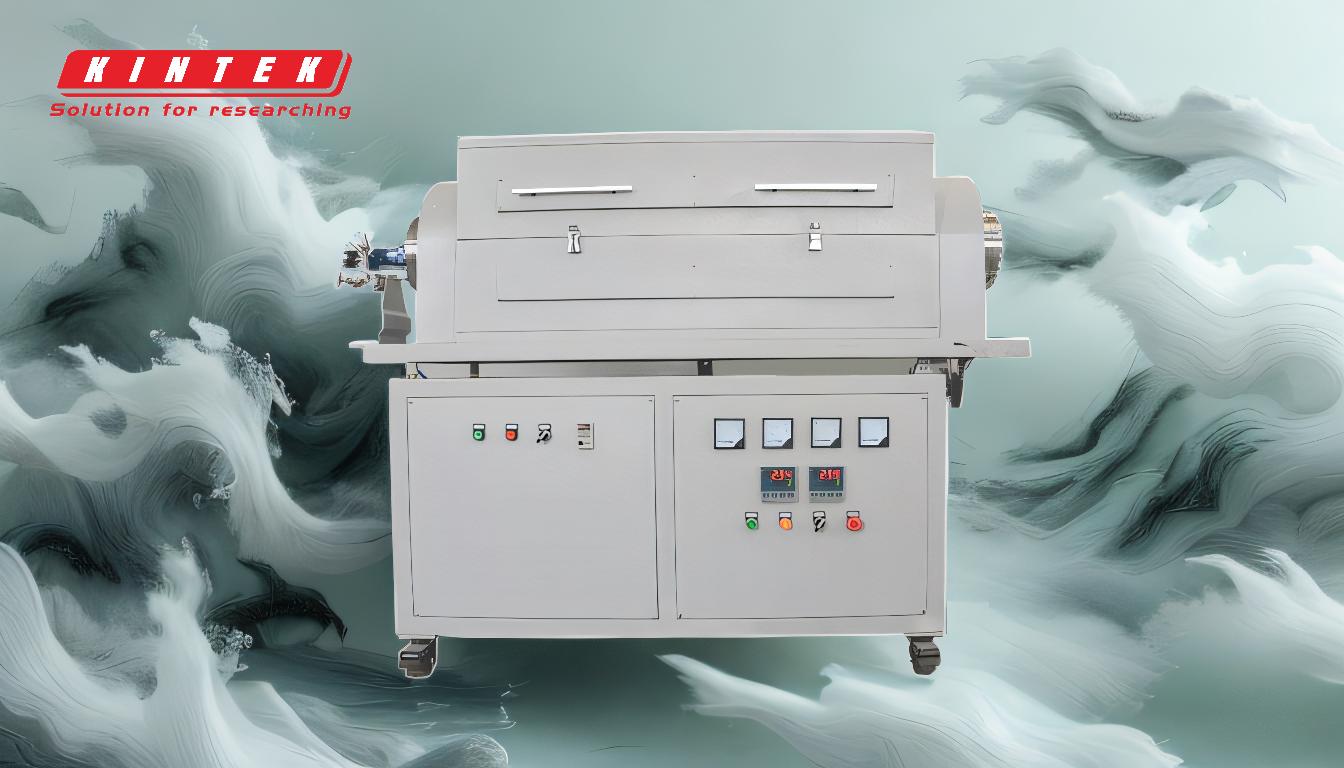
-
Temperaturbereich für Pyrolyse-Reaktoren:
- Die Hochtemperaturpyrolyse arbeitet normalerweise zwischen 350-400°C . Dieser Bereich ist notwendig, um die Zersetzung von Abfallstoffen in wertvolle Produkte wie Pyrolyseöl, Ruß und Synthesegas zu gewährleisten.
- Die Pyrolyse bei mittlerer Temperatur kann bei höheren Temperaturen erfolgen, die von 600-700°C je nach Art des Ausgangsmaterials und der gewünschten Leistung.
-
Zweck der Temperaturkontrolle:
- Die Temperatur ist entscheidend für die Einleitung und Aufrechterhaltung des Pyrolyseprozesses, der die thermische Zersetzung organischer Stoffe unter Ausschluss von Sauerstoff beinhaltet.
- Höhere Temperaturen gewährleisten die vollständige Aufspaltung komplexer Moleküle, was zur Erzeugung nützlicher Nebenprodukte führt.
-
Externe Wärmeversorgung:
- Pyrolysereaktoren basieren auf einem externe Wärmequelle um die erforderlichen Temperaturen aufrechtzuerhalten. Dies gewährleistet eine gleichmäßige und kontrollierte Erwärmung, die für einen effizienten Betrieb unerlässlich ist.
- Der Reaktor arbeitet als geschlossenes System das bedeutet, dass er versiegelt ist, um den Eintritt von Sauerstoff zu verhindern, der sonst zur Verbrennung statt zur Pyrolyse führen könnte.
-
Faktoren, die die Effizienz beeinflussen:
- Temperatur des Ofens: Die genaue Steuerung der Temperatur ist entscheidend für die Optimierung des Pyrolyseprozesses. Eine zu niedrige Temperatur kann zu einer unvollständigen Zersetzung führen, während zu hohe Temperaturen zu unerwünschten Nebenprodukten führen können.
- Aufenthaltsdauer: Die Verweildauer der Stoffe im Reaktor beeinflusst das Ausmaß der Zersetzung. Längere Verweilzeiten können die Ausbeute verbessern, aber auch den Energieverbrauch erhöhen.
- Innerer Druck: Die Druckregelung ist wichtig, um die Integrität des Reaktors zu erhalten und einen sicheren Betrieb zu gewährleisten. Sie beeinflusst auch die Geschwindigkeit der Zersetzung und die Qualität der Endprodukte.
-
Bedeutung einer ordnungsgemäßen Bedienung und Wartung:
- Regelmäßige Wartung und ordnungsgemäßer Betrieb sind unerlässlich, um sicherzustellen, dass der Reaktor mit höchster Effizienz arbeitet und sicher bleibt.
- Die Überwachung und Kontrolle der Temperatur, der Verweilzeit und des Drucks sind der Schlüssel zur Erzielung einer gleichmäßigen und hochwertigen Produktion.
-
Thermodynamische Grundsätze:
- Pyrolysereaktoren arbeiten auf der Grundlage von thermodynamische Grundsätze die die Wärmeübertragung und das Verhalten von Materialien bei hohen Temperaturen bestimmen.
- Das Verständnis dieser Prinzipien hilft bei der Planung und dem Betrieb von Reaktoren, die die Energieeffizienz und die Produktausbeute maximieren.
Wenn die Käufer von Anlagen und Verbrauchsmaterialien diese Schlüsselpunkte verstehen, können sie fundierte Entscheidungen über die Spezifikationen und Wartungsanforderungen von Pyrolysereaktoren treffen und so optimale Leistung und Sicherheit gewährleisten.
Zusammenfassende Tabelle:
Schlüsselfaktor | Einzelheiten |
---|---|
Hochtemperatur-Pyrolyse | 350-400°C zur Aufspaltung von Abfall in Pyrolyseöl, Ruß und Synthesegas. |
Pyrolyse bei mittlerer Temperatur | 600-700°C für bestimmte Einsatzstoffe und Verfahren. |
Externe Wärmequelle | Gewährleistet eine gleichmäßige und kontrollierte Erwärmung in einem geschlossenen System. |
Kritische Faktoren | Ofentemperatur, Verweilzeit und Innendruck. |
Wartung | Regelmäßige Kontrollen gewährleisten Effizienz, Sicherheit und qualitativ hochwertige Ergebnisse. |
Sind Sie bereit, Ihren Pyrolyseprozess zu optimieren? Kontaktieren Sie unsere Experten noch heute für maßgeschneiderte Lösungen!