Kalzinieröfen sind für den Betrieb bei hohen Temperaturen ausgelegt, die je nach Anwendungsfall typischerweise zwischen 800°C und 1300°C liegen.Der Temperaturbereich wird von den zu verarbeitenden Materialien, den gewünschten chemischen oder physikalischen Umwandlungen und der Effizienz des Ofens beeinflusst.Faktoren wie Temperaturregelung, Kalibrierung und Konstruktion des Ofens spielen eine entscheidende Rolle bei der Erzielung einheitlicher und genauer Ergebnisse.Darüber hinaus gewährleistet die Wahl eines Ofens mit einer Höchsttemperatur, die etwas höher ist als die erforderliche Verwendungstemperatur, eine optimale Leistung und Langlebigkeit des Geräts.
Die wichtigsten Punkte erklärt:
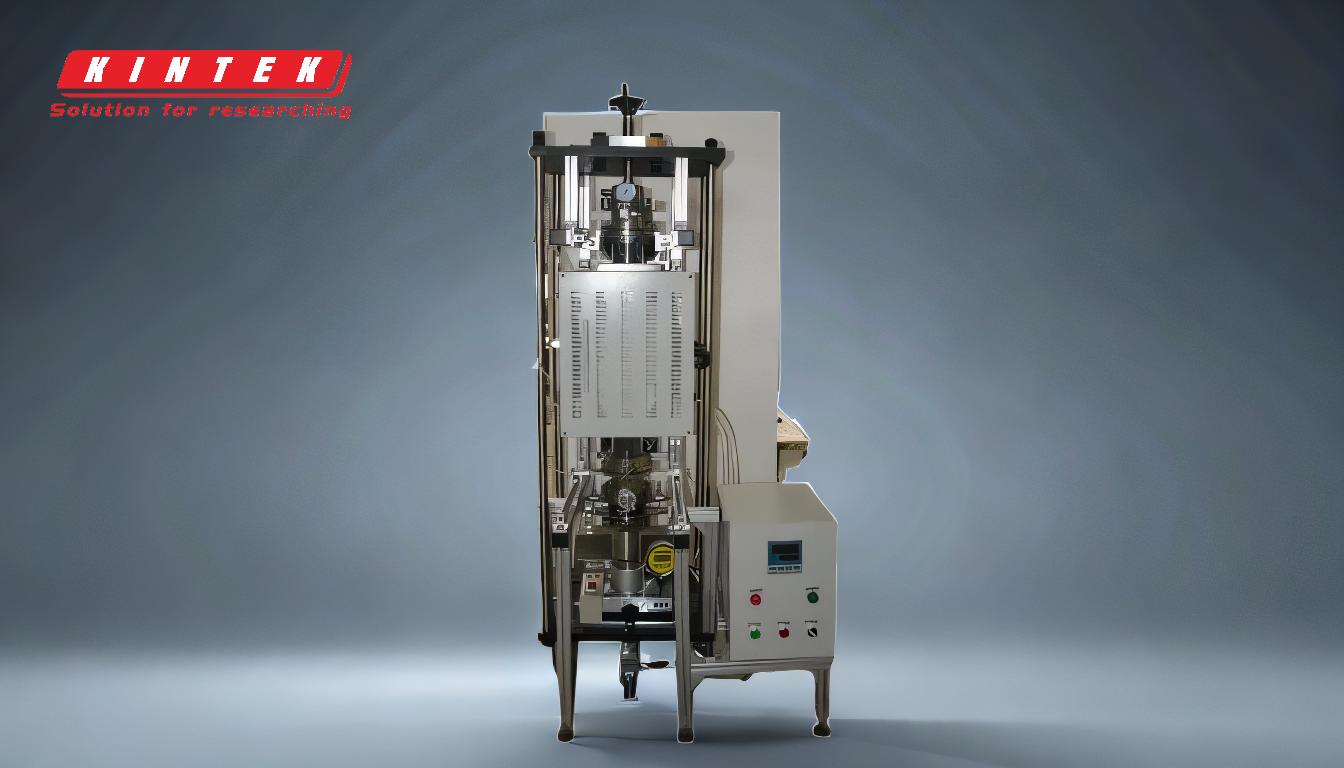
-
Typischer Temperaturbereich für Kalzinierungsöfen:
- Kalzinierungsöfen arbeiten im Allgemeinen bei Temperaturen zwischen 800°C und 1300°C .
- Dieser Bereich eignet sich für Prozesse wie thermische Zersetzung, Entfernung flüchtiger Bestandteile oder Phasenumwandlungen in Materialien wie Keramik, Metallen und Mineralien.
- Die genaue Temperatur hängt von der jeweiligen Anwendung und dem zu verarbeitenden Material ab.
-
Faktoren, die die Temperaturregelung beeinflussen:
-
Die Temperaturregelung in Öfen kann beeinflusst werden durch:
- Chemische und physikalische Einflüsse:Reaktionen innerhalb des Ofens können das Temperaturprofil verändern.
- Verschmutzung und Ablagerungen:Rückstände von Materialien wie Keramik, Legierungen oder Lötmaterialien können die Wärmeverteilung und Temperaturgenauigkeit beeinträchtigen.
- Kalibrierungsprozesse:Unterschiedliche Kalibrierungsmethoden der Hersteller können zu Unterschieden zwischen der tatsächlichen und der eingestellten Temperatur führen.
-
Die Temperaturregelung in Öfen kann beeinflusst werden durch:
-
Wichtigkeit der Ofenkonstruktion und -konfiguration:
-
Bei der Auswahl oder Konfiguration eines Kalzinierofens ist Folgendes zu beachten:
- Masse der heißen Zone:Dies wirkt sich auf die Wärmeverteilung und die Energieeffizienz aus.
- Betriebstemperaturbereich:Vergewissern Sie sich, dass der Ofen die erforderlichen Temperaturen bewältigen kann.
- Gasströmungsverteilung und Beladungsstrategie:Diese beeinflussen die Gleichmäßigkeit der Erwärmung und die Ergebnisse des Prozesses.
- Um eine optimale Leistung zu erzielen, sollte die Höchsttemperatur des Ofens 100 bis 200°C höher als die tatsächliche Verwendungstemperatur.
-
Bei der Auswahl oder Konfiguration eines Kalzinierofens ist Folgendes zu beachten:
-
Materialspezifische Temperaturanforderungen:
-
Die Temperatur und die Dauer der Kalzinierung hängen davon ab:
- dem zu verarbeitende Material (z. B. Keramiken, Metalle oder Mineralien).
- Die gewünschte Dichte oder Eigenschaften des Endprodukts.
- So erfordern beispielsweise Sinteröfen für Dentalanwendungen eine präzise Temperaturregelung, um die gewünschte Dichte und Festigkeit von Keramik- oder Legierungskomponenten zu erreichen.
-
Die Temperatur und die Dauer der Kalzinierung hängen davon ab:
-
Kontinuierliche vs. chargenweise Öfen:
- Durchlauföfen sind ideal für Prozesse, die konstante, dauerhafte Temperaturbedingungen erfordern, wie z. B. das Glühen oder Härten.
- Batch-Öfen sind vielseitiger und können mit unterschiedlichen Materialien und Temperaturprofilen umgehen, wodurch sie sich für Kalzinierungsprozesse mit spezifischen Temperatur- und Zeitanforderungen eignen.
-
Einfluss der Temperaturgenauigkeit auf die Ergebnisse:
- Die Genauigkeit der tatsächlichen Temperatur im Ofen ist entscheidend für die Erzielung einheitlicher Ergebnisse.
- Temperaturschwankungen aufgrund von Kalibrierungsunterschieden oder der Bauart des Ofens können die Qualität des Endprodukts beeinträchtigen.
- Regelmäßige Wartung und Kalibrierung sind unerlässlich, um die Temperaturgenauigkeit zu erhalten und eine zuverlässige Leistung zu gewährleisten.
-
Praktische Überlegungen für Einkäufer:
-
Bewerten Sie beim Kauf eines Kalzinierofens:
- Die maximale Temperatur und ob sie Ihren Prozessanforderungen entspricht.
- Die Website Energieeffizienz und Betriebskosten des Ofens.
- Die Haltbarkeit und Wartungsanforderungen des Geräts.
- Die Wahl eines Ofens mit einer etwas höheren Höchsttemperatur als erforderlich bietet eine Sicherheitsmarge und gewährleistet langfristige Zuverlässigkeit.
-
Bewerten Sie beim Kauf eines Kalzinierofens:
Wenn man diese wichtigen Punkte kennt, kann man bei der Auswahl eines Kalzinierofens fundierte Entscheidungen treffen und sicherstellen, dass er die spezifischen Temperatur- und Prozessanforderungen erfüllt und gleichzeitig effizient und zuverlässig ist.
Zusammenfassende Tabelle:
Aspekt | Details |
---|---|
Typischer Temperaturbereich | 800°C bis 1300°C, je nach Material und Verfahren. |
Faktoren, die die Kontrolle beeinflussen | Chemische/physikalische Reaktionen, Verschmutzung, Kalibrierungsmethoden. |
Konstruktion des Ofens | Masse der heißen Zone, Verteilung des Gasstroms, Beladungsstrategie. |
Materialspezifische Anforderungen | Temperatur und Dauer variieren je nach Material (Keramiken, Metalle, Mineralien). |
Kontinuierlich vs. Batch | Kontinuierlich für konstante Temperaturen; Batch für unterschiedliche Profile. |
Temperatur-Genauigkeit | Entscheidend für konsistente Ergebnisse; regelmäßige Kalibrierung ist unerlässlich. |
Überlegungen zum Kauf | Höchsttemperatur, Energieeffizienz, Haltbarkeit und Wartung. |
Sind Sie bereit, Ihre Hochtemperaturprozesse zu optimieren? Kontaktieren Sie uns noch heute für eine fachkundige Beratung bei der Auswahl des perfekten Kalzinierofens!