Die Pyrolyse ist ein thermischer Zersetzungsprozess, der in Abwesenheit von Sauerstoff abläuft, und der für die Pyrolyse erforderliche Temperaturbereich variiert je nach Art der Pyrolyse und den gewünschten Endprodukten. Im Allgemeinen kann die Pyrolyse in Niedertemperatur-, Mitteltemperatur- und Hochtemperaturverfahren eingeteilt werden, die jeweils spezifische Temperaturbereiche und Anwendungen haben. Die Niedertemperaturpyrolyse findet in der Regel zwischen 350-450 °C statt, die Mitteltemperaturpyrolyse zwischen 450-700 °C und die Hochtemperaturpyrolyse zwischen 700-1200 °C. Die Schnellpyrolyse, die auf eine maximale Bioölproduktion abzielt, arbeitet optimal bei etwa 500 °C mit schnellen Heizraten. Die Flash-Pyrolyse, ein weiteres schnelles Verfahren, erfordert Temperaturen zwischen 450 und 600 °C. Die Wahl des Temperaturbereichs hängt vom Ausgangsmaterial und dem gewünschten Ergebnis ab, z. B. Bioöl, Synthesegas oder Holzkohle.
Die wichtigsten Punkte werden erklärt:
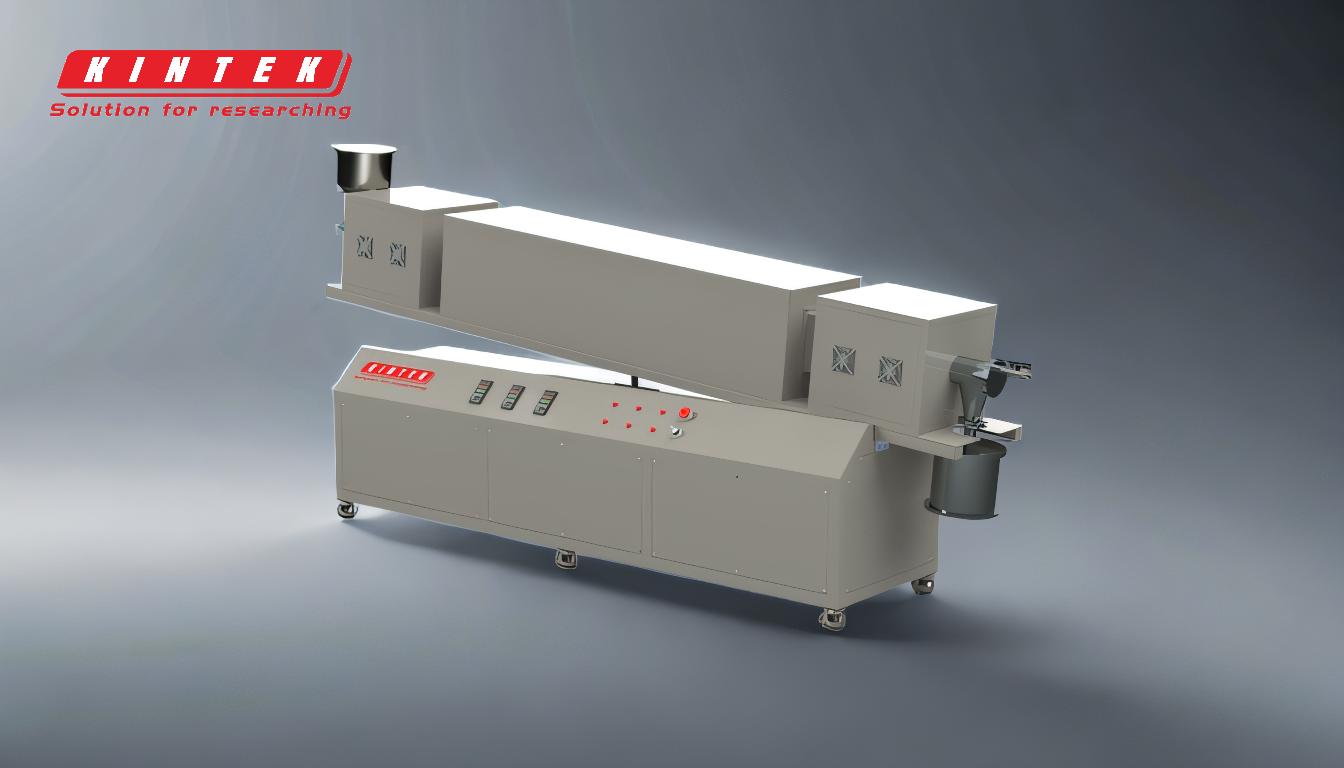
-
Allgemeine Temperaturbereiche für die Pyrolyse:
- Niedertemperatur-Pyrolyse (350-450°C): Diese Produktreihe eignet sich für Verfahren, bei denen das Hauptziel die Herstellung von Holzkohle oder Biokohle ist. Sie wird häufig in der Abfallwirtschaft und zur Bodenverbesserung eingesetzt.
- Pyrolyse bei mittlerer Temperatur (450-700°C): Dieser Bereich wird üblicherweise für die Herstellung von Bioöl und Synthesegas verwendet. Die Pyrolyse bei mittlerer Temperatur wird häufig bei Verfahren zur Umwandlung von Biomasse eingesetzt.
- Hochtemperatur-Pyrolyse (700-1200°C): Diese Produktreihe wird für Verfahren eingesetzt, bei denen komplexe Stoffe in einfachere Moleküle zerlegt werden müssen, wie z. B. bei der Herstellung von Synthesegas oder bei der Behandlung von Industrieabfällen.
-
Schnelle Pyrolyse:
- Optimale Temperatur (500°C): Die Schnellpyrolyse wurde entwickelt, um die Produktion von Bioöl zu maximieren. Die optimale Temperatur für dieses Verfahren liegt bei etwa 500°C, mit schnellen Heizraten (bis zu 1000°C/s) und kurzen Verweilzeiten für Pyrolysedämpfe.
- Bio-Öl-Erträge: Unter diesen Bedingungen kann die Bioölausbeute 60-70 Gew.-% erreichen, was die Schnellpyrolyse zu einer effizienten Methode für die Bioölproduktion macht.
-
Flash-Pyrolyse:
- Temperaturbereich (450-600°C): Die Flash-Pyrolyse ist ein weiteres schnelles Verfahren, das in einem etwas breiteren Temperaturbereich von 450-600°C arbeitet.
- Heizrate und Verweilzeit: Die Heizrate sollte zwischen 10^3 und 10^4 °C/s liegen, und die Verweilzeit sollte weniger als 1 Sekunde betragen, um eine effektive Flash-Pyrolyse zu erreichen.
-
Hochtemperatur-Pyrolyse:
- Temperaturbereich (700-1200°C): Die Hochtemperaturpyrolyse wird für komplexere Materialien und industrielle Anwendungen eingesetzt. Dieser Bereich ist für die Zerlegung von Abfallstoffen in wertvolle Produkte wie Pyrolyseöl, Ruß und Synthesegas erforderlich.
- Reaktorbedingungen: Bei der Hochtemperaturpyrolyse werden oft lange (20-30 Meter), dünne (1-2 Zoll) Reaktorrohre aus feuerfesten Legierungen von außen beheizt und mit Drücken zwischen 1-30 bar betrieben.
-
Anwendungen und Überlegungen:
- Art des Rohstoffs: Die Wahl der Pyrolysetemperatur hängt von der Art des Ausgangsmaterials ab. So sind für Biomasse in der Regel niedrigere Temperaturen erforderlich als für Industrieabfälle.
- Gewünschte Produkte: Der Temperaturbereich wird auch in Abhängigkeit von den gewünschten Endprodukten gewählt. So begünstigen beispielsweise niedrigere Temperaturen die Produktion von Holzkohle, während höhere Temperaturen Syngas und Bioöl begünstigen.
- Prozess-Effizienz: Schnelle Heizraten und kurze Verweilzeiten sind für Prozesse wie die Schnell- und Flash-Pyrolyse entscheidend, um die Produktausbeute und Effizienz zu maximieren.
Zusammenfassend lässt sich sagen, dass der für die Pyrolyse erforderliche Temperaturbereich je nach spezifischem Prozess und gewünschtem Ergebnis sehr unterschiedlich ist. Das Verständnis dieser Bereiche und ihrer Anwendungen ist entscheidend für die Optimierung von Pyrolyseprozessen für verschiedene Ausgangsstoffe und Endprodukte.
Zusammenfassende Tabelle:
Pyrolyse Typ | Temperaturbereich | Wichtige Anwendungen |
---|---|---|
Niedertemperatur | 350-450°C | Herstellung von Holzkohle/Biokohle, Abfallwirtschaft, Bodenverbesserung. |
Mitteltemperaturen | 450-700°C | Herstellung von Bioöl und Synthesegas, Umwandlung von Biomasse. |
Hochtemperatur | 700-1200°C | Synthesegaserzeugung, Behandlung von Industrieabfällen, komplexer Materialabbau. |
Schnelle Pyrolyse | ~500°C | Maximiert die Bioölproduktion mit schnellen Heizraten (bis zu 1000°C/s). |
Flash-Pyrolyse | 450-600°C | Schnelles Verfahren mit Heizraten von 10^3 bis 10^4 °C/s und kurzen Verweilzeiten. |
Benötigen Sie Hilfe bei der Auswahl der richtigen Pyrolysetemperatur für Ihre Anwendung? Kontaktieren Sie unsere Experten noch heute !