Die chemische Gasphasenabscheidung (CVD) ist eine weit verbreitete Methode zur Abscheidung dünner Schichten mit zahlreichen Vorteilen wie hoher Reinheit, Gleichmäßigkeit und der Möglichkeit, komplexe Formen zu beschichten.Sie hat jedoch auch einige entscheidende Nachteile, darunter hohe Betriebstemperaturen, die Notwendigkeit giftiger Vorläuferstoffe und Schwierigkeiten bei der Synthese von Mehrkomponentenmaterialien.Diese Nachteile können ihre Anwendbarkeit in bestimmten Szenarien einschränken, insbesondere bei der Arbeit mit thermisch empfindlichen Substraten oder wenn eine Abscheidung vor Ort erforderlich ist.
Die wichtigsten Punkte werden erklärt:
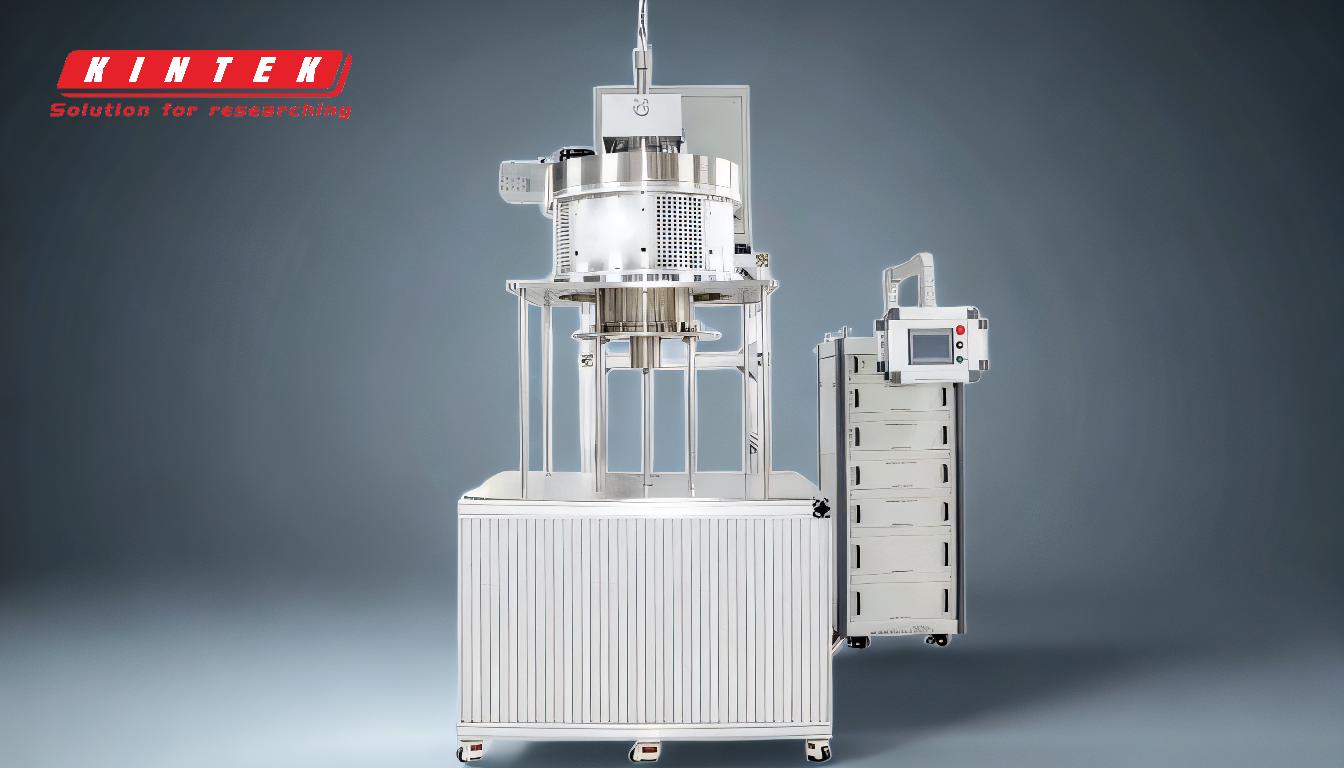
-
Hohe Betriebstemperaturen:
- CVD arbeitet in der Regel bei hohen Temperaturen, was bei vielen Substraten zu thermischer Instabilität führen kann.Dies ist vor allem bei Materialien problematisch, die hoher Hitze nicht standhalten können, und schränkt die Palette der Materialien ein, die mit CVD bearbeitet werden können.
-
Giftige und gefährliche Vorläuferstoffe:
- Das Verfahren erfordert chemische Ausgangsstoffe mit hohem Dampfdruck, die oft hochgiftig und gefährlich sind.Der Umgang mit diesen Ausgangsstoffen erfordert strenge Sicherheitsmaßnahmen, was die Komplexität und die Kosten des Prozesses erhöht.
-
Herausforderungen bei der Synthese von Multikomponentenmaterialien:
- Bei der CVD-Synthese von Multikomponenten-Materialien gibt es Schwierigkeiten aufgrund von Schwankungen des Dampfdrucks, der Keimbildung und der Wachstumsraten während der Umwandlung von Gas in Partikel.Dies führt zu einer heterogenen Zusammensetzung der Partikel, was ein erheblicher Nachteil sein kann, wenn die Einheitlichkeit entscheidend ist.
-
Umwelt- und Sicherheitsaspekte:
- Die Nebenprodukte der CVD sind oft giftig und korrosiv und müssen neutralisiert werden, was sowohl problematisch als auch kostspielig sein kann.Dies trägt zu den Gesamtkosten und der Umweltbelastung des Verfahrens bei.
-
Beschränkungen bei der Beschichtung größerer Flächen:
- Die Größe der bei der CVD verwendeten Vakuumkammer ist begrenzt, was die Beschichtung größerer Flächen erschwert.Dies kann bei Anwendungen, die großflächige Beschichtungen erfordern, eine erhebliche Einschränkung darstellen.
-
Alles-oder-nichts-Verfahren:
- CVD ist ein Alles-oder-Nichts-Verfahren, d. h. es ist schwierig, ein Material teilweise zu beschichten.Dies kann ein Nachteil sein, wenn eine selektive Beschichtung erforderlich ist.
-
Herausforderungen der Vor-Ort-Beschichtung:
- CVD kann in der Regel nicht vor Ort durchgeführt werden, sondern muss an ein Beschichtungszentrum geliefert werden.Dies kann unpraktisch und kostspielig sein, insbesondere bei großen oder komplexen Teilen, die transportiert werden müssen.
-
Wirtschaftliche Erwägungen:
- CVD ist zwar relativ wirtschaftlich, wenn es um die gleichzeitige Beschichtung zahlreicher Teile geht, aber die Gesamtkosten können aufgrund des Bedarfs an Spezialausrüstung, Sicherheitsmaßnahmen und Abfallneutralisierung hoch sein.
Zusammenfassend lässt sich sagen, dass CVD zwar viele Vorteile bietet, aber auch viele Nachteile, wie z. B. hohe Betriebstemperaturen, der Bedarf an giftigen Vorläufersubstanzen, Probleme bei der Synthese von Mehrkomponentenmaterialien sowie Umwelt- und Sicherheitsbedenken.Diese Faktoren müssen bei der Wahl von CVD als Verfahren zur Dünnschichtabscheidung sorgfältig berücksichtigt werden.Weitere Informationen über verwandte Verfahren finden Sie unter Kurzweg-Vakuumdestillation .
Zusammenfassende Tabelle :
Benachteiligung | Beschreibung |
---|---|
Hohe Betriebstemperaturen | Begrenzt die Verwendung mit thermisch empfindlichen Substraten aufgrund von thermischer Instabilität. |
Giftige und gefährliche Vorläuferstoffe | Erfordert strenge Sicherheitsmaßnahmen und erhöht Komplexität und Kosten. |
Herausforderungen bei Multikomponenten-Materialien | Schwierigkeit, eine einheitliche Zusammensetzung aufgrund von Schwankungen des Dampfdrucks und der Wachstumsrate zu erreichen. |
Umwelt- und Sicherheitsaspekte | Toxische Nebenprodukte müssen neutralisiert werden, was die Kosten und die Umweltbelastung erhöht. |
Beschränkungen bei der Beschichtung größerer Oberflächen | Begrenzt durch die Größe der Vakuumkammer, was großflächige Beschichtungen schwierig macht. |
Alles-oder-Nichts-Verfahren | Partielle Beschichtung ist eine Herausforderung, die selektive Beschichtungsanwendungen einschränkt. |
Herausforderungen der Vor-Ort-Beschichtung | Erfordert den Transport zu Beschichtungszentren, was Unannehmlichkeiten und Kosten verursacht. |
Wirtschaftliche Erwägungen | Hohe Gesamtkosten aufgrund von Spezialausrüstung, Sicherheitsmaßnahmen und Abfallneutralisierung. |
Benötigen Sie Hilfe bei der Bewältigung der Herausforderungen von CVD? Kontaktieren Sie noch heute unsere Experten für maßgeschneiderte Lösungen!