Hochöfen sind für die Eisenerzeugung von entscheidender Bedeutung, und die Wahl der Rohstoffe wirkt sich erheblich auf ihre Effizienz und Leistung aus.Sinter ist zwar ein häufig verwendetes Material in Hochöfen, aber die Verwendung von 100 % Sinter ist aus verschiedenen technischen und betrieblichen Gründen nicht praktikabel.Sinter, ein vorverarbeitetes Eisenerzprodukt, bietet Vorteile wie verbesserte Permeabilität und geringeren Energieverbrauch.Die ausschließliche Verwendung von Sinter kann jedoch zu Problemen führen, wie z. B. einer geringeren Stabilität des Ofens, einem erhöhten Schlackenvolumen und Einschränkungen bei der Steuerung von Gasfluss und Temperatur.In der Regel wird eine ausgewogene Mischung aus Sinter, Pellets und Stückerz verwendet, um die Ofenleistung zu optimieren und einen reibungslosen Betrieb und eine hochwertige Eisenproduktion zu gewährleisten.
Die wichtigsten Punkte erklärt:
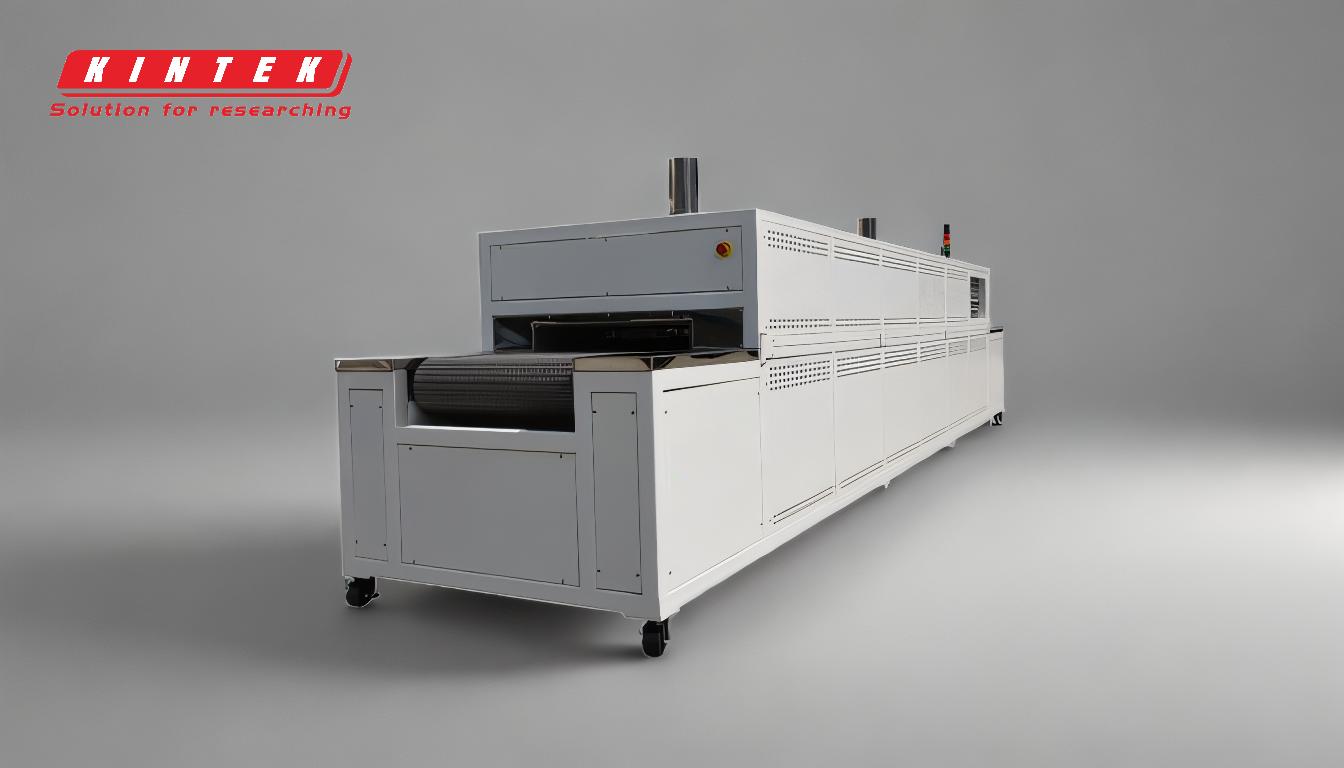
-
Ofenstabilität und Durchlässigkeit:
- Sinter verbessert die Durchlässigkeit des Hochofens und ermöglicht eine bessere Gasströmung und Wärmeverteilung.Die Verwendung von 100 % Sinter kann jedoch zu ungleichmäßiger Gasverteilung und geringerer Durchlässigkeit führen, da sich die Sinterpartikel zu dicht aneinanderlagern können.Dies kann zu Instabilitäten im Ofen und damit zu Ineffizienzen im Betrieb und möglichen Störungen führen.
- Eine Mischung aus Sinter, Pellets und Stückerz sorgt für eine gleichmäßigere Partikelgrößenverteilung, verbessert den Gasfluss und erhält die Stabilität des Ofens.
-
Schlackenbildung und Volumen:
- Sinter enthält Flussmittel wie Kalkstein, die bei der Schlackenbildung während des Eisenherstellungsprozesses helfen.Ein übermäßiger Einsatz von Sinter kann jedoch aufgrund des erhöhten Flussmittelgehalts zu einem größeren Schlackenvolumen führen.Dies erhöht nicht nur den Energiebedarf zum Schmelzen der Schlacke, sondern verringert auch die Effizienz des Ofens.
- Eine ausgewogene Mischung von Rohstoffen trägt dazu bei, das Schlackenvolumen und die Zusammensetzung zu kontrollieren, die Leistung des Ofens zu optimieren und den Energieverbrauch zu senken.
-
Temperaturregelung und Gasdurchfluss:
- Die Verwendung von 100 % Sinter kann die Kontrolle der Temperatur und des Gasflusses im Hochofen erschweren.Sinter hat im Vergleich zu anderen Materialien wie Pellets einen höheren Schmelzpunkt, was zu lokal begrenzten heißen Stellen und ungleichmäßiger Temperaturverteilung führen kann.
- Durch den Einsatz von Pellets und Stückerz kann der Ofenbetreiber die Temperatur und den Gasstrom besser regulieren und so einen gleichmäßigeren und effizienteren Eisenherstellungsprozess gewährleisten.
-
Kosten und Verfügbarkeit:
- Sinter ist zwar kosteneffizient und leicht verfügbar, aber sich ausschließlich darauf zu verlassen, ist auf lange Sicht möglicherweise nicht rentabel.Die Herstellung von Sinter erfordert einen erheblichen Energie- und Ressourcenaufwand, und seine Verfügbarkeit kann durch das Rohstoffangebot und die Produktionskapazität begrenzt sein.
- Eine diversifizierte Mischung von Rohstoffen, einschließlich Pellets und Stückerz, ermöglicht eine größere Flexibilität bei der Beschaffung und dem Kostenmanagement und gewährleistet einen nachhaltigeren und wirtschaftlicheren Betrieb.
-
Qualität des produzierten Eisens:
- Die Qualität des im Hochofen erzeugten Eisens hängt von den verwendeten Rohstoffen ab.Sinter allein bietet möglicherweise nicht die gewünschte chemische Zusammensetzung und die physikalischen Eigenschaften, die für hochwertiges Eisen erforderlich sind.
- Eine Kombination aus Sinter, Pellets und Stückerz gewährleistet eine ausgewogenere chemische Zusammensetzung, die zu hochwertigerem Eisen mit weniger Verunreinigungen führt.
-
Betriebliche Flexibilität:
- Die Verwendung einer Mischung von Rohstoffen bietet betriebliche Flexibilität, da die Ofenbetreiber die Beschickung an die sich ändernden Bedingungen und Anforderungen anpassen können.Diese Anpassungsfähigkeit ist entscheidend für die Aufrechterhaltung eines konstanten Produktionsniveaus und die Einhaltung von Qualitätsstandards.
- Die ausschließliche Verwendung von Sinter schränkt diese Flexibilität ein und macht es schwieriger, auf Schwankungen der Rohstoffqualität, der Marktnachfrage oder betriebliche Herausforderungen zu reagieren.
Zusammenfassend lässt sich sagen, dass Sinter zwar ein wertvoller Bestandteil des Hochofenbetriebs ist, die Verwendung von 100 % Sinter jedoch aufgrund seiner Auswirkungen auf die Stabilität des Ofens, das Schlackenvolumen, die Temperaturregelung, die Kosten und die Eisenqualität nicht machbar ist.Eine ausgewogene Mischung aus Sinter, Pellets und Stückerz ist für die Optimierung der Hochofenleistung und die Gewährleistung einer effizienten und qualitativ hochwertigen Eisenproduktion von entscheidender Bedeutung.
Zusammenfassende Tabelle:
Faktor | Auswirkung von 100% Sinter | Lösung mit gemischten Rohstoffen |
---|---|---|
Stabilität des Ofens | Ungleichmäßige Gasströmung, verringerte Durchlässigkeit und Instabilität | Gleichmäßige Partikelgrößenverteilung bei Sinter, Pellets und Erzklumpen erhöht die Stabilität |
Schlackenvolumen | Erhöhtes Schlackenvolumen durch höheren Flussmittelgehalt | Ausgewogene Mischung kontrolliert das Schlackenvolumen und reduziert den Energieverbrauch |
Temperaturkontrolle | Örtlich begrenzte heiße Stellen und ungleichmäßige Temperaturverteilung | Pellets und Stückerz verbessern die Temperaturregelung und den Gasfluss |
Kosten und Verfügbarkeit | Begrenzt durch Rohstoffversorgung und hohe Produktionskosten | Diversifizierte Mischung gewährleistet Kosteneffizienz und betriebliche Flexibilität |
Eisenqualität | Suboptimale chemische Zusammensetzung und physikalische Eigenschaften | Ausgewogene Mischung sorgt für höherwertiges Eisen mit weniger Verunreinigungen |
Betriebliche Flexibilität | Begrenzte Anpassungsfähigkeit an veränderte Bedingungen | Gemischte Materialien ermöglichen Anpassungen je nach Rohstoffqualität und Marktnachfrage |
Optimieren Sie die Leistung Ihres Hochofens mit der richtigen Rohstoffmischung. Kontaktieren Sie noch heute unsere Experten für maßgeschneiderte Lösungen!