Das Sintern ist ein entscheidender Schritt in der Keramikverarbeitung, da es Keramikpulver in ein vollständig dichtes, festes und dauerhaftes Material mit spezifischen mechanischen und physikalischen Eigenschaften verwandelt.Indem der Grünling hohen Temperaturen ausgesetzt wird, reduziert das Sintern die Porosität, erhöht die Dichte und verbessert die Festigkeit, so dass ein Material entsteht, das die gewünschten Leistungsanforderungen erfüllt.Dieses Verfahren ist wichtig, um komplizierte Formen zu schaffen, Materialeigenschaften zu kombinieren und eine kostengünstige Massenproduktion zu ermöglichen.Darüber hinaus gewährleistet das Sintern die Bildung einer gleichmäßigen Mikrostruktur, die für die Erzielung von Präzision, Härte und Zähigkeit in Hochleistungskeramik unerlässlich ist.Insgesamt ist das Sintern für die Herstellung hochwertiger keramischer Bauteile mit gleichbleibenden und zuverlässigen Eigenschaften unerlässlich.
Die wichtigsten Punkte erklärt:
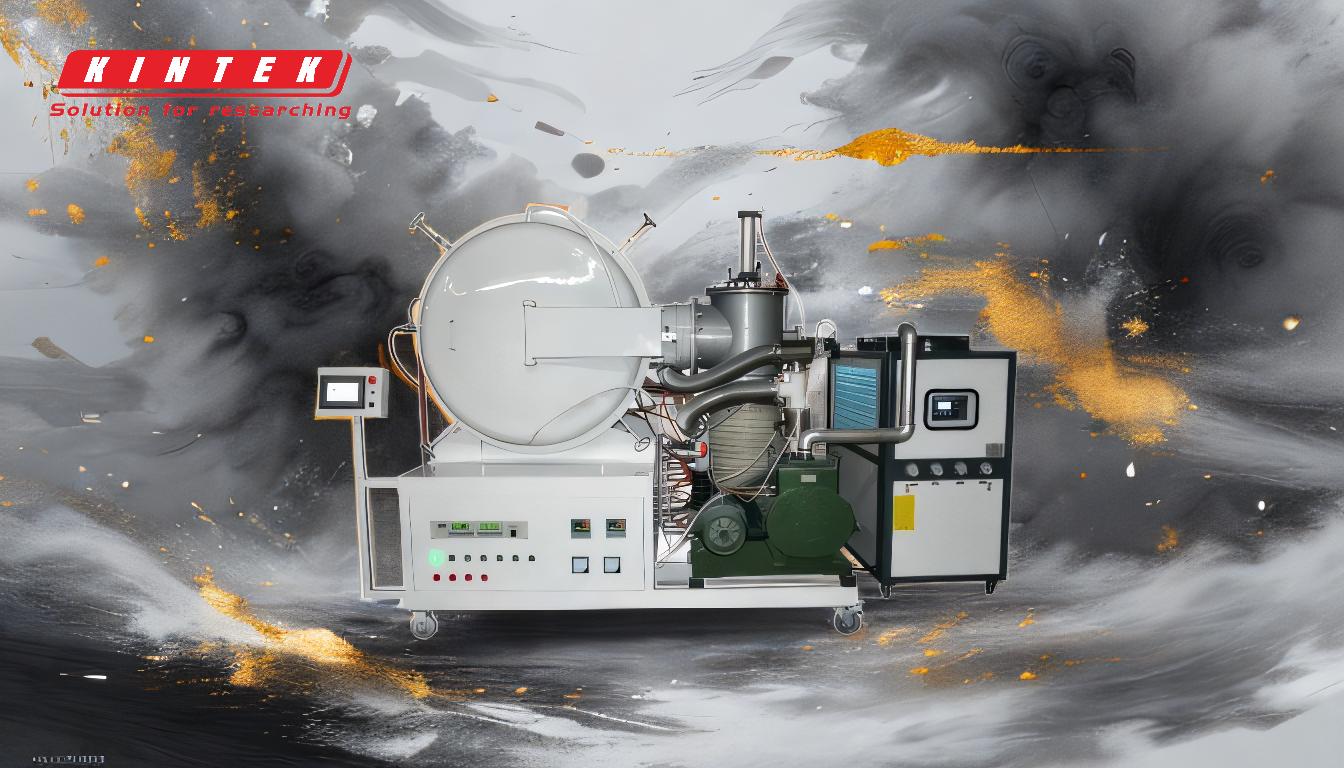
-
Umwandlung von keramischem Pulver in dichtes Material
- Beim Sintern wird Keramikpulver in polykristalline keramische Werkstoffe mit spezifischen Eigenschaften umgewandelt.
- Bei diesem Prozess kommt es zu Diffusion und Stoffübergang, was zu einer Verdichtung und zur Bildung einer einheitlichen Mikrostruktur führt.
- Das Ergebnis sind eine stabile Form und hervorragende mechanische Eigenschaften wie Härte und Zähigkeit, die für moderne keramische Anwendungen unerlässlich sind.
-
Verringerung der Porosität und Erhöhung der Dichte
- Während des Sinterns wird der Grünling bei hohen Temperaturen gebrannt, wodurch sich die Partikel verbinden und die Porosität verringert wird.
- Dieser Verdichtungsprozess erhöht die Festigkeit und Haltbarkeit des Materials und macht es für anspruchsvolle Anwendungen geeignet.
- Ein vollständig verdichtetes Teil weist die gewünschten Materialeigenschaften auf, wie z. B. Verschleiß- und Abriebfestigkeit.
-
Erzielung der gewünschten physikalischen und mechanischen Eigenschaften
- Durch das Sintern wird sichergestellt, dass das keramische Endprodukt bestimmte Leistungsanforderungen erfüllt, wie z. B. Festigkeit, Zähigkeit und Präzision.
- Durch das Verfahren wird die Mikrostruktur optimiert, was zu gleichbleibenden und zuverlässigen Eigenschaften über mehrere Produktionschargen hinweg führt.
- Dies ist besonders wichtig für Hochleistungskeramiken, die in Branchen wie Luft- und Raumfahrt, Elektronik und Medizintechnik eingesetzt werden.
-
Herstellung komplizierter Formen und Geometrien
- Das Sintern ermöglicht die Herstellung komplexer Formen und Geometrien, die mit herkömmlichen Fertigungsmethoden nur schwer zu erreichen sind.
- Diese Fähigkeit ist entscheidend für Anwendungen, die Präzision und komplizierte Designs erfordern, wie mikroelektronische Komponenten oder biomedizinische Implantate.
- Das Verfahren ermöglicht auch eine kostengünstigere Werkzeugherstellung, so dass es für die Massenproduktion wirtschaftlich ist.
-
Kombination von Materialeigenschaften
- Beim Sintern können die Eigenschaften mehrerer Werkstoffe miteinander kombiniert werden, z. B. Zähigkeit und Abriebfestigkeit.
- Diese Vielseitigkeit ermöglicht die Herstellung von maßgeschneiderten keramischen Verbundwerkstoffen für bestimmte Anwendungen.
- Durch Sintern können beispielsweise Werkstoffe hergestellt werden, die sowohl leicht als auch äußerst widerstandsfähig sind und sich ideal für Bauteile in der Automobil- oder Luftfahrtindustrie eignen.
-
Kosteneffiziente Massenproduktion
- Das Sintern ermöglicht eine schnelle Massenproduktion bei gleichbleibender Präzision und Wiederholbarkeit.
- Das Verfahren ist skalierbar und kann große Mengen keramischer Bauteile in gleichbleibender Qualität herstellen.
- Diese Effizienz senkt die Herstellungskosten und macht das Sintern zu einer attraktiven Option für industrielle Anwendungen.
-
Rolle in der Hochleistungskeramik
- Das Sintern ist der wichtigste Schritt bei der Herstellung von Hochleistungskeramik, da es die endgültigen Materialeigenschaften bestimmt.
- Das Verfahren gewährleistet die Bildung einer einheitlichen Mikrostruktur, die für die Herstellung von Hochleistungskeramik entscheidend ist.
- Durch Sintern hergestellte Hochleistungskeramik wird in Spitzentechnologien wie Halbleitern, Energiespeichersystemen und Hochtemperaturanwendungen eingesetzt.
-
Vergleich mit anderen Fertigungsverfahren
- Im Gegensatz zu herkömmlichen Verfahren ermöglicht das Sintern die Herstellung komplexer Teile mit minimalem Materialabfall.
- Das Verfahren ist im Vergleich zur maschinellen Bearbeitung oder zum Gießen energieeffizienter und umweltfreundlicher.
- Das Sintern bietet auch eine größere Flexibilität bei der Materialauswahl und der Anpassung der Eigenschaften.
Wenn die Hersteller die Bedeutung des Sinterns bei der Keramikverarbeitung verstehen, können sie den Prozess optimieren, um qualitativ hochwertige Komponenten herzustellen, die den Anforderungen der modernen Industrie entsprechen.Dieser schrittweise Ansatz stellt sicher, dass jeder Aspekt des Sinterprozesses sorgfältig kontrolliert wird, was zu Materialien mit überlegener Leistung und Zuverlässigkeit führt.
Zusammenfassende Tabelle:
Hauptnutzen | Beschreibung |
---|---|
Bildung von dichtem Material | Umwandlung von Keramikpulver in polykristalline Werkstoffe mit gleichmäßigem Gefüge. |
Verringerung der Porosität | Hohe Temperaturen verbinden die Partikel, verringern die Porosität und erhöhen die Dichte. |
Verbesserte mechanische Eigenschaften | Erzielt Festigkeit, Zähigkeit und Präzision für anspruchsvolle Anwendungen. |
Erstellung komplexer Formen | Ermöglicht komplizierte Designs für Mikroelektronik und biomedizinische Implantate. |
Kundenspezifische Materialeigenschaften | Kombiniert Eigenschaften wie Zähigkeit und Abriebfestigkeit für maßgeschneiderte Lösungen. |
Kosteneffiziente Massenproduktion | Skalierbares Verfahren für gleichbleibend hochwertige Keramikkomponenten. |
Hochleistungskeramik | Unverzichtbar für Halbleiter, Energiespeicher und Hochtemperaturanwendungen. |
Umweltfreundliche Herstellung | Minimaler Abfall, energieeffizient und flexible Materialanpassung. |
Sind Sie bereit, Ihre Keramikverarbeitung zu optimieren? Kontaktieren Sie noch heute unsere Experten um mehr über Sinterlösungen zu erfahren!