Sinterteile werden in einem mehrstufigen Verfahren hergestellt, bei dem pulverförmige Werkstoffe in feste, haltbare Komponenten verwandelt werden.Das Verfahren umfasst in der Regel die Herstellung einer Pulvermischung, die Verdichtung in die gewünschte Form und das anschließende Sintern bei hohen Temperaturen, um die Partikel miteinander zu verbinden.Diese Methode wird häufig für Metalle, Keramik und andere Werkstoffe eingesetzt und bietet eine präzise Kontrolle über die Materialeigenschaften und komplexe Geometrien.Der Sinterprozess gewährleistet, dass das Endprodukt strukturelle Integrität, geringere Porosität und verbesserte mechanische Eigenschaften aufweist.Im Folgenden werden die wichtigsten Schritte und ihre Bedeutung im Detail erläutert.
Die wichtigsten Punkte werden erklärt:
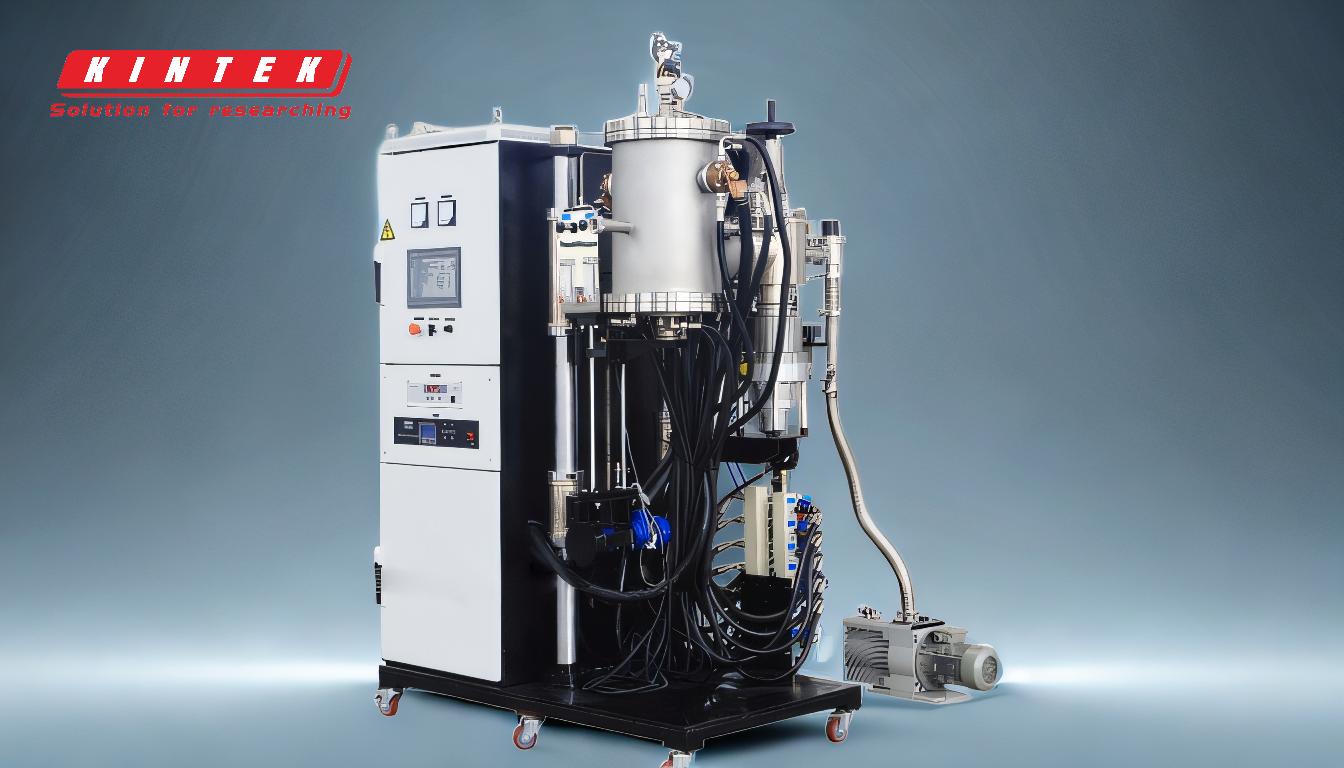
-
Pulveraufbereitung und Mischen
- Der Prozess beginnt mit der Aufbereitung von Rohstoffen in Pulverform.Diese Pulver werden häufig mit Zusatzstoffen wie Bindemitteln, Schmiermitteln oder Haftvermittlern gemischt, um die Fließfähigkeit, die Verdichtung und das Sinterverhalten zu verbessern.
- Bei Metallen kann das Pulver legiert oder gemischt werden, um bestimmte mechanische oder thermische Eigenschaften zu erzielen.Bei Keramik wird das Pulver häufig kalibriert, um die Einheitlichkeit der Partikelgröße und -zusammensetzung zu gewährleisten.
- Dieser Schritt ist von entscheidender Bedeutung, da sich die Qualität des Pulvers direkt auf die Dichte, Festigkeit und Maßhaltigkeit des Endprodukts auswirkt.
-
Verdichtung des Pulvers
- Das gemischte Pulver wird dann mit Hilfe von Hochdruckwerkzeugen, wie z. B. hydraulischen Pressen oder Matrizenformen, zu einem "Grünling" verdichtet.In diesem Schritt wird das Pulver in die gewünschte Form gebracht, wodurch eine kohärente, aber zerbrechliche Struktur entsteht.
- Der Verdichtungsprozess kann je nach Material bei Raumtemperatur oder mit leichter Erwärmung durchgeführt werden.Der ausgeübte Druck sorgt dafür, dass die Partikel in engem Kontakt stehen, was für eine effektive Sinterung unerlässlich ist.
- Für komplexe Formen können Techniken wie Kaltschweißen, 3D-Laserdruck oder isostatisches Pressen eingesetzt werden, um präzise Geometrien zu erzielen.
-
Sintern in einer kontrollierten Atmosphäre
- Der Grünling wird in einen Sinterofen gebracht, wo er auf eine Temperatur knapp unter dem Schmelzpunkt des Materials erhitzt wird.Durch diesen Schritt werden Diffusionsmechanismen aktiviert, wodurch sich die Partikel verbinden und verdichten.
- In einigen Fällen wird das Flüssigphasensintern (LPS) eingesetzt, bei dem sich an den Grenzflächen der Partikel eine kleine Menge Flüssigkeit bildet, die die Verdichtung beschleunigt und die Materialeigenschaften verbessert.
- Die Sinteratmosphäre (z. B. Inertgas, Vakuum oder reduzierende Umgebung) wird sorgfältig kontrolliert, um Oxidation oder Verunreinigung zu verhindern und eine gleichmäßige Erwärmung zu gewährleisten.
-
Abkühlung und Erstarrung
- Nach dem Sintern wird das Material allmählich auf Raumtemperatur abgekühlt.In diesem Schritt können sich die neu gebildeten Bindungen stabilisieren, so dass eine feste, einheitliche Masse mit geringerer Porosität und höherer mechanischer Festigkeit entsteht.
- Die Abkühlungsgeschwindigkeit kann die Mikrostruktur und die Eigenschaften des Materials, wie Härte und Zähigkeit, beeinflussen.
-
Verarbeitung nach dem Sintern
- Je nach Anwendung können gesinterte Teile weiteren Schritten wie der Bearbeitung, Oberflächenveredelung oder Montage unterzogen werden.Bei Keramiken werden häufig Diamantwerkzeuge oder Ultraschallbearbeitung eingesetzt, um präzise Abmessungen zu erzielen.
- In einigen Fällen werden gesinterte Teile metallisiert oder gelötet, um sie mit anderen Komponenten zu verbinden und ihre Funktionalität in komplexen Baugruppen zu verbessern.
-
Qualitätskontrolle und Prüfung
- Während des gesamten Prozesses werden Parameter wie Temperatur, Druck und Sinterzeit genau überwacht, um sicherzustellen, dass das Endprodukt den Spezifikationen entspricht.
- Die gesinterten Teile werden auf Eigenschaften wie Dichte, Porosität, Festigkeit und Maßhaltigkeit geprüft, um sicherzustellen, dass sie für den vorgesehenen Verwendungszweck geeignet sind.
Durch die Einhaltung dieser Schritte können Hersteller Sinterteile mit maßgeschneiderten Eigenschaften für eine Vielzahl von Anwendungen herstellen, von Automobilkomponenten bis hin zu Hochleistungskeramik in der Elektronik und Luft- und Raumfahrt.Das Sinterverfahren bietet eine kostengünstige und vielseitige Methode zur Herstellung von Hochleistungswerkstoffen mit komplexen Formen und präzisen Toleranzen.
Zusammenfassende Tabelle:
Schritt | Wichtige Details |
---|---|
Puderzubereitung | Rohstoffe in Pulverform, gemischt mit Zusatzstoffen zur Verbesserung der Eigenschaften. |
Verdichtung des Pulvers | Hochdruckwerkzeuge formen das Pulver zu einem "Grünling" mit präziser Geometrie. |
Sintern | Erhitzen unter den Schmelzpunkt in kontrollierter Atmosphäre, um die Partikel zu verbinden. |
Abkühlung und Verfestigung | Die allmähliche Abkühlung stabilisiert die Verbindungen, verringert die Porosität und erhöht die Festigkeit. |
Verarbeitung nach dem Sintern | Zusätzliche Schritte wie z. B. maschinelle Bearbeitung oder Oberflächenveredelung für endgültige Abmessungen. |
Qualitätskontrolle | Prüfung auf Dichte, Porosität, Festigkeit und Maßhaltigkeit. |
Erfahren Sie, wie Sinterteile Ihren Fertigungsprozess verbessern können. Kontaktieren Sie unsere Experten noch heute !