Die Partikelgröße spielt eine entscheidende Rolle im Sinterprozess und beeinflusst die Verdichtung, die mechanischen Eigenschaften und die Gesamtqualität des Endprodukts.Kleinere Partikel verbessern im Allgemeinen die Sinterung aufgrund ihrer höheren Oberflächenenergie und der größeren Antriebskraft für den Materialtransport, was zu einer besseren Verdichtung und geringeren Porosität führt.Zu feine Partikel können jedoch auch Probleme mit sich bringen, wie Agglomeration und Schwierigkeiten bei der Handhabung.Die Beziehung zwischen Partikelgröße und Sinterung ist komplex und umfasst Faktoren wie Oberflächenenergie, Diffusionsraten und Kornwachstum.Das Verständnis dieser Beziehung ist entscheidend für die Optimierung der Sinterbedingungen, um die gewünschten Materialeigenschaften zu erzielen.
Die wichtigsten Punkte werden erklärt:
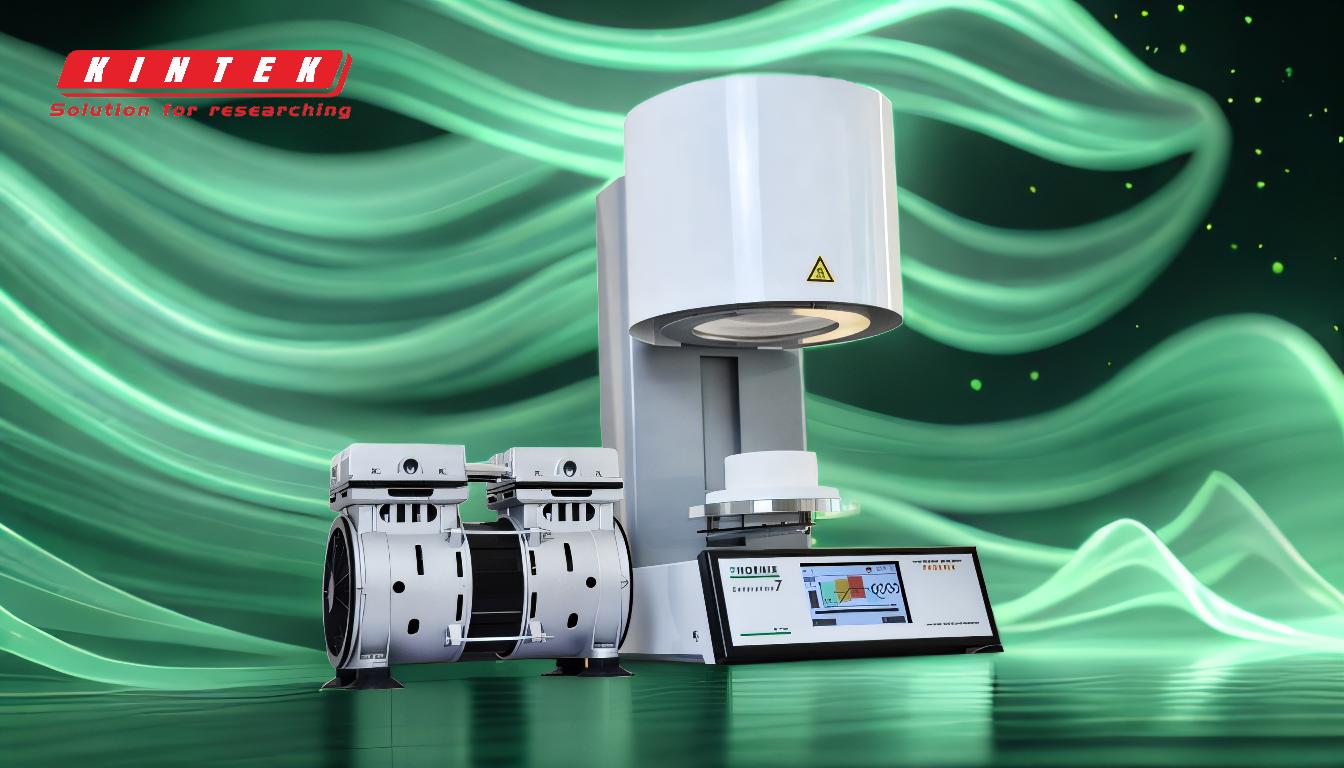
-
Oberflächenenergie und Antriebskraft:
- Kleinere Partikel haben ein größeres Verhältnis von Oberfläche zu Volumen, was zu einer höheren Oberflächenenergie führt.
- Diese höhere Oberflächenenergie bietet eine größere Antriebskraft für den Materialtransfer während des Sinterns und fördert die Verdichtung.
- Die erhöhte Oberflächenenergie beschleunigt auch Diffusionsmechanismen wie Oberflächendiffusion und Korngrenzendiffusion, die für die Sinterung entscheidend sind.
-
Verdichtung und Porosität:
- Kleinere Partikel ermöglichen eine bessere Partikelpackung und verringern die anfängliche Porosität des Grünlings.
- Während des Sinterns führen die verbesserten Materialtransportmechanismen bei feinen Partikeln zu einer effektiveren Porenbeseitigung und Verdichtung.
- Sind die Partikel jedoch zu fein, können sie agglomerieren, was zu einer ungleichmäßigen Verdichtung und der Bildung großer Poren führt.
-
Wachstum der Körner:
- Feine Partikel neigen dazu, während des Sinterns ein schnelles Kornwachstum zu fördern, da sie eine hohe Oberflächenenergie und erhöhte Diffusionsraten aufweisen.
- Ein gewisses Kornwachstum ist zwar notwendig, um starke Bindungen zwischen den Partikeln zu erreichen, ein übermäßiges Kornwachstum kann jedoch die mechanischen Eigenschaften beeinträchtigen, da große Körner mit schwächeren Grenzen entstehen.
- Die Steuerung der Partikelgröße und der Sinterparameter ist entscheidend für das Gleichgewicht zwischen Verdichtung und Kornwachstum.
-
Sintertemperatur und Sinterzeit:
- Kleinere Partikel erfordern niedrigere Sintertemperaturen und kürzere Zeiten aufgrund ihrer höheren Reaktivität und schnelleren Diffusionsraten.
- Dies kann zu Energieeinsparungen und einer verbesserten Prozesseffizienz führen.
- Es muss jedoch darauf geachtet werden, dass eine Überhitzung vermieden wird, die zu übermäßigem Kornwachstum oder unerwünschten Phasenumwandlungen führen kann.
-
Herausforderungen bei feinen Partikeln:
- Feine Partikel neigen eher zur Agglomeration, was eine gleichmäßige Verdichtung behindern und zu Mängeln im Endprodukt führen kann.
- Die Handhabung und Verarbeitung von feinen Pulvern kann aufgrund ihrer größeren Oberfläche und Reaktivität eine Herausforderung darstellen und erfordert spezielle Geräte und Techniken.
- Die größere Oberfläche macht feine Partikel auch anfälliger für Verunreinigungen, die das Sinterverhalten und die endgültigen Eigenschaften beeinträchtigen können.
-
Praktische Anwendungen:
- In der Keramiktechnologie werden häufig feinkörnige Materialien verwendet, um Produkte mit hoher Dichte und hoher Festigkeit herzustellen.
- In der Pulvermetallurgie ist die Kontrolle der Partikelgrößenverteilung entscheidend für die Herstellung von Bauteilen mit präzisen Abmessungen und mechanischen Eigenschaften.
- Moderne Sintertechniken wie das Spark-Plasma-Sintern (SPS) und das heißisostatische Pressen (HIP) machen sich die Vorteile feiner Partikel zunutze, um hervorragende Materialeigenschaften zu erzielen.
Zusammenfassend lässt sich sagen, dass die Partikelgröße einen erheblichen Einfluss auf die Sinterung hat, da sie die Oberflächenenergie, die Verdichtung, das Kornwachstum und die allgemeinen Materialeigenschaften beeinflusst.Während kleinere Partikel im Allgemeinen die Sinterung verbessern, ist eine sorgfältige Kontrolle der Partikelgröße und der Sinterparameter notwendig, um den Prozess zu optimieren und die gewünschten Ergebnisse zu erzielen.Das Verständnis dieser Zusammenhänge ist für Materialwissenschaftler und Ingenieure, die in Bereichen wie Keramik, Pulvermetallurgie und fortschrittliche Fertigung arbeiten, von entscheidender Bedeutung.
Zusammenfassende Tabelle:
Aspekt | Auswirkungen kleinerer Partikel | Herausforderungen |
---|---|---|
Oberflächenenergie | Ein höheres Oberflächen-Volumen-Verhältnis erhöht die Oberflächenenergie und die Antriebskraft für den Materialtransport | Agglomerationsrisiken und Schwierigkeiten bei der Handhabung |
Verdichtung | Bessere Packung der Partikel und Beseitigung von Poren, was zu einer besseren Verdichtung führt | Ungleichmäßige Verdichtung, wenn Partikel agglomerieren |
Wachstum der Körner | Fördert schnelles Kornwachstum und verbessert die Bindungen zwischen den Partikeln | Übermäßiges Kornwachstum kann die mechanischen Eigenschaften schwächen |
Sintertemperatur | Niedrigere Temperaturen und kürzere Zeiten sind erforderlich, was die Effizienz verbessert | Überhitzung kann zu Phasenumwandlungen führen |
Praktische Anwendungen | Einsatz in der Keramik und Pulvermetallurgie für Produkte mit hoher Dichte und hoher Festigkeit | Erfordert spezielle Anlagen und Techniken für die Handhabung feiner Partikel |
Sind Sie bereit, Ihren Sinterprozess zu optimieren? Kontaktieren Sie noch heute unsere Experten für maßgeschneiderte Lösungen!