Das Sintern ist ein wichtiger Prozess in der Werkstoffkunde, der die Dichte eines Materials durch Veränderung seiner Mikrostruktur erheblich beeinflusst.Durch die Anwendung von Hitze und Druck verringert das Sintern die Porosität und erhöht die Festigkeit und Haltbarkeit des Materials.Der Prozess beeinflusst die Korngröße, die Porengröße und die Verteilung der Korngrenzen, die für die endgültige Dichte des Materials ausschlaggebend sind.Das Sintern ermöglicht eine präzise Kontrolle dieser mikrostrukturellen Merkmale, was zu gleichmäßigeren und hochwertigeren Produkten führt.Außerdem ist es im Vergleich zum Schmelzen ein energieeffizientes und umweltfreundliches Verfahren, was es zu einer bevorzugten Wahl in der Fertigung macht.
Die wichtigsten Punkte werden erklärt:
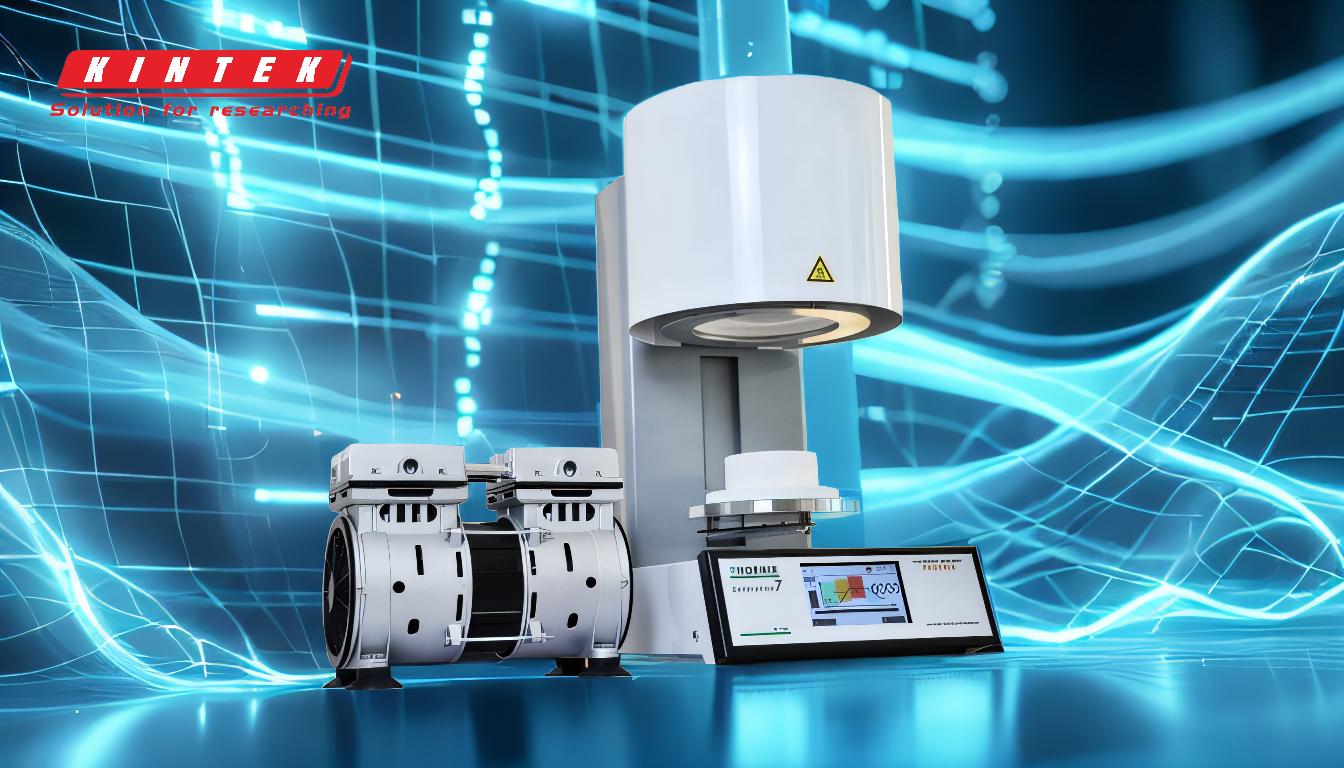
-
Definition und Mechanismus des Sinterns:
- Das Sintern ist ein Verfahren, bei dem Materialien durch Anwendung von Hitze und Druck miteinander verbunden werden, ohne sie zu schmelzen.
- Dabei wird die Oberflächenenergie der Partikel verringert, so dass sie sich auf atomarer Ebene verbinden.
-
Auswirkungen auf die Mikrostruktur:
- Korngröße:Die Sinterung beeinflusst die Größe der Körner im Material.Größere Körner können die Anzahl der Korngrenzen verringern, was die Dichte beeinflussen kann.
- Porengröße:Der Prozess reduziert die Größe und Anzahl der Poren im Material, was zu einer erhöhten Dichte führt.
- Korngrenzenverteilung:Das Sintern verändert die Form und Verteilung der Korngrenzen, was sich auf die Dichte des Materials auswirken kann.
-
Auswirkung auf die Dichte:
- Porositätsreduzierung:Durch die Minimierung der Porosität erhöht das Sintern die Gesamtdichte des Materials.
- Materialverfestigung:Das Verfahren verfestigt das Material und macht es gleichmäßiger und dichter.
- Vollständig verdichtete Teile:Das Sintern ist eine wesentliche Voraussetzung für die Herstellung völlig dichter Teile, die die gewünschten Materialeigenschaften wie Festigkeit und Haltbarkeit aufweisen.
-
Kontrollierte Variablen beim Sintern:
- Temperatur:Die Temperatur während des Sinterns ist entscheidend, da sie den Dampfdruck und die Geschwindigkeit, mit der sich die Partikel verbinden, beeinflusst.
- Ausgangskorngröße:Die Größe der Ausgangskörner kann sich auf die endgültige Dichte auswirken, da sich kleinere Körner dichter zusammenlagern können.
-
Vorteile des Sinterns:
- Stärke und Langlebigkeit:Durch die Verringerung der Porosität und die Verbesserung des Gefüges verbessert das Sintern die mechanischen Eigenschaften des Materials.
- Konsistenz:Das Verfahren ermöglicht eine bessere Kontrolle, was zu konsistenteren und zuverlässigeren Produkten führt.
- Energie-Effizienz:Das Sintern benötigt weniger Energie als das Schmelzen und ist damit eine nachhaltigere Option.
-
Anwendungen und Bedeutung:
- Herstellung:Das Sintern ist bei der Herstellung von Keramiken und Metallen weit verbreitet, um Materialien mit hoher Dichte und hervorragenden Eigenschaften zu erhalten.
- Umweltauswirkungen:Der geringere Energiebedarf des Sinterns im Vergleich zum Schmelzen macht es zu einer umweltfreundlichen Wahl bei der Materialverarbeitung.
Zusammenfassend lässt sich sagen, dass das Sintern eine entscheidende Rolle bei der Bestimmung der Dichte von Werkstoffen spielt, indem es deren Mikrostruktur beeinflusst.Durch die kontrollierte Anwendung von Wärme und Druck verringert das Sintern die Porosität, verbessert die Korn- und Porengrößenverteilung und führt letztlich zu Werkstoffen mit höherer Dichte, verbesserter Festigkeit und längerer Lebensdauer.Dies macht das Sintern zu einem unverzichtbaren Verfahren bei der Herstellung von Hochleistungswerkstoffen.
Zusammenfassende Tabelle:
Aspekt | Einfluss des Sinterns |
---|---|
Korngröße | Beeinflusst die Dichte durch Veränderung der Korngrenzen; größere Körner verringern die Grenzdichte. |
Porengröße | Verringert die Porosität, was zu einer höheren Materialdichte führt. |
Korngrenzenverteilung | Erhöht die Packungsdichte durch Optimierung der Korngrenzenform und -verteilung. |
Verringerung der Porosität | Minimiert Hohlräume und erhöht die Gesamtdichte. |
Energie-Effizienz | Benötigt weniger Energie als das Schmelzen und ist daher umweltfreundlich. |
Anwendungen | Weit verbreitet in Keramik und Metallen für hochdichte, leistungsstarke Materialien. |
Entdecken Sie, wie das Sintern Ihre Materialeigenschaften optimieren kann - Kontaktieren Sie noch heute unsere Experten um mehr zu erfahren!