Selektives Wärmesintern (SHS) ist eine 3D-Drucktechnologie, bei der ein Thermodruckkopf verwendet wird, um pulverförmiges Material selektiv Schicht für Schicht zu verschmelzen.Es weist Ähnlichkeiten mit dem Selektiven Lasersintern (SLS) auf, unterscheidet sich aber in der Wärmequelle.SHS bietet Vorteile wie Kosteneffizienz, schnellere Produktion und die Möglichkeit, komplexe Geometrien zu erzeugen.Es gibt jedoch auch Einschränkungen, darunter Materialbeschränkungen, eine geringere Auflösung im Vergleich zu anderen Verfahren und potenzielle Bedenken hinsichtlich der Materialstärke und -dichte.Im Folgenden werden die wichtigsten Vor- und Nachteile von SHS im Detail erläutert.
Die wichtigsten Punkte werden erklärt:
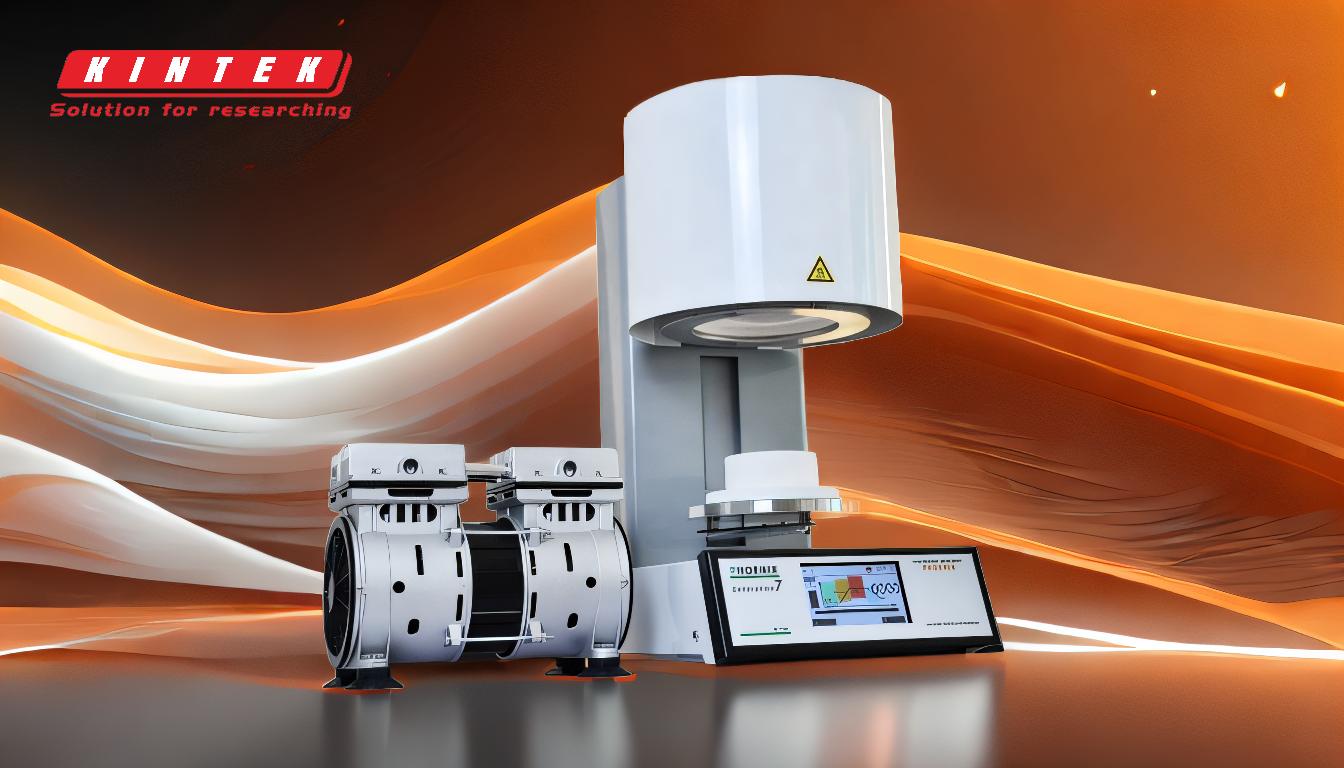
-
Vorteile des Selektiven Wärmesinterns (SHS):
-
Kosteneffizienz:
- SHS ist im Allgemeinen kostengünstiger als SLS, da ein Thermodruckkopf anstelle eines teuren Lasers verwendet wird.Dadurch werden sowohl die Anfangsinvestitionen als auch die Betriebskosten gesenkt.
- Die bei der SHS verwendeten Materialien sind häufig preiswerter als die für die SLS benötigten, was sie zu einer budgetfreundlichen Option für kleine bis mittlere Produktionsmengen macht.
-
Schnellere Produktion:
- Der thermische Druckkopf des SHS kann im Vergleich zu einem Laser größere Bereiche gleichzeitig abdecken, was ein schnelleres schichtweises Sintern ermöglicht.Dadurch eignet sich das SHS für das Rapid Prototyping und die Kleinserienfertigung.
-
Komplexe Geometrien:
- Wie SLS kann auch SHS komplizierte und funktionelle Formen herstellen, die mit herkömmlichen Fertigungsmethoden nur schwer oder gar nicht zu realisieren sind.Dies ist besonders vorteilhaft für Branchen, die kundenspezifische oder komplexe Teile benötigen.
-
Leichte Bedienbarkeit:
- SHS-Systeme sind oft einfacher zu bedienen als SLS-Maschinen, so dass weniger hochqualifizierte Bediener erforderlich sind.Dies senkt die Arbeitskosten und macht die Technologie für kleinere Unternehmen leichter zugänglich.
-
Kosteneffizienz:
-
Nachteile des Selektiven Wärmesinterns (SHS):
-
Materialbeschränkungen:
- SHS ist in der Regel auf bestimmte thermoplastische Materialien beschränkt, z. B. auf Nylon basierende Pulver.Dies schränkt die Anwendung im Vergleich zum SLS ein, das mit einer breiteren Palette von Materialien, einschließlich Metallen und Keramiken, arbeiten kann.
- Nicht alle Materiallieferanten unterstützen SHS, was auf Bedenken hinsichtlich der Materialkompatibilität, Festigkeit oder Dichte hinweisen kann.
-
Geringere Auflösung:
- Beim SHS-Verfahren werden im Allgemeinen Teile mit geringerer Auflösung und Oberflächengüte als beim SLS-Verfahren hergestellt.Dies ist auf die größere Punktgröße des Thermodruckkopfes im Vergleich zum Laserstrahl zurückzuführen.
- Nachbearbeitungen wie Schleifen oder Polieren können erforderlich sein, um eine glattere Oberfläche zu erzielen, was den Produktionsprozess zeit- und kostenaufwändiger macht.
-
Bedenken hinsichtlich Festigkeit und Dichte:
- Einige Studien deuten darauf hin, dass mit SHS hergestellte Teile im Vergleich zu SLS- oder Hochgeschwindigkeitssintern hergestellten Teilen eine etwas geringere Dichte und Festigkeit aufweisen können.Dies könnte ihre Verwendung in hochbelasteten Anwendungen einschränken.
-
Begrenzte Branchenakzeptanz:
- SHS ist nicht so weit verbreitet wie SLS oder andere 3D-Drucktechnologien, was zu weniger Ressourcen, Unterstützung und Materialoptionen für die Nutzer führen kann.
-
Materialbeschränkungen:
-
Vergleich mit anderen Sinterverfahren:
-
Selektives Laser-Sintern (SLS):
- SLS bietet eine höhere Auflösung und die Möglichkeit, mit einer breiteren Palette von Materialien, einschließlich Metallen und Keramiken, zu arbeiten.Es ist jedoch wesentlich teurer und erfordert qualifizierte Bediener.
-
Hochgeschwindigkeits-Sintern:
- Beim Hochgeschwindigkeitssintern können im Vergleich zum SHS eine etwas höhere Dichte und Festigkeit erreicht werden.Es wird jedoch nicht allgemein von den Materiallieferanten befürwortet, was auf mögliche Einschränkungen oder Bedenken hinweist.
-
Pulvermetallurgie:
- Die Pulvermetallurgie ist kostengünstiger für die Großserienproduktion von Teilen mittlerer Komplexität, kann aber aufgrund der Reibung zwischen Pulver und Werkzeug zu ungleichmäßigen Komponenten führen.
-
Selektives Laser-Sintern (SLS):
-
Anwendungen und Eignung:
- SHS eignet sich gut für Rapid Prototyping, Kleinserienfertigung und Anwendungen, bei denen Kosten und Geschwindigkeit Vorrang vor hoher Auflösung oder Materialvielfalt haben.
- Es ist möglicherweise nicht ideal für Branchen, die hochfeste, hochdichte Teile oder eine große Vielfalt an Materialoptionen benötigen.
Zusammenfassend lässt sich sagen, dass das selektive Wärmesintern eine kostengünstige und effiziente Lösung für die Herstellung komplexer Geometrien bietet, insbesondere bei der Herstellung von Prototypen und kleinen Serien.Allerdings können die Materialbeschränkungen, die geringere Auflösung und die potenziellen Bedenken hinsichtlich der Festigkeit und Dichte der Teile den Einsatz bei bestimmten Anwendungen einschränken.Das Verständnis dieser Kompromisse ist für die Auswahl des richtigen Sinterverfahrens für bestimmte Anforderungen von entscheidender Bedeutung.
Zusammenfassende Tabelle:
Blickwinkel | Vorteile | Nachteile |
---|---|---|
Kosten | Erschwinglicher als SLS; niedrigere Anfangs- und Betriebskosten. | Begrenzt auf bestimmte Materialien; höhere Nachbearbeitungskosten. |
Geschwindigkeit | Schnellere Produktion aufgrund der größeren thermischen Druckkopfabdeckung. | Geringere Auflösung im Vergleich zu SLS; erfordert Nachbearbeitung für glattere Oberflächen. |
Komplexität | Ermöglicht die Herstellung komplizierter und funktioneller Formen. | Die Teile können eine geringere Dichte und Festigkeit aufweisen, was Anwendungen mit hoher Beanspruchung einschränkt. |
Leichtere Handhabung | Einfachere Bedienung; geringerer Bedarf an Fachkräften. | Begrenzte Akzeptanz in der Industrie; weniger Material- und Supportoptionen. |
Suchen Sie nach der richtigen 3D-Drucklösung für Ihre Bedürfnisse? Kontaktieren Sie uns noch heute um mehr über Selektives Wärmesintern zu erfahren!