Das Sintern von Keramik ist ein wichtiger Prozess in der Materialwissenschaft, der Keramikpulver in dichte, feste und funktionale Komponenten verwandelt.Bei diesem Verfahren werden keramische Pulver unter ihren Schmelzpunkt erhitzt, wodurch sich die Partikel verbinden und verdichten, was ihre mechanischen, thermischen und elektrischen Eigenschaften verbessert.Zu den Vorteilen des keramischen Sinterns gehören eine höhere Festigkeit, eine geringere Porosität, eine verbesserte thermische und elektrische Leitfähigkeit und die Möglichkeit, mit hochschmelzenden Materialien zu arbeiten.Darüber hinaus bietet das Sintern eine präzise Kontrolle über die Materialeigenschaften, was es zu einer vielseitigen und effizienten Herstellungsmethode macht.Im Folgenden werden die wichtigsten Vorteile des keramischen Sinterns im Detail erläutert.
Die wichtigsten Punkte erklärt:
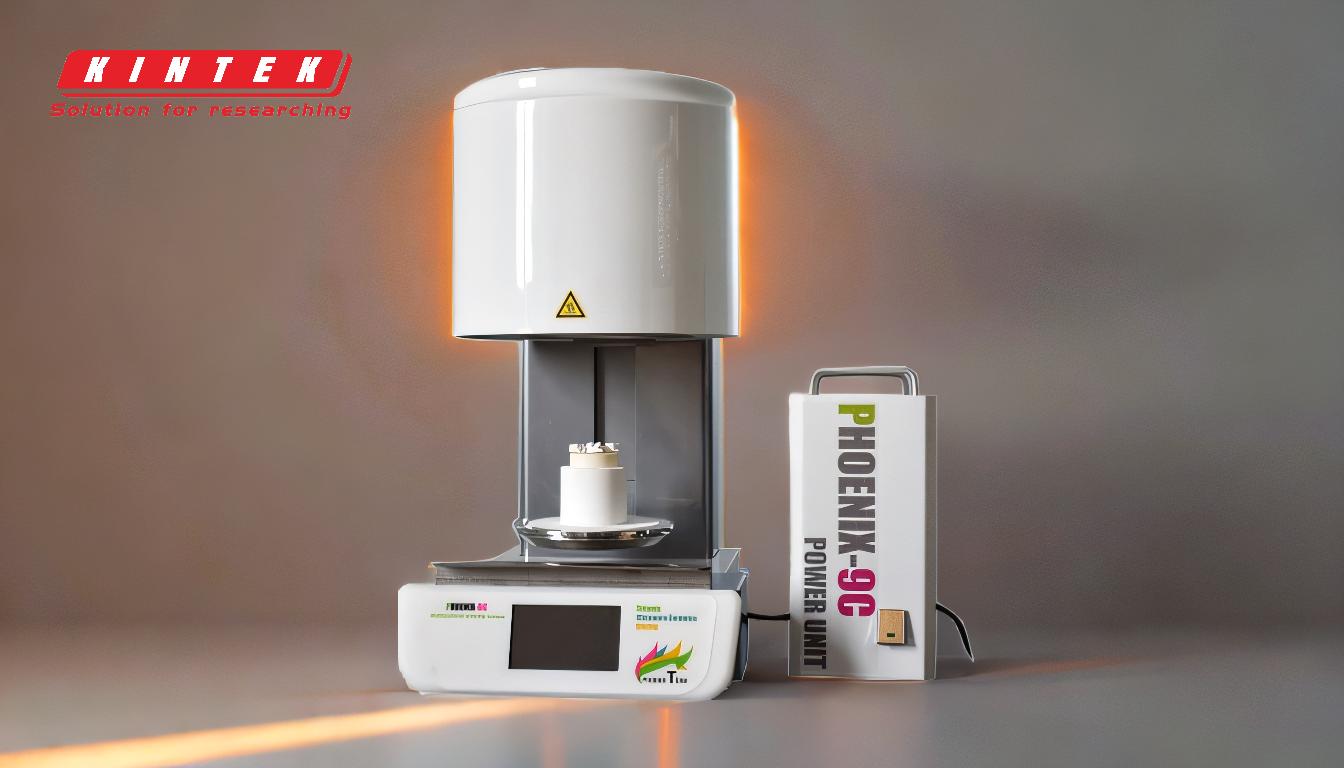
-
Verbesserte mechanische Eigenschaften
- Das Sintern verbessert die Festigkeit, Härte und Verschleißfestigkeit von keramischen Werkstoffen erheblich.
- Während des Sinterns verbinden sich die Partikel durch Diffusionsmechanismen, wodurch eine dichte und kohäsive Struktur entsteht.
- Dies führt zu Bauteilen mit hervorragender mechanischer Integrität, die sich für Hochleistungsanwendungen wie Turbinenschaufeln und Lager eignen.
-
Geringere Porosität
- Durch das Sintern wird die Porosität von keramischen Werkstoffen minimiert, was zu dichteren und haltbareren Bauteilen führt.
- Eine geringere Porosität verbessert Eigenschaften wie Festigkeit, Wärmeleitfähigkeit und elektrische Leitfähigkeit.
- Eine kontrollierte Porosität kann auch für spezielle Anwendungen wie Filter oder Katalysatoren erreicht werden, bei denen eine Gasabsorptionsfähigkeit erforderlich ist.
-
Verbesserte thermische und elektrische Leitfähigkeit
- Durch den Verdichtungsprozess während des Sinterns wird die thermische und elektrische Leitfähigkeit der Keramik verbessert.
- Dies ist besonders vorteilhaft für Anwendungen wie Wärmerohre, elektronische Komponenten und Wärmemanagementsysteme.
-
Verarbeitung von Materialien mit hohem Schmelzpunkt
- Das Sintern ermöglicht die Verarbeitung von Keramiken mit extrem hohen Schmelzpunkten, die mit herkömmlichen Schmelzverfahren nur schwer zu bearbeiten sind.
- Dies macht das Sintern zu einer idealen Methode für die Herstellung von Komponenten aus Hochleistungskeramik wie Aluminiumoxid, Zirkoniumdioxid und Siliziumkarbid.
-
Präzision und Kontrolle bei der Herstellung
- Das Sintern bietet ein hohes Maß an Kontrolle über die Materialeigenschaften, einschließlich Korngröße, Porosität und Dichte.
- Dies gewährleistet eine konsistente und wiederholbare Produktion von hochwertigen Komponenten.
- Das Verfahren ermöglicht auch die Herstellung von nahezu netzförmigen Objekten, wodurch sich der Bedarf an zusätzlicher Bearbeitung verringert.
-
Energieeffizienz und Umweltvorteile
- Das Sintern benötigt im Vergleich zu Schmelzverfahren weniger Energie und ist damit eine umweltfreundlichere Option.
- Das Verfahren macht den Einsatz von Schmiermitteln überflüssig und reduziert den Oberflächensauerstoff, was ebenfalls zur Nachhaltigkeit des Verfahrens beiträgt.
-
Vielseitigkeit der Anwendungen
- Sinterkeramik wird in einer Vielzahl von Anwendungen eingesetzt, darunter Schmuck, Lager, Wärmerohre und Gewehrschalen.
- Dank der Möglichkeit, die Materialeigenschaften individuell anzupassen, eignet sich das Sintern sowohl für strukturelle als auch für funktionelle Anwendungen.
-
Herstellung komplexer Formen
- Das Sintern ermöglicht die Herstellung komplexer Formen mit hoher Präzision, die mit anderen Fertigungsmethoden nur schwer zu erreichen ist.
- Dies ist besonders vorteilhaft für Branchen, die komplizierte Komponenten benötigen, wie die Luft- und Raumfahrt und medizinische Geräte.
-
Verbesserte Transluzenz
- Bei bestimmten Keramiken kann das Sintern die Lichtdurchlässigkeit verbessern, so dass sie sich für Anwendungen wie optische Komponenten und Zahnersatz eignen.
-
Kosteneffizienz
- Durch die Verringerung des Nachbearbeitungsbedarfs und die Möglichkeit der endkonturnahen Fertigung senkt das Sintern die Produktionskosten.
- Die Möglichkeit, schwierige Werkstoffe zu verarbeiten und Hochleistungseigenschaften zu erzielen, trägt ebenfalls zur Kosteneffizienz des Verfahrens bei.
Zusammenfassend lässt sich sagen, dass das keramische Sintern ein äußerst vorteilhaftes Verfahren ist, das die Materialeigenschaften verbessert, Präzision bei der Herstellung bietet und eine breite Palette von Anwendungen unterstützt.Seine Fähigkeit, die Festigkeit zu verbessern, die Porosität zu verringern und mit hochschmelzenden Werkstoffen zu arbeiten, macht es in der fortgeschrittenen Fertigung und der Materialwissenschaft unverzichtbar.
Zusammenfassende Tabelle:
Vorteil | Beschreibung |
---|---|
Verbesserte mechanische Eigenschaften | Verbessert Festigkeit, Härte und Verschleißfestigkeit von Hochleistungskomponenten. |
Reduzierte Porosität | Minimiert die Porosität und verbessert die Haltbarkeit und Leitfähigkeit. |
Verbesserte thermische/elektrische Leitfähigkeit | Verbessert die Leistung von Wärmerohren und elektronischen Komponenten. |
Materialien mit hohem Schmelzpunkt | Ermöglicht die Verarbeitung von Hochleistungskeramiken wie Aluminiumoxid und Siliziumkarbid. |
Präzision bei der Herstellung | Bietet Kontrolle über Korngröße, Porosität und Dichte für gleichbleibende Ergebnisse. |
Energie-Effizienz | Benötigt weniger Energie und reduziert die Umweltbelastung im Vergleich zum Schmelzen. |
Vielfältige Anwendungen | Geeignet für Schmuck, Lager, Wärmerohre und vieles mehr. |
Herstellung komplexer Formen | Zur Herstellung komplizierter Komponenten für die Luft- und Raumfahrt und die medizinische Industrie. |
Verbesserte Transluzenz | Verbessert die Lichtdurchlässigkeit für optische und zahnmedizinische Anwendungen. |
Kosteneffizienz | Reduziert die Nachbearbeitung und senkt die Produktionskosten. |
Erschließen Sie das Potenzial der keramischen Sinterung für Ihre Projekte. Kontaktieren Sie noch heute unsere Experten um mehr zu erfahren!