Sputtern und thermisches Verdampfen sind beides weit verbreitete Verfahren zur Abscheidung von Dünnschichten, doch bietet das Sputtern gegenüber dem thermischen Verdampfen mehrere Vorteile. Dazu gehören eine bessere Haftung, eine präzisere Kontrolle über den Abscheidungsprozess und die Möglichkeit, die Zusammensetzung des Ausgangsmaterials beizubehalten. Darüber hinaus bietet das Sputtern einen gleichmäßigeren und realistischeren Metalleffekt, eine größere Farbvielfalt und eine bessere Kompatibilität mit einer breiteren Palette von Materialien. Während die thermische Verdampfung schnellere Abscheidungsraten bietet, zeichnet sich das Sputtern durch die Herstellung hochwertiger, haltbarer Schichten mit verbesserten Eigenschaften aus.
Die wichtigsten Punkte werden erklärt:
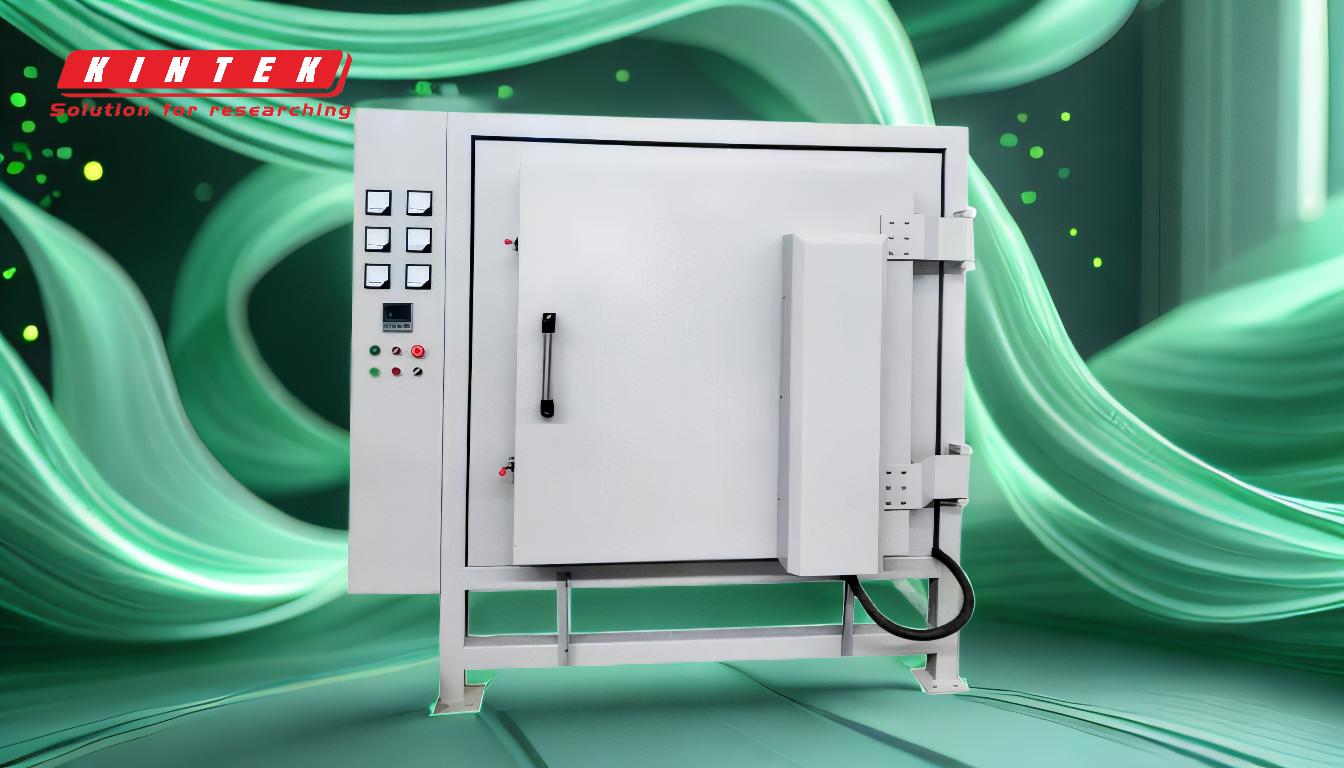
-
Bessere Adhäsion:
- Beim Sputtern prallen energiereiche Ionen auf ein Target, wodurch Atome ausgestoßen werden, die sich stärker mit dem Substrat verbinden. Dies führt zu einer besseren Haftung im Vergleich zur thermischen Verdampfung, bei der das verdampfte Material auf dem Substrat kondensiert und eine schwächere Bindung eingeht.
- Eine starke Haftung ist entscheidend für Anwendungen, die dauerhafte Beschichtungen erfordern, wie z. B. in der Elektronik, Optik und bei Schutzschichten.
-
Präzise Kontrolle über die Ablagerung:
- Das Sputtern ermöglicht eine bessere Kontrolle über den Abscheidungsprozess, einschließlich der Möglichkeit zur Feinabstimmung von Parametern wie Druck, Leistung und Target-Substrat-Abstand. Diese Präzision gewährleistet eine konstante Schichtdicke und Gleichmäßigkeit.
- Die thermische Verdampfung ist zwar schneller, aber weniger kontrollierbar und kann zu Schwankungen in der Folienqualität führen, insbesondere bei komplexen Geometrien oder mehrschichtigen Strukturen.
-
Kompositorische Integrität:
- Beim Sputtern bleibt die Zusammensetzung des Ausgangsmaterials erhalten, so dass die abgeschiedene Schicht dem Zielmaterial entspricht. Dies ist besonders wichtig für Legierungen und Verbundwerkstoffe, bei denen die thermische Verdampfung aufgrund von Unterschieden im Dampfdruck der einzelnen Elemente zu Änderungen in der Zusammensetzung führen kann.
- Bei der thermischen Verdampfung von Legierungen kann beispielsweise ein Element schneller verdampfen als ein anderes, was zu einer uneinheitlichen Zusammensetzung der Endschicht führt.
-
Gleichmäßiger und realistischer Metalleffekt:
- Das Sputtern erzeugt einen gleichmäßigeren und realistischeren Metalleffekt und ist daher ideal für Anwendungen wie dekorative Beschichtungen, Spiegel und optische Komponenten.
- Die thermische Verdampfung ist zwar in der Lage, reflektierende Beschichtungen zu erzeugen, erfordert aber häufig eine zusätzliche Bearbeitung (z. B. Spritzlackierung), um bestimmte Farben oder Effekte zu erzielen, was die Qualität beeinträchtigen kann.
-
Farbliche Vielseitigkeit:
- Das Sputtern bietet eine größere Farbvielfalt durch Modulation des Abscheidungsprozesses und ermöglicht die Herstellung einer breiten Palette von Farben, ohne dass zusätzliche Beschichtungen erforderlich sind.
- Im Gegensatz dazu ist die thermische Verdampfung auf die natürliche Farbe des Ausgangsmaterials (z. B. Aluminium) beschränkt und erfordert eine Nachbearbeitung für andere Farben.
-
Kompatibilität mit einer breiteren Palette von Materialien:
- Durch Sputtern kann ein breiteres Spektrum an Materialien abgeschieden werden, darunter Metalle, Legierungen, Keramiken und sogar Isoliermaterialien, da es sich um hochschmelzende Materialien und komplexe Zusammensetzungen handelt.
- Die thermische Verdampfung ist weniger effektiv bei Materialien mit sehr hohem Schmelzpunkt oder solchen, die sich beim Erhitzen zersetzen.
-
Verbesserte Filmqualität:
- Die energetische Natur des Sputterns führt zu dichteren, defektfreieren Schichten mit besseren mechanischen und optischen Eigenschaften im Vergleich zum thermischen Verdampfen.
- Dadurch eignet sich das Sputtern für Hochleistungsanwendungen wie Halbleiterbauelemente, Solarzellen und fortschrittliche Optiken.
-
Skalierbarkeit und Reproduzierbarkeit:
- Sputtering-Prozesse sind hochgradig skalierbar und reproduzierbar, was sie ideal für industrielle Anwendungen macht, bei denen Konsistenz und Zuverlässigkeit entscheidend sind.
- Die thermische Verdampfung ist zwar einfacher, aber weniger vorhersehbar und schwieriger zu skalieren für eine großflächige Produktion oder einen hohen Durchsatz.
-
Geringere thermische Belastung der Substrate:
- Das Sputtern erfolgt bei niedrigeren Temperaturen als das thermische Verdampfen, wodurch das Risiko einer thermischen Schädigung empfindlicher Substrate verringert wird.
- Dies ist besonders wichtig für Substrate wie Polymere oder temperaturempfindliche Materialien, die sich bei großer Hitze zersetzen oder verformen können.
-
Umwelt- und Sicherheitsaspekte:
- Das Sputtern ist im Allgemeinen sicherer und umweltfreundlicher, da die Materialien nicht auf extrem hohe Temperaturen erhitzt werden müssen, was das Risiko gefährlicher Emissionen verringert.
- Bei der thermischen Verdampfung hingegen können schädliche Dämpfe oder Partikel entstehen, insbesondere bei der Arbeit mit giftigen oder reaktiven Materialien.
Zusammenfassend lässt sich sagen, dass die thermische Verdampfung zwar aufgrund ihrer Einfachheit und der hohen Abscheideraten vorteilhaft ist, das Sputtern jedoch eine bessere Schichtqualität, Kontrolle und Vielseitigkeit bietet, so dass es für viele fortschrittliche Anwendungen die erste Wahl ist.
Zusammenfassende Tabelle:
Merkmal | Sputtern | Thermische Verdampfung |
---|---|---|
Haftung | Stärkere Bindung durch energiereiche Ionenstöße | Schwächere Bindung, weniger haltbar |
Kontrolle über die Ablagerung | Präzise Steuerung der Parameter (Druck, Leistung, Abstand) | Weniger kontrollierbar, variable Filmqualität |
Kompositorische Integrität | Behält die Zusammensetzung des Ausgangsmaterials bei, ideal für Legierungen und Verbindungen | Gefahr von Änderungen der Zusammensetzung aufgrund von Dampfdruckunterschieden |
Einheitlichkeit | Gleichmäßiger und realistischer Metalleffekt | Erfordert zusätzliche Verarbeitung für Einheitlichkeit |
Farbliche Vielseitigkeit | Breites Farbspektrum ohne Beschichtungen realisierbar | Begrenzt auf die Farbe des Ausgangsmaterials, erfordert Nachbearbeitung |
Kompatibilität der Materialien | Arbeitet mit Metallen, Legierungen, Keramiken und Isolatoren | Begrenzte Wirksamkeit bei hochschmelzenden oder hitzeempfindlichen Materialien |
Qualität der Filme | Dichtere, fehlerfreie Folien mit hervorragenden mechanischen und optischen Eigenschaften | Weniger dicht, mehr Mängel |
Skalierbarkeit | Hochgradig skalierbar und reproduzierbar für industrielle Anwendungen | Weniger vorhersehbar, schwieriger zu skalieren |
Thermische Belastung | Niedrigere Temperaturen verringern das Risiko von Substratschäden | Höhere Temperaturen können empfindliche Substrate beschädigen |
Umwelt und Sicherheit | Sicherer, weniger gefährliche Emissionen | Gefahr durch schädliche Dämpfe oder Partikel |
Sind Sie bereit, Ihren Dünnschicht-Beschichtungsprozess zu verbessern? Kontaktieren Sie uns heute um zu erfahren, wie das Sputtern Ihre fortschrittlichen Anwendungsanforderungen erfüllen kann!