Das Sputtering-Verfahren ist eine äußerst vorteilhafte Abscheidungstechnik, die in verschiedenen Branchen wie der Mikroelektronik, der Halbleiterindustrie und der Oberflächenbeschichtung weit verbreitet ist.Dabei werden Atome aus einem festen Zielmaterial mit Hilfe von hochenergetischen Ionen in eine Gasphase geschleudert, die dann in einer Vakuumkammer auf ein Substrat abgeschieden werden.Dieses Verfahren bietet eine hervorragende Schichtverdichtung, geringere Eigenspannungen, hohe Abscheideraten und eine ausgezeichnete Kontrolle über die Schichtdicke und -gleichmäßigkeit.Darüber hinaus ermöglicht es eine In-situ-Substratreinigung und eignet sich für Anwendungen, die eine präzise morphologische Qualität erfordern, wie z. B. die Kontrolle von Oberflächenrauhigkeit, Korngröße und Stöchiometrie.
Die wichtigsten Punkte erklärt:
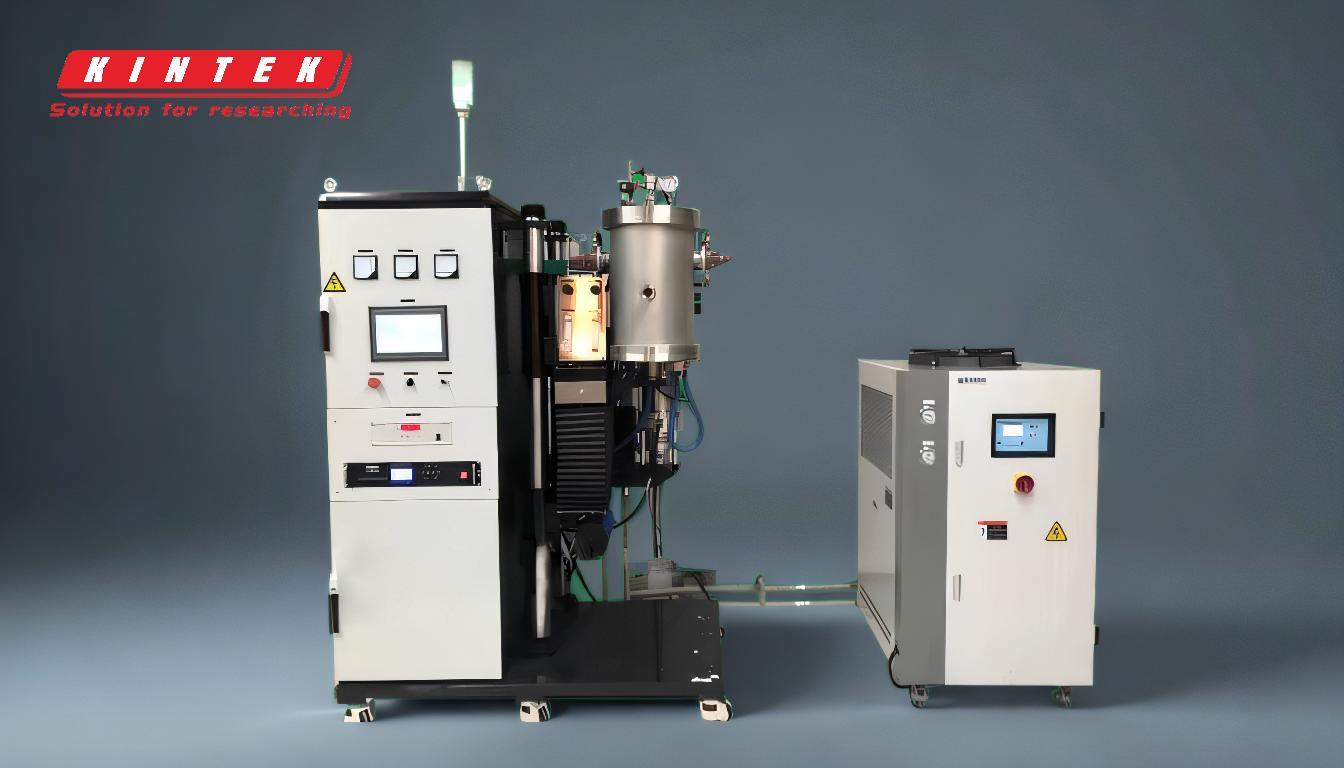
-
Bessere Filmverdichtung:
- Durch das Sputtern werden dichte und hochwertige Schichten erzeugt, da das Verfahren hochenergetisch ist.Die ausgestoßenen Atome haben genügend Energie, um dicht gepackte Schichten auf dem Substrat zu bilden, was zu Schichten mit minimalen Hohlräumen oder Defekten führt.Dies ist besonders vorteilhaft für Anwendungen, die robuste und dauerhafte Beschichtungen erfordern.
-
Reduzierte Eigenspannungen:
- Das Verfahren arbeitet bei niedrigen oder mittleren Temperaturen, wodurch die thermische Belastung des Substrats minimiert wird.Dies ist von entscheidender Bedeutung für empfindliche Materialien oder Bauteile, die sich bei hohen Temperaturen verformen oder zersetzen könnten.Die verringerte Spannung verbessert auch die Haftung und Langlebigkeit der abgeschiedenen Schicht.
-
Hohe Abscheideraten:
- Das Sputtern ermöglicht hohe Abscheideraten und ist damit effizient für die Herstellung dicker Schichten ohne Qualitätseinbußen.Im Gegensatz zu anderen Abscheidungsmethoden gibt es keine inhärenten Dickenbegrenzungen, was die Herstellung von Schichten ermöglicht, die auf spezifische industrielle Anforderungen zugeschnitten sind.
-
In-Situ-Substratreinigung:
- Die Umgebung der Vakuumkammer erleichtert die Reinigung des Substrats vor der Abscheidung.In diesem Schritt, der häufig durch kathodisches Ätzen erfolgt, werden Oberflächenverunreinigungen entfernt und eine bessere Haftung des abgeschiedenen Materials gewährleistet.Dadurch werden separate Reinigungsprozesse überflüssig, was Zeit und Ressourcen spart.
-
Präzise Kontrolle über Filmdicke und Gleichmäßigkeit:
- Durch die Anpassung von Prozessparametern wie Leistung, Druck und Abscheidungszeit bietet das Sputtern eine außergewöhnliche Kontrolle über die Schichtdicke und Gleichmäßigkeit.Diese Präzision ist für Anwendungen wie die Halbleiterherstellung von entscheidender Bedeutung, bei der selbst kleine Abweichungen die Leistung beeinträchtigen können.
-
Vielseitigkeit bei der Materialabscheidung:
- Durch Sputtern kann eine breite Palette von Materialien abgeschieden werden, darunter Metalle, Legierungen, Dielektrika und Nitride.Techniken wie das Gleichstromsputtern (DC) und das Hochfrequenzsputtern (RF) erhöhen die Vielseitigkeit des Verfahrens noch weiter, so dass es sich für zahlreiche Anwendungen eignet, von der Mikroelektronik bis zu optischen Beschichtungen.
-
Verbesserte morphologische Qualität:
- Bei Anwendungen, die eine hervorragende Oberflächenmorphologie erfordern, lassen sich durch Sputtern Faktoren wie Rauheit, Korngröße und Stöchiometrie besonders gut steuern.Dies macht es ideal für Branchen, in denen die Oberflächenqualität wichtiger ist als die Abscheidegeschwindigkeit, wie z. B. bei modernen Halbleitergeräten.
-
Fortschritte beim Magnetronsputtern:
- Das Magnetronsputtern, eine spezielle Form des Verfahrens, bietet noch höhere Abscheidungsraten und eine bessere Kontrolle.Es eignet sich besonders gut für die Abscheidung von dielektrischen und Nitridschichten, die in der Mikroelektronik unerlässlich sind.Die laufenden Forschungsarbeiten dienen der Verbesserung der Effizienz und der Erweiterung der Anwendungsmöglichkeiten.
Zusammenfassend lässt sich sagen, dass sich das Sputtering-Verfahren durch seine Fähigkeit auszeichnet, hochwertige, gleichmäßige Schichten mit präziser Kontrolle über Dicke und Morphologie zu erzeugen.Seine Vielseitigkeit, Effizienz und die Möglichkeit, bei niedrigeren Temperaturen zu arbeiten, machen es zu einer bevorzugten Wahl für eine breite Palette industrieller Anwendungen.
Zusammenfassende Tabelle:
Vorteil | Beschreibung |
---|---|
Bessere Verdichtung der Folie | Erzeugt dichte, qualitativ hochwertige Folien mit minimalen Hohlräumen oder Defekten. |
Reduzierte Eigenspannungen | Arbeitet bei niedrigen/mittleren Temperaturen und minimiert die thermische Belastung der Substrate. |
Hohe Abscheideraten | Ermöglicht eine effiziente Produktion von dicken Schichten ohne Qualitätseinbußen. |
In-Situ-Substratreinigung | Reinigt Substrate in Vakuumkammern und sorgt für bessere Haftung. |
Präzise Kontrolle über Filme | Passt Leistung, Druck und Zeit für exakte Dicke und Gleichmäßigkeit an. |
Vielseitigkeit bei Materialien | Abscheidung von Metallen, Legierungen, Dielektrika und Nitriden für verschiedene Anwendungen. |
Verbesserte morphologische Qualität | Kontrolliert Oberflächenrauhigkeit, Korngröße und Stöchiometrie für höchste Qualität. |
Fortschritte bei der Magnetronsputternutzung | Bietet höhere Abscheidungsraten und bessere Kontrolle für die Mikroelektronik. |
Erschließen Sie das volle Potenzial der Sputtertechnik für Ihre Anwendungen. Kontaktieren Sie unsere Experten noch heute !