Das Formendesign ist ein entscheidender Aspekt der Fertigung, insbesondere in Branchen wie Spritzguss, Guss und Kunststoffproduktion. Dabei geht es darum, eine präzise und funktionale Form zu schaffen, mit der sich qualitativ hochwertige Teile effizient herstellen lassen. Zu den wichtigsten Überlegungen gehören Materialauswahl, Teilegeometrie, Kühlsysteme und Herstellbarkeit. Eine gut gestaltete Form gewährleistet Haltbarkeit, Kosteneffizienz und Konsistenz in der Produktion. Im Folgenden untersuchen wir die wesentlichen Faktoren, die bei der Gestaltung einer Form zu berücksichtigen sind, um sicherzustellen, dass sie sowohl funktionale als auch wirtschaftliche Anforderungen erfüllt.
Wichtige Punkte erklärt:
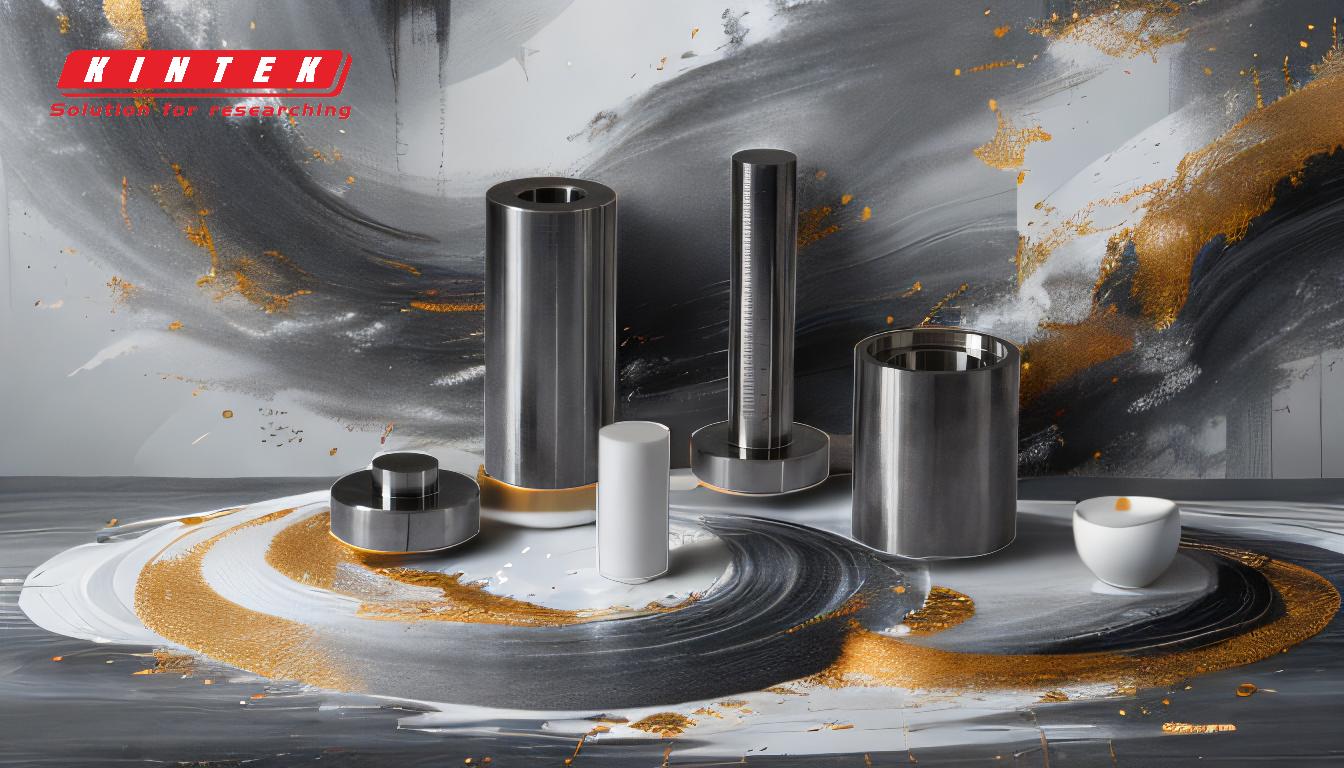
-
Materialauswahl
- Die Wahl des Materials für die Form ist entscheidend, da es sich direkt auf Haltbarkeit, Wärmeleitfähigkeit und Kosten auswirkt. Zu den gängigen Materialien gehören Stahl, Aluminium und Beryllium-Kupfer-Legierungen.
- Aufgrund seiner Haltbarkeit und Verschleißfestigkeit wird Stahl häufig für die Massenproduktion bevorzugt. Aluminium hingegen ist leichter und bietet eine bessere Wärmeleitfähigkeit, wodurch es sich für Prototypen oder die Produktion kleiner Stückzahlen eignet.
- Das Material muss außerdem Korrosion und thermischer Ermüdung standhalten, insbesondere bei Hochtemperaturanwendungen wie dem Spritzguss.
-
Teilegeometrie und Design
- Das Formdesign muss die Geometrie des endgültigen Teils berücksichtigen, einschließlich Merkmalen wie Hinterschneidungen, Rippen und Vorsprüngen.
- Formschrägen sind wichtig, um das einfache Auswerfen des Teils aus der Form zu erleichtern. Typischerweise wird ein Entformungswinkel von 1–2 Grad empfohlen, dieser kann jedoch je nach Material und Komplexität des Teils variieren.
- Die Gleichmäßigkeit der Wandstärke ist entscheidend, um Fehler wie Verwerfungen, Einfallstellen oder Hohlräume zu vermeiden. Eine ungleichmäßige Dicke kann zu ungleichmäßiger Kühlung und Spannungskonzentrationen führen.
-
Kühlsystemdesign
- Eine effiziente Kühlung ist für die Einhaltung der Zykluszeiten und die Sicherstellung der Teilequalität von entscheidender Bedeutung. Das Kühlsystem muss so ausgelegt sein, dass die Wärme gleichmäßig aus der Form abgeleitet wird.
- Kühlkanäle sollten strategisch platziert werden, um Hotspots zu vermeiden und eine gleichmäßige Kühlung zu gewährleisten. Computational Fluid Dynamics (CFD)-Simulationen können dabei helfen, die Kanalplatzierung zu optimieren.
- Die Wahl des Kühlmittels (Wasser, Öl oder Luft) hängt vom Formmaterial und den thermischen Anforderungen des Prozesses ab.
-
Auswurfsystem
- Das Auswurfsystem muss so ausgelegt sein, dass das Teil ohne Beschädigung aus der Form entnommen werden kann. Zu den gängigen Auswurfmethoden gehören Auswerferstifte, Auswerferhülsen und Luftstöße.
- Die Platzierung und Größe der Auswerferstifte muss sorgfältig geplant werden, um Markierungen oder Verformungen des Teils zu vermeiden.
- Bei komplexen Teilen können zusätzliche Mechanismen wie Heber oder Schieber erforderlich sein, um Hinterschnitte freizugeben.
-
Anguss- und Läufersysteme
- Der Anschnitt ist der Eintrittspunkt für das Material in den Formhohlraum. Sein Design beeinflusst den Materialfluss, die Füllzeit und die Teilequalität.
- Angusssysteme verteilen das Material in Mehrfachkavitätenwerkzeugen auf mehrere Kavitäten. Ausgewogene Läufer sorgen für eine gleichmäßige Befüllung und reduzieren den Abfall.
- Die Anschnittposition sollte Schweißnähte und Lufteinschlüsse minimieren, die das Teil schwächen oder Oberflächenfehler verursachen können.
-
Entlüften
- Damit während des Formvorgangs Luft und Gase entweichen können, ist eine ordnungsgemäße Entlüftung erforderlich. Eine unzureichende Entlüftung kann zu Defekten wie Verbrennungen, Hohlräumen oder unvollständiger Füllung führen.
- Entlüftungskanäle sollten am Ende des Strömungswegs platziert werden und so gestaltet sein, dass ein Materialaustritt verhindert wird.
- Größe und Tiefe der Entlüftungsöffnungen hängen von der Materialviskosität und den Fließeigenschaften ab.
-
Herstellbarkeit und Wartung
- Das Formendesign soll Herstellungs- und Montageprozesse vereinfachen. Komplexe Designs können die Produktionskosten erhöhen und zu längeren Lieferzeiten führen.
- Dabei sollte auf eine einfache Wartung geachtet werden, beispielsweise auf die Zugänglichkeit für Reinigung, Reparaturen und den Austausch von Teilen.
- Modulare Designs können Ausfallzeiten reduzieren und schnelle Änderungen oder Upgrades ermöglichen.
-
Kostenüberlegungen
- Das Design muss Leistung und Kosten in Einklang bringen. Hochwertige Materialien und komplexe Funktionen können die Anfangsinvestition erhöhen, können aber durch verbesserte Haltbarkeit und Effizienz die langfristigen Kosten senken.
- Die Prinzipien des „Design for Manufacturability“ (DFM) sollten angewendet werden, um Abfall zu minimieren und Produktionsprozesse zu optimieren.
- Prototyping und Tests können dazu beitragen, potenzielle Probleme frühzeitig zu erkennen und so das Risiko kostspieliger Neukonstruktionen zu verringern.
-
Oberflächenbeschaffenheit und Textur
- Die Oberflächenbeschaffenheit der Form beeinflusst das Aussehen und die Funktionalität des Endteils. Der Form können Texturen hinzugefügt werden, um bestimmte ästhetische oder funktionale Anforderungen zu erfüllen.
- Das Polieren oder Beschichten der Formoberfläche kann die Teilefreigabe verbessern und den Verschleiß verringern.
- Die Wahl der Oberflächenbeschaffenheit hängt von der Anwendung ab und reicht von Spiegelglanz bis hin zu rauen Texturen.
-
Toleranz und Präzision
- Formen müssen so konstruiert sein, dass sie enge Toleranzen einhalten und konsistente Teileabmessungen und -qualität gewährleisten.
- Um die erforderliche Genauigkeit zu erreichen, werden häufig Präzisionsbearbeitungstechniken wie CNC-Fräsen und EDM (Funkenerosion) eingesetzt.
- Bei Toleranzüberlegungen sollten Materialschrumpfung, Wärmeausdehnung und andere Faktoren berücksichtigt werden, die sich auf die Teileabmessungen auswirken können.
-
Umwelt- und Sicherheitsaspekte
- Das Formendesign sollte die Auswirkungen auf die Umwelt minimieren, indem es Materialverschwendung und Energieverbrauch reduziert.
- Sicherheitsfunktionen wie Verriegelungen und Schutzvorrichtungen sollten eingebaut werden, um die Bediener während des Betriebs und der Wartung der Form zu schützen.
- Die Einhaltung von Branchenstandards und -vorschriften ist für eine sichere und nachhaltige Produktion von entscheidender Bedeutung.
Durch die Berücksichtigung dieser Überlegungen können Formenbauer effiziente, langlebige und kostengünstige Formen entwickeln, die den Anforderungen der modernen Fertigung gerecht werden. Jeder Faktor spielt eine entscheidende Rolle für den Erfolg des Formprozesses, vom ersten Entwurf bis zur Endproduktion.
Übersichtstabelle:
Wichtige Überlegung | Details |
---|---|
Materialauswahl | Stahl für Haltbarkeit, Aluminium für Wärmeleitfähigkeit und Korrosionsbeständigkeit. |
Teilegeometrie | Entformungswinkel, Gleichmäßigkeit der Wandstärke und Komplexität der Merkmale. |
Kühlsystem | Gleichmäßige Kühlung, strategische Kanalplatzierung und Kühlmittelauswahl. |
Auswurfsystem | Auswerferstifte, Hülsen und Mechanismen für komplexe Teile. |
Anguss- und Läufersysteme | Angussdesign, ausgewogene Läufer und Minimierung von Bindenähten. |
Entlüften | Richtige Entlüftung, um Defekte wie Verbrennungen und Hohlräume zu vermeiden. |
Herstellbarkeit | Vereinfachtes Design, Modularität und einfache Wartung. |
Kostenüberlegungen | Ausbalancieren von Leistung und Kosten durch Anwendung der DFM-Prinzipien. |
Oberflächenbeschaffenheit | Texturen, Polieren und Beschichtungen für Teilefreigabe und Ästhetik. |
Toleranz und Präzision | Enge Toleranzen, Präzisionsbearbeitung und Berücksichtigung von Materialschwund. |
Umwelt und Sicherheit | Abfallreduzierung, Energieeffizienz und Einhaltung von Sicherheitsstandards. |
Sind Sie bereit, eine Form zu entwerfen, die Ihren Produktionsanforderungen entspricht? Kontaktieren Sie noch heute unsere Experten für eine individuelle Beratung!