Sintern ist ein kritischer Prozess in der Materialherstellung, aber er ist nicht ohne Probleme und Fehler.Zu den häufigsten Problemen gehören Übersinterung, Untersinterung, Blasenbildung und Schwitzen, die die Qualität und Leistung des Endprodukts beeinträchtigen können.Außerdem können Probleme wie Verformung und Durchbiegung aufgrund von Schwerkraft oder Reibung zu strukturellen Mängeln führen.Hochtemperatursintern ist zwar effektiv, verbraucht aber viel Energie und kann die Materialsynthese und Phasenstabilität einschränken.Herkömmliche Sinterverfahren erfordern oft langes Erhitzen und hohe Temperaturen, was zu Kornwachstum und Restporen führt.Diese Mängel und Einschränkungen machen deutlich, dass die Sinterparameter genau kontrolliert werden müssen, um optimale Ergebnisse zu erzielen.
Die wichtigsten Punkte werden erklärt:
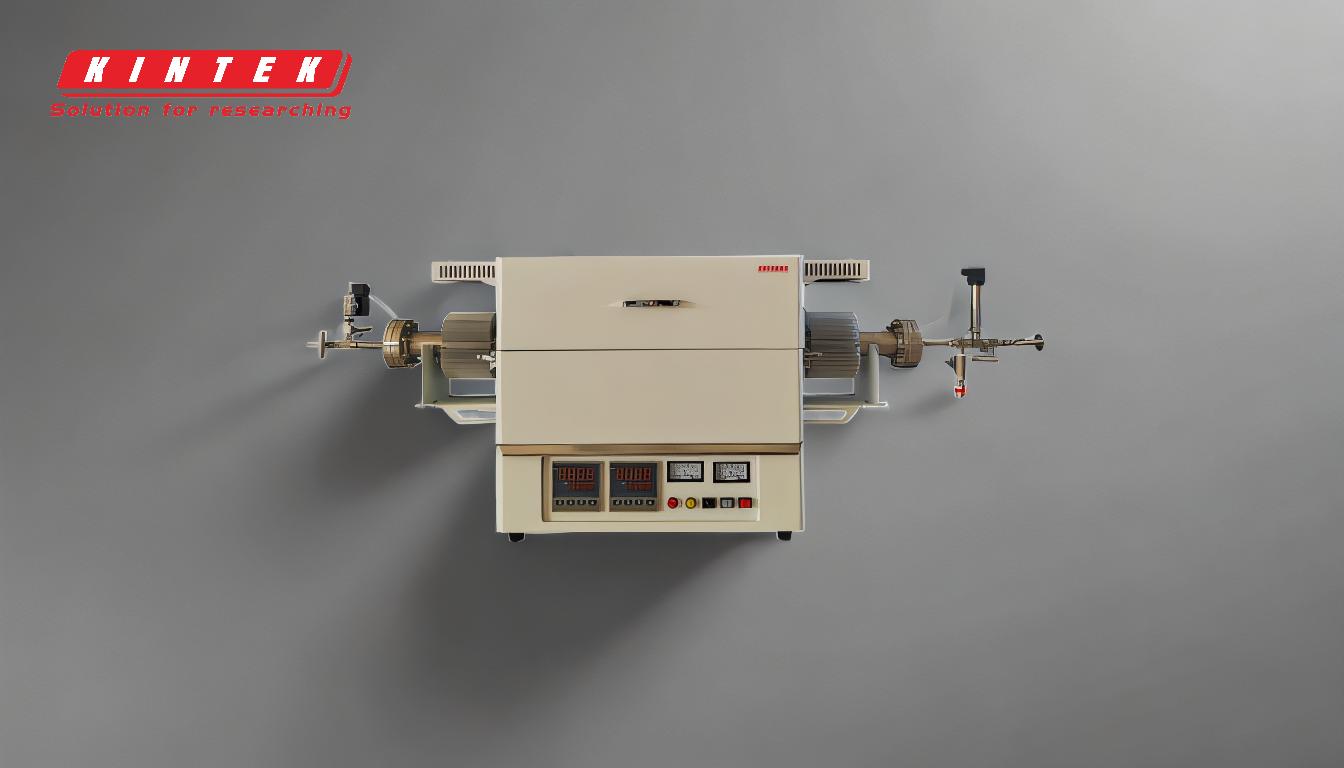
-
Übersintern:
- Definition:Tritt auf, wenn die Sintertemperatur zu hoch ist oder die Sinterzeit zu lang ist.
- Aufprall:Führt zu einer Verschlechterung des Produkts, z. B. übermäßiges Kornwachstum, Verlust der mechanischen Eigenschaften oder sogar Schmelzen des Materials.
- Beispiel:Bei der Keramikherstellung kann eine Übersinterung dazu führen, dass das Material spröde wird und seine strukturelle Integrität verliert.
-
Untersinterung:
- Definition:Tritt auf, wenn die Sintertemperatur zu niedrig ist oder die Sinterzeit zu kurz ist.
- Aufprall:Dies führt zu einer unzureichenden Bindung zwischen den Partikeln, was eine schlechte mechanische Festigkeit und eine unzureichende Verdichtung zur Folge hat.
- Beispiel:Beim Sintern von Metallpulver kann Untersinterung zu einem porösen Endprodukt mit schwachen strukturellen Eigenschaften führen.
-
Blasenbildung:
- Definition:Oberflächenfehler, die durch die Freisetzung von eingeschlossenen Gasen während des Sinterprozesses verursacht werden.
- Aufprall:Führt zu Oberflächenfehlern, wie Blasen oder Bläschen, die die ästhetische und funktionelle Qualität des Produkts beeinträchtigen können.
- Beispiel:Bei keramischen Fliesen kann die Blasenbildung zu Unregelmäßigkeiten auf der Oberfläche führen, die für hochwertige Oberflächen nicht akzeptabel sind.
-
Schwitzen:
- Definition:Tritt auf, wenn während der Wärmebehandlung eine flüssige Phase aus dem Material austritt.
- Aufprall:Kann zu Oberflächenverschmutzung, ungleichmäßiger Materialverteilung und beeinträchtigten mechanischen Eigenschaften führen.
- Beispiel:Bei bestimmten Metalllegierungen kann es durch Schwitzen zur Entmischung von Legierungselementen kommen, was zu ungleichmäßigen Materialeigenschaften führt.
-
Verziehen und Durchbiegen:
- Definition:Verformung des Materials aufgrund von Schwerkraft oder Reibung während des Sinterprozesses.
- Aufprall:Dies führt zu Maßungenauigkeiten und strukturellen Mängeln im fertigen Teil.
- Beispiel:Bei der additiven Fertigung kann die Verformung dazu führen, dass die Teile von ihrer vorgesehenen Form abweichen, was eine Nachbearbeitung zur Korrektur erfordert.
-
Herausforderungen des Hochtemperatursinterns:
- Definition:Sinterverfahren, die extrem hohe Temperaturen erfordern.
- Aufschlag:Verbraucht mehr Energie und kann die Arten von Materialien, die gesintert werden können, aufgrund von Problemen mit der thermischen Stabilität einschränken.
- Beispiel:Das Hochtemperatursintern von Keramik kann zu einer Phaseninstabilität führen, bei der das Material unerwünschte Phasenumwandlungen durchlaufen kann.
-
Kornwachstum und Restporen:
- Definition:Probleme, die durch lange Sinterzeiten und hohe Temperaturen entstehen.
- Auswirkungen:Das Kornwachstum kann die mechanische Festigkeit des Materials verringern, während Restporen die Dichte und strukturelle Integrität beeinträchtigen können.
- Beispiel:In der Pulvermetallurgie kann ein übermäßiges Kornwachstum zu einem groben Gefüge führen, das die Zähigkeit des Werkstoffs verringert.
-
Energieverbrauch und Umweltauswirkungen:
- Definition:Hoher Energiebedarf bei herkömmlichen Sinterverfahren.
- Aufprall:Erhöht die Produktionskosten und den ökologischen Fußabdruck und macht den Prozess weniger nachhaltig.
- Beispiel:Der hohe Energieverbrauch von Sinteröfen trägt zu höheren Betriebskosten und Kohlenstoffemissionen bei.
-
Herausforderungen für die Prozesssteuerung:
- Definition:Schwierigkeit, die Sinterparameter genau zu kontrollieren.
- Aufprall:Inkonsistente Sinterergebnisse, die zu Schwankungen in der Produktqualität führen.
- Beispiel:Eine uneinheitliche Temperaturregelung kann zu Teilen mit unterschiedlichen Dichten und mechanischen Eigenschaften führen.
-
Materielle Beschränkungen:
- Definition:Beschränkungen für die Arten von Materialien, die effektiv gesintert werden können.
- Aufprall:Begrenzt den Anwendungsbereich und die möglichen Innovationen in der Materialwissenschaft.
- Beispiel:Bestimmte hochentwickelte Werkstoffe, wie z. B. Hochleistungskeramik, eignen sich aufgrund ihrer thermischen Empfindlichkeit möglicherweise nicht für herkömmliche Sinterverfahren.
Zusammenfassend lässt sich sagen, dass das Sintern zwar ein leistungsfähiges Herstellungsverfahren ist, dass es aber unbedingt notwendig ist, seine potenziellen Mängel und Einschränkungen zu verstehen und zu mindern.Durch eine sorgfältige Kontrolle der Sinterparameter und die Erforschung alternativer Sinterverfahren können die Hersteller die Produktqualität verbessern und die Palette der Werkstoffe, die effektiv gesintert werden können, erweitern.
Zusammenfassende Tabelle:
Defekt/Beschränkung | Definition | Auswirkung | Beispiel |
---|---|---|---|
Übersinterung | Zu hohe Temperatur oder zu lange Zeit. | Produktverschlechterung, übermäßiges Kornwachstum oder Schmelzen. | Die Keramik wird spröde und verliert ihre strukturelle Integrität. |
Untersinterung | Zu niedrige Temperatur oder zu kurze Zeit. | Schlechte mechanische Festigkeit und unzureichende Verdichtung. | Das Sintern von Metallpulver führt zu einem porösen, schwachen Produkt. |
Blasenbildung | Eingeschlossene Gase, die während des Sinterns freigesetzt werden. | Oberflächenmängel wie Blasen oder Bläschen. | Keramische Fliesen entwickeln Oberflächenunregelmäßigkeiten. |
Ausschwitzen | Flüssige Phase sickert während der Wärmebehandlung aus. | Oberflächenverschmutzung, ungleichmäßige Materialverteilung. | Bei Metalllegierungen kommt es zu einer Entmischung der Elemente, was zu ungleichmäßigen Eigenschaften führt. |
Verformung und Durchbiegung | Verformung aufgrund von Schwerkraft oder Reibung. | Maßliche Ungenauigkeiten und strukturelle Mängel. | Additiv gefertigte Teile weichen von der vorgesehenen Form ab. |
Herausforderungen bei hohen Temperaturen | Extrem hohe Temperaturen erforderlich. | Hoher Energieverbrauch und Materialbeschränkungen. | Keramiken unterliegen unerwünschten Phasenumwandlungen. |
Kornwachstum und Poren | Längeres Erhitzen und hohe Temperaturen. | Geringere mechanische Festigkeit und geringere Dichte. | Die Pulvermetallurgie führt zu einer groben Mikrostruktur. |
Verbrauch von Energie | Hoher Energiebedarf beim herkömmlichen Sintern. | Erhöhte Kosten und Umweltauswirkungen. | Sinteröfen tragen zu höheren Kohlenstoffemissionen bei. |
Prozesskontrolle | Schwierigkeit, präzise Sinterparameter einzuhalten. | Inkonsistente Produktqualität. | Die Teile haben unterschiedliche Dichten und mechanische Eigenschaften. |
Beschränkungen des Materials | Beschränkungen bei sinterfähigen Materialien. | Schränkt Anwendungen und Innovationen ein. | Hochleistungskeramik eignet sich möglicherweise nicht für das traditionelle Sintern. |
Kämpfen Sie mit Sinterfehlern?Optimieren Sie Ihren Prozess mit fachkundiger Anleitung. Kontaktieren Sie uns noch heute !