Das Induktionsschmelzen ist aufgrund seiner Effizienz, Schnelligkeit und Präzision ein weit verbreitetes Verfahren in der Metallurgie.Es ist jedoch nicht frei von Nachteilen.Zu den Hauptnachteilen gehören ein zeitaufwändiger Abkühlungsprozess, Probleme bei der Einhaltung enger Maßtoleranzen und die Notwendigkeit zusätzlicher Bearbeitungs- und Poliervorgänge, die Kosten und Produktionszeit erhöhen können.Trotz dieser Einschränkungen bleibt das Induktionsschmelzen aufgrund seiner zahlreichen Vorteile wie Energieeffizienz, Umweltfreundlichkeit und der Fähigkeit, hochwertige Metalle mit minimaler Verunreinigung zu produzieren, für viele Anwendungen die bevorzugte Methode.
Die wichtigsten Punkte erklärt:
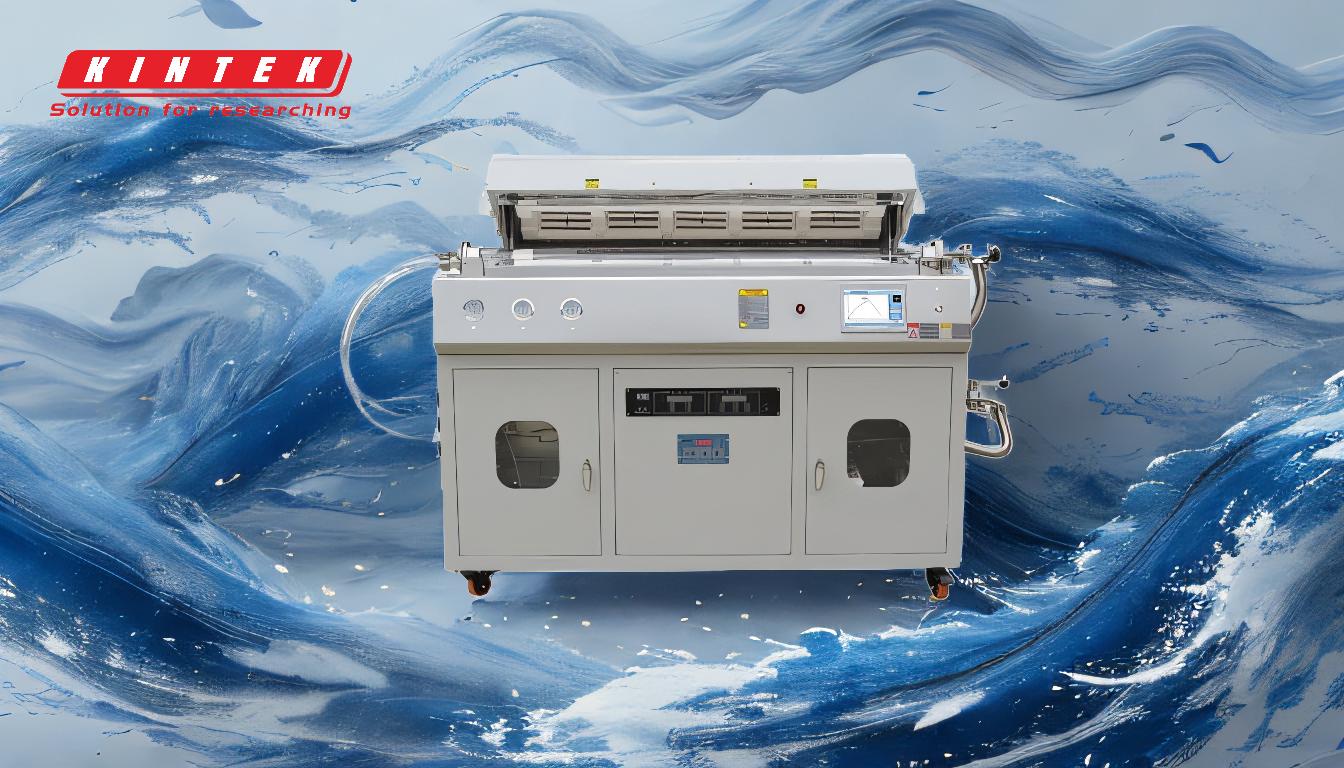
-
Zeitaufwändiger Abkühlungsprozess:
- Das Induktionsschmelzen beinhaltet eine schnelle Erwärmung, aber der Abkühlungsprozess kann langsamer sein, insbesondere wenn eine präzise Temperaturkontrolle erforderlich ist.Dies kann zu längeren Produktionszyklen führen, insbesondere bei groß angelegten Operationen oder bei Metallen, die bestimmte Abkühlungsraten erfordern, um die gewünschten Materialeigenschaften zu erreichen.
-
Schwierigkeit, enge Maßtoleranzen einzuhalten:
- Das Induktionsschmelzen bietet zwar eine präzise Kontrolle über den Schmelzprozess, doch die Einhaltung enger Maßtoleranzen beim Endprodukt kann eine Herausforderung sein.Dies liegt oft an der inhärenten Natur des Prozesses, die zu leichten Abweichungen im Fließ- und Erstarrungsmuster des geschmolzenen Metalls führen kann.Infolgedessen kann eine zusätzliche Bearbeitung erforderlich sein, um die gewünschten Abmessungen zu erreichen, was die Gesamtkosten und den Zeitaufwand erhöht.
-
Notwendigkeit zusätzlicher Bearbeitungen und Polieren:
- Die Oberflächenbeschaffenheit von Teilen, die durch Induktionsschmelzen hergestellt werden, entspricht nicht immer den geforderten Standards direkt aus dem Schmelzofen.Daher sind zusätzliche Bearbeitungs- und Polierarbeiten erforderlich, um die gewünschte Oberflächenqualität zu erreichen.Diese Nachbearbeitungsschritte können die Gesamtproduktionskosten erheblich erhöhen und die Vorlaufzeit verlängern.
-
Energieeffizienz und Umweltauswirkungen:
- Trotz der Nachteile ist das Induktionsschmelzen im Vergleich zu herkömmlichen Verfahren wie Öfen für fossile Brennstoffe sehr energieeffizient.Induktionsöfen können einen Wirkungsgrad von bis zu 92 % erreichen, was den Energieverbrauch erheblich senkt und die Umweltbelastung minimiert.Dies macht das Induktionsschmelzen auf lange Sicht zu einer nachhaltigeren Option.
-
Produktion von hochwertigen Metallen:
- Das Induktionsschmelzen ist bekannt für die Herstellung hochwertiger Metalle mit minimaler Verunreinigung.Das Verfahren ermöglicht eine präzise Kontrolle der Legierungszusammensetzung und gewährleistet, dass das Endprodukt strengen Qualitätsstandards entspricht.Darüber hinaus sorgt das inhärente induktive Rühren für eine homogene Mischung des geschmolzenen Metalls, was für das Erreichen gleichmäßiger Materialeigenschaften entscheidend ist.
-
Flexibilität und Anpassungsfähigkeit:
- Einer der wichtigsten Vorteile des Induktionsschmelzens ist seine Flexibilität.Das Verfahren lässt sich leicht an das Schmelzen verschiedener Metalle und Legierungen anpassen und eignet sich daher für eine Vielzahl von Anwendungen.Die Möglichkeit, schnell zwischen verschiedenen Materialien zu wechseln, und die Option, die Anlage bei Bedarf sofort abzuschalten, erhöhen die Betriebseffizienz zusätzlich.
-
Sicherheit und Sauberkeit:
- Das Induktionsschmelzen ist ein sauberes Verfahren, bei dem weder Staub noch Rauch oder Schadstoffe entstehen, was es sowohl für das Personal als auch für die Umwelt sicherer macht.Durch den Wegfall der Verbrennungserwärmung wird die Gefahr von Bränden, Explosionen oder Verbrennungen verringert, was zu einer sichereren Arbeitsumgebung beiträgt.
Zusammenfassend lässt sich sagen, dass das Induktionsschmelzen zwar seine Nachteile hat, wie z. B. die Notwendigkeit einer zusätzlichen Bearbeitung und die Schwierigkeit, enge Toleranzen einzuhalten, aber seine Vorteile in Bezug auf Energieeffizienz, Umweltverträglichkeit und die Herstellung hochwertiger Metalle machen es zu einem wertvollen Verfahren in der modernen Metallurgie.
Zusammenfassende Tabelle:
Benachteiligungen | Herausforderungen | Auswirkungen |
---|---|---|
Zeitaufwändiger Abkühlungsprozess | Langsamere Abkühlung, insbesondere bei präziser Temperaturkontrolle | Längere Produktionszyklen, höhere Kosten |
Schwierigkeit, enge Toleranzen einzuhalten | Schwankungen beim Fließen und Erstarren des geschmolzenen Metalls | Zusätzliche Bearbeitung erforderlich, höhere Kosten |
Bedarf an zusätzlicher Bearbeitung und Polieren | Die Oberflächengüte entspricht möglicherweise nicht den Standards direkt aus dem Ofen | Erhöhte Produktionskosten und Vorlaufzeiten |
Vorteile | Vorteile | Auswirkungen |
Energie-Effizienz | Bis zu 92% Effizienz, reduzierter Energieverbrauch | Niedrigere Betriebskosten, ökologische Nachhaltigkeit |
Hochwertige Metallproduktion | Minimale Verunreinigung, präzise Kontrolle der Legierungszusammensetzung | Konsistente Materialeigenschaften, hochwertige Produktion |
Flexibilität und kundenspezifische Anpassung | Geeignet für verschiedene Metalle und Legierungen, schnelle Umstellung | Verbesserte Betriebseffizienz |
Sicherheit und Sauberkeit | Kein Staub, Rauch oder Schadstoffe; geringere Brand- und Explosionsgefahr | Sicherere Arbeitsumgebung, umweltfreundliches Verfahren |
Möchten Sie mehr über das Induktionsschmelzen erfahren und darüber, wie Ihr Betrieb davon profitieren kann? Kontaktieren Sie noch heute unsere Experten für eine maßgeschneiderte Beratung!