Das Nitrieren bietet zwar erhebliche Vorteile bei der Verbesserung von Materialeigenschaften wie Verschleißfestigkeit und Oberflächenhärte, hat aber auch einige Nachteile.Dazu gehören Herausforderungen im Zusammenhang mit der Prozesssteuerung, Umweltbelange und wirtschaftliche Faktoren.Das Plasmanitrieren beispielsweise erfordert eine sorgfältige Oberflächenvorbereitung und ein sorgfältiges Management der Energieverteilung, um Überhitzung und instabile Lichtbögen zu vermeiden.Das Flüssignitrierverfahren hingegen unterliegt trotz der Entwicklung ungiftiger Alternativen Einschränkungen aufgrund der Verwendung giftiger Zyanidsalze.Darüber hinaus erschweren die hohen Anschaffungskosten für Plasmanitrieranlagen und die Beschränkungen bei der Stapelverarbeitung aufgrund des Verhältnisses zwischen Leistung und Fläche die Einführung des Verfahrens.
Die wichtigsten Punkte werden erklärt:
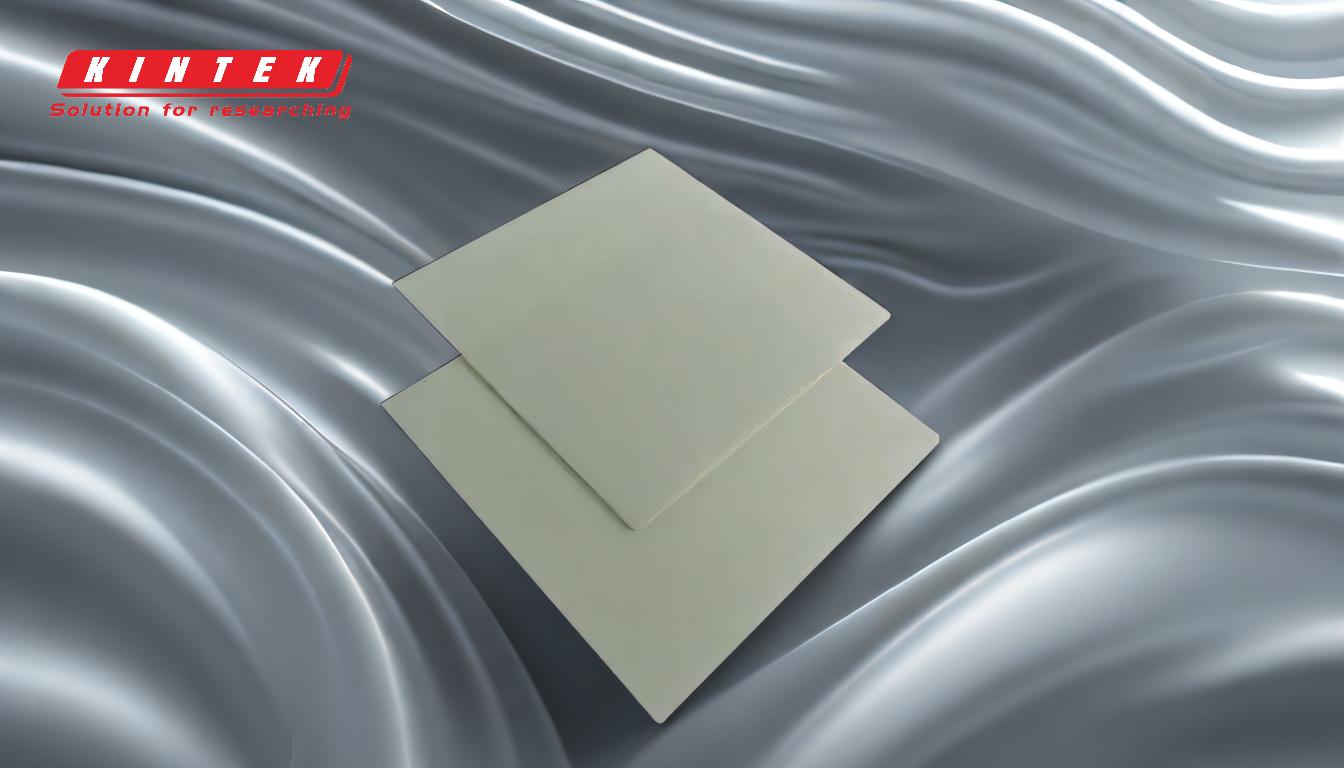
-
Oberflächenreinheit und -stabilität beim Plasmanitrieren:
- Kritische Oberflächenvorbereitung:Die Wirksamkeit des Plasmanitrierens hängt stark von der Sauberkeit der Bauteiloberflächen ab.Jede Verunreinigung kann zur Bildung instabiler Lichtbögen während der Heizzyklen führen, was die Qualität der Nitrierschicht beeinträchtigen kann.
- Vermeidung von Überhitzung:Die Teile müssen präzise repariert und vorbereitet werden, um eine Überhitzung während des Prozesses zu vermeiden, die zu Materialverschlechterung oder Versagen führen kann.
-
Beschränkungen der Chargenverarbeitung:
- Leistung/Bereich Beziehung:Beim Plasmanitrieren können Bauteile ähnlicher Größe aufgrund des Verhältnisses zwischen Leistung und Fläche nicht in einer Charge bearbeitet werden.Diese Einschränkung macht mehrere Durchläufe oder spezielle Aufbauten erforderlich, was sowohl den Zeitaufwand als auch die Produktionskosten erhöht.
-
Wirtschaftliche Erwägungen:
- Hohe Anfangskosten:Die Einrichtung des Plasmanitrierens erfordert erhebliche Anfangsinvestitionen in Ausrüstung und Technologie.Diese hohen Kosten können ein Hindernis für kleinere Betriebe oder solche mit begrenzten Budgets sein.
-
Umwelt- und Gesundheitsaspekte beim Flüssignitrieren:
- Verwendung von giftigen Cyanidsalzen:Bei herkömmlichen Flüssignitrierverfahren werden Zyanidsalze verwendet, die für die Bediener ein ernsthaftes Gesundheitsrisiko darstellen und bei der Abfallentsorgung Umweltprobleme verursachen.
- Regulatorische Beschränkungen:Aufgrund dieser Gesundheits- und Umweltrisiken wird die Verwendung von Zyanidsalzen zunehmend eingeschränkt, so dass die Industrie auf ungiftige Alternativen ausweicht, die allerdings noch nicht die Wirksamkeit der traditionellen Verfahren erreichen.
-
Dünne Nitrierschicht:
- Schichtdicke:Das Flüssignitrieren führt in der Regel zu einer relativ dünnen Nitrierschicht (0,01-0,02 mm), die für Anwendungen, die eine tiefere Einsatzhärtung erfordern, möglicherweise nicht ausreichend ist.
Zusammenfassend lässt sich sagen, dass Nitrierverfahren zwar die Materialeigenschaften erheblich verbessern, aber auch eine Reihe von Herausforderungen mit sich bringen, die sorgfältig bedacht werden müssen.Dazu gehören technische Einschränkungen bei der Verarbeitung, wirtschaftliche Hindernisse sowie Umwelt- und Gesundheitsbedenken, insbesondere beim Flüssignitrieren.Die Kenntnis dieser Nachteile ist für die Industrie von entscheidender Bedeutung, um fundierte Entscheidungen über die Einführung und Umsetzung von Nitrierverfahren zu treffen.
Zusammenfassende Tabelle:
Benachteiligung | Beschreibung |
---|---|
Oberflächenreinheit und Stabilität | Das Plasmanitrieren erfordert eine sorgfältige Oberflächenvorbereitung, um instabile Lichtbögen und Überhitzung zu vermeiden. |
Einschränkungen bei der Stapelverarbeitung | Das Verhältnis zwischen Leistung und Fläche schränkt die Stapelverarbeitung ein, was Zeit und Kosten erhöht. |
Hohe Anfangskosten | Plasmanitrierungsanlagen sind mit erheblichen Vorabinvestitionen verbunden. |
Umwelt- und Gesundheitsaspekte | Beim Flüssignitridieren werden giftige Zyanidsalze verwendet, was Probleme bei der Gesundheit und der Entsorgung mit sich bringt. |
Dünne Nitrierschicht | Beim Flüssignitrieren entstehen dünne Schichten (0,01-0,02 mm), was die Tiefe für einige Anwendungen begrenzt. |
Benötigen Sie Hilfe bei der Bewältigung der Herausforderungen des Nitrierens? Kontaktieren Sie noch heute unsere Experten für maßgeschneiderte Lösungen!