Die Wärmeerzeugung bei der induktiven Erwärmung hängt von mehreren miteinander verknüpften Faktoren ab, darunter die Materialeigenschaften des Werkstücks, die Konstruktion und Konfiguration der Induktionsspule, die Eigenschaften der Stromversorgung und die Betriebsbedingungen.Diese Faktoren beeinflussen die Effizienz und Effektivität des Erwärmungsprozesses und bestimmen, wie viel Wärme erzeugt wird und wie schnell das Material die gewünschte Temperatur erreicht.Das Verständnis dieser Faktoren ist entscheidend für die Optimierung von Induktionserwärmungsanlagen für bestimmte Anwendungen.
Die wichtigsten Punkte erklärt:
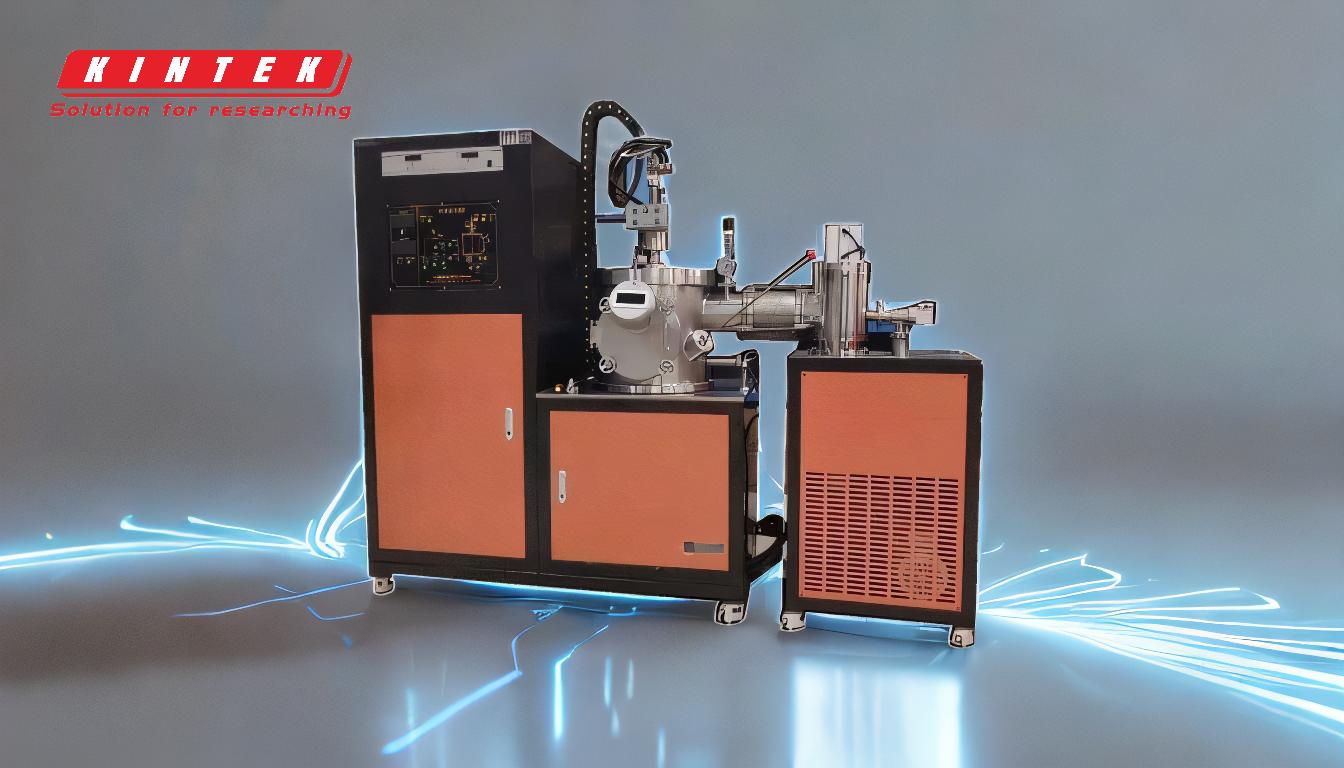
-
Materialeigenschaften:
- Art des Materials:Die Induktionserwärmung funktioniert am besten mit leitfähigen Materialien, wie z. B. Metallen.Magnetische Materialien (z. B. Eisen, Stahl) erwärmen sich sowohl durch Wirbelströme als auch durch Hystereseverluste, während nichtmagnetische, leitfähige Materialien (z. B. Kupfer, Aluminium) ausschließlich auf Wirbelströme angewiesen sind.
- Widerstandswert:Materialien mit höherem Widerstand erzeugen mehr Wärme, da sie dem Fluss von Wirbelströmen widerstehen und mehr elektrische Energie in Wärmeenergie umwandeln.
- Größe und Dicke:Kleinere und dünnere Materialien erwärmen sich schneller, weil die induzierten Ströme das Material besser durchdringen.Dickere Materialien benötigen möglicherweise niedrigere Frequenzen, um eine tiefere Erwärmung zu erreichen.
- Spezifische Wärme und Masse:Die Energiemenge, die erforderlich ist, um die Temperatur eines Materials zu erhöhen, hängt von dessen spezifischer Wärme und Masse ab.Eine höhere spezifische Wärme oder eine größere Masse erfordert mehr Energie für den gleichen Temperaturanstieg.
-
Konstruktion der Induktionsspule:
- Geometrie der Spule:Form und Größe der Induktionsspule müssen auf das Werkstück abgestimmt sein, um eine gleichmäßige Erwärmung zu gewährleisten.Schlecht ausgelegte Spulen können zu ungleichmäßiger Erwärmung oder Energieverlusten führen.
- Anzahl der Windungen:Die Anzahl der Windungen in der Spule beeinflusst die Stärke und Verteilung des Magnetfelds.Mehr Windungen können das Magnetfeld verstärken, aber auch den Widerstand und die Energieverluste erhöhen.
- Nähe zum Werkstück:Der Abstand zwischen der Spule und dem Werkstück (Kopplung) beeinflusst die Heizleistung.Eine engere Kopplung verbessert die Energieübertragung, muss aber ausgewogen sein, um physikalische Störungen zu vermeiden.
-
Merkmale der Energieversorgung:
- Frequenz:Höhere Frequenzen führen zu einer geringeren Erwärmungstiefe (Skin-Effekt) und eignen sich daher für die Erwärmung dünner Materialien oder Oberflächenbehandlungen.Niedrigere Frequenzen dringen tiefer ein und sind ideal für dickere Materialien.
- Leistung:Die Stromversorgung muss ausreichend Energie bereitstellen, um den erforderlichen Temperaturanstieg unter Berücksichtigung der spezifischen Wärme, der Masse und der Wärmeverluste des Materials zu erreichen.
- Steuerung und Modulation:Hochentwickelte Netzteile ermöglichen eine präzise Steuerung von Frequenz und Ausgangsleistung, was eine Optimierung für unterschiedliche Materialien und Heizanforderungen ermöglicht.
-
Betriebsbedingungen:
- Temperaturschwankungen:Der Grad der erforderlichen Temperaturänderung beeinflusst die benötigte Leistung.Größere Temperaturschwankungen erfordern mehr Energie und eine höhere Leistungskapazität.
- Wärmeverluste:Wärme kann durch Leitung, Konvektion und Strahlung verloren gehen.Durch die Isolierung des Werkstücks oder die Verwendung von Schutzatmosphären können diese Verluste minimiert werden.
- Umweltfaktoren:Das Vorhandensein von Verunreinigungen, Oxidationsmitteln oder Schlacken kann die Heizleistung und die Materialeigenschaften beeinträchtigen, insbesondere bei Schmelzanwendungen.
-
Magnetische und elektrische Phänomene:
- Wirbelstürme:Hierbei handelt es sich um induzierte Ströme innerhalb des leitfähigen Materials, die aufgrund des Widerstands Wärme erzeugen.Das Ausmaß der Wirbelströme hängt von der Leitfähigkeit des Materials und der Stärke des Magnetfelds ab.
- Hysterese-Verluste:In magnetischen Materialien entsteht Wärme durch die wiederholte Ausrichtung und Neuausrichtung der magnetischen Bereiche unter dem magnetischen Wechselfeld.Dieser Effekt ist bei nichtmagnetischen Materialien vernachlässigbar.
-
System-Wirkungsgrad:
- Energietransfer-Effizienz:Der Wirkungsgrad der Energieübertragung von der Stromquelle auf das Werkstück hängt von der Spulenkonstruktion, der Kopplung und den Materialeigenschaften ab.
- Thermischer Wirkungsgrad:Die Minimierung der Wärmeverluste an die Umgebung und die Gewährleistung einer gleichmäßigen Beheizung verbessern die Gesamteffizienz des Systems.
Durch sorgfältige Berücksichtigung dieser Faktoren können Induktionserwärmungssysteme für bestimmte Anwendungen optimiert werden, um eine effiziente und effektive Wärmeerzeugung zu gewährleisten.Dieses Verständnis ist für die Käufer von Geräten und Verbrauchsmaterialien unerlässlich, um die richtigen Komponenten und Konfigurationen für ihre Bedürfnisse auszuwählen.
Zusammenfassende Tabelle:
Faktor | Wichtige Überlegungen |
---|---|
Materialeigenschaften | Typ, spezifischer Widerstand, Größe, Dicke, spezifische Wärme und Masse. |
Induktionsspulen-Design | Spulengeometrie, Anzahl der Windungen und Nähe zum Werkstück. |
Stromversorgung | Frequenz, Leistungskapazität und Steuer-/Modulationsmöglichkeiten. |
Betriebsbedingungen | Temperaturschwankungen, Wärmeverluste und Umweltfaktoren. |
Wirkungsgrad | Effizienz der Energieübertragung und thermischer Wirkungsgrad. |
Optimieren Sie Ihr Induktionserwärmungssystem für maximale Effizienz - Kontaktieren Sie noch heute unsere Experten !