Beim Sintern müssen verschiedene Parameter optimiert werden, um die gewünschten Materialeigenschaften zu erzielen.Zu den Schlüsselfaktoren gehören Temperatur, Druck, Partikelgröße und Atmosphäre, die die Verdichtung, Porosität und mechanischen Eigenschaften beeinflussen.Die Wahl des Sinterverfahrens hängt von den Materialeigenschaften und den gewünschten Ergebnissen wie Festigkeit, Leitfähigkeit oder Ermüdungsbeständigkeit ab.Darüber hinaus spielt die Konfiguration des Ofens, einschließlich Temperaturbereich, Gasfluss und Beladungsstrategie, eine entscheidende Rolle bei der Gewährleistung einer effizienten und effektiven Sinterung.Durch die sorgfältige Kontrolle dieser Variablen können Hersteller den Sinterprozess auf die spezifischen Produktanforderungen zuschneiden und so ein Gleichgewicht zwischen Leistung, Kosten und Produktionseffizienz herstellen.
Die wichtigsten Punkte erklärt:
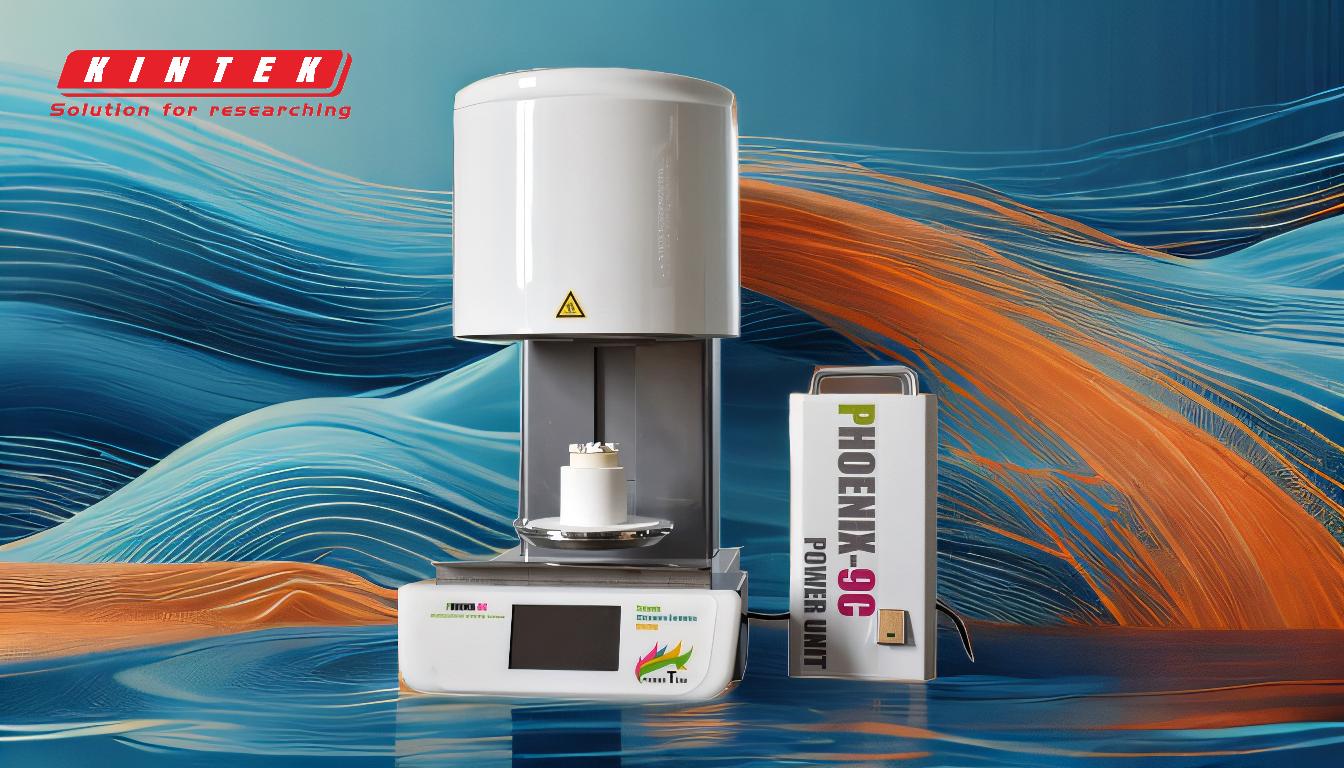
-
Sinterparameter und ihr Einfluss:
- Temperatur:Bestimmt die Sinterkinetik und die Materialeigenschaften.Höhere Temperaturen erhöhen im Allgemeinen die Verdichtung und Verdichtung, müssen aber ausgeglichen werden, um übermäßiges Kornwachstum oder Schmelzen zu vermeiden.
- Druck:Verbessert die Umlagerung der Partikel und verringert die Porosität, was zu besseren mechanischen Eigenschaften führt.Die Anwendung von Druck kann auch die Sinterzeit verkürzen.
- Partikelgröße:Kleinere Partikel vergrößern die Bindungsfläche und verbessern Eigenschaften wie Festigkeit und Leitfähigkeit.Feinere Pulver fördern eine bessere Verdichtung, erfordern aber eine sorgfältige Kontrolle der Sinterbedingungen.
- Atmosphäre:Die Wahl der Atmosphäre (z. B. Luft, Vakuum oder Inertgase wie Argon/Stickstoff) wirkt sich auf Oxidation, Verunreinigung und Sinterverhalten aus.Inerte Atmosphären werden zum Beispiel häufig verwendet, um die Oxidation beim Sintern von Metallen zu verhindern.
-
Materialspezifische Überlegungen:
- Keramiken:Reine Oxidkeramiken erfordern aufgrund der Festkörperdiffusion längere Sinterzeiten und höhere Temperaturen.Druckunterstütztes Sintern kann dazu beitragen, die Porosität zu verringern und die Verdichtung zu verbessern.
- Metalle und Legierungen:Die Sinterbedingungen müssen die Schmelzpunkte, die Legierungszusammensetzung und die Phasenumwandlungen berücksichtigen.Das Sintern in der Flüssigphase kann die Verdichtung verbessern, erfordert aber eine genaue Kontrolle des Flüssigphasenvolumens.
- Eigenschaften des Pulvers:Die anfängliche Porosität des Grünlings, die Partikelgrößenverteilung und die Zusammensetzung haben einen erheblichen Einfluss auf das endgültige gesinterte Produkt.
-
Sintertechniken:
- Druckloses Sintern:Geeignet für Materialien, die sich ohne äußeren Druck gut verdichten.Es beruht auf der Kontrolle von Temperatur und Atmosphäre.
- Druckunterstütztes Sintern:Dazu gehören Techniken wie Heißpressen und Spark-Plasma-Sintern (SPS), bei denen Druck angewendet wird, um die Verdichtung zu verbessern und die Sinterzeit zu verkürzen.
- Flüssig-Phasen-Sintern:Die Bildung einer flüssigen Phase zur Unterstützung der Verdichtung.Es wird üblicherweise für Materialien mit niedrigem Schmelzpunkt oder komplexer Zusammensetzung verwendet.
- Feldunterstütztes Sintern:Bei Techniken wie SPS werden elektrische Ströme zur gleichzeitigen Erzeugung von Wärme und Druck eingesetzt, was eine schnelle Sinterung bei niedrigeren Temperaturen ermöglicht.
-
Konstruktion und Betrieb von Öfen:
- Temperaturbereich:Der Ofen muss innerhalb des für das zu sinternde Material erforderlichen Temperaturbereichs arbeiten.Hochtemperatursintern kann die mechanischen Eigenschaften verbessern, erhöht aber die Betriebskosten.
- Gasfluss- und Atmosphärensteuerung:Die gleichmäßige Verteilung des Gasstroms sorgt für konstante Sinterbedingungen und verhindert Verunreinigungen.Die Wahl der Atmosphäre hängt von den Materialanforderungen ab.
- Strategie der Beladung:Die richtige Beladung der Teile gewährleistet eine gleichmäßige Erwärmung und minimiert Wärmegradienten, die zu Verformungen oder ungleichmäßiger Verdichtung führen können.
- Effizienz und Kosten:Faktoren wie die Masse der heißen Zone, Leistungsspitzen und Kühlraten wirken sich auf den Energieverbrauch und die Betriebskosten aus.
-
Optimierung der Leistung:
- Verdichtung:Das Erreichen einer hohen Dichte ist entscheidend für die mechanische Festigkeit und Haltbarkeit.Dies erfordert eine sorgfältige Kontrolle von Temperatur, Druck und Sinterzeit.
- Kontrolle der Porosität:Die Anfangsporosität des Grünlings und die Sinterbedingungen bestimmen die Endporosität.Eine geringere Porosität verbessert die mechanischen Eigenschaften, kann aber längere Sinterzeiten oder höhere Drücke erfordern.
- Korngrößenmanagement:Die Kontrolle des Kornwachstums während des Sinterns ist für die Erhaltung der Materialeigenschaften von entscheidender Bedeutung.Übermäßiges Kornwachstum kann die Festigkeit und Zähigkeit verringern.
-
Praktische Überlegungen für Einkäufer:
- Auswahl der Materialien:Wählen Sie Pulver mit geeigneter Partikelgröße, Zusammensetzung und Reinheit für die gewünschte Anwendung.
- Gerätekompatibilität:Sicherstellen, dass der Sinterofen und das Zubehör (z. B. Matrizen, Formen) mit den Material- und Prozessanforderungen kompatibel sind.
- Kosten-Nutzen-Analyse:Abwägung der Vorteile fortschrittlicher Sintertechniken (z. B. SPS) gegen ihre höheren Kosten und ihre Komplexität.
- Qualitätskontrolle:Durchführung robuster Qualitätskontrollmaßnahmen zur Überwachung der Sinterparameter und zur Gewährleistung einer gleichbleibenden Produktleistung.
Durch das Verständnis und die Anwendung dieser Richtlinien können Hersteller und Einkäufer Sinterprozesse optimieren, um Hochleistungsmaterialien zu erhalten, die auf spezifische Anwendungen zugeschnitten sind.
Zusammenfassende Tabelle:
Wichtige Sinterparameter | Einfluss |
---|---|
Temperatur | Bestimmt die Sinterkinetik und die Materialeigenschaften. |
Druck | Verbessert die Umlagerung von Partikeln und verringert die Porosität. |
Partikelgröße | Kleinere Partikel verbessern die Festigkeit und Leitfähigkeit. |
Atmosphäre | Beeinflusst die Oxidation, die Verunreinigung und das Sinterverhalten. |
Sintertechniken | Drucklose, druckunterstützte, Flüssigphasen- und feldunterstützte Sintertechniken. |
Konstruktion des Ofens | Temperaturbereich, Gasfluss und Beladungsstrategie sind entscheidend für die Effizienz. |
Optimierung der Leistung | Konzentrieren Sie sich auf Verdichtung, Porositätskontrolle und Korngrößenmanagement. |
Optimieren Sie Ihren Sinterprozess noch heute - Kontaktieren Sie unsere Experten für maßgeschneiderte Lösungen!