Die Pulvermetallurgie ist ein vielseitiges Fertigungsverfahren zur Herstellung von Sinterteilen mit komplizierten Formen und genauen Abmessungen.Das Verfahren umfasst in der Regel drei Hauptschritte: die Auswahl des Pulvers, die Verdichtung und das Sintern.Fortschrittliche Techniken wie Metallspritzguss (MIM), heißisostatisches Pressen (HIP), additive Fertigung und Spark Plasma Sintering (SPS) haben die Möglichkeiten der Pulvermetallurgie jedoch erweitert.Diese Verfahren ermöglichen die Herstellung komplexer Komponenten für Branchen wie Automobilbau, Luft- und Raumfahrt und Schneidwerkzeuge.Die Wahl des Verfahrens hängt von den gewünschten Eigenschaften des Endprodukts ab, darunter Festigkeit, Härte und Maßhaltigkeit.
Die wichtigsten Punkte werden erklärt:
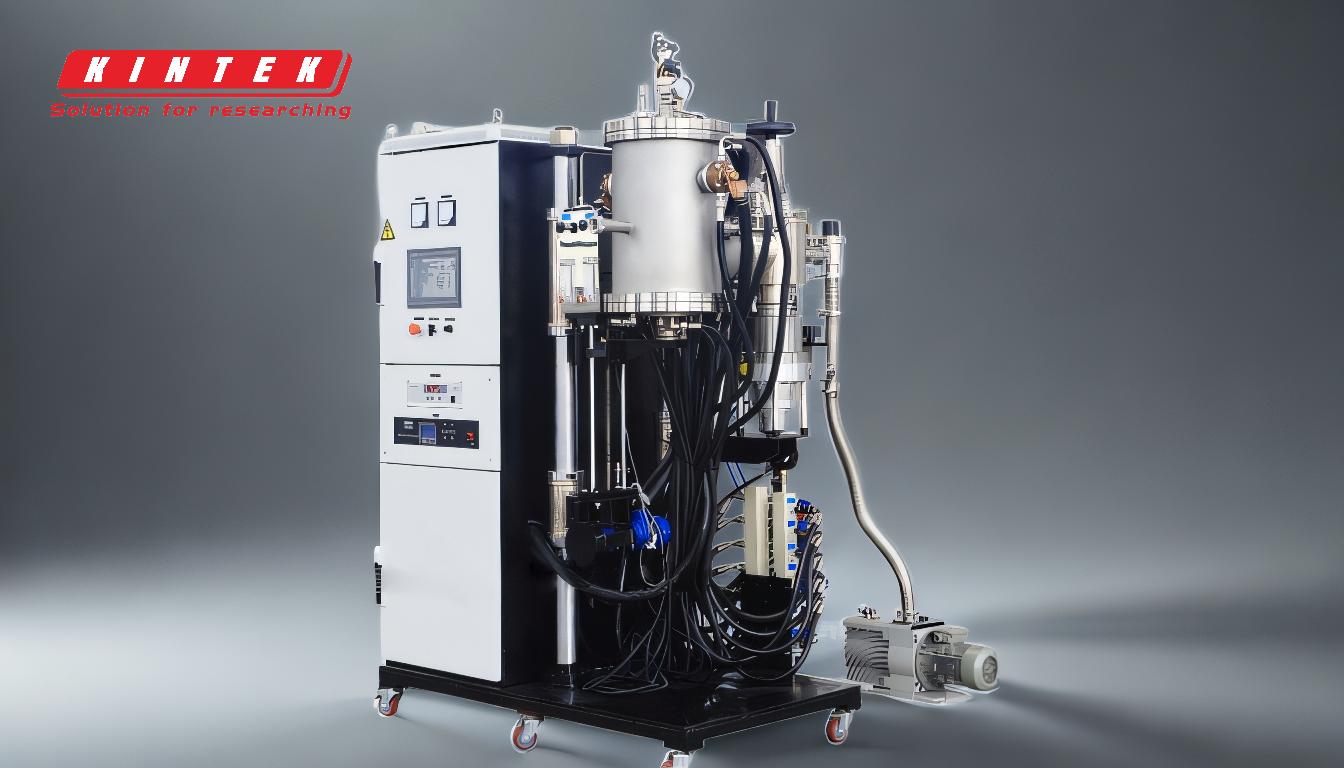
-
Traditionelle Pulvermetallurgie (Pressen und Sintern)
- Auswahl des Pulvers:Das Verfahren beginnt mit der Auswahl von Metallpulvern wie Eisen, Nickel, Molybdän oder Kupfer, die oft mit Schmiermitteln gemischt werden, um den Fluss und die Verdichtung zu verbessern.
- Verdichtung:Das Pulver wird bei Raumtemperatur in eine Matrize gepresst, um ein \"grünes" Teil mit anfänglicher Festigkeit zu formen.Dieser Schritt bestimmt die Form und Dichte des Teils.
- Sintern:Das Grünteil wird in einem Ofen bei Temperaturen knapp unter dem Schmelzpunkt des Metalls erhitzt.Dadurch werden die Partikel miteinander verbunden und die Festigkeit und Härte erhöht, ohne dass sich das Material verflüssigt.Häufig werden kontrollierte atmosphärische Bedingungen verwendet, um Oxidation zu verhindern.
-
Metall-Spritzgießen (MIM)
- Pulver mischen:Feine Metallpulver werden mit einem thermoplastischen Bindemittel gemischt, um ein Ausgangsmaterial zu erhalten.
- Spritzgießen:Das Ausgangsmaterial wird unter hohem Druck in eine Form gespritzt, um ein Grünteil zu formen.
- Entbindern:Das Bindemittel wird durch thermische oder chemische Verfahren entfernt.
- Sintern:Das Teil wird gesintert, um seine volle Dichte und mechanischen Eigenschaften zu erreichen.MIM ist ideal für die Herstellung kleiner, komplexer Teile mit hoher Präzision.
-
Heiß-Isostatisches Pressen (HIP)
- Pulver-Verdichtung:Metallpulver wird in eine Form gegeben und gleichzeitig einem hohen Druck und einer hohen Temperatur ausgesetzt.
- Sintern:Durch die Kombination von Hitze und Druck wird das Pulver verdichtet, wodurch ein nahezu endkonturiertes Teil mit minimaler Porosität entsteht.HIP wird für Hochleistungskomponenten verwendet, die hervorragende mechanische Eigenschaften erfordern.
-
Additive Fertigung (3D-Druck)
- Pulverbettfusion:Metallpulver wird mit einem Laser- oder Elektronenstrahl selektiv aufgeschmolzen, um Teile Schicht für Schicht aufzubauen.
- Binder Jetting:Ein flüssiges Bindemittel wird selektiv auf ein Pulverbett aufgebracht, um ein Grünteil zu erzeugen, das anschließend gesintert wird.
- Direkte Energieabscheidung:Metallpulver wird in ein durch einen Laser- oder Elektronenstrahl erzeugtes Schmelzbad eingebracht, so dass vorhandene Teile repariert oder mit neuem Material versehen werden können.Die additive Fertigung ist ideal für das Prototyping und die Herstellung komplexer Geometrien.
-
Funkenplasmasintern (SPS)
- Vorbereitung des Pulvers:Metallpulver wird in eine Graphitmatrize gefüllt.
- Sintern:Es wird ein gepulster elektrischer Strom angelegt, der ein Plasma erzeugt, das das Pulver schnell erhitzt.Die gleichzeitige Anwendung von Druck führt zu einer schnellen Verdichtung.SPS wird für hochentwickelte Werkstoffe, einschließlich Keramik und Verbundwerkstoffe, eingesetzt, da sich damit hohe Dichten bei niedrigeren Temperaturen erzielen lassen.
-
Nachbehandlungsverfahren
- Bearbeitungen:Gesinterte Teile erfordern möglicherweise eine zusätzliche Bearbeitung, um präzise Abmessungen oder Oberflächengüten zu erzielen.Für harte Materialien wie Keramik werden häufig Diamantwerkzeuge oder Ultraschallbearbeitung eingesetzt.
- Montage:Bei keramischen Teilen werden die Komponenten durch Metallisierung und Hartlöten verbunden.Dies ist üblich bei Anwendungen, die elektrische Leitfähigkeit oder hermetische Abdichtung erfordern.
- Wärmebehandlung:Zusätzliche Wärmebehandlungen, wie Anlassen oder Einsatzhärten, können zur Verbesserung der mechanischen Eigenschaften durchgeführt werden.
-
Anwendungen von Sinterteilen
- Autoindustrie:Sinterteile werden aufgrund ihrer Festigkeit und Verschleißbeständigkeit häufig für Zahnräder, Nockenwellen und Ventilsitze verwendet.
- Schneidende Werkzeuge:Gesinterte Hartmetallwerkzeuge sind für ihre Härte und Haltbarkeit bekannt.
- Filter:Gesinterte Metallfilter werden in Anwendungen eingesetzt, die eine präzise Filtration erfordern, wie z. B. in der chemischen und pharmazeutischen Industrie.
Durch die Kenntnis dieser Verfahren können die Hersteller die am besten geeignete Technik zur Herstellung von Sinterteilen auswählen, die den spezifischen Leistungsanforderungen und Kostenerwägungen entsprechen.
Zusammenfassende Tabelle:
Methode | Wichtige Schritte | Anwendungen |
---|---|---|
Traditionelle Pulvermetallurgie | Pulverauswahl, Verdichtung, Sintern | Kfz-Zahnräder, Nockenwellen, Ventilsitze |
Metall-Spritzgießen (MIM) | Pulvermischen, Spritzgießen, Entbindern, Sintern | Kleine, komplexe Teile mit hoher Präzision |
Heiß-Isostatisches Pressen (HIP) | Verdichtung des Pulvers, Sintern unter hohem Druck und hoher Temperatur | Hochleistungskomponenten mit minimaler Porosität |
Additive Fertigung | Pulverbettschmelzen, Binder-Jetting, direkte Energieabscheidung | Prototyping, komplexe Geometrien |
Spark-Plasma-Sintern (SPS) | Pulveraufbereitung, schnelles Sintern mit gepulstem elektrischem Strom und Druck | Moderne Werkstoffe wie Keramik und Verbundwerkstoffe |
Nachbehandlungsprozesse | Bearbeitung, Montage, Wärmebehandlung | Verbesserung der mechanischen Eigenschaften und der Oberflächenbeschaffenheit |
Entdecken Sie die beste pulvermetallurgische Lösung für Ihren Bedarf. Kontaktieren Sie unsere Experten noch heute !