Unter Beschichtung versteht man das Aufbringen einer dünnen Materialschicht auf ein Substrat, um dessen Eigenschaften zu verbessern, z. B. Korrosionsbeständigkeit, Verschleißfestigkeit, elektrische Leitfähigkeit oder ästhetische Wirkung.Dieses Verfahren ist in Branchen wie der Automobilindustrie, der Luft- und Raumfahrt, der Elektronik und der Fertigung weit verbreitet.Die Abscheidetechniken variieren je nach den gewünschten Eigenschaften, dem Substratmaterial und den Anwendungsanforderungen.Zu den gängigen Verfahren gehören die physikalische Abscheidung aus der Gasphase (PVD), die chemische Abscheidung aus der Gasphase (CVD), die galvanische Abscheidung und das thermische Spritzen.Jede Methode hat ihre eigenen Vorteile und Grenzen und eignet sich daher für bestimmte Anwendungen.Das Verständnis des Abscheidungsprozesses ist entscheidend für die Auswahl der richtigen Technik, um die gewünschten Beschichtungseigenschaften zu erreichen.
Die wichtigsten Punkte werden erklärt:
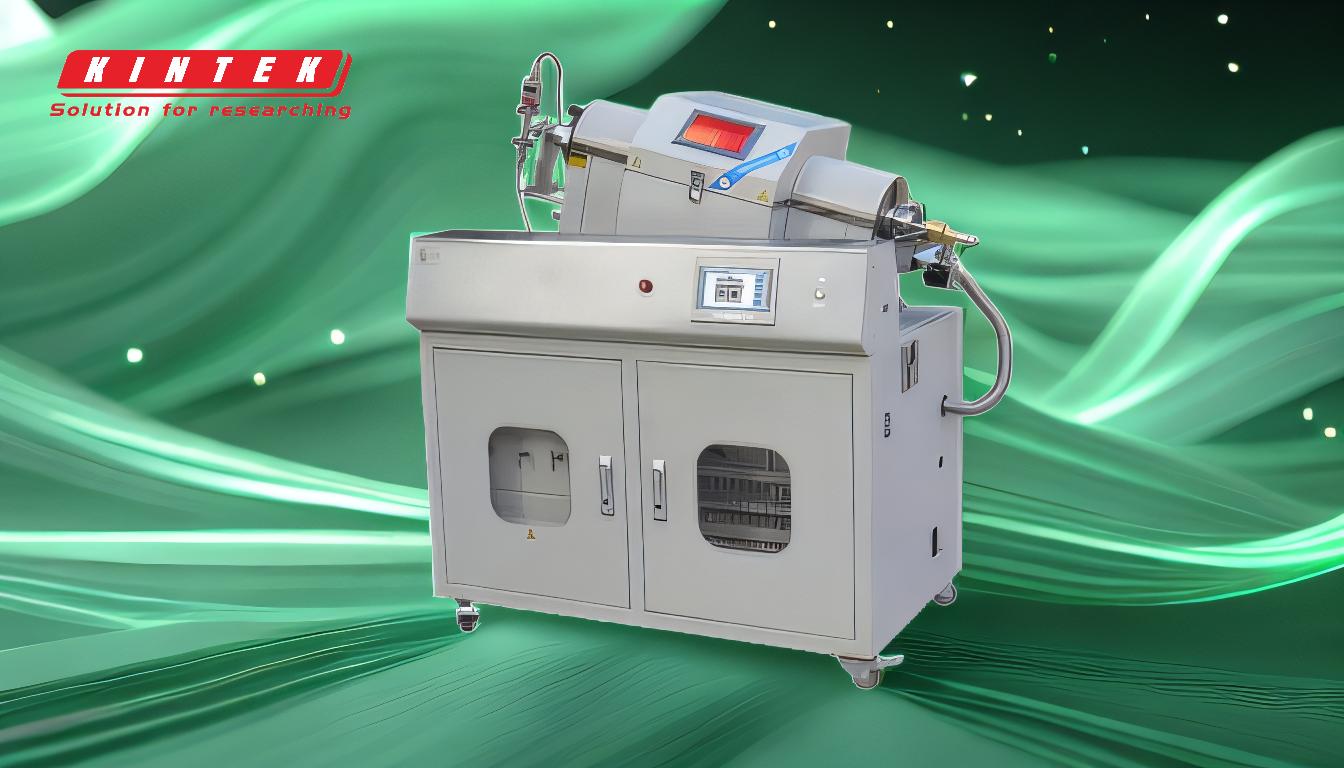
-
Definition von Coating Deposition:
- Unter Beschichtung versteht man das Aufbringen einer dünnen Materialschicht auf ein Substrat.Diese Schicht kann je nach Anwendung aus Metall, Keramik, Polymer oder Verbundwerkstoff bestehen.
- Das Hauptziel besteht darin, die Leistung des Substrats zu verbessern, indem Eigenschaften wie Härte, Korrosionsbeständigkeit, Wärmeisolierung oder elektrische Leitfähigkeit erhöht werden.
-
Die Bedeutung der Beschichtung:
- Schutz:Beschichtungen schützen Substrate vor Umwelteinflüssen wie Korrosion, Oxidation und Verschleiß.
- Funktionsweise:Sie können funktionelle Eigenschaften wie elektrische Leitfähigkeit oder Wärmedämmung hinzufügen.
- Ästhetik:Beschichtungen werden häufig verwendet, um das Aussehen von Produkten zu verbessern, z. B. als dekorative Oberflächenbeschichtung von Konsumgütern.
-
Gängige Beschichtungstechniken:
-
Physikalische Gasphasenabscheidung (PVD):
- Beim PVD-Verfahren wird das Beschichtungsmaterial im Vakuum verdampft und auf das Substrat aufgebracht.Zu den Techniken gehören Sputtern und Verdampfen.
- Es wird für harte, verschleißfeste Beschichtungen wie Titannitrid (TiN) auf Schneidwerkzeugen verwendet.
-
Chemische Gasphasenabscheidung (CVD):
- Bei der CVD-Beschichtung werden chemische Reaktionen genutzt, um eine Beschichtung aus der Gasphase auf das Substrat aufzubringen.Das Verfahren ist ideal für Hochtemperaturanwendungen und erzeugt gleichmäßige, hochwertige Beschichtungen.
- Zu den Anwendungen gehören die Halbleiterherstellung und Schutzbeschichtungen auf Turbinenschaufeln.
-
Galvanische Beschichtung:
- Bei der Galvanotechnik wird mit Hilfe von elektrischem Strom eine Metallschicht auf ein leitfähiges Substrat aufgebracht.Es wird häufig für dekorative Oberflächen, Korrosionsschutz und zur Verbesserung der elektrischen Leitfähigkeit verwendet.
-
Thermisches Spritzen:
- Bei dieser Technik wird das Beschichtungsmaterial geschmolzen und auf das Substrat gesprüht.Es wird für dicke Beschichtungen und große Oberflächen verwendet, wie z. B. in der Luft- und Raumfahrt und in der Automobilindustrie.
-
Physikalische Gasphasenabscheidung (PVD):
-
Faktoren, die die Abscheidung beeinflussen:
- Material des Substrats:Die Wahl des Beschichtungsverfahrens hängt von den Eigenschaften des Substrats ab, z. B. von der thermischen Stabilität und der Oberflächenrauhigkeit.
- Material der Beschichtung:Verschiedene Materialien erfordern spezifische Abscheidetechniken, um die gewünschten Eigenschaften zu erzielen.
- Anforderungen an die Anwendung:Der Verwendungszweck des beschichteten Produkts bestimmt die Schichtdicke, die Haftfestigkeit und andere Leistungskriterien.
-
Vorteile und Beschränkungen:
-
Vorteile:
- Bessere Haltbarkeit und Leistung von Substraten.
- Die Möglichkeit, Beschichtungen für spezifische Anwendungen anzupassen.
- Verbesserte Produktlebensdauer und geringere Wartungskosten.
-
Beschränkungen:
- Hohe Ausrüstungs- und Betriebskosten für einige Techniken.
- Komplexität beim Erreichen gleichmäßiger Beschichtungen auf komplexen Geometrien.
- Umwelt- und Sicherheitsbedenken, insbesondere bei Verfahren auf chemischer Basis.
-
Vorteile:
-
Anwendungen der Beschichtungsabscheidung:
- Automobilindustrie:Beschichtungen werden auf Triebwerkskomponenten, Bremssystemen und Zierleisten verwendet, um Leistung und Ästhetik zu verbessern.
- Luft- und Raumfahrt:Schutzbeschichtungen werden auf Turbinenschaufeln, Rumpf und andere kritische Komponenten aufgetragen, um extremen Bedingungen standzuhalten.
- Elektronik:Dünne Schichten werden auf Halbleitern, Schaltkreisen und Displays aufgebracht, um die elektrischen Eigenschaften zu verbessern.
- Herstellung:Schneidwerkzeuge, Formen und Matrizen werden beschichtet, um die Verschleißfestigkeit zu erhöhen und die Lebensdauer zu verlängern.
Wenn die Hersteller den Beschichtungsprozess und seine verschiedenen Techniken verstehen, können sie die am besten geeignete Methode auswählen, um die gewünschten Beschichtungseigenschaften für ihre spezifischen Anwendungen zu erreichen.Dies gewährleistet eine optimale Leistung, Haltbarkeit und Kosteneffizienz der beschichteten Produkte.
Zusammenfassende Tabelle:
Aspekt | Einzelheiten |
---|---|
Definition | Auftragen einer dünnen Materialschicht zur Verbesserung der Substrateigenschaften. |
Wichtigste Vorteile | Korrosionsbeständigkeit, Verschleißfestigkeit, elektrische Leitfähigkeit, Ästhetik. |
Gängige Techniken | PVD, CVD, Galvanotechnik, thermisches Spritzen. |
Anwendungen | Automobilindustrie, Luft- und Raumfahrt, Elektronik, Fertigung. |
Vorteile | Erhöhte Haltbarkeit, maßgeschneiderte Beschichtungen, Kosteneffizienz. |
Beschränkungen | Hohe Kosten, komplexe Geometrien, Umweltprobleme. |
Entdecken Sie die beste Beschichtungslösung für Ihre Anforderungen. Kontaktieren Sie unsere Experten noch heute !