Das kaltisostatische Pressverfahren (CIP) ist eine Pulververdichtungstechnik, bei der Flüssigkeitsdruck verwendet wird, um Materialien bei Umgebungstemperaturen gleichmäßig zu verdichten. Dabei wird Pulver oder ein vorgeformtes Teil in eine flexible Form gegeben, die dann aus allen Richtungen einer Hochdruckflüssigkeit (häufig Wasser oder einer Öl-Wasser-Mischung) ausgesetzt wird. Diese Methode gewährleistet eine gleichmäßige Dichte und Formbeständigkeit und eignet sich daher ideal für Materialien wie Keramik, Metalle und Verbundwerkstoffe. CIP wird in Wet-Bag- und Dry-Bag-Verfahren unterteilt, je nachdem, wie die Form mit dem Druckmedium interagiert. Es wird häufig in Branchen eingesetzt, die hochdichte, komplex geformte Komponenten erfordern, beispielsweise in der Luft- und Raumfahrt, der Medizintechnik und der Werkzeugherstellung.
Wichtige Punkte erklärt:
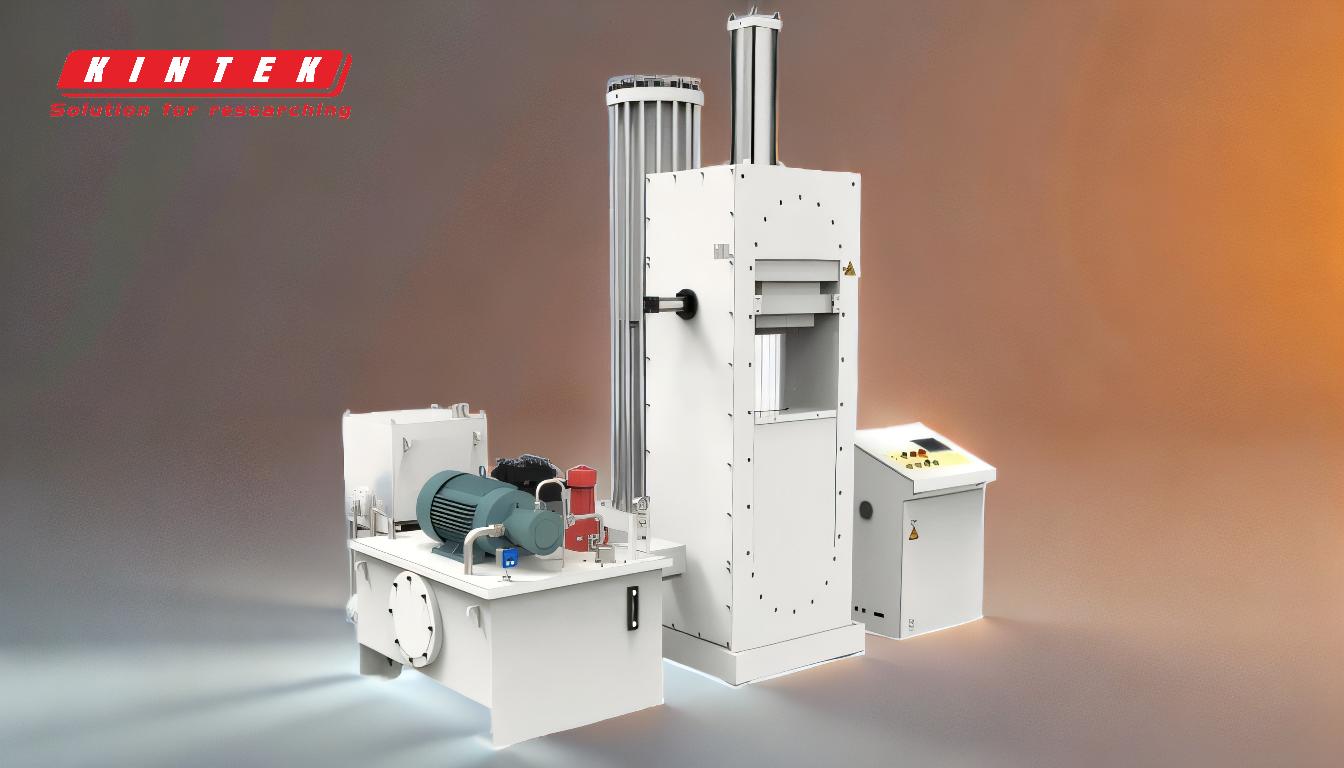
-
Definition und Prozess des kaltisostatischen Pressens (CIP):
- CIP ist eine Pulververdichtungsmethode, die bei Raumtemperatur einen gleichmäßigen hydrostatischen Druck auf Materialien ausübt.
- Das Material wird in eine flexible Form gegeben, die dann in ein unter Druck stehendes flüssiges Medium (z. B. Wasser oder ein Öl-Wasser-Gemisch) getaucht wird.
- Der Druck, der bis zu 100.000 psi erreichen kann, wird gleichmäßig verteilt und sorgt so für eine gleichmäßige Dichte und Form.
-
Nassbeutel- vs. Trockenbeutel-Methoden:
- Wet-Bag-Methode: Die Form wird nach jedem Zyklus aus dem Druckbehälter entfernt. Diese Methode eignet sich für die Produktion in kleinem Maßstab oder für den Prototypenbau.
- Trockenbeutelmethode: Die Form verbleibt im Druckbehälter und nur das Material wird geladen und entladen. Diese Methode ist für die Produktion in großem Maßstab effizienter.
-
Anwendungen von CIP:
-
CIP wird bei der Pulverformung verschiedener Materialien eingesetzt, darunter:
- Feuerfeste Materialien und Isolatoren.
- Isotroper Graphit und hochschmelzende Metalle.
- Hartmetalle und Werkzeugstahl.
- Gesinterte Filter, künstliche Knochen und Harzpulver.
- Lebensmittelverarbeitende Industrie.
-
CIP wird bei der Pulverformung verschiedener Materialien eingesetzt, darunter:
-
Vorteile von CIP:
- Gleichmäßige Dichte- und Druckverteilung, was zu einer gleichbleibenden Produktqualität führt.
- Fähigkeit zur Herstellung komplexer Formen und großer Komponenten.
- Geeignet für eine Vielzahl von Materialien, einschließlich spröder und schwer zu verdichtender Pulver.
-
Im CIP verwendete Ausrüstung:
- Die Kernausrüstung ist die isostatische Presse , das aus einer Druckkammer, einer Pumpe zum Unterdrucksetzen des flüssigen Mediums und einer flexiblen Form besteht.
- Die Druckkammer ist für zyklische Belastungen und extreme Drücke ausgelegt.
-
Prozessparameter:
- Die Druckwerte liegen je nach Material und Anwendung typischerweise zwischen 15.000 und 100.000 psi.
- Das flüssige Medium enthält häufig Korrosionsinhibitoren zum Schutz der Ausrüstung und der Form.
-
Branchen, die CIP nutzen:
- Luft- und Raumfahrt: Zur Herstellung hochfester, leichter Bauteile.
- Medizin: Zur Herstellung künstlicher Knochen und Implantate.
- Werkzeuge: Zur Herstellung langlebiger Schneidwerkzeuge und Matrizen.
- Lebensmittelverarbeitung: Zum Verdichten von pulverförmigen Lebensmitteln.
Durch den Einsatz des CIP-Verfahrens können Hersteller hochdichte, komplex geformte Komponenten mit hervorragenden Materialeigenschaften herstellen, was es zu einer vielseitigen und unverzichtbaren Technik in der modernen Fertigung macht.
Übersichtstabelle:
Aspekt | Einzelheiten |
---|---|
Verfahren | Gleichmäßiger hydrostatischer Druck bei Raumtemperatur unter Verwendung eines flüssigen Mediums. |
Methoden | Nassbeutel (klein) und Trockenbeutel (groß). |
Anwendungen | Keramik, Metalle, Verbundwerkstoffe, künstliche Knochen und Lebensmittelverarbeitung. |
Vorteile | Gleichmäßige Dichte, komplexe Formen und Kompatibilität mit spröden Materialien. |
Druckbereich | 15.000 bis 100.000 psi. |
Branchen | Luft- und Raumfahrt, Medizin, Werkzeugbau und Lebensmittelverarbeitung. |
Entdecken Sie, wie der CIP-Prozess Ihre Fertigung verändern kann – Kontaktieren Sie noch heute unsere Experten !