Sintern und Schmelzen sind beides Verfahren zum Verbinden oder Verfestigen von Werkstoffen, die sich jedoch hinsichtlich ihrer Mechanismen, ihres Energiebedarfs und ihrer Anwendungen erheblich unterscheiden. Beim Sintern werden die Partikel eines Materials durch Hitze und Druck verdichtet und verbunden, ohne dass das Material verflüssigt wird, so dass es sich um ein energieärmeres Verfahren handelt. Beim Schmelzen hingegen wird ein Material bis zu seinem Schmelzpunkt erhitzt und verflüssigt, bevor es sich in einer neuen Form verfestigt. Während das Schmelzen ideal für die Herstellung starker, homogener Verbindungen ist, eignet sich das Sintern besser für die Herstellung poröser oder komplexer Strukturen mit kontrollierten Eigenschaften. Im Folgenden werden die wichtigsten Unterschiede und Anwendungen dieser Verfahren im Detail erläutert.
Die wichtigsten Punkte werden erklärt:
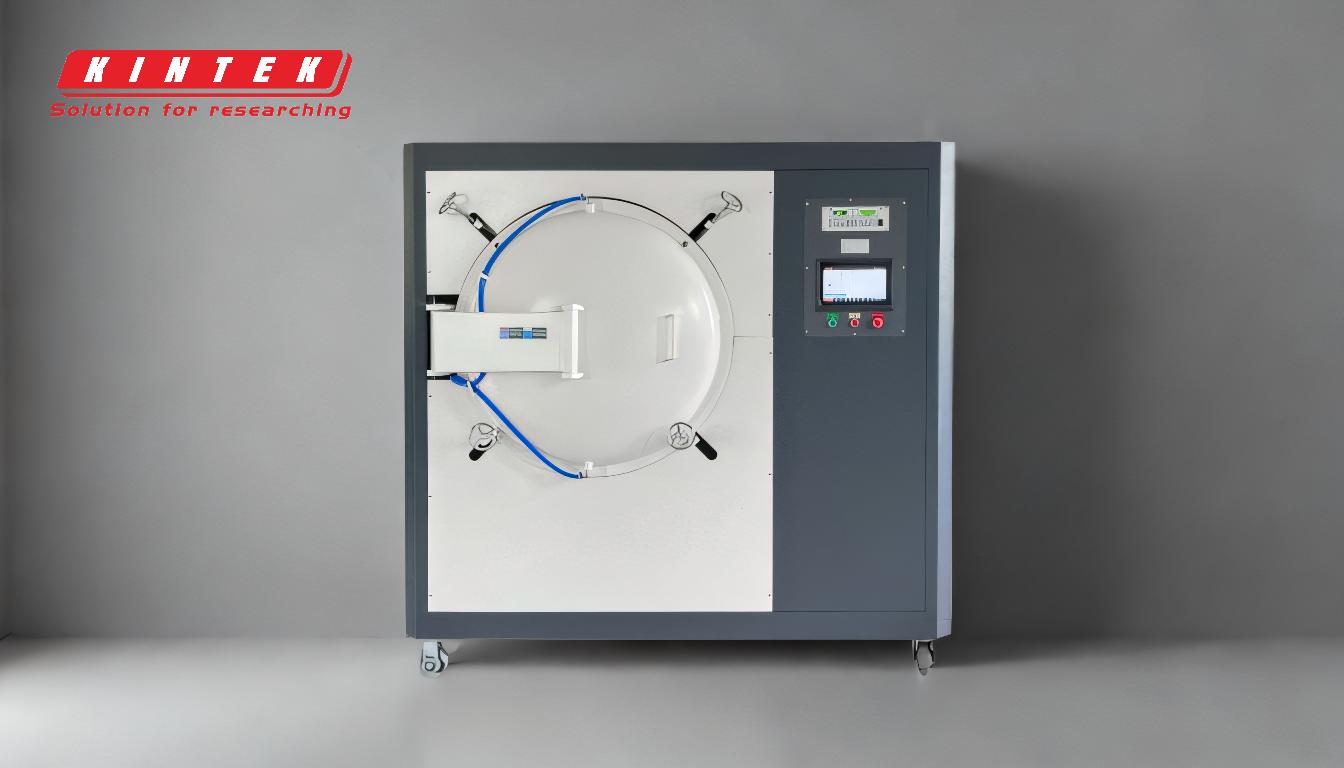
-
Definition und Mechanismus:
- Fusion (Schmelzen): Bei der Fusion wird ein Material bis zu seinem Schmelzpunkt erhitzt, wo es von einem festen in einen flüssigen Zustand übergeht. Dieser Prozess erfordert erhebliche Energie, um die latente Schmelzwärme des Materials zu überwinden. Nach der Verflüssigung kann das Material umgeformt oder mit anderen Materialien verbunden werden, bevor es abkühlt und sich verfestigt.
- Sintern: Beim Sintern werden Partikel eines Materials durch Hitze und Druck verdichtet und verbunden, ohne dass der Schmelzpunkt erreicht wird. Die Partikel verschmelzen an ihren Grenzen und bilden eine feste Struktur. Dieser Prozess findet unterhalb der Schmelztemperatur des Materials statt und ist daher weniger energieintensiv.
-
Energiebedarf:
- Fusion: Erfordert hohe Temperaturen, um den Schmelzpunkt des Materials zu erreichen, was energieintensiv sein kann, insbesondere bei Materialien mit hohem Schmelzpunkt wie Metallen.
- Sintern: Funktioniert bei niedrigeren Temperaturen, da keine Verflüssigung erforderlich ist. Dies macht das Sintern für bestimmte Anwendungen energie- und kosteneffizienter.
-
Materialzustand während der Verarbeitung:
- Fusion: Das Material geht in einen flüssigen Zustand über, der eine vollständige Homogenisierung und die Bildung starker, kontinuierlicher Bindungen ermöglicht.
- Sintern: Das Material bleibt in einem festen Zustand, wobei sich die Partikel an der Oberfläche verbinden. Dies kann zu einer porösen Struktur führen, die für bestimmte Anwendungen wie Filter oder leichte Bauteile wünschenswert sein kann.
-
Anwendungen:
- Fusion: Wird häufig beim Schweißen, Gießen und bei der additiven Fertigung (z. B. beim 3D-Druck mit Metallpulvern) verwendet. Es ist ideal für die Herstellung dichter, homogener Strukturen mit hoher Festigkeit und Integrität.
- Sintern: Weit verbreitet in der Pulvermetallurgie, Keramik und bei der Herstellung von Verbundwerkstoffen. Es eignet sich für die Herstellung komplexer Formen, poröser Strukturen und Komponenten mit kontrollierter Porosität oder thermischen Eigenschaften.
-
Resultierende Materialeigenschaften:
- Fusion: Erzeugt dichte, nicht poröse Materialien mit hoher mechanischer Festigkeit und Gleichmäßigkeit. Der flüssige Zustand ermöglicht die Beseitigung von Hohlräumen und Defekten.
- Sintern: Das Ergebnis sind Materialien mit unterschiedlichen Porositätsgraden, abhängig von den Prozessparametern. Dies kann bei Anwendungen, die leichte Materialien, Wärmedämmung oder kontrollierte Permeabilität erfordern, von Vorteil sein.
-
Prozesskontrolle und Komplexität:
- Fusion: Erfordert eine präzise Steuerung der Temperatur und der Abkühlungsgeschwindigkeit, um Defekte wie Risse oder Verformungen zu vermeiden. Das Verfahren ist komplexer, da der flüssige Zustand des Materials gesteuert werden muss.
- Sintern: Bietet eine bessere Kontrolle über die Mikrostruktur und Porosität des Endmaterials. Es ist weniger komplex in Bezug auf das Temperaturmanagement, erfordert aber eine sorgfältige Kontrolle des Drucks und der Partikelgrößenverteilung.
-
Kompatibilität der Materialien:
- Fusion: Geeignet für Materialien, die geschmolzen werden können, ohne sich zu zersetzen, wie Metalle und einige Polymere. Nicht ideal für Materialien, die sich bei hohen Temperaturen zersetzen oder oxidieren.
- Sintern: Kompatibel mit einer größeren Anzahl von Materialien, einschließlich Keramik, Metallen und Verbundwerkstoffen. Es ist besonders nützlich für Materialien, die den für das Schmelzen erforderlichen hohen Temperaturen nicht standhalten.
-
Wirtschaftliche und ökologische Erwägungen:
- Fusion: Höherer Energieverbrauch und höhere Kosten aufgrund der erforderlichen hohen Temperaturen. Außerdem kann eine zusätzliche Nachbearbeitung zur Beseitigung von Mängeln erforderlich sein.
- Sintern: Wirtschaftlicher und umweltfreundlicher aufgrund des geringeren Energiebedarfs. Außerdem wird der Materialabfall reduziert, da häufig pulverförmige Materialien verwendet werden, die genau abgemessen und geformt werden können.
Zusammenfassend lässt sich sagen, dass sowohl das Schmelzen als auch das Sintern zum Verbinden oder Verfestigen von Werkstoffen verwendet werden, sich aber in ihren Mechanismen, ihrem Energiebedarf und ihren Anwendungen grundlegend unterscheiden. Das Schmelzen ist ideal für die Herstellung dichter, fester Strukturen, während das Sintern besser für die Herstellung poröser oder komplexer Komponenten mit kontrollierten Eigenschaften geeignet ist. Das Verständnis dieser Unterschiede ist entscheidend für die Auswahl des geeigneten Verfahrens auf der Grundlage der gewünschten Materialeigenschaften und Anwendungsanforderungen.
Zusammenfassende Tabelle:
Aspekt | Fusion (Schmelzen) | Sintern |
---|---|---|
Definition | Erhitzt das Material bis zum Schmelzpunkt und macht es flüssig. | Verdichtet und bindet Partikel, ohne das Material zu verflüssigen. |
Energiebedarf | Hohe Energie aufgrund der Schmelzpunkttemperaturen. | Geringere Energie, da es unterhalb des Schmelzpunktes arbeitet. |
Materieller Zustand | Flüssiger Zustand für die Homogenisierung. | Festkörper mit Partikelbindung an Oberflächen. |
Anwendungen | Schweißen, Gießen, additive Fertigung (z. B. 3D-Druck). | Pulvermetallurgie, Keramik, Verbundwerkstoffe. |
Materialeigenschaften | Dicht, porenfrei, hohe Festigkeit. | Porös, leicht, kontrollierte Durchlässigkeit. |
Komplexität der Prozesse | Erfordert eine präzise Steuerung von Temperatur und Abkühlgeschwindigkeit. | Leichteres Temperaturmanagement, aber Druck- und Partikelgrößenkontrolle erforderlich. |
Kompatibilität der Materialien | Metalle, einige Polymere. Nicht geeignet für Materialien, die sich bei hohen Temperaturen zersetzen. | Keramiken, Metalle, Verbundwerkstoffe. Ideal für hitzeempfindliche Materialien. |
Wirtschaft und Umwelt | Höhere Energiekosten, mögliche Nachbearbeitung. | Geringerer Energieverbrauch, weniger Abfall, kosteneffizient. |
Benötigen Sie Hilfe bei der Auswahl des richtigen Verfahrens für Ihr Material? Kontaktieren Sie unsere Experten noch heute !