Plasmanitrieren und Nitrocarburieren sind beides thermochemische Oberflächenhärtungsverfahren, die zur Verbesserung der mechanischen Eigenschaften von Metallteilen, wie Härte, Verschleißfestigkeit und Ermüdungsfestigkeit, eingesetzt werden.Sie unterscheiden sich jedoch in ihren Mechanismen, den in das Metall eingebrachten Elementen und den daraus resultierenden Oberflächeneigenschaften.Beim Plasmanitrieren wird Stickstoff durch eine Plasmaumgebung in die Metalloberfläche diffundiert, während beim Nitrocarburieren sowohl Stickstoff als auch Kohlenstoff in die Oberflächenschicht eingebracht werden.Diese Unterschiede führen zu einzigartigen Vorteilen und Anwendungen für jedes Verfahren.
Die wichtigsten Punkte werden erklärt:
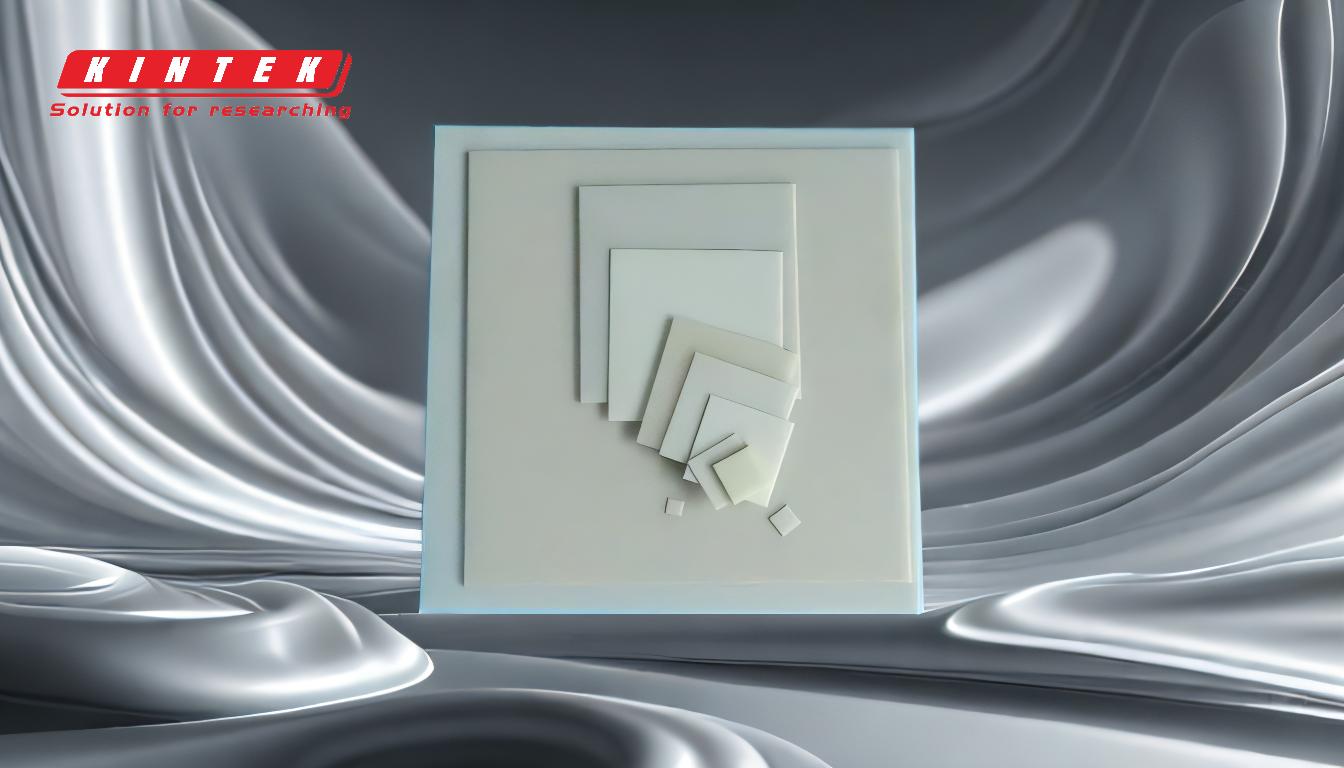
-
Mechanismus der Prozesse:
- Plasma-Nitrieren:Bei diesem Verfahren wird in einer Plasmaumgebung Stickstoffgas ionisiert, das dann in die Metalloberfläche diffundiert.Das Plasma wird durch Anlegen einer Hochspannung zwischen dem Werkstück (Kathode) und den Kammerwänden (Anode) erzeugt.Die ionisierten Stickstoffatome werden in Richtung des Werkstücks beschleunigt und bilden eine harte Nitridschicht auf der Oberfläche.
- Nitrocarburieren:Bei diesem Verfahren werden sowohl Stickstoff als auch Kohlenstoff gleichzeitig in die Metalloberfläche eingebracht.Es wird in der Regel in einer gasförmigen Atmosphäre durchgeführt, die Ammoniak (für Stickstoff) und ein kohlenstoffreiches Gas (wie Kohlendioxid oder Methan) enthält.Durch die kombinierte Diffusion von Stickstoff und Kohlenstoff entsteht eine Verbindungsschicht und eine darunter liegende Diffusionszone.
-
Eingeführte Elemente:
- Plasma-Nitrieren:Nur Stickstoff wird in die Metalloberfläche eingebracht, wodurch sich Nitride bilden, die die Härte und Verschleißfestigkeit erhöhen.
- Nitrocarburieren:Es werden sowohl Stickstoff als auch Kohlenstoff eingebracht, was zu einer Verbundschicht führt, die reich an Karbonitriden und Nitriden ist und für eine verbesserte Verschleißfestigkeit und geringere Reibung sorgt.
-
Temperatur- und Prozesskontrolle:
- Plasma-Nitrieren:Arbeitet bei unterkritischen Temperaturen (typischerweise zwischen 350°C und 600°C), was den Verzug minimiert und eine präzise Steuerung der Nitridschichtdicke ermöglicht.
- Nitrocarburieren:Funktioniert auch bei unterkritischen Temperaturen (normalerweise zwischen 500°C und 600°C), aber das Vorhandensein von Kohlenstoff erfordert eine sorgfältige Kontrolle der Gaszusammensetzung, um die gewünschten Oberflächeneigenschaften zu erzielen.
-
Oberflächeneigenschaften:
- Plasma-Nitrieren:Erzeugt eine harte, verschleißfeste Oberfläche mit minimaler Verformung.Das Verfahren eignet sich besonders gut für komplexe Geometrien und dünnwandige Bauteile, da es auch komplizierte Formen gleichmäßig behandeln kann.
- Nitrocarburieren:Erzeugt eine Verbundschicht mit hervorragender Verschleißfestigkeit und verringerter Reibung und eignet sich daher für Anwendungen, die verbesserte Gleiteigenschaften erfordern.Das Verfahren erhöht auch die Korrosionsbeständigkeit durch die Bildung einer dichten Verbundschicht.
-
Anwendungen:
- Plasma-Nitrieren:Wird häufig für Hochpräzisionsbauteile wie Zahnräder, Matrizen und Gussformen verwendet, bei denen Härte und Verschleißfestigkeit entscheidend sind.Es wird auch für Werkstoffe wie rostfreien Stahl und Titan bevorzugt, die von der Bildung einer harten Nitridschicht profitieren.
- Nitrocarburieren:Ideal für Bauteile, die gleitendem Verschleiß ausgesetzt sind, wie Kurbelwellen, Nockenwellen und Hydraulikzylinder.Das Verfahren wird auch für Teile verwendet, die eine verbesserte Dauerfestigkeit und Korrosionsbeständigkeit erfordern.
-
Vorteile und Beschränkungen:
- Plasma-Nitrieren:Bietet präzise Kontrolle über die Nitridschicht, ausgezeichnete Oberflächenhärte und minimalen Verzug.Es erfordert jedoch eine spezielle Ausrüstung und ist teurer als einige andere Oberflächenhärtungsmethoden.
- Nitrocarburieren:Bietet eine Kombination aus Härte, Verschleißfestigkeit und Korrosionsbeständigkeit.Es ist für bestimmte Anwendungen kostengünstiger, erreicht aber möglicherweise nicht den gleichen Härtegrad wie das Plasmanitrieren.
Durch die Kenntnis dieser Hauptunterschiede können Käufer von Anlagen und Verbrauchsmaterialien fundierte Entscheidungen darüber treffen, welches Verfahren ihren spezifischen Anforderungen am besten entspricht, unabhängig davon, ob sie die Härte, die Verschleißfestigkeit oder die Kosteneffizienz in den Vordergrund stellen.
Zusammenfassende Tabelle:
Aspekt | Plasma-Nitrieren | Nitrocarburieren |
---|---|---|
Mechanismus | Verwendet ein Plasma, um Stickstoff in die Metalloberfläche zu diffundieren. | Führt sowohl Stickstoff als auch Kohlenstoff in die Metalloberfläche ein. |
Eingebrachte Elemente | Nur Stickstoff. | Stickstoff und Kohlenstoff. |
Temperaturbereich | 350°C bis 600°C. | 500°C bis 600°C. |
Eigenschaften der Oberfläche | Harte, verschleißfeste Oberfläche mit minimaler Verformung. | Verbundschicht mit Verschleißfestigkeit, reduzierter Reibung und Korrosionsbeständigkeit. |
Anwendungen | Hochpräzise Bauteile wie Zahnräder, Werkzeuge und Formen. | Bauteile, die einem gleitenden Verschleiß unterliegen, wie Kurbel- und Nockenwellen. |
Vorteile | Präzise Steuerung, ausgezeichnete Härte, minimale Verformung. | Kostengünstig, verbesserte Verschleißfestigkeit und Korrosionsbeständigkeit. |
Beschränkungen | Erfordert spezielle Ausrüstung, höhere Kosten. | Erreicht möglicherweise nicht die gleiche Härte wie das Plasmanitrieren. |
Benötigen Sie Hilfe bei der Auswahl des richtigen Oberflächenhärteverfahrens für Ihre Metallteile? Kontaktieren Sie noch heute unsere Experten für eine maßgeschneiderte Beratung!