Physical Vapor Deposition (PVD) und Atomic Layer Deposition (ALD) sind zwei unterschiedliche Verfahren zur Abscheidung von Dünnschichten, die in verschiedenen Industriezweigen eingesetzt werden und jeweils eigene Prozesse, Vorteile und Anwendungen haben.PVD beruht auf physikalischen Prozessen wie Verdampfung oder Sputtern, um Materialien abzuscheiden, oft bei niedrigeren Temperaturen und mit hohen Abscheideraten, wodurch es sich für einfachere Geometrien und Legierungsabscheidungen eignet.Im Gegensatz dazu ist ALD ein chemischer Prozess, der sequenzielle, selbstbegrenzende Reaktionen nutzt, um ultradünne, konforme Schichten mit präziser Dickenkontrolle abzuscheiden, ideal für komplexe Geometrien und hochpräzise Anwendungen.Während PVD ein \"Sichtlinien"-Verfahren ist, bietet ALD eine isotrope Beschichtung, die eine gleichmäßige Bedeckung aller Oberflächen gewährleistet.
Die wichtigsten Punkte werden erklärt:
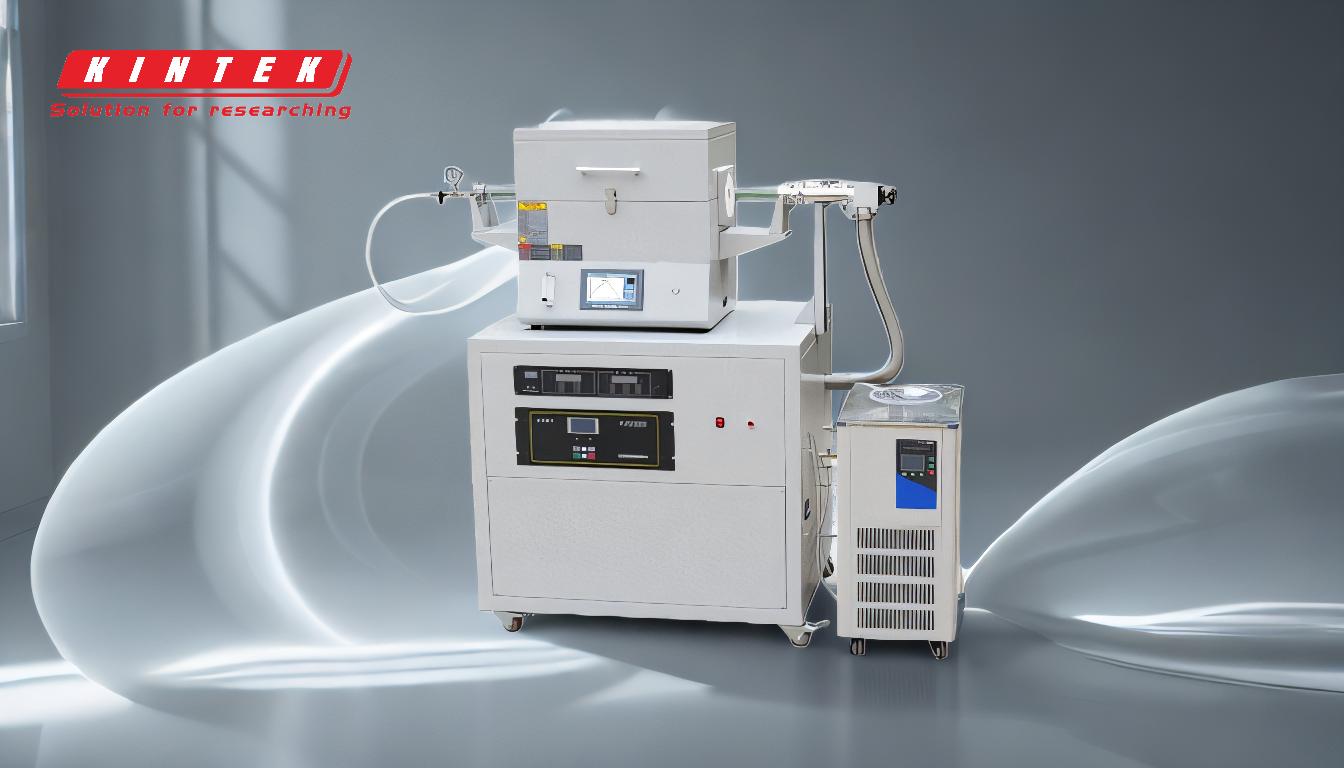
-
Mechanismus des Prozesses:
- PVD:Physikalische Verfahren wie Verdampfen oder Sputtern, bei denen feste Materialien verdampft und dann auf einem Substrat kondensiert werden.Dieser Prozess beruht nicht auf chemischen Reaktionen und wird unter Vakuumbedingungen durchgeführt.
- ALD:Ein chemisches Verfahren, bei dem durch aufeinanderfolgende Pulse von Vorläufern und Reaktanten eine chemisch gebundene Monoschicht auf dem Substrat gebildet wird.Jeder Schritt ist selbstlimitierend und gewährleistet eine präzise Kontrolle der Schichtdicke.
-
Temperatur-Anforderungen:
- PVD:Kann bei relativ niedrigen Temperaturen durchgeführt werden, wodurch es sich für temperaturempfindliche Substrate eignet.Dies ist besonders vorteilhaft für Anwendungen, die eine geringe thermische Belastung erfordern.
- ALD:In der Regel sind höhere Temperaturen erforderlich, um die für das Schichtwachstum notwendigen chemischen Reaktionen zu ermöglichen.In einigen Fällen kann ALD jedoch auch für Niedrigtemperaturverfahren angepasst werden.
-
Abscheideraten:
- PVD:Bietet hohe Abscheideraten, die je nach Verfahren (z. B. EBPVD) von 0,1 bis 100 μm/min reichen.Dadurch eignet es sich für Anwendungen, bei denen eine schnelle Beschichtung erforderlich ist.
- ALD:Deutlich niedrigere Abscheidungsraten aufgrund des Schicht-für-Schicht-Wachstumsmechanismus.Bei jedem Zyklus wird nur eine einzige Atomschicht abgeschieden, was zu einer langsameren Gesamtabscheidung, aber zu einer außergewöhnlichen Präzision führt.
-
Gleichmäßigkeit und Konformität der Beschichtung:
- PVD:Es handelt sich um ein "Sichtlinien"-Verfahren, d. h. es werden nur die Oberflächen beschichtet, die der Lichtquelle direkt ausgesetzt sind.Dies schränkt die Wirksamkeit bei komplexen Geometrien oder Substraten mit komplizierten Merkmalen ein.
- ALD:Ermöglicht eine isotrope Beschichtung, die eine gleichmäßige Bedeckung auf allen Oberflächen gewährleistet, auch auf solchen mit komplexen Geometrien.Dies macht ALD ideal für Anwendungen, die eine hohe Konformität erfordern.
-
Materialausnutzung und Effizienz:
- PVD:Hohe Materialausnutzung, insbesondere bei Verfahren wie EBPVD.Das Verfahren ist effizient im Hinblick auf den Rohstoffverbrauch und kann für die Produktion in großem Maßstab kostengünstig sein.
- ALD:ALD ist zwar hochpräzise, kann aber aufgrund des sequentiellen Charakters des Prozesses und der Notwendigkeit einer präzisen Zufuhr von Ausgangsstoffen weniger effizient sein, was den Materialverbrauch angeht.
-
Anwendungen:
- PVD:Wird häufig für Anwendungen verwendet, die hohe Abscheidungsraten erfordern, wie z. B. dekorative Beschichtungen, harte Beschichtungen für Werkzeuge und Legierungsabscheidungen.Es ist auch für einfachere Substratgeometrien geeignet.
- ALD:Ideal für Anwendungen, die ultradünne, konforme Schichten mit präziser Dickenkontrolle erfordern, wie z. B. die Halbleiterherstellung, MEMS-Bauteile und moderne Optik.
-
Sicherheit und Handhabung:
- PVD:Im Allgemeinen sicherer und einfacher zu handhaben, da keine giftigen Chemikalien verwendet werden und keine hohen Substrattemperaturen erforderlich sind.Bei diesem Verfahren fallen weniger korrosive Nebenprodukte an.
- ALD:ALD ist zwar auch sicher, aber es erfordert den Umgang mit reaktiven Ausgangsstoffen und möglicherweise strengere Sicherheitsprotokolle, um chemische Reaktionen und Nebenprodukte zu beherrschen.
-
Kosten und Skalierbarkeit:
- PVD:Aufgrund höherer Abscheideraten und einfacherer Prozessanforderungen oft kostengünstiger für die Großproduktion.Sie ist für industrielle Anwendungen skalierbar.
- ALD:Teurer und langsamer, daher weniger geeignet für die Großserienproduktion.Seine Präzision und Konformität rechtfertigen jedoch seinen Einsatz bei hochwertigen, spezialisierten Anwendungen.
Durch die Kenntnis dieser Hauptunterschiede können Käufer von Geräten und Verbrauchsmaterialien fundierte Entscheidungen darüber treffen, welche Beschichtungstechnik ihren spezifischen Anforderungen am besten entspricht, unabhängig davon, ob Geschwindigkeit, Präzision oder Kosteneffizienz im Vordergrund stehen.
Zusammenfassende Tabelle:
Blickwinkel | PVD | ALD |
---|---|---|
Prozess-Mechanismus | Physikalische Prozesse wie Verdampfung oder Sputtern | Chemische Prozesse mit sequenziellen, selbstbegrenzenden Reaktionen |
Temperatur | Niedrigere Temperaturen, geeignet für empfindliche Substrate | Höhere Temperaturen, aber anpassbar für Niedertemperaturprozesse |
Abscheiderate | Hoch (0,1 bis 100 μm/min) | Niedrig (schichtweises Wachstum) |
Gleichmäßigkeit der Beschichtung | Sichtlinie, begrenzt für komplexe Geometrien | Isotrop, gleichmäßige Abdeckung auf allen Oberflächen |
Material-Effizienz | Hohe Materialausnutzung | Weniger effizient aufgrund des sequentiellen Prozesses |
Anwendungen | Dekorative Beschichtungen, harte Beschichtungen, Legierungsabscheidungen | Halbleiterherstellung, MEMS-Bauteile, moderne Optik |
Sicherheit | Sicherer, weniger giftige Chemikalien | Erfordert den Umgang mit reaktiven Vorläufersubstanzen |
Kosten und Skalierbarkeit | Kostengünstig für die Großproduktion | Teuer, geeignet für hochwertige, spezialisierte Anwendungen |
Benötigen Sie Hilfe bei der Auswahl der richtigen Dünnschicht-Beschichtungstechnik? Kontaktieren Sie noch heute unsere Experten für eine persönliche Beratung!