Das Spark-Plasma-Sintern (SPS) und das konventionelle Sintern unterscheiden sich erheblich in den Methoden der Wärmeerzeugung, den Verarbeitungszeiten und den resultierenden Materialeigenschaften.SPS nutzt die interne Joule-Erwärmung, die schnelle Aufheiz- und Abkühlraten ermöglicht und im Vergleich zum konventionellen Sintern eine nahezu theoretische Dichte bei niedrigeren Temperaturen und in viel kürzerer Zeit erreicht.Dies macht SPS besonders vorteilhaft für das Sintern fortschrittlicher Materialien, einschließlich nanokristalliner und gradienter Funktionsmaterialien, ohne deren ursprüngliche Eigenschaften zu beeinträchtigen.Das konventionelle Sintern hingegen ist auf externe Heizelemente angewiesen, was zu langsameren Verarbeitungszeiten und potenziell höheren Temperaturen führt, die die Materialeigenschaften beeinträchtigen können.
Die wichtigsten Punkte werden erklärt:
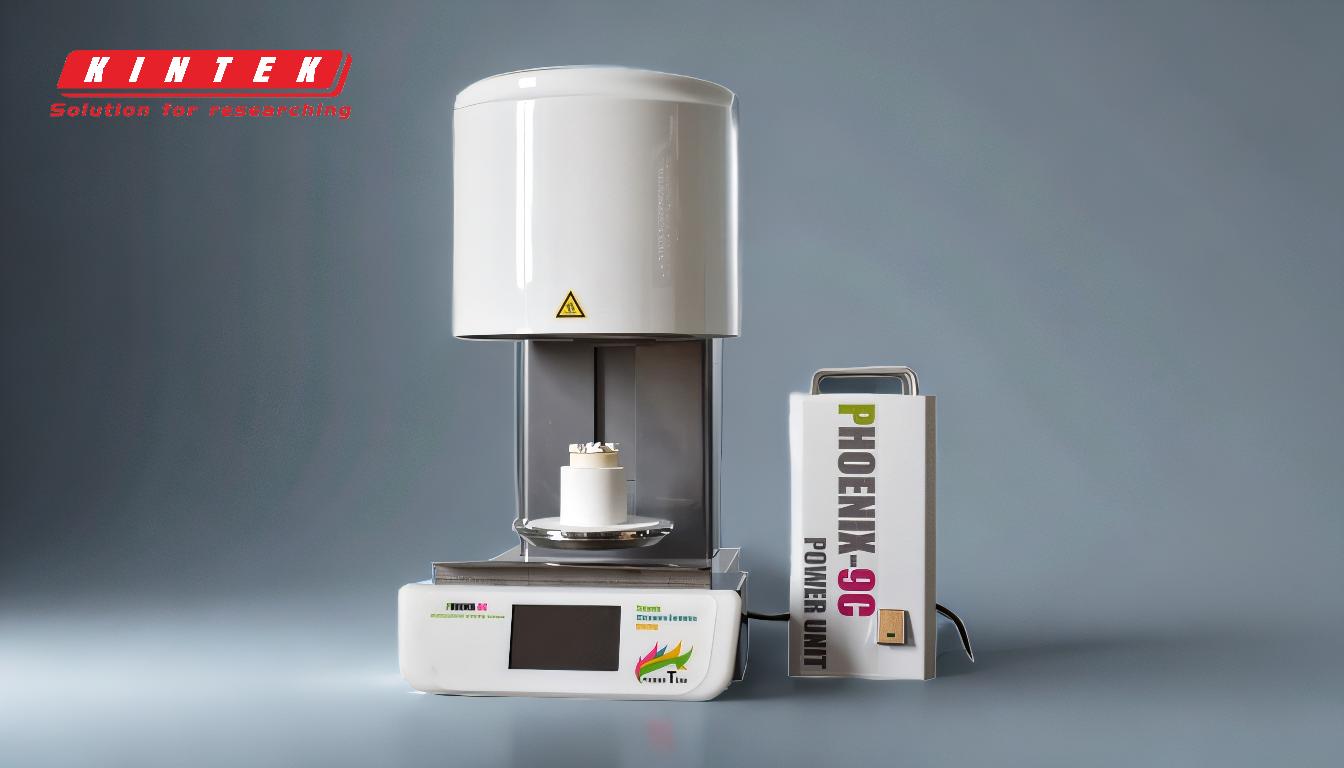
-
Methode der Wärmeerzeugung:
- Spark Plasma Sintering (SPS):Die Wärme wird intern durch Joule-Erwärmung erzeugt, bei der ein elektrischer Strom direkt durch die Graphitform und das Pulverbrikett fließt.Dieser interne Erhitzungsmechanismus ermöglicht eine präzise Temperaturkontrolle und schnelle Erhitzungsraten.
- Konventionelles Sintern:Die Wärme wird durch externe Heizelemente, wie z. B. Öfen, bereitgestellt.Diese Methode beruht auf der Wärmeleitung von außen, was zu einer langsameren und weniger gleichmäßigen Erwärmung führt.
-
Verarbeitungszeit:
- SPS:Der Sinterprozess ist aufgrund der hohen Aufheiz- und Abkühlraten (bis zu 1000 K/min) extrem schnell und oft innerhalb von Minuten abgeschlossen.Durch diese schnelle Verarbeitung können Keramiken und andere Werkstoffe 10- bis 100-mal schneller verdichtet werden als mit herkömmlichen Verfahren.
- Konventionelles Sintern:Der Prozess dauert in der Regel mehrere Stunden, da er von einer langsameren Wärmeübertragung durch externe Quellen abhängt.Diese längere Dauer kann zu Kornwachstum und anderen unerwünschten Veränderungen der Materialeigenschaften führen.
-
Anforderungen an die Temperatur:
- SPS:Erzielt eine nahezu theoretische Dichte bei niedrigeren Sintertemperaturen.Die interne Joule-Erwärmung ermöglicht eine effiziente Energieübertragung direkt auf das Material, so dass keine hohen Außentemperaturen erforderlich sind.
- Konventionelles Sintern:Erfordert oft höhere Temperaturen, um ähnliche Dichten zu erreichen, was zu einer thermischen Zersetzung des Materials führen kann.
-
Materialeigenschaften:
- SPS:Das Schnellsinterverfahren bewahrt die ursprünglichen Eigenschaften des Materials und ist daher ideal für das Sintern von amorphen, nanokristallinen und Gradienten-Funktionsmaterialien.Dies ist besonders wichtig für hochentwickelte Werkstoffe, bei denen die Beibehaltung der Nanostruktur oder spezifischer Materialgradienten entscheidend ist.
- Konventionelles Sintern:Der langsamere Prozess und die höheren Temperaturen können zu Kornwachstum und anderen Veränderungen im Materialgefüge führen, wodurch sich die Eigenschaften des Materials verschlechtern können.
-
Anwendungen:
- SPS:Besonders geeignet für das Sintern fortschrittlicher Werkstoffe, einschließlich solcher mit komplexer Zusammensetzung oder die eine genaue Kontrolle des Gefüges erfordern.Es eignet sich auch zum Sintern von Verbindungen zwischen verschiedenen Metallen oder zwischen Metallen und Nichtmetallen.
- Konventionelle Sinterung:Wird häufiger für herkömmliche Werkstoffe verwendet, bei denen eine schnelle Sinterung keine kritische Anforderung ist und der Werkstoff höhere Temperaturen ohne Beeinträchtigung vertragen kann.
Zusammenfassend lässt sich sagen, dass das Spark-Plasma-Sintern gegenüber dem konventionellen Sintern erhebliche Vorteile in Bezug auf Geschwindigkeit, Temperatureffizienz und die Fähigkeit, die Materialintegrität zu erhalten, bietet.Diese Vorteile machen SPS zu einer bevorzugten Methode für das Sintern fortschrittlicher und komplexer Werkstoffe, bei denen herkömmliche Sinterverfahren versagen können.
Zusammenfassende Tabelle:
Aspekt | Spark-Plasma-Sintern (SPS) | Konventionelles Sintern |
---|---|---|
Wärmeerzeugung | Interne Joule-Erwärmung über elektrischen Strom durch die Graphitform und das Pulverbrikett. | Externe Heizelemente wie Öfen, die auf der Wärmeleitung von außen beruhen. |
Verarbeitungszeit | Extrem schnell (Minuten), mit hohen Aufheiz-/Abkühlraten (bis zu 1000 K/min). | Langsamer (mehrere Stunden), aufgrund der langsameren Wärmeübertragung von externen Quellen. |
Temperatur | Erreicht bei niedrigeren Temperaturen eine nahezu theoretische Dichte. | Erfordert höhere Temperaturen, was zu thermischer Zersetzung führen kann. |
Materialeigenschaften | Bewahrt die ursprünglichen Eigenschaften, ideal für nanokristalline und Gradienten-Funktionsmaterialien. | Kann zu Kornwachstum und Mikrostrukturveränderungen führen, was die Eigenschaften beeinträchtigen kann. |
Anwendungen | Hochentwickelte Werkstoffe, komplexe Zusammensetzungen und präzise Mikrostrukturkontrolle. | Traditionelle Werkstoffe, bei denen eine schnelle Sinterung nicht entscheidend ist und höhere Temperaturen toleriert werden. |
Erfahren Sie mehr darüber, wie Spark Plasma Sintering Ihre Materialverarbeitung revolutionieren kann. Kontaktieren Sie unsere Experten noch heute !