Sputtern und thermische Abscheidung sind zwei unterschiedliche Verfahren zur Abscheidung von Dünnschichten, die in verschiedenen Industriezweigen eingesetzt werden und jeweils eigene Mechanismen, Vorteile und Anwendungen haben. Beim Sputtern werden energiereiche Ionen eingesetzt, um Atome aus einem Zielmaterial herauszulösen, die sich dann auf einem Substrat ablagern. Dieses Verfahren arbeitet mit niedrigeren Temperaturen und ist daher für hitzeempfindliche Materialien geeignet. Bei der thermischen Abscheidung hingegen wird das Zielmaterial erhitzt, um einen Dampfstrom zu erzeugen, der auf dem Substrat kondensiert. Diese Methode ist für höhere Abscheideraten und kürzere Laufzeiten bekannt, was sie ideal für Anwendungen macht, die eine schnelle Beschichtung erfordern. Die Wahl zwischen diesen Verfahren hängt von Faktoren wie der Materialkompatibilität, den gewünschten Schichteigenschaften und den Produktionsanforderungen ab.
Die wichtigsten Punkte werden erklärt:
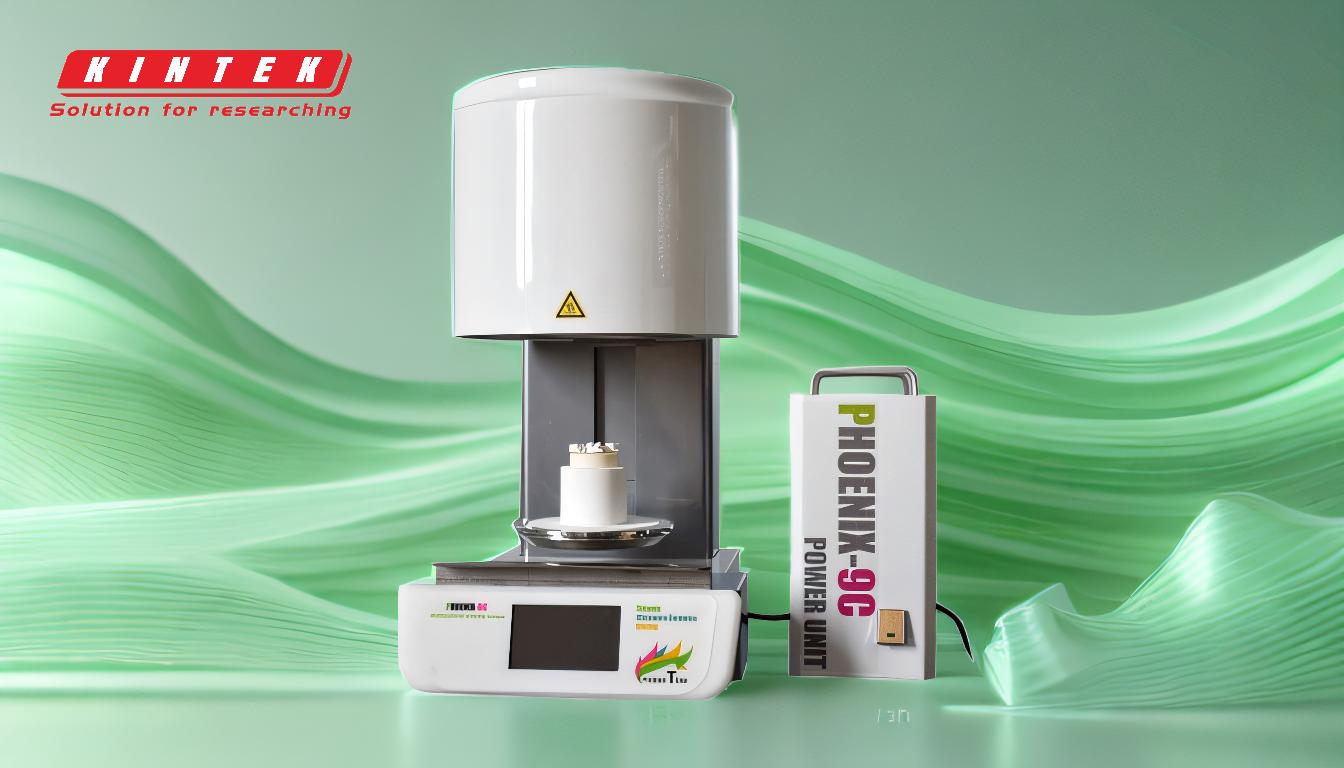
-
Mechanismus der Ablagerung:
-
Sputtern:
- Verwendet ein Plasma, das durch elektrische Erregung einer Kathode in einer Vakuumkammer erzeugt wird, die mit einem kontrollierten Gas (in der Regel Argon) gefüllt ist.
- Positiv geladene Gasionen werden in Richtung des Zielmaterials beschleunigt, wodurch Atome oder Moleküle physikalisch herausgelöst werden.
- Die ausgestoßenen Atome bilden einen Dampfstrom, der sich als dünner Film auf dem Substrat ablagert.
-
Thermische Abscheidung:
- Das Zielmaterial wird bis zu seinem Verdampfungspunkt erhitzt, wodurch ein robuster Dampfstrom entsteht.
- Der Dampf kondensiert auf dem Substrat und bildet einen dünnen Film.
- Bei Materialien, die höheren Temperaturen standhalten können, ist dieses Verfahren oft schneller und effizienter.
-
Sputtern:
-
Temperatur-Empfindlichkeit:
-
Sputtern:
- Arbeitet bei niedrigeren Temperaturen und eignet sich daher für die Beschichtung hitzeempfindlicher Materialien wie Kunststoffe, organische Stoffe und bestimmte Metalle.
- Ideal für Anwendungen, bei denen thermische Spannungen das Substrat beschädigen oder die Materialeigenschaften verändern könnten.
-
Thermische Abscheidung:
- Erfordert höhere Temperaturen, um das Zielmaterial zu verdampfen.
- Am besten geeignet für Substrate und Materialien, die thermische Belastungen vertragen, wie z. B. Metalle und Keramiken.
-
Sputtern:
-
Ablagerungsrate und Effizienz:
-
Sputtern:
- Es werden einzelne Atome oder kleine Cluster ausgestoßen, was zu einer langsameren Abscheidungsrate im Vergleich zu thermischen Verfahren führt.
- Bietet eine präzise Kontrolle der Schichtdicke und der Gleichmäßigkeit und ist damit ideal für Anwendungen, die hochwertige Beschichtungen erfordern.
-
Thermische Abscheidung:
- Erzeugt einen robusten Dampfstrom, der höhere Abscheideraten und kürzere Laufzeiten ermöglicht.
- Effizienter für Großproduktionen oder Anwendungen, bei denen es auf Geschwindigkeit ankommt.
-
Sputtern:
-
Anwendungen:
-
Sputtern:
- Wird häufig in der elektrischen und optischen Produktion verwendet, z. B. bei der Herstellung von Dünnschichttransistoren, OLEDs und reflektierenden Beschichtungen.
- Geeignet für Anwendungen, die eine genaue Kontrolle der Folieneigenschaften und Kompatibilität mit wärmeempfindlichen Substraten erfordern.
-
Thermische Abscheidung:
- Sie werden häufig in Branchen wie der Solarzellenherstellung, der Glasbeschichtung und der Metallbeschichtung eingesetzt.
- Ideal für Anwendungen, bei denen es auf schnelle Beschichtung und hohen Durchsatz ankommt.
-
Sputtern:
-
Materialkompatibilität:
-
Sputtern:
- Kann eine Vielzahl von Materialien abscheiden, darunter Metalle, Legierungen und Keramiken, ohne dass hohe Temperaturen erforderlich sind.
- Besonders wirksam bei Materialien, die sich nur schwer thermisch verdampfen lassen.
-
Thermische Abscheidung:
- Beschränkt auf Materialien, die ohne Zersetzung oder Abbau verdampft werden können.
- Funktioniert gut mit Metallen und einfachen Verbindungen, die einen genau definierten Verdampfungspunkt haben.
-
Sputtern:
-
Komplexität von Ausrüstung und Verfahren:
-
Sputtern:
- Für die Erzeugung und Kontrolle des Plasmas sind spezielle Geräte erforderlich, was den Prozess komplexer und potenziell teurer macht.
- Bietet größere Flexibilität in Bezug auf Zielmaterialien und Substratkompatibilität.
-
Thermische Abscheidung:
- Einfacherer Aufbau der Ausrüstung, vor allem mit Heizelementen und Vakuumkammern.
- Einfacher zu skalieren für die Großserienproduktion, aber weniger vielseitig in Bezug auf die Materialoptionen.
-
Sputtern:
Zusammenfassend lässt sich sagen, dass Sputtern und thermische Abscheidung komplementäre Techniken sind, die sich jeweils in bestimmten Situationen auszeichnen. Das Sputtern wird für Präzisionsanwendungen, Niedrigtemperaturanwendungen und wärmeempfindliche Materialien bevorzugt, während die thermische Abscheidung wegen ihrer Schnelligkeit, Effizienz und Eignung für Substrate mit hoher Temperaturtoleranz bevorzugt wird. Die Wahl zwischen den beiden Verfahren hängt von den spezifischen Anforderungen des Projekts ab, einschließlich der Materialeigenschaften, der gewünschten Filmeigenschaften und der Produktionseinschränkungen.
Zusammenfassende Tabelle:
Aspekt | Sputtern | Thermische Abscheidung |
---|---|---|
Mechanismus | Verwendet energiereiche Ionen, um Atome aus einem Zielmaterial herauszulösen. | Erhitzt das Zielmaterial, um einen Dampfstrom für die Abscheidung zu erzeugen. |
Temperatur-Empfindlichkeit | Arbeitet bei niedrigeren Temperaturen, ideal für hitzeempfindliche Materialien. | Benötigt höhere Temperaturen, geeignet für hitzebeständige Substrate. |
Ablagerungsrate | Langsamer, aber mit präziser Kontrolle über Schichtdicke und Gleichmäßigkeit. | Schnellere Abscheidungsraten, ideal für Anwendungen mit hohem Durchsatz. |
Anwendungen | Elektrische/optische Produktion (z. B. OLEDs, Dünnschichttransistoren). | Solarzellen, Glasbeschichtung, Metallbeschichtung. |
Kompatibilität der Materialien | Arbeitet mit Metallen, Legierungen, Keramiken und wärmeempfindlichen Materialien. | Begrenzt auf Materialien, die ohne Beeinträchtigung verdampft werden können. |
Komplexität der Ausrüstung | Erfordert spezielle plasmaerzeugende Geräte und eine komplexere Einrichtung. | Einfacherer Aufbau mit Heizelementen und Vakuumkammern. |
Benötigen Sie Hilfe bei der Auswahl des richtigen Verfahrens zur Dünnschichtabscheidung? Kontaktieren Sie unsere Experten noch heute für maßgeschneiderte Lösungen!