Dickschicht- und Dünnschicht-PCBs (Printed Circuit Boards) sind zwei unterschiedliche Technologien, die bei der Herstellung elektronischer Schaltkreise verwendet werden, jede mit ihren eigenen Eigenschaften, Vorteilen und Anwendungen. Bei Dickschicht-Leiterplatten werden in der Regel Siebdruckverfahren verwendet, um leitfähige, widerstandsbehaftete und isolierende Pasten auf ein Substrat aufzutragen, die dann bei hohen Temperaturen gebrannt werden, um den Schaltkreis zu bilden. Diese Methode ist kostengünstig und eignet sich für die Herstellung großer Schaltkreismengen mit mäßiger Präzision. Bei Dünnschicht-Leiterplatten hingegen werden sehr dünne Schichten aus leitenden und isolierenden Materialien durch Prozesse wie Sputtern oder Verdampfen abgeschieden. Diese Technik ermöglicht eine viel höhere Präzision und feinere Merkmale und eignet sich daher ideal für Anwendungen mit hoher Frequenz und hoher Dichte. Die Wahl zwischen Dickschicht- und Dünnschicht-Leiterplatten hängt von Faktoren wie der erforderlichen Präzision, der Komplexität der Schaltung, dem Produktionsvolumen und Kostenüberlegungen ab.
Wichtige Punkte erklärt:
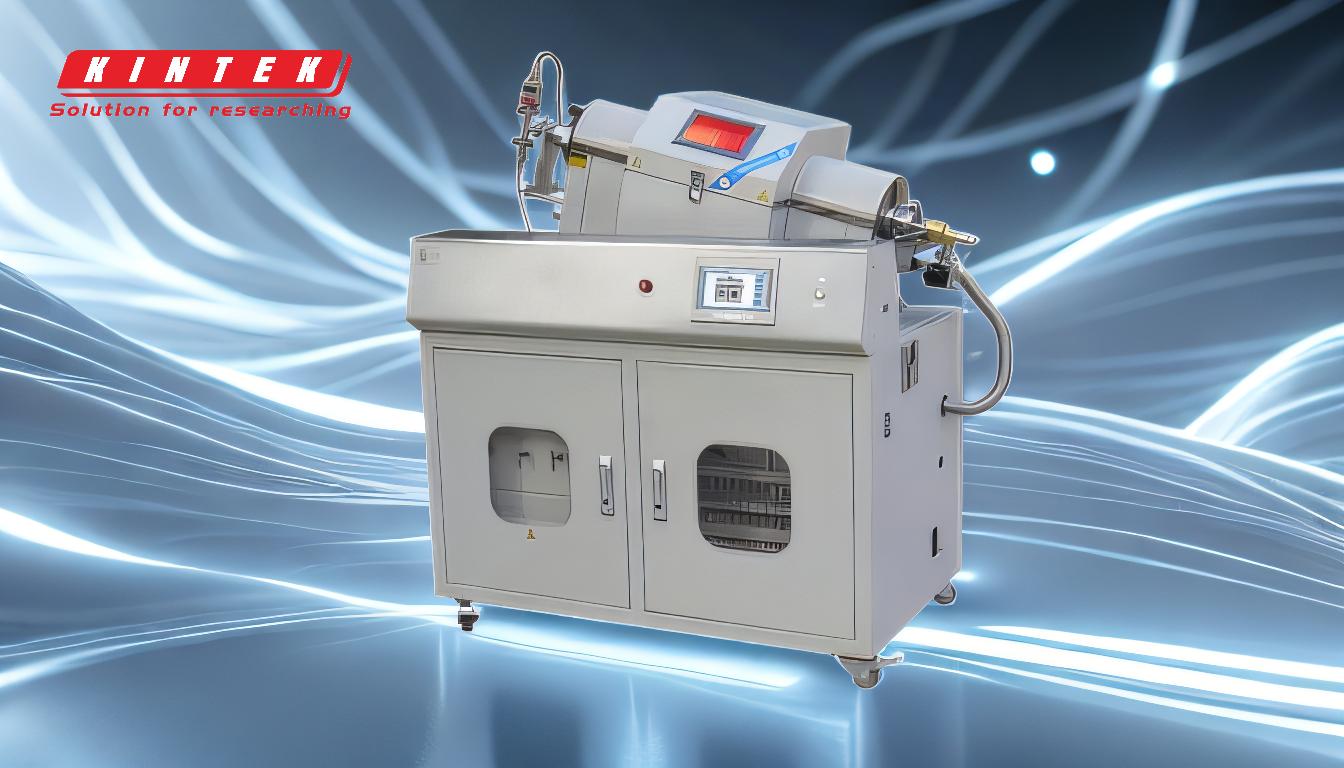
-
Herstellungsprozess:
- Dickschicht-Leiterplatten: Diese werden mithilfe von Siebdrucktechniken hergestellt, bei denen leitfähige, ohmsche und isolierende Pasten auf ein Keramik- oder Glassubstrat aufgetragen werden. Anschließend werden die Pasten bei hohen Temperaturen (typischerweise etwa 850 °C) gebrannt, um den Schaltkreis zu bilden. Dieses Verfahren ist relativ einfach und kostengünstig und eignet sich daher für die Produktion in großem Maßstab.
- Dünnschicht-Leiterplatten: Diese werden mithilfe fortschrittlicher Abscheidungstechniken wie Sputtern oder Verdampfen hergestellt. Diese Methoden ermöglichen die Abscheidung sehr dünner Schichten (oft im Nanometerbereich) aus leitenden und isolierenden Materialien auf einem Substrat. Dieses Verfahren erfordert eine anspruchsvollere Ausrüstung und ist teurer, bietet jedoch eine höhere Präzision und die Möglichkeit, sehr feine Merkmale zu erzeugen.
-
Präzision und Merkmalsgröße:
- Dickschicht-Leiterplatten: Das in der Dickschichttechnologie verwendete Siebdruckverfahren begrenzt die minimal erreichbare Strukturgröße und Linienbreite. Typischerweise beträgt die minimale Linienbreite etwa 100–150 Mikrometer, was für viele Anwendungen ausreichend ist, jedoch nicht für Schaltkreise mit hoher Dichte.
- Dünnschicht-Leiterplatten: Mit der Dünnschichttechnologie können viel feinere Merkmale mit Linienbreiten von nur 10 Mikrometern oder weniger erzielt werden. Dadurch eignen sich Dünnschicht-Leiterplatten für Anwendungen, die hochpräzise und hochdichte Verbindungen erfordern, beispielsweise in HF- (Radiofrequenz-) und Mikrowellenschaltungen.
-
Materialeigenschaften:
- Dickschicht-Leiterplatten: Die in der Dickschichttechnologie verwendeten Materialien sind typischerweise eine Kombination aus Metalloxiden und Glasfritten. Diese Materialien werden aufgrund ihrer Fähigkeit ausgewählt, hohen Brenntemperaturen standzuhalten und eine gute Haftung auf dem Untergrund zu bieten. Allerdings sind die elektrischen Eigenschaften von Dickschichtmaterialien im Allgemeinen nicht so gut wie die von Dünnschichtmaterialien.
- Dünnschicht-Leiterplatten: Die Dünnschichttechnologie ermöglicht die Verwendung hochreiner Metalle und Dielektrika, die hervorragende elektrische Eigenschaften bieten. Beispielsweise können Dünnschichtwiderstände im Vergleich zu Dickschichtwiderständen einen viel niedrigeren Temperaturkoeffizienten des Widerstands (TCR) und eine bessere Stabilität über die Zeit aufweisen.
-
Anwendungen:
- Dickschicht-Leiterplatten: Aufgrund ihrer geringeren Kosten und des einfacheren Herstellungsprozesses werden Dickschicht-Leiterplatten häufig in der Unterhaltungselektronik, in Automobilanwendungen und in industriellen Steuerungen verwendet. Sie werden auch in Hybridschaltungen verwendet, bei denen eine Kombination aus Dickschicht- und diskreten Komponenten erforderlich ist.
- Dünnschicht-Leiterplatten: Die Dünnschichttechnologie wird in Anwendungen eingesetzt, bei denen es auf hohe Präzision und Leistung ankommt. Dazu gehören HF- und Mikrowellenschaltungen, Sensoren und digitale Hochfrequenzschaltungen. Dünnschicht-Leiterplatten werden auch in medizinischen Geräten und Luft- und Raumfahrtanwendungen eingesetzt, wo Zuverlässigkeit und Leistung von größter Bedeutung sind.
-
Kostenüberlegungen:
- Dickschicht-Leiterplatten: Die Kosten für die Herstellung von Dickschicht-Leiterplatten sind aufgrund des einfacheren Herstellungsprozesses und der Verwendung kostengünstigerer Materialien im Allgemeinen niedriger. Dies macht die Dickschichttechnologie attraktiver für die Massenproduktion, bei der die Kosten ein wesentlicher Faktor sind.
- Dünnschicht-Leiterplatten: Die höhere Präzision und die fortschrittlichen Materialien, die in der Dünnschichttechnologie verwendet werden, führen zu höheren Produktionskosten. Allerdings können die überlegene Leistung und Zuverlässigkeit von Dünnschicht-Leiterplatten die höheren Kosten in Anwendungen rechtfertigen, in denen diese Eigenschaften unerlässlich sind.
-
Thermische und mechanische Eigenschaften:
- Dickschicht-Leiterplatten: Dickschichtmaterialien sind im Allgemeinen robuster und können höheren mechanischen Belastungen und Temperaturwechseln standhalten. Dadurch eignen sie sich für Anwendungen, bei denen die Leiterplatte rauen Umgebungsbedingungen ausgesetzt sein kann.
- Dünnschicht-Leiterplatten: Dünnschichtmaterialien bieten zwar hervorragende elektrische Eigenschaften, sind jedoch möglicherweise anfälliger für mechanische Beanspruchung und Temperaturwechsel. Allerdings können diese Probleme durch den Einsatz fortschrittlicher Substrate und Verkapselungstechniken gemildert werden.
Zusammenfassend lässt sich sagen, dass die Wahl zwischen Dickschicht- und Dünnschicht-Leiterplatten von den spezifischen Anforderungen der Anwendung abhängt, einschließlich der Notwendigkeit von Präzision, Leistung, Kosten und Umweltbeständigkeit. Die Dickschichttechnologie eignet sich gut für eine kostengünstige Produktion in großen Stückzahlen, während die Dünnschichttechnologie ideal für leistungsstarke und hochpräzise Anwendungen ist.
Übersichtstabelle:
Aspekt | Dickschicht-Leiterplatten | Dünnschicht-Leiterplatten |
---|---|---|
Herstellungsprozess | Siebdruck mit leitfähigen, Widerstands- und Isolierpasten, gebrannt bei ~850°C. | Fortschrittliche Abscheidungstechniken (Sputtern/Verdampfen) für nanometerdünne Schichten. |
Präzision | Mindestlinienbreite: 100–150 Mikrometer. | Mindestlinienbreite: 10 Mikrometer oder weniger. |
Materialien | Metalloxide und Glasfritten mit mäßigen elektrischen Eigenschaften. | Hochreine Metalle und Dielektrika mit hervorragenden elektrischen Eigenschaften. |
Anwendungen | Unterhaltungselektronik, Automobil, Industriesteuerungen, Hybridschaltungen. | HF-/Mikrowellenschaltungen, Sensoren, medizinische Geräte, Luft- und Raumfahrt. |
Kosten | Niedrigere Kosten, geeignet für die Massenproduktion. | Höhere Kosten, gerechtfertigt für Hochleistungsanwendungen. |
Haltbarkeit | Robust, widersteht mechanischer Beanspruchung und Temperaturwechsel. | Anfällig für Stress, aber durch fortschrittliche Substrate und Kapselung gemildert. |
Benötigen Sie Hilfe bei der Auswahl der richtigen PCB-Technologie für Ihr Projekt? Kontaktieren Sie uns noch heute für fachkundige Beratung!