Das Doppelsinterverfahren ist eine spezielle Sintertechnik, die hauptsächlich bei der Herstellung von Hochleistungskeramik und bestimmten Metalllegierungen eingesetzt wird.Es umfasst zwei verschiedene Sinterstufen, um optimale Materialeigenschaften wie hohe Dichte, verbesserte mechanische Festigkeit und geringere Porosität zu erreichen.In der ersten Stufe wird das Material bei einer niedrigeren Temperatur gesintert, um eine teilweise Verdichtung zu erreichen und die Struktur zu stabilisieren.In der zweiten Stufe wird das Material bei einer höheren Temperatur gesintert, um es vollständig zu verdichten und seine mechanischen und thermischen Eigenschaften zu verbessern.Dieses Verfahren eignet sich besonders für Werkstoffe, die aufgrund ihrer komplexen Zusammensetzung oder ihrer Empfindlichkeit gegenüber Temperaturgradienten nur schwer in einem einzigen Schritt gesintert werden können.
Die wichtigsten Punkte erklärt:
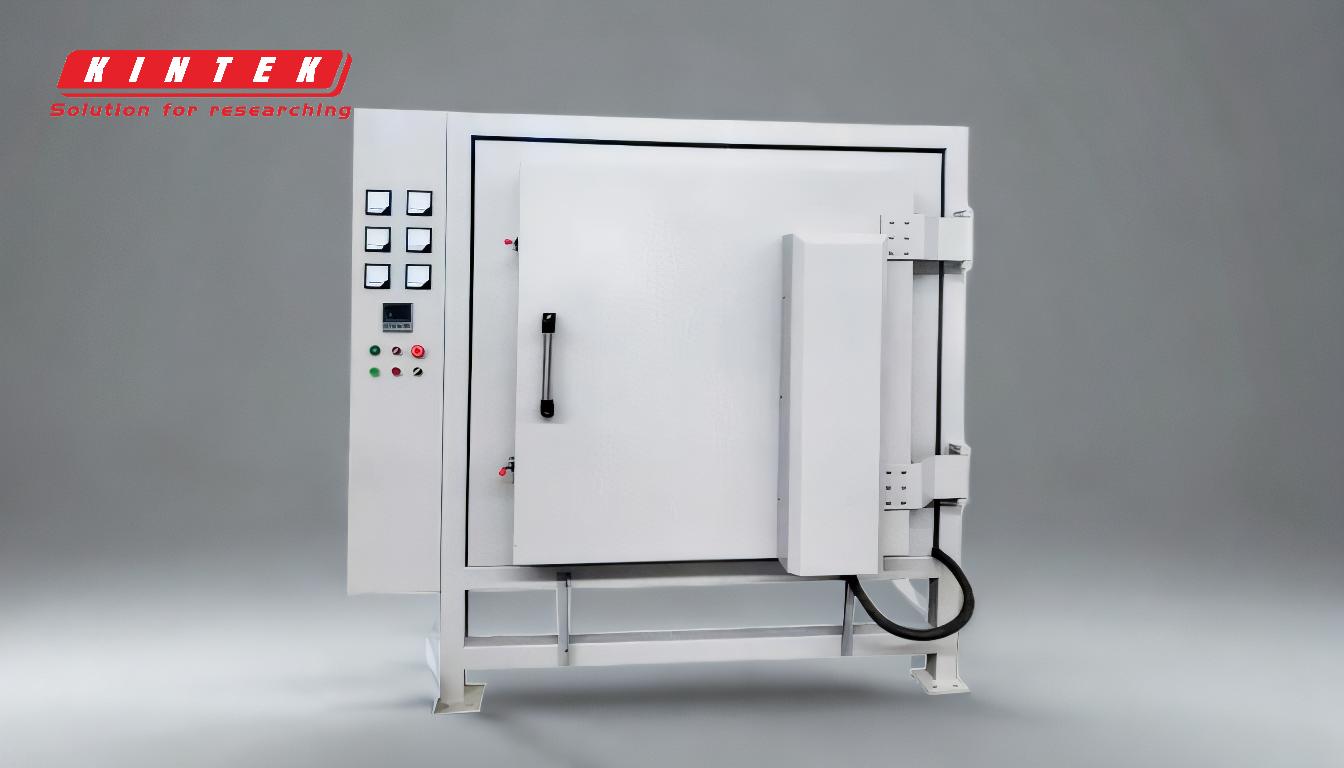
-
Definition des Doppelsinterns:
- Das Doppelsintern ist ein zweistufiges Sinterverfahren zur Optimierung der Verdichtung und der mechanischen Eigenschaften von Werkstoffen, insbesondere von Keramiken und Metalllegierungen.
- In der ersten Stufe wird bei einer niedrigeren Temperatur gesintert, um eine teilweise Verdichtung und strukturelle Stabilität zu erreichen.
- In der zweiten Stufe wird das Material bei einer höheren Temperatur gesintert, um es vollständig zu verdichten und seine Eigenschaften zu verbessern.
-
Zweck und Nutzen:
- Verbesserte Verdichtung:Das zweistufige Verfahren ermöglicht eine bessere Kontrolle des Verdichtungsprozesses und verringert das Risiko von Fehlern wie Rissen oder Hohlräumen.
- Verbesserte mechanische Eigenschaften:Durch die vollständige Verdichtung des Materials in der zweiten Stufe weist das Endprodukt eine höhere Festigkeit, Zähigkeit und Verschleißfestigkeit auf.
- Reduzierte Porosität:Durch das Doppelsinterverfahren wird die Porosität wirksam minimiert, was für Anwendungen, die eine hohe Dichte und eine geringe Permeabilität erfordern, entscheidend ist.
-
Anwendungen:
- Hochleistungskeramik:Zur Herstellung von Hochleistungskeramik für Anwendungen in der Elektronik, Luft- und Raumfahrt und in medizinischen Geräten.
- Metall-Legierungen:Wird bei der Herstellung komplexer Metallteile verwendet, die eine hohe Festigkeit und Haltbarkeit erfordern.
- Spezialisierte Materialien:Geeignet für Materialien, die aufgrund ihrer komplexen Zusammensetzung oder ihrer Empfindlichkeit gegenüber thermischen Gradienten schwer in einem einzigen Schritt zu sintern sind.
-
Vergleich mit Einzelsintern:
- Einzelne Sinterung:Ein einziger Erhitzungszyklus reicht möglicherweise nicht aus, um bei komplexen Materialien eine vollständige Verdichtung zu erreichen.
- Doppel-Sintern:Ermöglicht ein kontrollierteres und schrittweises Vorgehen, das ein besseres Management von thermischen Spannungen und Materialeigenschaften erlaubt.
-
Prozess-Details:
- Erste Stufe:Das Material wird auf eine Temperatur knapp unter seinem Schmelzpunkt erhitzt, um eine teilweise Verdichtung zu erreichen.In dieser Phase wird die Materialstruktur stabilisiert und die anfängliche Porosität verringert.
- Zweite Stufe:Das Material wird dann auf eine höhere Temperatur erhitzt, um eine vollständige Verdichtung zu erreichen.In dieser Phase werden die mechanischen und thermischen Eigenschaften des Materials verbessert.
-
Technologische Überlegungen:
- Temperaturkontrolle:Die genaue Kontrolle der Temperatur in beiden Phasen ist entscheidend, um einen Temperaturschock zu vermeiden und eine gleichmäßige Verdichtung zu gewährleisten.
- Atmosphärenkontrolle:Der Sinterprozess kann eine kontrollierte Atmosphäre erfordern (z. B. Vakuum oder Inertgas), um Oxidation oder Verunreinigung zu vermeiden.
- Abkühlungsrate:Die Abkühlungsgeschwindigkeit nach dem Sintern kann die endgültigen Materialeigenschaften beeinflussen, und eine kontrollierte Abkühlung ist oft notwendig, um die gewünschte Mikrostruktur zu erreichen.
Zusammenfassend lässt sich sagen, dass das Doppelsinterverfahren eine hochentwickelte Technik ist, die erhebliche Vorteile bei der Herstellung von Hochleistungswerkstoffen bietet.Durch die Aufteilung des Sinterprozesses in zwei Stufen lassen sich die Materialeigenschaften besser kontrollieren, was zu Produkten mit höherer Dichte, Festigkeit und Haltbarkeit führt.Diese Methode ist besonders wertvoll für Hochleistungskeramiken und komplexe Metalllegierungen, bei denen es schwierig ist, in einem einzigen Sinterschritt optimale Eigenschaften zu erzielen.
Zusammenfassende Tabelle:
Aspekt | Einzelheiten |
---|---|
Definition | Zweistufiges Sinterverfahren für Keramiken und Metalllegierungen. |
Erste Stufe | Niedrigere Temperatur für eine teilweise Verdichtung und strukturelle Stabilität. |
Zweite Stufe | Höhere Temperatur für vollständige Verdichtung und verbesserte Eigenschaften. |
Wesentliche Vorteile | Verbesserte Dichte, Festigkeit und geringere Porosität. |
Anwendungen | Hochleistungskeramik, Metalllegierungen und Spezialwerkstoffe. |
Vergleich | Bei komplexen Werkstoffen dem Einzelsintern überlegen. |
Technologische Faktoren | Präzise Temperatur-, Atmosphären- und Kühlratensteuerung. |
Sind Sie an einer Optimierung Ihrer Materialproduktion interessiert? Kontaktieren Sie noch heute unsere Experten um mehr über das Doppelsinterverfahren zu erfahren!