Die Sintertemperatur spielt eine entscheidende Rolle bei der Bestimmung der Dichte eines Sinterkörpers.Höhere Sintertemperaturen führen in der Regel zu einer höheren Dichte, da sich die Materialpartikel besser verbinden und die Poren schrumpfen oder sich schließen.Zu hohe Temperaturen können jedoch zu Kornwachstum führen, das Materialeigenschaften wie Festigkeit und Härte beeinträchtigen kann.Umgekehrt führen zu niedrige Sintertemperaturen zu einer unvollständigen Verdichtung, wodurch das Material porös und schwach wird.Die optimale Sintertemperatur stellt ein Gleichgewicht zwischen Verdichtung und Materialintegrität her und gewährleistet, dass die gewünschten mechanischen Eigenschaften erreicht werden.
Die wichtigsten Punkte werden erklärt:
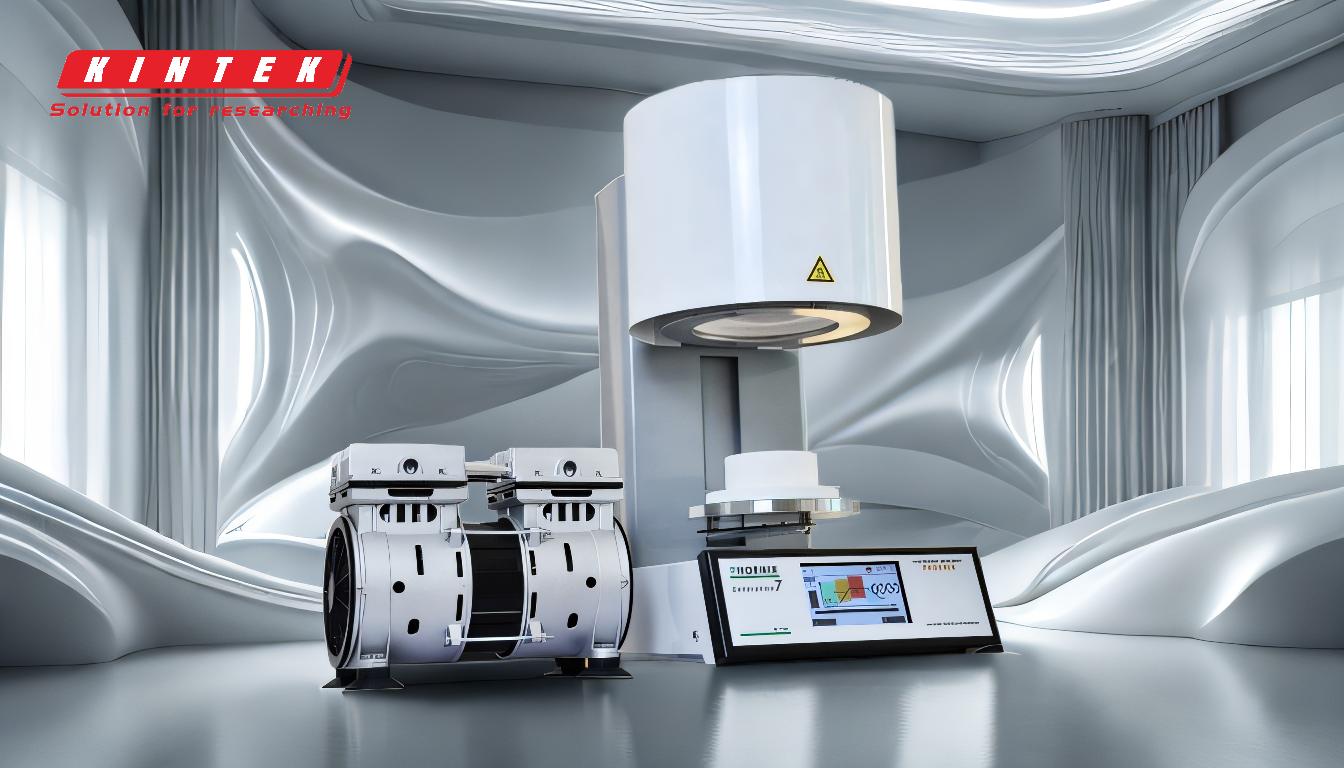
-
Beziehung zwischen Sintertemperatur und Dichte:
- Die Sintertemperatur hat einen direkten Einfluss auf die Dichte des Sinterkörpers.
- Höhere Temperaturen fördern die Partikelbindung und den Porenschluss, was zu einer höheren Dichte führt.
- Zu niedrige Temperaturen führen zu einer unvollständigen Verdichtung, so dass das Material porös bleibt.
-
Auswirkung einer zu hohen Sintertemperatur:
- Extrem hohe Temperaturen können Kornwachstum verursachen, das sich negativ auf die Materialeigenschaften auswirkt.
- Das Kornwachstum verringert die Festigkeit und Härte, da größere Körner schwächere Korngrenzen erzeugen.
- Überhöhte Temperaturen können auch zu Defekten wie Rissen oder Verformungen führen.
-
Optimale Sintertemperatur:
- Es gibt einen idealen Sintertemperaturbereich, der die Dichte maximiert und gleichzeitig die Materialintegrität erhält.
- Zirkoniumdioxid beispielsweise erreicht seine maximale Festigkeit bei etwa 1500℃.Abweichungen von dieser Temperatur, selbst um 150℃, können die Festigkeit aufgrund von Kornwachstum erheblich verringern.
-
Die Rolle der Sinterzeit:
- Die Sinterzeit wirkt sich zusammen mit der Temperatur auf die Dichte aus.
- Längere Sinterzeiten bei optimalen Temperaturen können die Verdichtung weiter verbessern.
- Zu lange Sinterzeiten bei hohen Temperaturen können jedoch zu einer Übersinterung führen, die Kornwachstum und eine Verschlechterung der Eigenschaften zur Folge hat.
-
Einfluss der Sinteratmosphäre:
- Die Sinteratmosphäre (z. B. reduzierend oder inert) beeinflusst die endgültige Dichte und die Eigenschaften.
- Eine reduzierende Atmosphäre verhindert die Oxidation und fördert die Verdichtung durch den Abbau von Oberflächenoxiden.
- Durch die Wahl der Atmosphäre kann der Sinterprozess für bestimmte Werkstoffe optimiert werden.
-
Mikrostrukturelle Veränderungen während des Sinterns:
- Das Sintern verändert das Mikrogefüge, einschließlich der Korngröße, der Porengröße und der Korngrenzenverteilung.
- Diese Veränderungen haben einen direkten Einfluss auf die mechanischen Eigenschaften des Materials, wie Festigkeit und Haltbarkeit.
- Die richtige Steuerung der Sintertemperatur gewährleistet ein feinkörniges, dichtes Gefüge mit minimalen Defekten.
-
Ausgewogene Dichte und Materialeigenschaften:
- Das Ziel des Sinterns ist es, ein vollständig dichtes Teil mit den gewünschten mechanischen Eigenschaften zu erhalten.
- Eine Überbetonung der Dichte allein kann zu einer Beeinträchtigung der Festigkeit oder Härte aufgrund von Kornwachstum führen.
- Ein ausgewogener Ansatz gewährleistet eine optimale Dichte und Materialleistung.
Zusammenfassend lässt sich sagen, dass die Sintertemperatur ein entscheidender Faktor für die Dichte und Gesamtqualität eines Sintermaterials ist.Eine ordnungsgemäße Kontrolle von Temperatur, Zeit und Atmosphäre gewährleistet ein dichtes, festes und haltbares Produkt, während Abweichungen von den optimalen Bedingungen zu Mängeln oder verschlechterten Eigenschaften führen können.
Zusammenfassende Tabelle:
Faktor | Auswirkungen auf das gesinterte Material |
---|---|
Höhere Sintertemperatur | Erhöht die Dichte durch Verringerung der Porosität; zu hohe Temperaturen führen zu Kornwachstum und Defekten. |
Unzureichende Temperatur | Führt zu einer unvollständigen Verdichtung, wodurch das Material porös und schwach wird. |
Optimale Temperatur | Sorgt für ein Gleichgewicht zwischen Verdichtung und Materialintegrität und gewährleistet Festigkeit und Haltbarkeit. |
Sinterzeit | Längere Zeiten verbessern die Verdichtung; zu lange Zeiten bei hohen Temperaturen verursachen Kornwachstum. |
Sinteratmosphäre | Beeinflusst Dichte und Eigenschaften; reduzierende Atmosphären verhindern Oxidation und fördern die Verdichtung. |
Mikrostrukturelle Veränderungen | Beeinflusst die Korngröße, die Porengröße und die Korngrenzen und wirkt sich direkt auf die mechanischen Eigenschaften aus. |
Erzielen Sie das perfekte Gleichgewicht zwischen Dichte und Materialfestigkeit. Kontaktieren Sie noch heute unsere Experten um Ihren Sinterprozess zu optimieren!