Die Abscheidungsrate einer Dünnschicht ist ein kritischer Parameter bei der Abscheidung von Dünnschichten, da sie bestimmt, wie schnell die Schicht hergestellt wird.Sie wird in der Regel in Einheiten der Dicke pro Zeiteinheit gemessen (z. B. Nanometer pro Sekunde oder Angström pro Minute).Die Abscheiderate hängt von der verwendeten Abscheidungstechnologie ab, wie z. B. Magnetronsputtern, chemische Gasphasenabscheidung (CVD) oder physikalische Gasphasenabscheidung (PVD).Beim Magnetronsputtern beispielsweise kann die Abscheiderate nach folgender Formel berechnet werden:( R_{dep} = A \times R_{sputter} ), wobei ( R_{dep} ) die Abscheiderate, ( A ) die Abscheidefläche und ( R_{sputter} ) die Sputterrate ist.Das Verständnis und die Kontrolle der Abscheidungsrate sind für das Erreichen der gewünschten Schichtdicke und Qualität bei verschiedenen Anwendungen von entscheidender Bedeutung.
Die wichtigsten Punkte werden erklärt:
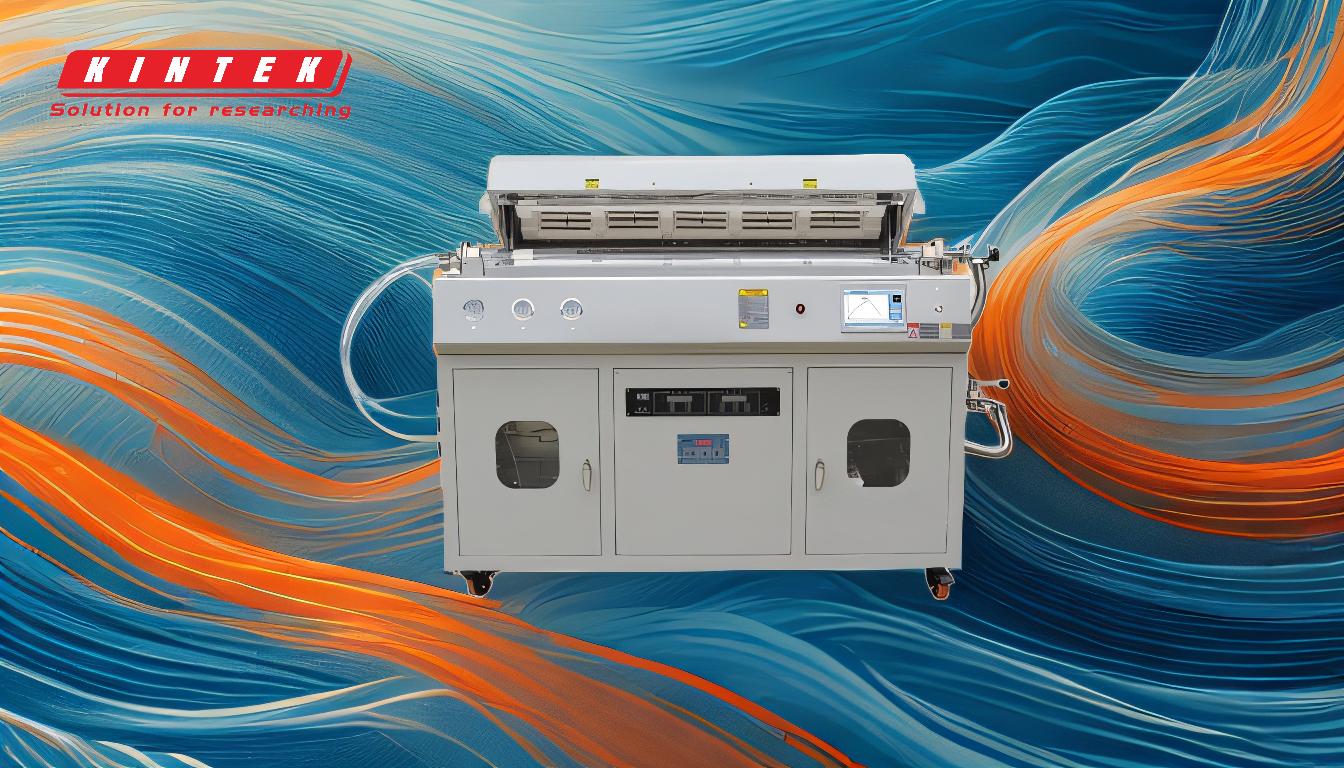
-
Definition der Depositionsrate:
- Die Abscheiderate ist ein Maß dafür, wie schnell sich ein dünner Film auf einem Substrat abscheidet.Sie wird in der Regel in Einheiten der Dicke (z. B. Nanometer, Angström) geteilt durch die Zeit (z. B. Sekunden, Minuten) angegeben.
- Dieser Parameter ist von entscheidender Bedeutung, um sicherzustellen, dass die Folie mit einer für die Anwendung angemessenen Geschwindigkeit hergestellt wird, so dass ein Gleichgewicht zwischen der Notwendigkeit einer schnellen Produktion und dem Erfordernis einer präzisen Kontrolle der Foliendicke besteht.
-
Maßeinheiten:
- Die Abscheiderate wird in der Regel in Einheiten wie Nanometer pro Sekunde (nm/s) oder Angström pro Minute (Å/min) gemessen.Diese Einheiten spiegeln die Dicke der in einem bestimmten Zeitraum abgeschiedenen Schicht wider.
- Die Wahl der Einheiten hängt von der jeweiligen Anwendung und der erforderlichen Präzision bei der Kontrolle der Schichtdicke ab.
-
Formel für die Abscheiderate bei der Magnetronzerstäubung:
-
Beim Magnetronsputtern, einem gängigen Verfahren zur Abscheidung von Dünnschichten, kann die Abscheiderate anhand der folgenden Formel berechnet werden:
- [
- R_{dep} = A \times R_{sputter}
- ]
- wobei:
-
Beim Magnetronsputtern, einem gängigen Verfahren zur Abscheidung von Dünnschichten, kann die Abscheiderate anhand der folgenden Formel berechnet werden:
-
( R_{dep} ) = Ablagerungsrate ( A ) = Abscheidungsfläche
- ( R_{sputter} ) = Sputteringrate Diese Formel besagt, dass die Abscheidungsrate direkt proportional zur Abscheidungsfläche und zur Sputterrate ist.Die Sputterrate wird von Faktoren wie der am Magnetron angelegten Leistung, der Art des Targetmaterials und dem Druck des Sputtergases beeinflusst.
- Faktoren, die die Abscheiderate beeinflussen:
- Angewandte Energie:Höhere Leistungen in Sputtersystemen erhöhen im Allgemeinen die Sputterrate, was zu einer höheren Abscheidungsrate führt.
- Ziel-Material:Verschiedene Materialien haben unterschiedliche Sputtering-Ausbeuten, die sich auf die Abscheidungsrate auswirken.So haben Metalle in der Regel höhere Sputteringraten als Isolatoren.
-
Gasdruck:Der Druck des Sputtergases (z. B. Argon) kann die Abscheidungsrate beeinflussen.Um die gewünschte Abscheidungsrate und Schichtqualität zu erreichen, sind optimale Druckwerte erforderlich.
- Temperatur des Substrats
- :Die Temperatur des Substrats kann sich ebenfalls auf die Abscheiderate auswirken, da höhere Temperaturen die Mobilität der Adatome auf der Substratoberfläche erhöhen können.
- Bedeutung der Kontrolle der Abscheidungsrate
-
: Die Steuerung der Abscheiderate ist für die Erzielung der gewünschten Schichteigenschaften, wie Dicke, Gleichmäßigkeit und Haftung, von entscheidender Bedeutung.
- Bei industriellen Anwendungen kann eine hohe Abscheiderate wünschenswert sein, um den Durchsatz zu erhöhen, sie muss jedoch mit der Notwendigkeit einer genauen Kontrolle der Schichtdicke und -qualität in Einklang gebracht werden. In der Forschung und Entwicklung ist eine präzise Steuerung der Abscheidungsrate häufig erforderlich, um die Auswirkungen der Schichtdicke auf die Materialeigenschaften zu untersuchen.
- Anwendungen der Abscheideratenkontrolle:
- Halbleiterherstellung:Bei der Herstellung von Halbleiterbauelementen ist eine präzise Steuerung der Abscheidungsrate entscheidend für die Erzeugung dünner Schichten mit spezifischen elektrischen Eigenschaften.
Optische Beschichtungen
:Bei optischen Beschichtungen, wie z. B. Antireflexbeschichtungen, muss die Abscheidungsrate sorgfältig kontrolliert werden, um die gewünschte optische Leistung zu erzielen.
Schutzschichten | :Bei Anwendungen, bei denen dünne Schichten zu Schutzzwecken eingesetzt werden, wie z. B. bei korrosionsbeständigen Beschichtungen, muss die Abscheidungsrate optimiert werden, um eine angemessene Abdeckung und Haltbarkeit zu gewährleisten. |
---|---|
Zusammenfassend lässt sich sagen, dass die Abscheiderate ein grundlegender Parameter bei der Abscheidung von Dünnschichten ist und dass ihre Steuerung für das Erreichen der gewünschten Schichteigenschaften in verschiedenen Anwendungen von wesentlicher Bedeutung ist.Die Formel zur Berechnung der Abscheiderate beim Magnetronsputtern ( R_{dep} = A \times R_{sputter} ) liefert eine klare Beziehung zwischen Abscheiderate, Abscheidefläche und Sputterrate.Das Verständnis und die Kontrolle der Faktoren, die die Abscheidungsrate beeinflussen, sind der Schlüssel zur Optimierung von Dünnschichtabscheidungsprozessen. | Zusammenfassende Tabelle: |
Hauptaspekt | Einzelheiten |
Definition | Die Geschwindigkeit, mit der ein dünner Film auf ein Substrat aufgebracht wird. |
Einheiten | Nanometer pro Sekunde (nm/s) oder Angström pro Minute (Å/min). |
Formel (Magnetronzerstäubung) | ( R_{dep} = A \mal R_{sputter} ) |
Beeinflussende Faktoren Angewandte Leistung, Zielmaterial, Gasdruck und Substrattemperatur. Anwendungen