Die Haltezeit für das Sintern, d. h. die Dauer, in der das Material auf der Sintertemperatur gehalten wird, ist je nach Material, gewünschten Eigenschaften und spezifischem Sinterverfahren sehr unterschiedlich. Im Allgemeinen kann die Sinterung von Sekunden bis zu mehreren Stunden dauern, wobei typische industrielle Prozesse oft zwischen 15 und 20 Stunden dauern. Die genaue Haltezeit wird von Faktoren wie Temperatur, Druck, Partikelgröße, Zusammensetzung und der Art des verwendeten Ofens beeinflusst. Das Verständnis dieser Variablen ist entscheidend für die Optimierung des Sinterprozesses, um die gewünschten Materialeigenschaften wie Dichte, Festigkeit und Porosität zu erreichen.
Die wichtigsten Punkte werden erklärt:
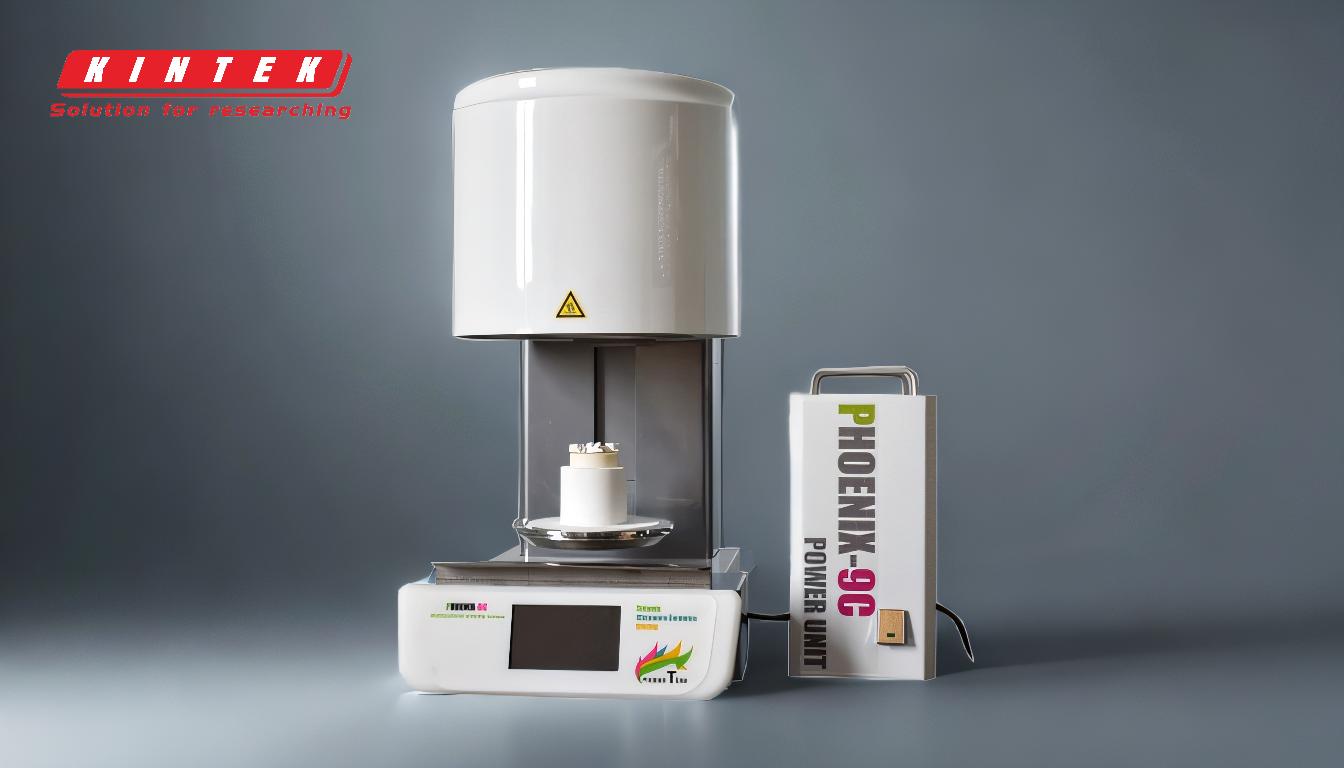
-
Definition der Haltezeit beim Sintern:
- Die Haltezeit ist der Zeitraum, in dem das Material auf der Sintertemperatur gehalten wird, um eine Verdichtung und Bindung der Partikel zu ermöglichen. Diese Phase ist entscheidend für das Erreichen der gewünschten mechanischen und physikalischen Eigenschaften des gesinterten Produkts.
-
Typische Dauer der Sinterung:
-
Die Sinterung kann von Sekunden bis zu mehreren Stunden dauern. Ein Beispiel:
- Kurzzeitsintern: Einige Verfahren, insbesondere solche mit feinen Pulvern oder hohen Temperaturen, können innerhalb von Sekunden abgeschlossen werden.
- Sintern mit langer Dauer: Industrielle Prozesse, insbesondere solche, die Teile mit hoher Dichte erfordern, dauern oft zwischen 15 und 20 Stunden.
-
Die Sinterung kann von Sekunden bis zu mehreren Stunden dauern. Ein Beispiel:
-
Faktoren, die die Haltezeit beeinflussen:
- Temperatur: Höhere Temperaturen können die erforderliche Haltezeit verkürzen, indem sie die Sinterkinetik beschleunigen. Zu hohe Temperaturen können jedoch zu unerwünschtem Kornwachstum oder Materialverschlechterung führen.
- Druck: Angewandter Druck kann die Umlagerung der Partikel fördern und die Porosität verringern, wodurch die Haltezeit verkürzt werden kann.
- Partikelgröße: Kleinere Partikel haben ein größeres Verhältnis von Oberfläche zu Volumen, was eine schnellere Verdichtung fördert und die Verweilzeit verkürzen kann.
- Zusammensetzung: Homogene Zusammensetzungen mit gleichmäßiger Partikelverteilung neigen dazu, effizienter zu sintern, was sich auf die optimale Haltedauer auswirkt.
- Atmosphäre: Die Sinterumgebung (z. B. Luft, Vakuum oder Inertgase) kann die Oxidation oder Verunreinigung beeinflussen, was sich indirekt auf die Haltedauer auswirkt.
-
Sintertechniken und ihr Einfluss auf die Haltezeit:
- Konventionelles Sintern: Erfordert in der Regel längere Haltezeiten (15-20 Stunden), um Teile mit hoher Dichte zu erhalten.
- Spark Plasma Sintering (SPS): Das Material wird mit Hilfe elektrischer Ströme schnell erhitzt, wodurch die Haltezeit auf Minuten oder sogar Sekunden verkürzt wird.
- Heißpressen: Kombiniert Hitze und Druck, was im Vergleich zum herkömmlichen Sintern oft zu kürzeren Haltezeiten führt.
-
Materialspezifische Überlegungen:
-
Verschiedene Werkstoffe erfordern je nach ihren thermischen und mechanischen Eigenschaften unterschiedliche Haltezeiten. Zum Beispiel:
- Keramiken: Aufgrund ihres hohen Schmelzpunkts und ihrer geringen Diffusionsrate benötigen sie oft längere Haltezeiten.
- Metalle: Können schneller sintern, insbesondere bei Verwendung von feinen Pulvern oder hohem Druck.
- Verbundwerkstoffe: Die Haltezeit muss das Sinterverhalten der einzelnen Komponenten ausgleichen, um Delamination oder ungleichmäßige Verdichtung zu vermeiden.
-
Verschiedene Werkstoffe erfordern je nach ihren thermischen und mechanischen Eigenschaften unterschiedliche Haltezeiten. Zum Beispiel:
-
Ofentyp und seine Rolle:
-
Die Art des verwendeten Ofens (z. B. Förderband-, Schub- oder Batch-Ofen) kann die Haltezeit beeinflussen. Zum Beispiel:
- Förderbandöfen: Geeignet für kontinuierliche Prozesse mit kürzeren Haltezeiten.
- Batch-Öfen: Ermöglichen eine präzise Steuerung von Temperatur und Atmosphäre und werden häufig für längere Haltezeiten bei hochpräzisen Anwendungen eingesetzt.
-
Die Art des verwendeten Ofens (z. B. Förderband-, Schub- oder Batch-Ofen) kann die Haltezeit beeinflussen. Zum Beispiel:
-
Optimierung der Haltezeit:
- Die optimale Haltezeit wird durch ein Gleichgewicht zwischen den gewünschten Materialeigenschaften (z. B. Dichte, Festigkeit) und der Prozesseffizienz bestimmt. Eine Übersinterung kann zu übermäßigem Kornwachstum führen, während eine Untersinterung eine unzureichende Verdichtung zur Folge haben kann.
-
Praktische Auswirkungen für Einkäufer von Anlagen und Verbrauchsmaterialien:
-
Die Kenntnis der Haltezeit ist für die Auswahl der geeigneten Sinteranlagen und Verbrauchsmaterialien von entscheidender Bedeutung. Zum Beispiel:
- Auswahl des Ofens: Wählen Sie einen Ofen, der die erforderliche Temperatur und Atmosphäre für die angegebene Haltezeit aufrechterhalten kann.
- Auswahl des Materials: Stellen Sie sicher, dass das Sinterverhalten des Materials mit den gewählten Prozessparametern übereinstimmt.
- Kostenüberlegungen: Längere Haltezeiten können den Energieverbrauch und die Betriebskosten erhöhen, so dass die Optimierung des Prozesses für die Kosteneffizienz entscheidend ist.
-
Die Kenntnis der Haltezeit ist für die Auswahl der geeigneten Sinteranlagen und Verbrauchsmaterialien von entscheidender Bedeutung. Zum Beispiel:
Durch die sorgfältige Berücksichtigung dieser Faktoren können Einkäufer und Ingenieure den Sinterprozess optimieren, um auf effiziente Weise qualitativ hochwertige Produkte herzustellen.
Zusammenfassende Tabelle:
Faktor | Einfluss auf die Haltezeit |
---|---|
Temperatur | Höhere Temperaturen verkürzen die Zeit; übermäßige Hitze kann zu Kornwachstum oder Zersetzung führen. |
Druck | Angewandter Druck verkürzt die Zeit, indem er die Umlagerung der Partikel fördert. |
Partikelgröße | Kleinere Partikel verkürzen die Zeit aufgrund des besseren Verhältnisses von Oberfläche zu Volumen. |
Zusammensetzung | Homogene Zusammensetzungen sintern effizienter, was sich auf die optimale Zeit auswirkt. |
Atmosphäre | Die Sinterumgebung (Luft, Vakuum, Inertgase) beeinflusst Oxidation und Verunreinigung. |
Sintertechnik | Konventionell: 15-20 Stunden; SPS: Minuten/Sekunden; Heißpressen: kürzer als konventionell. |
Materialtyp | Keramik: länger; Metalle: schneller; Verbundwerkstoffe: ausgewogenes Sinterverhalten erforderlich. |
Ofentyp | Förderband: kürzere Zeiten; Batch: präzise Steuerung, längere Zeiten für hohe Präzision. |
Optimieren Sie Ihren Sinterprozess noch heute - Kontaktieren Sie unsere Experten für maßgeschneiderte Lösungen!