Das Spritzgussverfahren ist ein hocheffizientes Herstellungsverfahren, mit dem komplex geformte Kunststoffteile in großen Mengen produziert werden können.Dabei wird das Kunststoffmaterial geschmolzen und in eine Pressform Die Form wird unter hohem Druck in den Hohlraum gepresst, zum Erstarren abgekühlt und das fertige Produkt anschließend ausgeworfen.Dieses Verfahren ist in der Industrie wegen seiner Präzision, Wiederholbarkeit und der Möglichkeit, komplizierte Designs herzustellen, weit verbreitet.Im Folgenden wird das Spritzgießverfahren Schritt für Schritt erklärt.
Die wichtigsten Punkte werden erklärt:
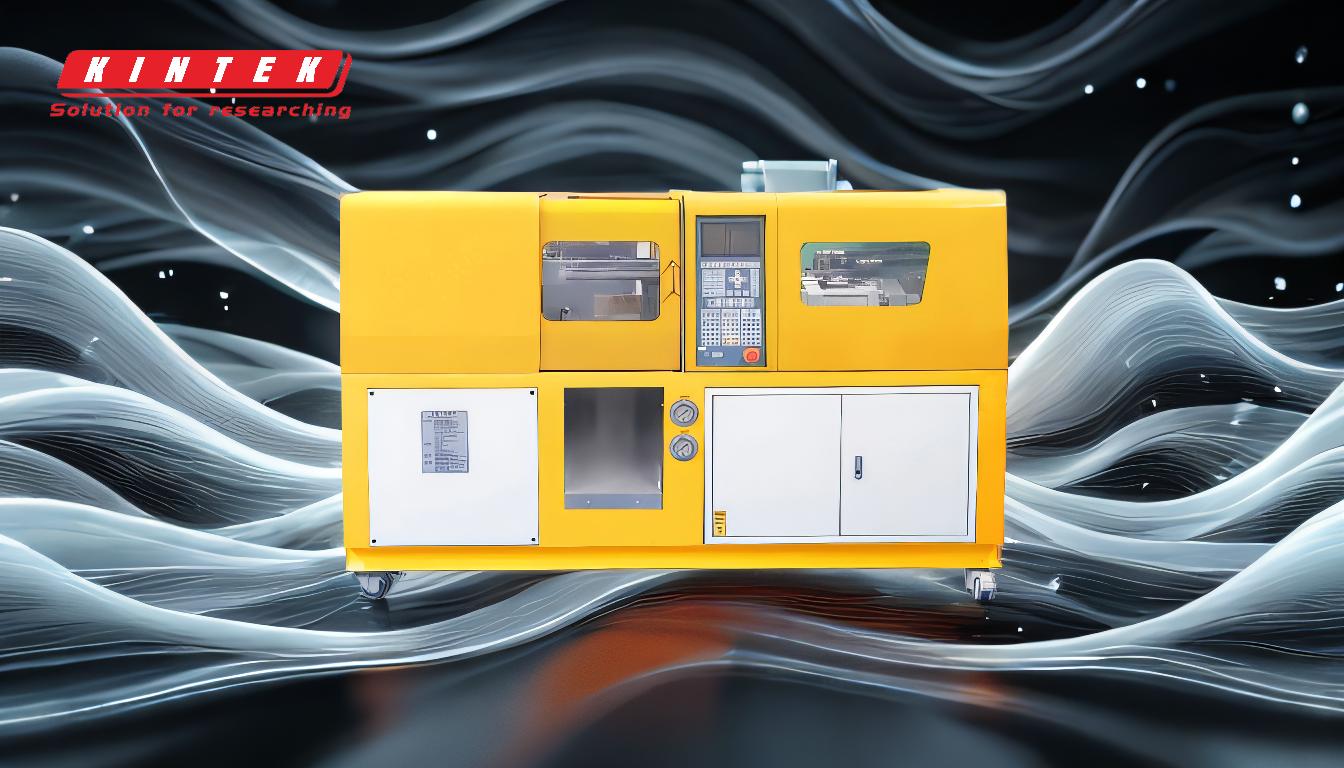
-
Materialaufbereitung und -zufuhr
- Kunststoffpellets oder -granulate werden in den Trichter der Spritzgießmaschine eingefüllt.
- Das Material wird dann in den Zylinder befördert, wo es von einer rotierenden Schnecke erhitzt und gemischt wird.
- Die Schnecke sorgt für ein gleichmäßiges Schmelzen und Homogenisieren des Kunststoffs.
-
Schmelzen und Plastifizieren
- Im Inneren des Zylinders wird das Kunststoffmaterial bis zu seinem Schmelzpunkt erhitzt, wodurch es in einen geschmolzenen Zustand übergeht.
- Die Schnecke mischt und verdichtet den geschmolzenen Kunststoff weiter, um eine gleichmäßige Viskosität und Temperatur zu gewährleisten.
- Dieser Schritt ist entscheidend für die Qualität der Gussteile.
-
Einspritzen in den Formhohlraum
- Sobald der Kunststoff vollständig geschmolzen ist, bewegt sich die Schnecke nach vorne und wirkt wie ein Kolben, um das geschmolzene Material in den Formhohlraum zu spritzen.
- Es wird ein hoher Druck ausgeübt, um sicherzustellen, dass das Material jedes Detail der Form ausfüllt, einschließlich komplizierter Geometrien.
- Die Form wird durch eine Schließeinheit geschlossen gehalten, um dem Einspritzdruck standzuhalten.
-
Abkühlung und Erstarrung
- Nach dem Füllen des Formhohlraums beginnt der geschmolzene Kunststoff abzukühlen und zu erstarren, wobei er die Form der Form annimmt.
- Die Abkühlungszeit hängt von den Materialeigenschaften, der Dicke des Teils und der Konstruktion der Form ab.
- Eine ordnungsgemäße Kühlung ist wichtig, um Defekte wie Verzug oder Einfallstellen zu vermeiden.
-
Öffnen der Form und Auswerfen
- Sobald das Teil erstarrt ist, öffnet sich die Form, und Auswerferstifte drücken das fertige Produkt aus dem Formhohlraum.
- Das ausgeworfene Teil wird dann für die weitere Verarbeitung oder Verpackung gesammelt.
- Die Form schließt sich wieder, und der Zyklus wiederholt sich für das nächste Teil.
-
Nachbearbeitung (falls erforderlich)
- Bei einigen Teilen sind zusätzliche Schritte wie Beschneiden, Lackieren oder Montage erforderlich.
- Diese Schritte gewährleisten, dass das Endprodukt den gewünschten Spezifikationen und Qualitätsstandards entspricht.
Ausführliche Erläuterung:
-
Materialaufbereitung und -zuführung
Der Prozess beginnt mit der Auswahl des geeigneten Kunststoffmaterials, das in der Regel in Form von Pellets oder Granulat vorliegt.Diese Materialien werden in den Trichter eingefüllt, der sie in den Zylinder der Spritzgießmaschine befördert.Der Zylinder ist mit einer rotierenden Schnecke ausgestattet, die das Material vorwärts transportiert, während es auf die erforderliche Temperatur erhitzt wird.Dieser Schritt stellt sicher, dass das Material für die nächste Phase des Schmelzens und Plastifizierens bereit ist. -
Schmelzen und Plastifizieren
Im Inneren des Zylinders wird das Kunststoffmaterial durch die Schnecke erhitzt und mechanisch geschert.Die Kombination aus Wärme und Reibung schmilzt den Kunststoff und verwandelt ihn in eine viskose Flüssigkeit.Die Konstruktion der Schnecke sorgt für eine gründliche Durchmischung, wodurch Ungleichmäßigkeiten im Material vermieden werden.Dieser Schritt ist von entscheidender Bedeutung, da sich die Qualität des geschmolzenen Kunststoffs direkt auf die Eigenschaften des Endprodukts auswirkt, z. B. auf die Festigkeit, die Oberflächenbeschaffenheit und die Maßhaltigkeit. -
Einspritzen in den Formhohlraum
Sobald der Kunststoff vollständig geschmolzen ist, beginnt die Einspritzphase.Die Schnecke bewegt sich vorwärts und wirkt wie ein Kolben, um das geschmolzene Material in den Formhohlraum einzuspritzen.Die Form ist so präzise gestaltet, dass die gewünschte Form des Teils entsteht.Während des Einspritzens wird hoher Druck ausgeübt, um sicherzustellen, dass das Material alle Bereiche der Form ausfüllt, einschließlich feiner Details und dünner Abschnitte.Die Schließeinheit hält die Form fest geschlossen, um dem hohen Einspritzdruck standzuhalten, und verhindert so jegliche Leckage oder Verformung. -
Kühlung und Erstarrung
Nachdem der Formhohlraum gefüllt ist, beginnt die Abkühlphase.Der geschmolzene Kunststoff beginnt abzukühlen und zu erstarren, wobei er die Form des Werkzeugs annimmt.Die Abkühlzeit ist ein kritischer Faktor im Spritzgießprozess, da sie die Zykluszeit bestimmt und die Qualität des Teils beeinflusst.Eine ordnungsgemäße Kühlung stellt sicher, dass das Teil gleichmäßig erstarrt und Fehler wie Verformungen, Einfallstellen oder innere Spannungen minimiert werden.Das Kühlsystem in der Form, das häufig Wasserkanäle verwendet, trägt zur Temperaturregulierung und Beschleunigung des Prozesses bei. -
Öffnen der Form und Auswerfen
Sobald das Teil ausreichend abgekühlt und verfestigt ist, öffnet sich die Form, und das fertige Produkt wird ausgeworfen.Auswerferstifte oder -platten werden verwendet, um das Teil aus dem Formhohlraum zu drücken.Dann schließt sich die Form und der Zyklus wiederholt sich für das nächste Teil.Dieser Schritt erfordert Präzision, um sicherzustellen, dass das Teil ohne Beschädigung ausgeworfen wird und die Form für die nächste Einspritzung bereit ist. -
Nachbearbeitung (falls erforderlich)
Je nach Anwendung sind bei einigen Teilen zusätzliche Nachbearbeitungsschritte erforderlich.Dazu kann das Beschneiden von überschüssigem Material (Grat), das Lackieren oder Beschichten zu ästhetischen Zwecken oder das Zusammenfügen mehrerer Komponenten gehören.Durch die Nachbearbeitung wird sichergestellt, dass das Endprodukt die erforderlichen Spezifikationen und Qualitätsstandards erfüllt.
Schlussfolgerung:
Das Spritzgießverfahren ist ein vielseitiges und effizientes Verfahren zur Herstellung hochwertiger Kunststoffteile mit komplexen Geometrien.Durch die Abfolge der Schritte Materialvorbereitung, Schmelzen, Einspritzen, Abkühlen, Auswerfen und Nachbearbeitung können Hersteller konsistente und präzise Ergebnisse erzielen.Dieses Verfahren ist in vielen Industriezweigen weit verbreitet, da es große Mengen von Teilen mit minimalem Ausschuss und hoher Wiederholbarkeit produzieren kann.
Zusammenfassende Tabelle:
Schritt | Beschreibung |
---|---|
1.Vorbereitung des Materials | Kunststoffgranulat wird in den Trichter gefüllt, erhitzt und in der Trommel gemischt. |
2.Schmelzen & Plastifizieren | Das Material wird geschmolzen und von der Schnecke homogenisiert, um eine gleichmäßige Viskosität zu erreichen. |
3.Einspritzen in die Form | Geschmolzener Kunststoff wird unter hohem Druck in den Formhohlraum gespritzt. |
4.Abkühlung und Erstarrung | Der Kunststoff kühlt ab und erstarrt in der gewünschten Form. |
5.Öffnen der Form und Auswerfen | Die Form öffnet sich, und die Auswerferstifte drücken das fertige Teil heraus. |
6.Nachbearbeitung | Zusätzliche Schritte wie Beschneiden oder Lackieren können für die endgültige Qualität erforderlich sein. |
Sind Sie bereit, Ihren Fertigungsprozess zu optimieren? Kontaktieren Sie uns noch heute um mehr über Spritzgießlösungen zu erfahren!