Die thermische Verdampfung ist ein Vakuumverfahren zur Herstellung dünner Schichten, bei dem ein Material in einer Vakuumkammer erhitzt wird, bis es verdampft. Die verdampften Atome oder Moleküle wandern dann durch das Vakuum und lagern sich auf einem Substrat ab, wobei sie eine gleichmäßige Beschichtung bilden. Dieses Verfahren ist eine der ältesten und einfachsten Formen der physikalischen Gasphasenabscheidung (PVD). Es wird häufig in Branchen wie Elektronik, Optik und Solarenergie eingesetzt, um Metalle wie Silber und Aluminium für Anwendungen wie OLEDs, Solarzellen und Dünnschichttransistoren abzuscheiden. Das Verfahren beruht auf einer Widerstandsheizung, bei der ein elektrischer Strom ein Schiffchen, eine Spule oder einen Korb mit dem Zielmaterial erhitzt, so dass es schmilzt und verdampft. Der daraus resultierende Dampfstrom beschichtet das Substrat und erzeugt einen dünnen Film, dessen Dicke und Zusammensetzung sich genau steuern lässt.
Die wichtigsten Punkte werden erklärt:
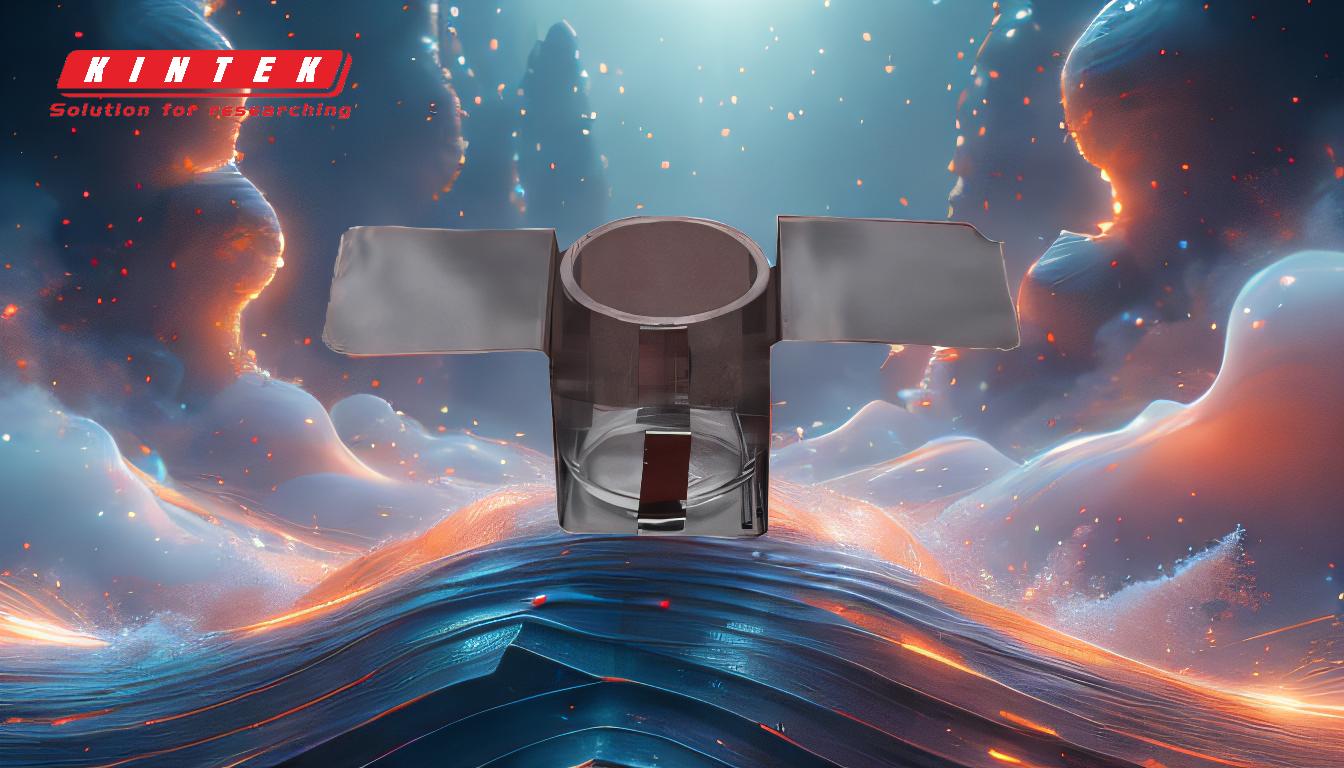
-
Definition und Grundprinzip der thermischen Verdampfung:
- Bei der thermischen Verdampfung handelt es sich um eine Technik der physikalischen Gasphasenabscheidung (PVD), bei der ein Material in einer Hochvakuumumgebung erhitzt wird, bis es verdampft. Die verdampften Atome oder Moleküle wandern durch das Vakuum und lagern sich auf einem Substrat ab und bilden einen dünnen Film.
- Das Verfahren beruht auf dem Prinzip des Dampfdrucks: Wenn ein Material bis zu seinem Verdampfungspunkt erhitzt wird, entsteht ein Dampfstrom, der auf dem Substrat kondensiert.
-
Komponenten des thermischen Verdampfungssystems:
- Vakuumkammer: Eine geschlossene Umgebung mit niedrigem Druck, um die Kontamination zu minimieren und dem verdampften Material eine ungehinderte Bewegung zu ermöglichen.
- Verdampfung Quelle: In der Regel ein Widerstandsschiffchen, eine Spule oder ein Korb aus Materialien wie Wolfram oder Molybdän. Die Quelle enthält das Zielmaterial und wird durch Durchleiten eines elektrischen Stroms erhitzt.
- Substrat: Die Oberfläche, auf die das verdampfte Material aufgebracht wird. Sie ist oberhalb der Verdampfungsquelle angeordnet, um eine gleichmäßige Beschichtung zu gewährleisten.
- Stromversorgung: Liefert den elektrischen Strom, der zum Erhitzen der Verdampfungsquelle benötigt wird.
-
Prozess-Schritte:
- Materialbeschickung: Das Zielmaterial (z. B. Metallgranulat) wird in die Verdampfungsquelle eingebracht.
- Vakuumerzeugung: Die Kammer wird evakuiert, um ein Hochvakuum zu erreichen, das die Anwesenheit von Luftmolekülen, die den Dampfstrom stören könnten, reduziert.
- Heizung: Ein elektrischer Strom wird durch die Verdampfungsquelle geleitet und erhitzt sie bis zu dem Punkt, an dem das Zielmaterial schmilzt und verdampft.
- Ablage: Das verdampfte Material wandert durch das Vakuum und lagert sich auf dem Substrat ab und bildet einen dünnen Film.
- Kühlung: Nach der Abscheidung lässt man das System abkühlen und entfernt das Substrat.
-
Anwendungen der thermischen Verdampfung:
- Elektronik: Für die Abscheidung von Metallen wie Silber und Aluminium für OLEDs, Dünnschichttransistoren und andere elektronische Bauteile.
- Optik: Wird bei der Herstellung von Reflexionsschichten, Antireflexionsschichten und optischen Filtern verwendet.
- Solarenergie: Wird zur Herstellung von Dünnschicht-Solarzellen und anderen photovoltaischen Geräten verwendet.
- Dekorative Beschichtungen: Wird zum Aufbringen von Metallic-Lackierungen auf Konsumgütern verwendet.
-
Vorteile der thermischen Verdampfung:
- Vereinfachung: Es handelt sich um eines der einfachsten und kostengünstigsten PVD-Verfahren.
- Hohe Reinheit: Die Vakuumumgebung minimiert die Verunreinigung, was zu hochreinen Filmen führt.
- Präzision: Ermöglicht eine präzise Kontrolle der Schichtdicke und -zusammensetzung.
- Vielseitigkeit: Kann eine breite Palette von Materialien abscheiden, darunter Metalle, Legierungen und einige Verbindungen.
-
Beschränkungen der thermischen Verdampfung:
- Materielle Beschränkungen: Einige Materialien, z. B. solche mit sehr hohem Schmelzpunkt, lassen sich mit dieser Methode nur schwer verdampfen.
- Herausforderungen bei der Einheitlichkeit: Es kann schwierig sein, gleichmäßige Beschichtungen auf komplexen oder großen Substraten zu erzielen.
- Thermische Belastung: Die hohen Temperaturen können zu einer thermischen Belastung des Substrats oder der Verdunstungsquelle führen.
-
Vergleich mit anderen PVD-Techniken:
- Sputtern: Im Gegensatz zur thermischen Verdampfung werden beim Sputtern energiereiche Ionen verwendet, um Atome aus einem Zielmaterial zu lösen. Beim Sputtern kann eine größere Bandbreite von Materialien abgeschieden werden, darunter auch Isolatoren, aber es ist komplexer und teurer.
- Elektronenstrahlverdampfung: Bei dieser Methode wird das Zielmaterial mit einem Elektronenstrahl erhitzt, was höhere Verdampfungstemperaturen und eine bessere Kontrolle des Abscheidungsprozesses ermöglicht. Sie ist jedoch teurer und komplexer als die thermische Verdampfung.
-
Wichtige Überlegungen für Einkäufer von Geräten und Verbrauchsmaterial:
- Kompatibilität der Materialien: Stellen Sie sicher, dass die Materialien der Verdampfungsquelle und der Kammer mit dem Zielmaterial kompatibel sind.
- Qualität des Vakuumsystems: Ein hochwertiges Vakuumsystem ist entscheidend, um eine geringe Kontamination und gleichbleibende Ergebnisse zu erzielen.
- Auslegung der Heizquelle: Das Design des Schiffchens, der Spule oder des Korbes sollte den Eigenschaften des Zielmaterials und der gewünschten Abscheiderate entsprechen.
- Handhabung von Substraten: Berücksichtigen Sie bei der Auswahl der Geräte die Größe, Form und Wärmeempfindlichkeit des Substrats.
Durch das Verständnis dieser Schlüsselpunkte können Käufer von Geräten und Verbrauchsmaterialien für die thermische Verdampfung fundierte Entscheidungen treffen, die auf ihre spezifischen Anwendungsanforderungen abgestimmt sind.
Zusammenfassende Tabelle:
Aspekt | Einzelheiten |
---|---|
Definition | Ein PVD-Verfahren, bei dem Materialien in einem Vakuum erhitzt werden, um dünne Schichten zu bilden. |
Wichtige Komponenten | Vakuumkammer, Verdampfungsquelle, Substrat, Stromversorgung. |
Prozess-Schritte | Materialbeschickung, Vakuumerzeugung, Erwärmung, Ablagerung, Abkühlung. |
Anwendungen | Elektronik (OLEDs, Dünnschichttransistoren), Optik, Solarenergie, Beschichtungen. |
Vorteile | Einfachheit, hohe Reinheit, Präzision und Vielseitigkeit. |
Beschränkungen | Materialbeschränkungen, Gleichmäßigkeitsprobleme, thermische Belastung. |
Vergleich mit PVD | Einfacher und kostengünstiger als Sputtern oder Elektronenstrahlverfahren. |
Tipps für den Einkauf | Beachten Sie die Materialverträglichkeit, die Vakuumqualität und die Handhabung des Substrats. |
Sind Sie bereit, Ihren Dünnschichtabscheidungsprozess zu verbessern? Kontaktieren Sie uns heute für fachkundige Beratung und Ausrüstungslösungen!