Reaktives Sputtern ist ein Verfahren zur Abscheidung von Dünnschichten, bei dem ein Zielmaterial in Gegenwart eines reaktiven Gases wie Sauerstoff oder Stickstoff gesputtert wird, um einen Verbundfilm auf einem Substrat zu bilden.Bei diesem Verfahren wird das reaktive Gas in einer Plasmaumgebung ionisiert, das dann mit den gesputterten Zielatomen chemisch reagiert und Verbindungen wie Oxide oder Nitride bildet.Mit dieser Methode lassen sich die Zusammensetzung und die Eigenschaften der Schichten durch Einstellung von Parametern wie Gasfluss und Partialdruck genau steuern.Der Mechanismus ist aufgrund der Wechselwirkungen zwischen dem reaktiven Gas und dem Target komplex und erfordert oft eine sorgfältige Optimierung, um ein hystereseähnliches Verhalten zu vermeiden und die gewünschte Filmstöchiometrie und die gewünschten funktionellen Eigenschaften zu erreichen.
Die wichtigsten Punkte werden erklärt:
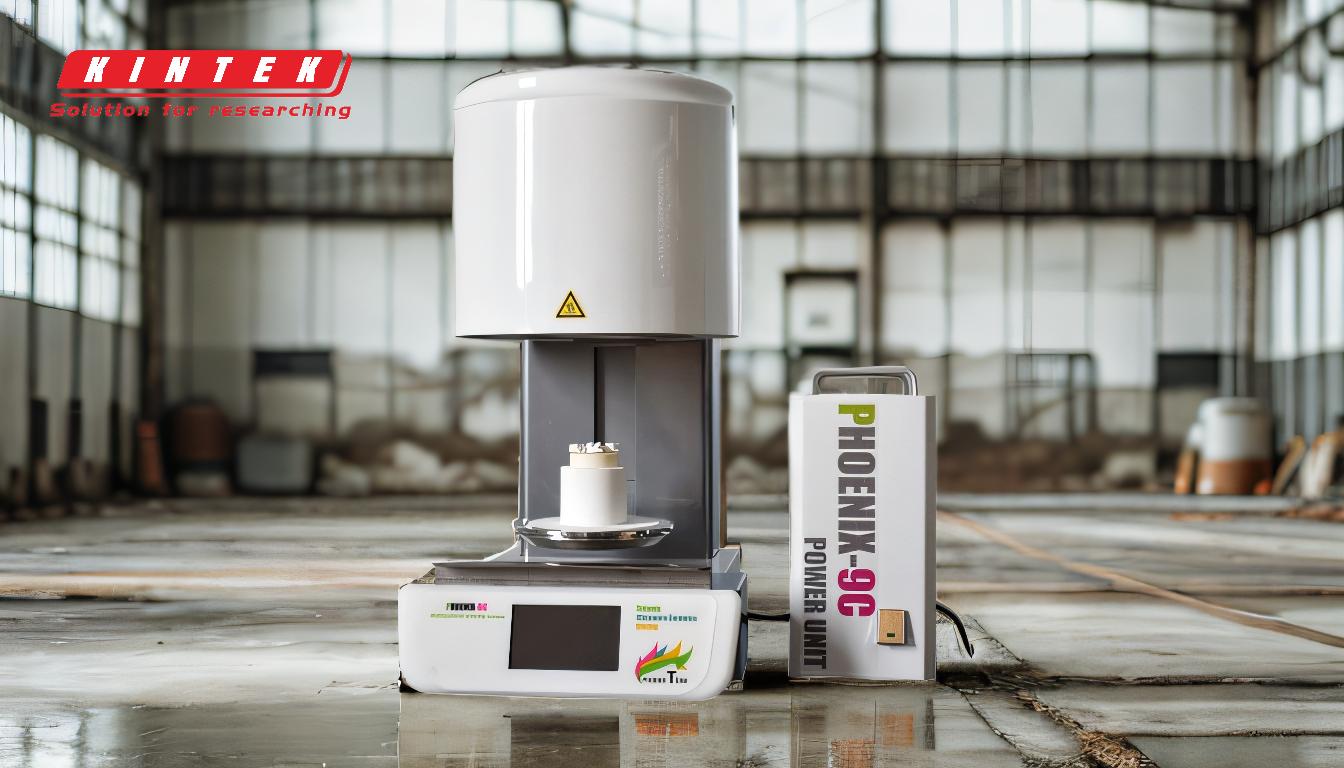
-
Definition und Zweck des reaktiven Sputterns:
- Reaktives Sputtern ist eine Variante des Plasmasputterns, die zur Abscheidung dünner Schichten mit bestimmten chemischen Zusammensetzungen wie Oxiden oder Nitriden verwendet wird.
- Bei diesem Verfahren wird ein reaktives Gas (z. B. Sauerstoff oder Stickstoff) in die Sputterkammer eingeleitet, das mit dem gesputterten Zielmaterial chemisch reagiert und eine Verbundschicht bildet.
-
Wichtigste beteiligte Komponenten:
- Ziel Material:Die Quelle der zu zerstäubenden Atome (z. B. Silizium, Aluminium oder Titan).
- Reaktives Gas:Ein Gas wie Sauerstoff oder Stickstoff, das mit den gesputterten Atomen reagiert und eine Verbindung bildet.
- Inertes Gas:In der Regel Argon, das zur Erzeugung des Plasmas verwendet wird, das das Zielmaterial zerstäubt.
- Substrat:Die Oberfläche, auf der die dünne Schicht abgeschieden wird (z. B. ein Silizium-Wafer).
-
Mechanismus des reaktiven Sputterns:
- Das Inertgas (Argon) wird ionisiert und bildet ein Plasma, das das Zielmaterial beschießt und Atome in die Kammer schleudert.
- Das reaktive Gas wird in die Kammer eingeleitet und in der Plasmaumgebung ionisiert.
- Das ionisierte reaktive Gas reagiert chemisch mit den gesputterten Zielatomen und bildet eine Verbindung (z. B. Siliziumoxid oder Titannitrid).
- Die Verbindung wird dann als Dünnschicht auf dem Substrat abgeschieden.
-
Die Rolle des reaktiven Gases:
- Das reaktive Gas bestimmt die chemische Zusammensetzung der abgeschiedenen Schicht.
- Sauerstoff kann beispielsweise Oxide (z. B. Siliziumoxid) bilden, während Stickstoff Nitride (z. B. Titannitrid) bilden kann.
- Die Menge und die Art des reaktiven Gases beeinflussen die Stöchiometrie und die Eigenschaften des Films.
-
Herausforderungen und Kontrollparameter:
- Hysterese-ähnliches Verhalten:Die Einführung eines reaktiven Gases kann zu nichtlinearen Effekten führen, was die Kontrolle des Prozesses erschwert.Dies erfordert ein sorgfältiges Management von Parametern wie Gasfluss und Partialdruck.
- Berg Modell:Ein theoretischer Rahmen zur Vorhersage der Auswirkungen des reaktiven Gases auf die Erosions- und Ablagerungsraten des Targets.
- Stöchiometrische Kontrolle:Die Einstellung der relativen Drücke von Inert- und Reaktivgasen ermöglicht eine präzise Kontrolle der Schichtzusammensetzung und der Eigenschaften, wie Spannung und Brechungsindex.
-
Anwendungen des reaktiven Sputterns:
- Optische Beschichtungen:Herstellung von Schichten mit spezifischen Brechungsindizes für Linsen und Spiegel.
- Barriere-Schichten:Herstellung dünner fester Schichten wie Titannitrid zur Verwendung in Halbleiterbauelementen.
- Funktionelle Filme:Abscheidung von Materialien mit maßgeschneiderten mechanischen, elektrischen oder optischen Eigenschaften für moderne Anwendungen.
-
DC- und HF-Varianten:
- Das reaktive Sputtern kann mit Gleichstrom- (DC) oder Hochfrequenz- (HF) Stromquellen durchgeführt werden.
- Die Wahl der Stromquelle hängt vom Zielmaterial und den gewünschten Schichteigenschaften ab.
-
Vorteile des reaktiven Sputterns:
- Ermöglicht die Abscheidung einer breiten Palette von Verbundfolien mit präziser Kontrolle über Zusammensetzung und Eigenschaften.
- Geeignet für die Herstellung von Folien mit spezifischen funktionellen Eigenschaften, wie hohe Härte, Transparenz oder Leitfähigkeit.
-
Praktische Überlegungen:
- Das Verfahren erfordert eine sorgfältige Optimierung, um den Reaktivgasfluss und die Sputterrate auszugleichen.
- Ein geeignetes Kammerdesign und Gaszufuhrsysteme sind entscheidend, um konsistente Ergebnisse zu erzielen.
Durch das Verständnis dieser Schlüsselpunkte können die Käufer von Anlagen und Verbrauchsmaterialien die Anforderungen an reaktive Sputtersysteme, wie z. B. die Auswahl von Targetmaterialien, reaktiven Gasen und Prozesssteuerungsinstrumenten, besser einschätzen, um optimale Ergebnisse bei der Dünnschichtabscheidung zu erzielen.
Zusammenfassende Tabelle:
Aspekt | Einzelheiten |
---|---|
Definition | Dünnschichtabscheidung unter Verwendung eines reaktiven Gases zur Bildung von Verbundschichten. |
Wichtige Komponenten | Zielmaterial, reaktives Gas (z. B. Sauerstoff, Stickstoff), Inertgas, Substrat. |
Mechanismus | Ein Inertgasplasma zerstäubt Zielatome, die mit reaktiven Gasionen reagieren. |
Anwendungen | Optische Beschichtungen, Barriereschichten, Funktionsfolien. |
Vorteile | Genaue Kontrolle über die Zusammensetzung und die Eigenschaften der Folie. |
Herausforderungen | Hystereseähnliches Verhalten, erfordert sorgfältige Parameteroptimierung. |
Sind Sie bereit, Ihren Dünnschichtabscheidungsprozess zu optimieren? Kontaktieren Sie noch heute unsere Experten für maßgeschneiderte Lösungen!