Der Schmelzverlust eines Induktionsofens bezieht sich auf die Verringerung des Metallgewichts während des Schmelzprozesses aufgrund von Faktoren wie Oxidation, Verdunstung und Schlackenbildung. Dieser Verlust wird durch mehrere Variablen beeinflusst, darunter die Schmelzrate, die Leistungskonfiguration, die Sauberkeit der Charge, das Ofendesign und die verwendeten feuerfesten Materialien. Eine saubere Beschickung, die richtige Ofenblocklänge und geeignete Tiegel wie Quarztiegel können den Schmelzverlust minimieren, indem sie die Effizienz verbessern und den Wärmeübertragungsverbrauch senken. Darüber hinaus kann eine Überhitzung aufgrund eines falschen Wasserflusses, der Abmessungen der Ofenauskleidung oder des feuerfesten Materials den Schmelzverlust verschlimmern. Das Verständnis dieser Faktoren hilft, den Ofenbetrieb zu optimieren und Materialverschwendung zu reduzieren.
Wichtige Punkte erklärt:
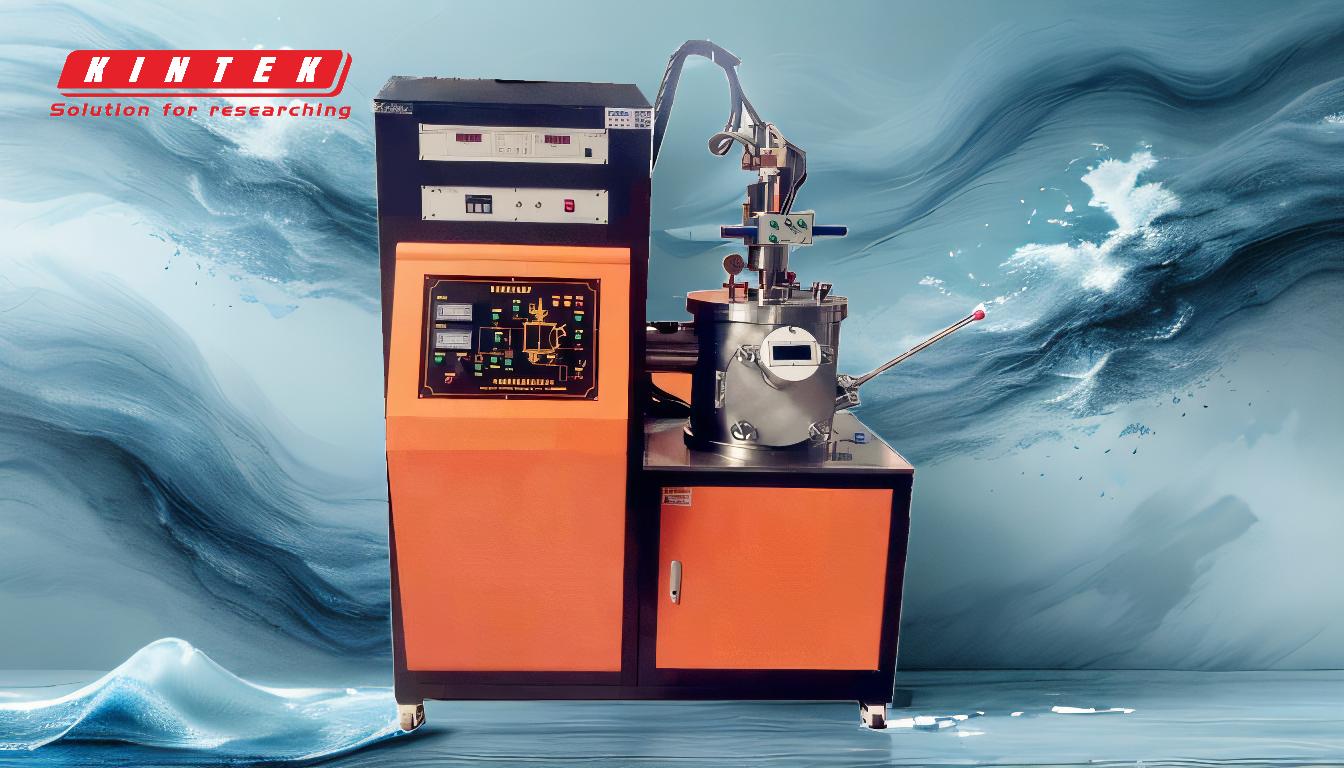
-
Definition von Schmelzverlust:
- Unter Schmelzverlust versteht man die Verringerung des Metallgewichts während des Schmelzprozesses in einem Induktionsofen. Dieser Verlust entsteht durch Oxidation, Verdunstung und Schlackenbildung, die mit dem Schmelzprozess einhergehen.
-
Faktoren, die den Schmelzverlust beeinflussen:
- Schmelzgeschwindigkeit und Leistungskonfiguration: Die Schmelzrate, berechnet als (Leistung in kW) / (Standardstromverbrauch in kWh/Tonne), wirkt sich direkt auf den Schmelzverlust aus. Konfigurationen mit höherer Leistung können die Schmelzzeit verkürzen, können jedoch die Oxidation und Verdunstung erhöhen, wenn sie nicht kontrolliert werden.
- Sauberkeit und Größe der Ladung: Eine saubere Charge mit minimalen Verunreinigungen reduziert die Schlackenbildung und Oxidation und minimiert dadurch den Schmelzverlust. Die Größe der Ladung beeinflusst auch die Gleichmäßigkeit des Schmelzens und der Wärmeverteilung.
- Feuerfeste Materialien und Tiegel: Die Art der verwendeten feuerfesten Materialien und Tiegel, wie z. B. Quarztiegel, spielt eine wichtige Rolle bei der Reduzierung von Wärmeübertragungsverlusten und der Verbesserung der Gesamteffizienz.
- Ofendesign und -auskleidung: Die richtige Dimensionierung der Ofenauskleidung und ausreichend feuerfestes Material verhindern eine Überhitzung und Schäden an der Spule, die andernfalls zu erhöhten Schmelzverlusten führen können.
-
Überhitzung und ihre Auswirkungen:
- Eine Überhitzung der Ofenschlange, die durch Einschränkungen im Wasserflussweg oder eine falsche Ofenkonstruktion verursacht wird, kann zu erhöhten Schmelzverlusten führen. Überhitzung beschleunigt die Oxidation und Verdunstung und trägt so zu einer höheren Materialverschwendung bei.
-
Berechnung der Schmelzgeschwindigkeit und -zeit:
- Die Schmelzrate wird nach folgender Formel berechnet: (Leistung in kW) / (Standardstromverbrauch in kWh/Tonne) = (Gewicht des Metalls in kg) / (1000 kg). Bei 325 kW beträgt die Schmelzrate beispielsweise 520 kg/Stunde.
- Die Schmelzzeit wird nach der Formel berechnet: (Leistung in kW * Zeit in Stunden) / (Gewicht des Metalls in kg) = (Standardstromverbrauch in kWh/Tonne * 1 Stunde) / (1000 kg). Bei einem 550-kg-Ofen mit einer Stromversorgung von 325 kW beträgt die Schmelzzeit 1,06 Stunden (64 Minuten).
-
Optimierungsstrategien:
- Saubere Ladung: Durch die Sicherstellung, dass die Ladung frei von Verunreinigungen und Verunreinigungen ist, werden Schlackenbildung und Oxidation reduziert.
- Richtiges Ofendesign: Die Einhaltung der richtigen Ofenblocklänge und Auskleidungsabmessungen verhindert eine Überhitzung und verbessert die Effizienz.
- Passende Tiegel: Die Verwendung von Tiegeln wie Quarztiegeln reduziert den Wärmeübertragungsverlust und verbessert die Schmelzeffizienz.
- Regelmäßige Wartung: Durch die regelmäßige Inspektion und Wartung der Wasserdurchflusswege, Wärmetauscher und Stromkabel wird eine Überhitzung verhindert und eine gleichbleibende Leistung gewährleistet.
Durch das Verständnis und die Berücksichtigung dieser Faktoren können Betreiber Schmelzverluste minimieren, die Ofeneffizienz verbessern und Materialverschwendung beim Betrieb von Induktionsöfen reduzieren.
Übersichtstabelle:
Schlüsselfaktor | Einfluss auf den Schmelzverlust |
---|---|
Schmelzrate und -leistung | Eine höhere Leistung verkürzt die Schmelzzeit, kann jedoch die Oxidation und Verdunstung erhöhen. |
Sauberkeit und Größe der Ladung | Saubere Chargen minimieren die Schlackenbildung und Oxidation und reduzieren so den Schmelzverlust. |
Feuerfeste Materialien | Geeignete Materialien wie Quarztiegel reduzieren den Wärmeübertragungsverlust und verbessern die Effizienz. |
Ofendesign und -auskleidung | Die richtigen Abmessungen verhindern Überhitzung und Schäden an der Spule und reduzieren so den Materialabfall. |
Überhitzung | Überhitzung beschleunigt die Oxidation und Verdunstung und erhöht den Schmelzverlust. |
Optimieren Sie den Betrieb Ihres Induktionsofens und reduzieren Sie Schmelzverluste – Kontaktieren Sie noch heute unsere Experten für maßgeschneiderte Lösungen!