Physikalische Abscheidetechniken sind Verfahren zur Herstellung dünner Filme oder Beschichtungen auf Substraten durch physikalische Übertragung von Material von einer Quelle auf das Substrat, ohne dass chemische Reaktionen erforderlich sind.Diese Verfahren beruhen auf mechanischen, elektromechanischen oder thermodynamischen Prozessen und erfordern in der Regel eine Vakuumumgebung, um sicherzustellen, dass das Material gleichmäßig und genau abgeschieden wird.Zu den gebräuchlichsten physikalischen Abscheidungsmethoden gehören das Verdampfen und das Sputtern, jeweils mit verschiedenen Untertechniken wie dem thermischen Vakuumverdampfen, dem Elektronenstrahlverdampfen und der kathodischen Lichtbogenabscheidung.Diese Verfahren werden aufgrund ihrer Präzision und ihrer Fähigkeit, qualitativ hochwertige dünne Schichten zu erzeugen, in Branchen wie Elektronik, Optik und Fertigung eingesetzt.
Die wichtigsten Punkte werden erklärt:
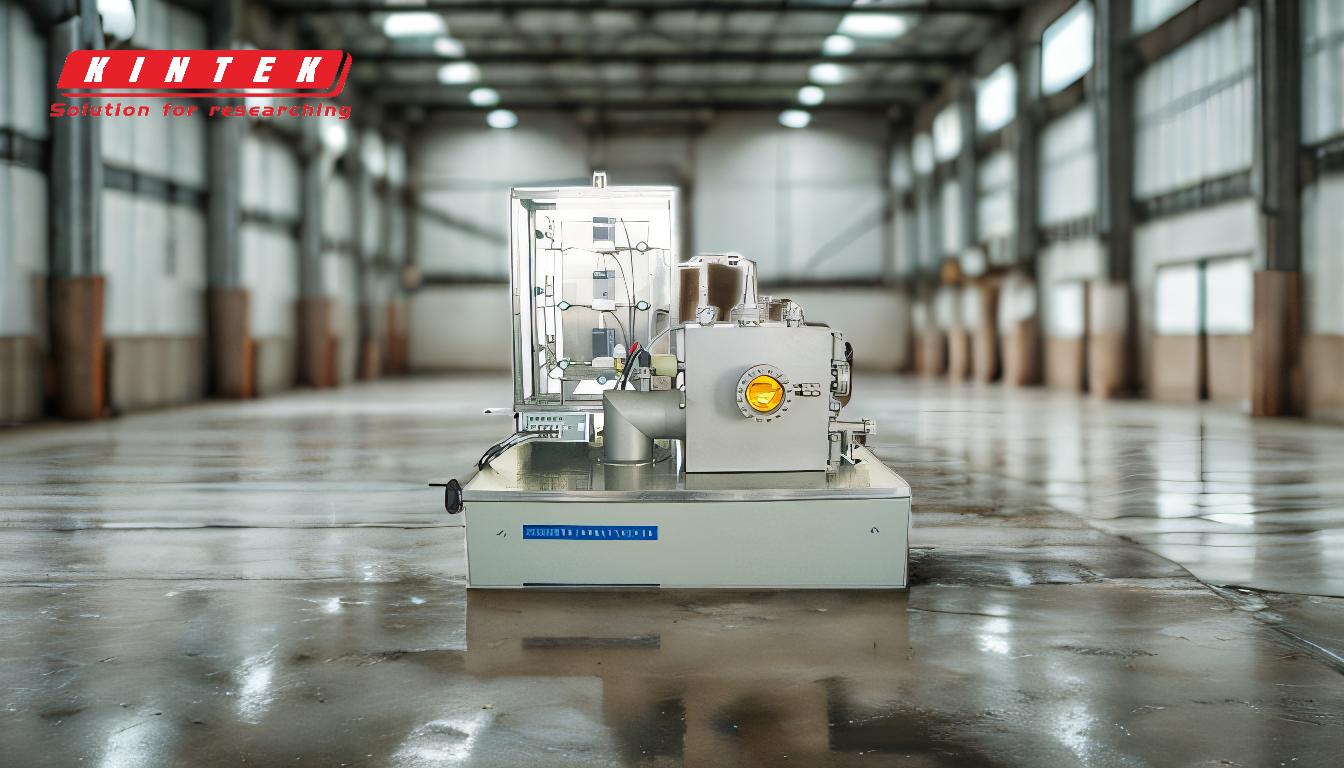
-
Definition der physikalischen Abscheidungstechniken:
- Bei physikalischen Abscheidungsverfahren wird das Material mit Hilfe mechanischer, elektromechanischer oder thermodynamischer Methoden von einer Quelle auf ein Substrat übertragen.
- Im Gegensatz zur chemischen Abscheidung beruht die physikalische Abscheidung nicht auf chemischen Reaktionen zur Bildung der dünnen Schicht.
- Diese Verfahren werden in der Regel in einer Vakuumumgebung durchgeführt, um sicherzustellen, dass das Material gleichmäßig und ohne Verunreinigungen abgeschieden wird.
-
Schlüsselkomponenten der physikalischen Abscheidung:
- Vakuumkammer:Wesentlich für die Schaffung einer Niederdruckumgebung, in der sich die Materialpartikel frei bewegen und gleichmäßig auf dem Substrat absetzen können.
- Ausgangsmaterial:Das abzuscheidende Material, das sich anfangs oft in festem oder flüssigem Zustand befindet.
- Substrat:Die Oberfläche, auf der die dünne Schicht abgeschieden wird. Sie ist in der Regel kühler als das Ausgangsmaterial, um die Abscheidung zu erleichtern.
-
Gängige physikalische Abscheidungsmethoden:
-
Verdunstung:
- Hierbei wird das Ausgangsmaterial erhitzt, bis es verdampft oder in einen gasförmigen Zustand übergeht.
- Das gasförmige Material kondensiert dann auf dem kühleren Substrat und bildet einen dünnen Film.
-
Zu den Untertechniken gehören:
- Thermische Vakuumverdampfung:Verdampfen des Materials unter Verwendung von Wärme im Vakuum.
- Elektronenstrahl-Verdampfung:Erhitzt und verdampft das Material mit Hilfe eines Elektronenstrahls.
- Laserstrahl-Verdampfung:Verwendet einen Laser, um das Material abzutragen und zu verdampfen.
- Lichtbogenverdampfung:Das Material wird mit einem Lichtbogen verdampft.
- Molekularstrahlepitaxie (MBE):Eine hochgradig kontrollierte Form der Verdampfung, die für das Wachstum kristalliner Schichten verwendet wird.
- Ionenplattierung Verdampfung:Kombiniert Verdampfung mit Ionenbeschuss zur Verbesserung der Schichthaftung und -dichte.
-
Sputtern:
- Dabei wird das Ausgangsmaterial (Target) mit hochenergetischen Ionen oder Plasma beschossen, wodurch Atome aus dem Target herausgeschleudert werden.
- Diese ausgestoßenen Atome lagern sich dann auf dem Substrat ab und bilden einen dünnen Film.
- Das Sputtern wird häufig bei der Herstellung von Halbleitern und optischen Beschichtungen eingesetzt.
-
Verdunstung:
-
Vorteile der physikalischen Abscheidetechniken:
- Hohe Präzision:Ermöglicht die Abscheidung sehr dünner und gleichmäßiger Schichten, oft im Nanometerbereich.
- Material Vielseitigkeit:Kann für eine Vielzahl von Materialien verwendet werden, darunter Metalle, Keramiken und Halbleiter.
- Kontrollierte Umgebung:Die Vakuumumgebung minimiert Verunreinigungen und ermöglicht eine präzise Kontrolle der Abscheidungsparameter.
- Haftung und Dichte:Mit Techniken wie Ionenplattieren und Sputtern lassen sich Schichten mit hervorragender Haftung und Dichte herstellen.
-
Anwendungen der physikalischen Abscheidetechniken:
- Elektronik:Für die Abscheidung dünner Schichten bei der Herstellung von Halbleitern, integrierten Schaltkreisen und mikroelektromechanischen Systemen (MEMS).
- Optik:Wird zur Herstellung von Antireflexionsbeschichtungen, Spiegeln und optischen Filtern verwendet.
- Herstellung:Angewandt bei der Herstellung von harten Beschichtungen für Werkzeuge, dekorativen Beschichtungen und korrosionsbeständigen Schichten.
-
Vergleich mit chemischen Abscheidungsverfahren:
- Physikalische Abscheidung (PVD):Beruht auf physikalischen Prozessen und beinhaltet keine chemischen Reaktionen.Es wird in der Regel im Vakuum durchgeführt und eignet sich für eine breite Palette von Materialien.
- Chemische Abscheidung (CVD):Chemische Reaktionen zur Bildung der dünnen Schicht.Es kann bei Atmosphärendruck oder im Vakuum durchgeführt werden und wird häufig für die Abscheidung komplexer Materialien wie Oxide und Nitride verwendet.
-
Beispiele für physikalische Abscheidetechniken:
- Arc-PVD (kathodische Lichtbogenabscheidung):Mit Hilfe eines Lichtbogens wird Material von einer Kathode verdampft, das sich dann auf dem Substrat ablagert.
- Gepulste Laserabscheidung (PLD):Mit einem Hochleistungslaser wird Material von einem Target abgetragen, das sich dann auf dem Substrat ablagert.
- Sputtern:Dazu gehören Techniken wie das Magnetron-Sputtern, bei dem ein Magnetfeld zur Verbesserung der Effizienz des Sputterprozesses eingesetzt wird.
- Thermische Verdampfung:Eine der einfachsten und am weitesten verbreiteten physikalischen Abscheidungsmethoden, insbesondere für Metalle und einfache Verbindungen.
Zusammenfassend lässt sich sagen, dass physikalische Abscheidungsverfahren für die Herstellung hochwertiger dünner Schichten in einer Vielzahl von Branchen unerlässlich sind.Sie bieten eine präzise Kontrolle über den Abscheidungsprozess und sind in der Lage, Schichten mit hervorragenden Eigenschaften zu erzeugen, was sie für viele Anwendungen zur bevorzugten Wahl macht.
Zusammenfassende Tabelle:
Aspekt | Einzelheiten |
---|---|
Definition | Techniken, bei denen Stoffe physikalisch ohne chemische Reaktionen übertragen werden. |
Wichtige Komponenten | Vakuumkammer, Ausgangsmaterial und Substrat. |
Gängige Methoden | Verdampfung (thermisch, Elektronenstrahl, Laser) und Sputtern. |
Vorteile | Hohe Präzision, Vielseitigkeit der Materialien, kontrollierte Umgebung, starke Haftung. |
Anwendungen | Elektronik (Halbleiter), Optik (Spiegel), Fertigung (Beschichtungen). |
Vergleich mit CVD | PVD:Keine chemischen Reaktionen, vakuumbasiert.CVD:Chemische Reaktionen, atmosphärisch oder im Vakuum. |
Sind Sie an hochwertigen dünnen Schichten für Ihre Anwendungen interessiert? Kontaktieren Sie noch heute unsere Experten um mehr zu erfahren!