Beim Formen einer Form, insbesondere beim Blasformen, wird der Kunststoff mit Hilfe einer Form in die gewünschte Form gebracht.Dieser Prozess umfasst in der Regel das Schmelzen des Kunststoffs zu einem Vorformling, das Einspannen in eine Form, das Aufblasen mit Luft, um ihn an die Form anzupassen, das Abkühlen des Materials und schließlich das Ausstoßen des fertigen Produkts.Die drei gängigen Blasformverfahren sind Extrusions-, Spritzguss- und Streckblasformen, wobei jedes Verfahren seine eigenen spezifischen Schritte und Anwendungen hat.
Die wichtigsten Punkte werden erklärt:
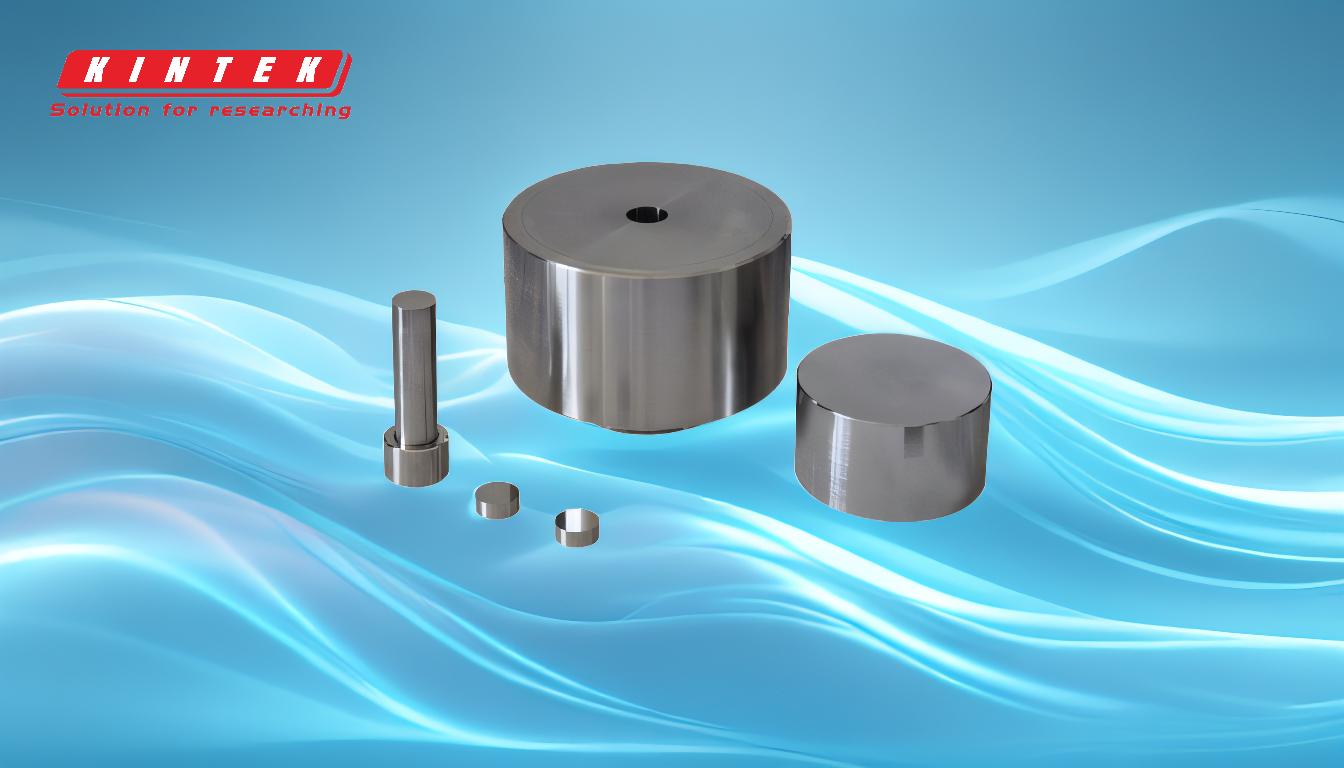
-
Schmelzen von Kunststoff zu einer Vorform:
- Das Verfahren beginnt mit dem Schmelzen von Kunststoffgranulat oder Harz, um eine rohrförmige Vorform zu bilden.Dieser Vorformling ist die Ausgangsform, die weiter geformt wird.
- Die Art des verwendeten Kunststoffs kann je nach den gewünschten Eigenschaften des Endprodukts, wie Flexibilität, Festigkeit oder Transparenz, variieren.
-
Einspannen des Vorformlings in eine Form:
- Die Vorform wird dann in eine Form eingespannt, die genau nach den Spezifikationen des Endprodukts gestaltet ist.
- Die Form ist in der Regel aus Metall und kann für die Herstellung einer Vielzahl von Formen und Größen angepasst werden.
-
Aufblasen der Vorform mit Luft:
- Sobald die Vorform sicher eingespannt ist, wird Luft hineingepumpt, um den Kunststoff gegen die Wände der Form zu drücken.
- Dieser Schritt stellt sicher, dass der Kunststoff die genaue Form der Form annimmt, einschließlich aller komplizierten Details oder Strukturen.
-
Abkühlen des Formteils:
- Nachdem der Kunststoff geformt wurde, wird er in der Form abgekühlt.Die Abkühlung ist von entscheidender Bedeutung, da sie den Kunststoff verfestigt und sicherstellt, dass er seine neue Form beibehält.
- Die Abkühlzeit kann je nach Dicke des Kunststoffs und der Art des verwendeten Kunststoffs variieren.
-
Ausstoßen des fertigen Produkts:
- Sobald der Kunststoff abgekühlt und verfestigt ist, wird die Form geöffnet und das fertige Produkt ausgeworfen.
- Anschließend wird das Produkt auf seine Qualität geprüft und gegebenenfalls nachbearbeitet, z. B. durch Abschneiden von überschüssigem Material oder Hinzufügen zusätzlicher Komponenten.
-
Übliche Blasformverfahren:
- Extrusionsblasformen:Bei diesem Verfahren wird ein Schlauch aus geschmolzenem Kunststoff (Vorformling) in eine Form extrudiert und anschließend aufgeblasen.Dieses Verfahren wird häufig zur Herstellung von Hohlkörpern wie Flaschen und Behältern verwendet.
- Spritzblasformen:Dieses Verfahren beginnt mit dem Einspritzen von geschmolzenem Kunststoff in eine Vorformwerkzeug.Der Vorformling wird dann in eine Blasform übertragen, wo er aufgeblasen wird.Dieses Verfahren wird häufig für kleine, präzise Gegenstände wie medizinische Flaschen verwendet.
- Streckblasformen:Bei dieser Technik wird der Vorformling vor dem Einblasen in die Form sowohl in Längsrichtung als auch in radialer Richtung gestreckt.Es wird in der Regel für die Herstellung von hochfesten, leichten Behältern, wie PET-Flaschen, verwendet.
Durch die Einhaltung dieser Schritte können die Hersteller eine Vielzahl von Kunststoffprodukten mit gleichbleibender Qualität und Präzision herstellen.Jedes Blasformverfahren hat seine eigenen Vorteile und wird je nach den spezifischen Anforderungen des herzustellenden Produkts ausgewählt.
Zusammenfassende Tabelle:
Schritt | Beschreibung |
---|---|
Schmelzen von Kunststoff zu einem Vorformling | Kunststoffgranulat wird zu einem rohrförmigen Vorformling geschmolzen, der auf die Eigenschaften des Endprodukts zugeschnitten ist. |
Einspannen in eine Form | Die Vorform wird in eine speziell für die endgültige Form entwickelte Metallform eingespannt. |
Aufblasen mit Luft | Luft wird in den Vorformling gepumpt, um ihn für eine präzise Formgebung gegen die Formwände zu drücken. |
Abkühlen des Formteils | Der Kunststoff kühlt in der Form ab, um sich zu verfestigen und seine Form beizubehalten. |
Auswerfen des fertigen Produkts | Das gekühlte Produkt wird ausgeworfen, geprüft und je nach Bedarf fertiggestellt. |
Gängige Verfahren | Extrusions-, Spritzguss- und Streckblasformen, die jeweils für spezifische Produktanforderungen geeignet sind. |
Sind Sie bereit, Ihren Kunststoffspritzgussprozess zu optimieren? Kontaktieren Sie noch heute unsere Experten für maßgeschneiderte Lösungen!