Die physikalische Gasphasenabscheidung (PVD) ist ein hochentwickeltes Verfahren zur Abscheidung dünner Materialschichten auf ein Substrat in einer Vakuumumgebung.Das Verfahren umfasst mehrere wichtige Schritte: die Vergasung eines festen Vorläufermaterials, den Transport der vergasten Atome in eine Reaktionskammer und die Abscheidung dieser Atome auf dem Substrat zur Bildung einer dünnen Schicht.Dieses Verfahren wird in verschiedenen Industriezweigen zur Herstellung von Hochleistungsbeschichtungen mit hervorragender Haftung, Gleichmäßigkeit und Haltbarkeit eingesetzt.
Die wichtigsten Punkte werden erklärt:
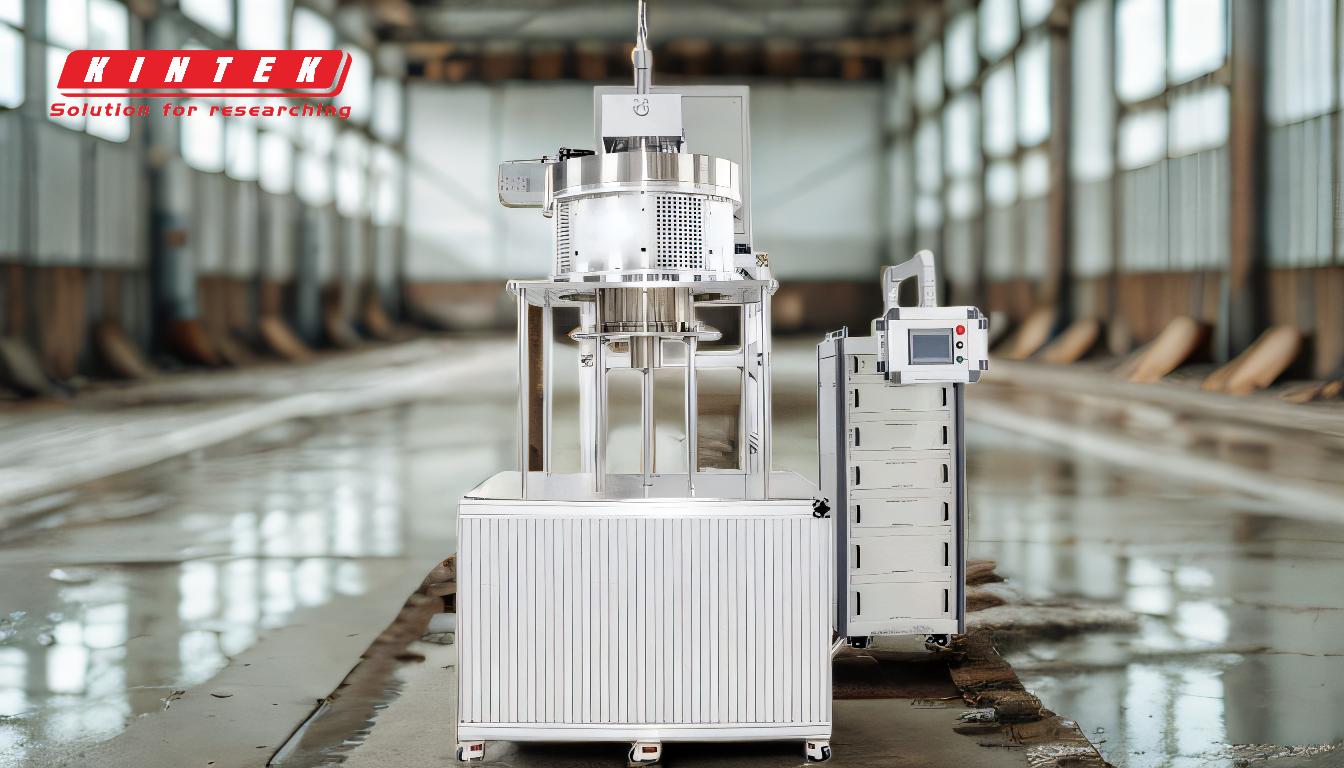
-
Vergasung des Vorläufermaterials:
- Das PVD-Verfahren beginnt mit der Vergasung eines festen Vorläufermaterials.Dies geschieht in der Regel mit Hilfe von Hochleistungsstrom oder einem Laser.Durch den Energieeintrag verdampft das feste Material und bildet eine Wolke aus Gasatomen.Dieser Schritt ist entscheidend, da er das Material für den Transport zum Substrat vorbereitet.
-
Transport von vergasten Atomen:
- Nach der Vergasung des Vorläufermaterials werden die Atome in eine Reaktionskammer transportiert, in der sich das Substrat befindet.Dieser Transport erfolgt in einer Vakuumumgebung, die sicherstellt, dass sich die Atome frei bewegen können, ohne von Luftmolekülen gestört zu werden.Das Vakuum trägt auch dazu bei, die Reinheit des abgeschiedenen Materials zu erhalten.
-
Abscheidung auf dem Substrat:
- In der Reaktionskammer haften die vergasten Atome an der Oberfläche des Substrats.Dieser Abscheidungsprozess wird kontrolliert, um sicherzustellen, dass die Atome einen gleichmäßigen dünnen Film bilden.Das Substrat wird häufig erhitzt, um eine bessere Haftung zu erreichen und die Qualität der abgeschiedenen Schicht zu verbessern.Das Ergebnis ist eine dünne, dauerhafte Beschichtung, die die Eigenschaften des Substrats verbessern kann, z. B. Härte, Korrosionsbeständigkeit oder elektrische Leitfähigkeit.
-
Bildung von Plasma:
- Bei einigen PVD-Verfahren wird ein Plasma aus einem Gas erzeugt, in der Regel mit Hilfe eines induktiv gekoppelten Plasmas (ICP).Das Gas wird ionisiert, und hochenergetische Elektronen stoßen mit den Gasmolekülen zusammen, wodurch diese in Atome dissoziieren.Diese Atome werden dann auf dem Substrat abgeschieden, wo sie kondensieren und einen dünnen Film bilden.Dieser Schritt ist besonders wichtig bei Verfahren, bei denen reaktive Gase zur Bildung von Verbindungen mit dem verdampften Material verwendet werden.
-
Einführung reaktiver gasförmiger Spezies:
- Bei bestimmten PVD-Verfahren wird eine reaktive Gasspezies in die Reaktionskammer eingeleitet.Dieses Gas reagiert mit dem verdampften Material und bildet eine Verbindung, die dann auf dem Substrat abgeschieden wird.Mit dieser Methode lassen sich Beschichtungen mit bestimmten chemischen Zusammensetzungen und Eigenschaften herstellen, z. B. Nitride oder Oxide.
-
Glühen oder Wärmebehandlung:
- Nach dem Abscheidungsprozess kann die dünne Schicht einer Glühung oder Wärmebehandlung unterzogen werden.Dieser Schritt trägt dazu bei, die mechanischen Eigenschaften der Schicht, wie Härte und Haftung, zu verbessern, indem die Atome sich zu einer stabileren kristallinen Struktur umordnen können.Der Wärmebehandlungsprozess wird sorgfältig kontrolliert, um eine Beschädigung des Substrats oder der abgeschiedenen Schicht zu vermeiden.
-
Analyse und Prozessmodifikation:
- Der letzte Schritt des PVD-Verfahrens besteht in der Analyse der Eigenschaften der abgeschiedenen Schicht.Diese Analyse kann Messungen der Dicke, Gleichmäßigkeit, Haftung und anderer relevanter Eigenschaften umfassen.Auf der Grundlage der Ergebnisse kann das Abscheideverfahren modifiziert werden, um die Qualität der Schicht zu verbessern oder bestimmte Leistungsmerkmale zu erreichen.
Zusammenfassend lässt sich sagen, dass der PVD-Beschichtungsprozess ein mehrstufiges Verfahren ist, das die Vergasung eines Vorläufermaterials, den Transport der vergasten Atome zu einem Substrat und die Abscheidung dieser Atome zur Bildung einer dünnen Schicht umfasst.Das Verfahren lässt sich sehr gut steuern und kann auf die Herstellung von Beschichtungen mit spezifischen Eigenschaften zugeschnitten werden, was es zu einer wertvollen Technik für verschiedene industrielle Anwendungen macht.Weitere Informationen über verwandte Verfahren finden Sie auf der Seite System der chemischen Gasphasenabscheidung .
Zusammenfassende Tabelle :
Schritt | Beschreibung |
---|---|
1.Vergasung | Festes Ausgangsmaterial wird mit Hilfe von Hochleistungsstrom oder einem Laser verdampft. |
2.Transport | Die vergasten Atome werden in einer Vakuumumgebung in die Reaktionskammer transportiert. |
3.Abscheidung | Die Atome haften auf dem Substrat und bilden einen gleichmäßigen dünnen Film. |
4.Plasmabildung | Plasma wird aus Gas erzeugt, das die Atome für die Abscheidung ionisiert. |
5.Reaktive gasförmige Spezies | Reaktive Gase bilden Verbindungen mit verdampftem Material für bestimmte Beschichtungen. |
6.Glühen/Wärmebehandlung | Verbessert Folieneigenschaften wie Härte und Haftung durch kontrollierte Erwärmung. |
7.Analyse & Modifizierung | Die Filmeigenschaften werden analysiert, und der Prozess wird für optimale Ergebnisse verfeinert. |
Entdecken Sie, wie die PVD-Beschichtung Ihre Materialien verbessern kann. Kontaktieren Sie noch heute unsere Experten für maßgeschneiderte Lösungen!