Das Spark-Plasma-Sintern (SPS) ist ein fortschrittliches pulvermetallurgisches Verfahren, das zur Verfestigung von Pulverwerkstoffen zu dichten, festen Strukturen eingesetzt wird.Es kombiniert gepulsten Gleichstrom (DC) und axialen Druck, um Materialien bei hohen Temperaturen, die oft bis zu 10.000°C erreichen, schnell zu erhitzen und zu sintern.Dieses Verfahren erzeugt ein lokales Plasma und hohe Temperaturen zwischen den Partikeln, was die Oberflächendiffusion, die Partikelbindung und die schnelle Verdichtung erleichtert.SPS ist bekannt für seine schnellen Heizraten, die gleichmäßige Erwärmung und die Fähigkeit, eine nahezu theoretische Dichte (über 99 %) in Materialien zu erreichen.Trotz des Namens deuten Forschungsergebnisse darauf hin, dass das Plasma nicht der primäre Mechanismus ist, was zu alternativen Namen wie Field Assisted Sintering Technique (FAST) oder Direct Current Sintering (DCS) führt.SPS wird häufig für Keramiken, Metalle und Verbundwerkstoffe eingesetzt, da es im Vergleich zu herkömmlichen Verfahren effizient ist und Materialien bei niedrigeren Temperaturen und in kürzerer Zeit sintert.
Die wichtigsten Punkte werden erklärt:
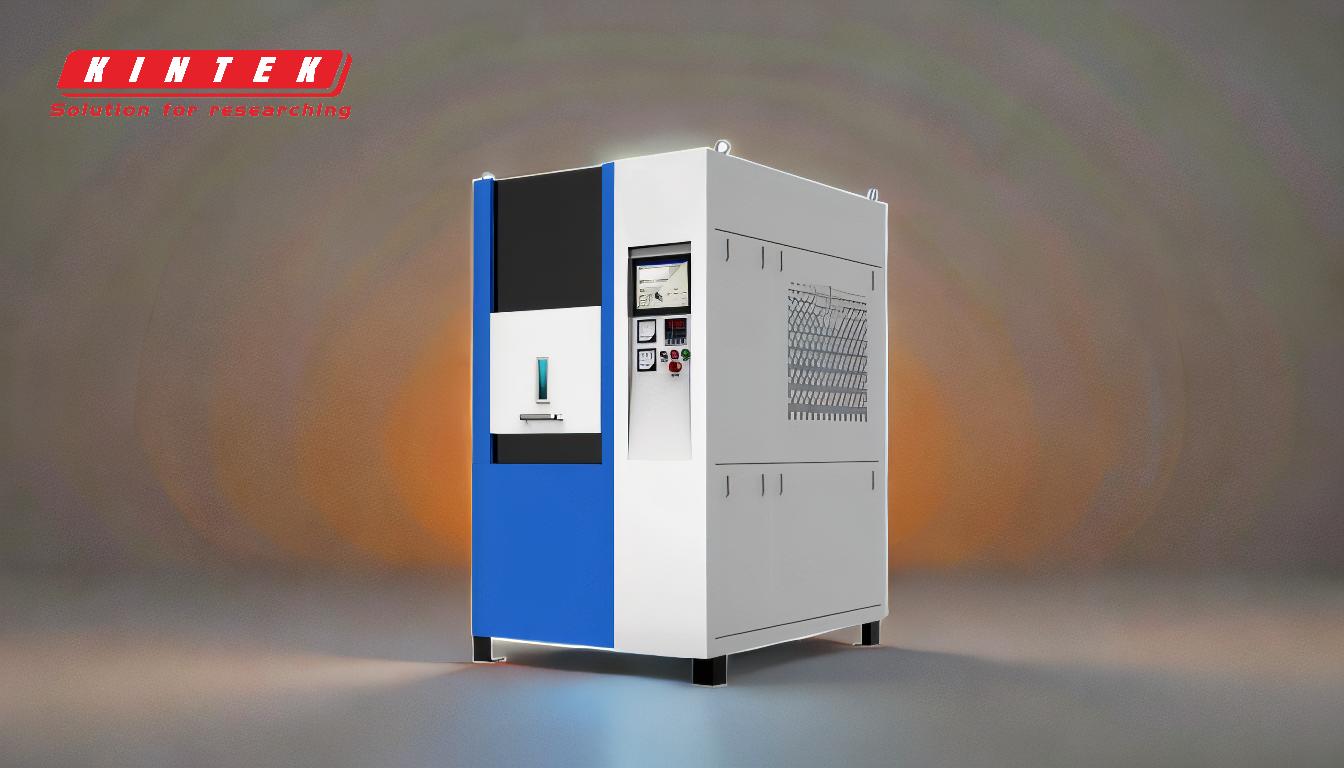
-
Definition und Zweck von SPS:
- Das Spark-Plasma-Sintern (SPS) ist ein Verfahren zur Pulverkonsolidierung, bei dem gepulster Gleichstrom und axialer Druck eingesetzt werden, um Pulvermaterialien schnell zu dichten, festen Strukturen zu sintern.
- Es ist besonders nützlich, um Materialien mit hoher Dichte und minimaler Porosität zu erhalten, die oft eine Dichte von 99 % überschreiten.
-
Mechanismus der SPS:
- Gepulster Gleichstrom und Funkenentladung:Es wird ein gepulster Hochenergiestrom angelegt, der elektrische Funkenentladungen zwischen Partikeln erzeugt.Dies erzeugt ein lokales Plasma und extrem hohe Temperaturen (bis zu 10.000 °C).
- Partikelbindung:Die hohen Temperaturen führen dazu, dass die Partikeloberflächen schmelzen und verschmelzen, wodurch sich zwischen den Partikeln "Hälse" bilden.Im Laufe der Zeit wachsen diese Verengungen und erhöhen die Gesamtdichte des Materials.
- Entfernung von Verunreinigungen:Die intensive Hitze kann Oberflächenverunreinigungen oxidieren oder verdampfen und sorgt so für eine saubere Partikelbindung.
-
Die wichtigsten Vorteile von SPS:
- Schnelles Heizen und Kühlen Tarife:SPS ermöglicht ein schnelles Aufheizen und Abkühlen, wodurch die Verarbeitungszeit im Vergleich zu herkömmlichen Sinterverfahren erheblich verkürzt wird.
- Niedrigere Sintertemperaturen:Bei diesem Verfahren erfolgt die Verdichtung bei Temperaturen, die mehrere hundert Grad niedriger sind als beim herkömmlichen Sintern, wodurch die Materialeigenschaften erhalten bleiben.
- Gleichmäßige Erwärmung:Die Kombination aus interner und externer Beheizung sorgt für eine gleichmäßige Temperaturverteilung, reduziert die thermische Belastung und verbessert die Materialkonsistenz.
-
Ausrüstung und Prozessdetails:
- Dirigieren Die:In der Regel wird eine Graphitmatrize verwendet, um Druck auszuüben und den gepulsten Gleichstrom zu leiten.Die Matrize dient sowohl als Wärmequelle als auch als Druckapplikator.
- Gerät zur Leistungssteuerung:Ein spezielles Gerät legt eine EIN-AUS-Gleichstromimpulsspannung an die Pulverprobe an, erzeugt ein Entladungsplasma und nutzt die Joule-Erwärmung für eine schnelle Verdichtung.
- Druck Anwendung:Gleichzeitig mit dem elektrischen Strom wird axialer Druck ausgeübt, um die Partikelbindung und die Verdichtung zu verbessern.
-
Anwendungen von SPS:
- Keramiken und Metalle:SPS wird häufig zum Sintern von Keramiken, Metallen und Verbundwerkstoffen eingesetzt, um Hochleistungswerkstoffe mit hervorragenden mechanischen, thermischen und elektrischen Eigenschaften herzustellen.
- Nanowerkstoffe:Das Verfahren eignet sich besonders gut für die Verfestigung von Nanomaterialien, da es das Kornwachstum verhindert und die Nanostrukturen erhält.
-
Missverständnisse und alternative Bezeichnungen:
- Plasma Missverständnis:Trotz des Namens deuten Forschungsergebnisse darauf hin, dass Plasma nicht der primäre Mechanismus bei SPS ist.Stattdessen beruht der Prozess auf elektrischer Entladung und Joule-Erwärmung.
- Alternative Bezeichnungen:Aufgrund dieses Missverständnisses wird SPS auch als Field Assisted Sintering Technique (FAST), Electric Field Assisted Sintering (EFAS) oder Direct Current Sintering (DCS) bezeichnet.
-
Vergleich mit konventionellem Sintern:
- Zeit-Effizienz:SPS verkürzt die Sinterzeit erheblich, so dass der Prozess oft in Minuten statt in Stunden abgeschlossen ist.
- Temperatur-Effizienz:Niedrigere Sintertemperaturen bei SPS tragen dazu bei, die Materialeigenschaften zu erhalten und den Energieverbrauch zu senken.
- Dichte und Qualität:SPS erzielt im Vergleich zu herkömmlichen Sinterverfahren höhere Dichten und eine bessere Materialqualität.
-
Herausforderungen und Überlegungen:
- Material Leitfähigkeit:Materialien mit geringer elektrischer Leitfähigkeit erfordern möglicherweise leitende Zusätze oder alternative Heizmethoden.
- Ausrüstung Kosten:Die spezielle Ausrüstung für SPS kann teuer sein, was sie für einige Anwendungen weniger zugänglich macht.
- Prozess-Optimierung:Um optimale Ergebnisse zu erzielen, ist eine sorgfältige Kontrolle von Parametern wie Strom, Druck und Temperatur erforderlich.
Durch das Verständnis dieser Schlüsselpunkte können Käufer von Anlagen und Verbrauchsmaterialien die Eignung von SPS für ihre spezifischen Materialverarbeitungsanforderungen besser beurteilen und fundierte Entscheidungen über die Einführung dieser fortschrittlichen Sintertechnik treffen.
Zusammenfassende Tabelle:
Hauptaspekt | Einzelheiten |
---|---|
Definition | Fortgeschrittenes pulvermetallurgisches Verfahren mit gepulstem Gleichstrom und axialem Druck. |
Mechanismus | Erzeugt ein lokalisiertes Plasma und hohe Temperaturen für die Partikelbindung. |
Vorteile | Schnelle Erwärmung, niedrigere Sintertemperaturen und gleichmäßige Erwärmung. |
Anwendungen | Keramiken, Metalle, Verbundwerkstoffe und Nanomaterialien. |
Alternative Bezeichnungen | Feldunterstützte Sintertechnik (FAST), Gleichstromsintern (DCS). |
Vergleich mit konventionellen Verfahren | Schneller, niedrigere Temperaturen, höhere Dichte und bessere Qualität. |
Sind Sie bereit, Ihre Materialverarbeitung zu verbessern? Kontaktieren Sie uns noch heute um mehr über Spark Plasma Sintering zu erfahren!