Der Abstand des Zielsubstrats beim Sputtern ist ein kritischer Parameter, der die Qualität, Gleichmäßigkeit und Dicke der abgeschiedenen Dünnschicht direkt beeinflusst.Dieser Abstand muss sorgfältig kontrolliert werden, um optimale Abscheidungsbedingungen zu gewährleisten, da er die kinetische Energie der gesputterten Partikel, ihre Ausrichtung und die Gesamtabscheidungsrate beeinflusst.Der ideale Abstand zum Zielsubstrat hängt von Faktoren wie der Sputtermethode, dem Zielmaterial, dem Substratmaterial, dem Kammerdruck und der Sputterleistung ab.Im Allgemeinen wird ein Abstand von 5 bis 15 cm verwendet, doch können spezifische Anwendungen Anpassungen erfordern, um die gewünschten Schichteigenschaften zu erreichen.Der richtige Abstand gewährleistet eine gleichmäßige Abdeckung, minimiert Fehler und verbessert die Gesamtqualität der Beschichtung.
Die wichtigsten Punkte erklärt:
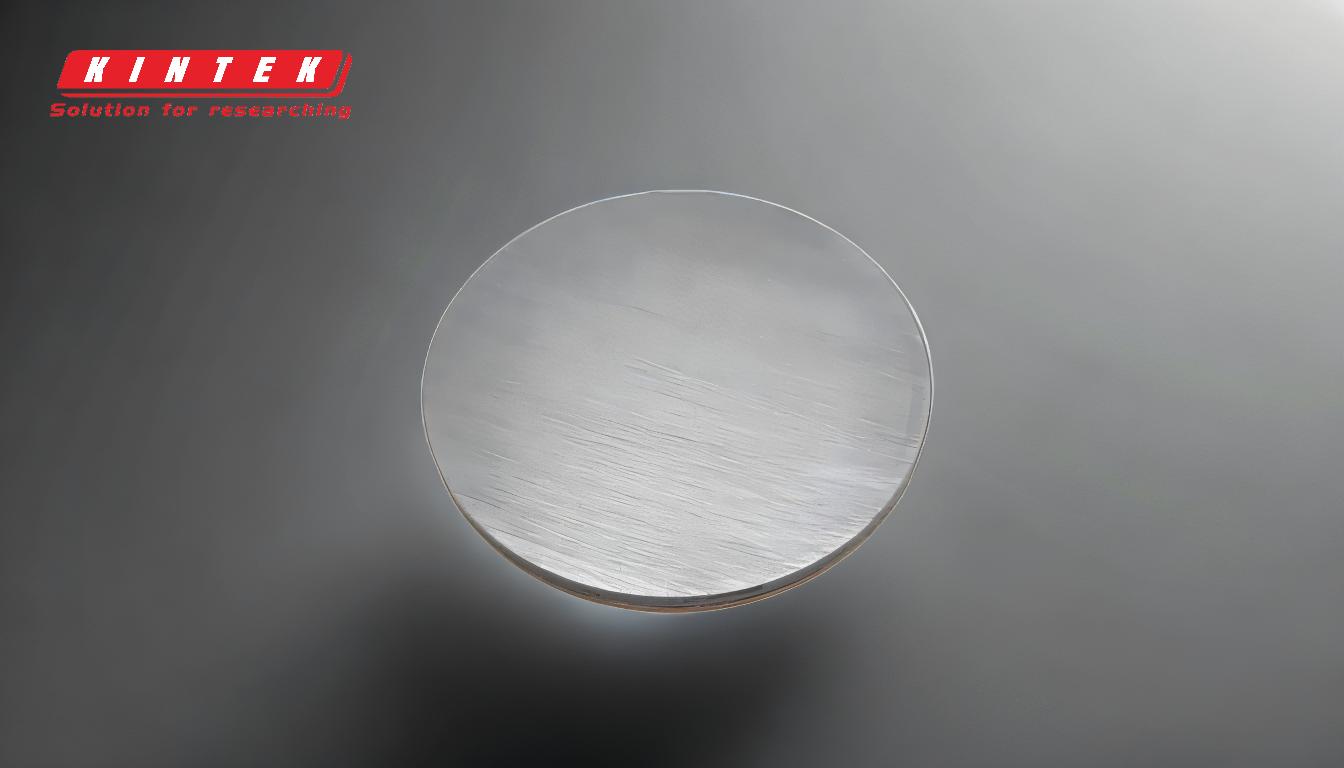
-
Bedeutung des Zielsubstrats Abstand:
- Der Abstand zwischen dem Target und dem Substrat ist entscheidend für die gleichmäßige Abscheidung dünner Schichten.
- Er wirkt sich auf die kinetische Energie und die Ausrichtung der gesputterten Partikel aus, was wiederum die Dicke, Gleichmäßigkeit und Qualität der Schicht beeinflusst.
- Der richtige Abstand sorgt für gleichmäßige Abscheidungsraten und minimiert Defekte wie ungleichmäßige Beschichtung oder Hohlräume.
-
Typischer Bereich für den Zielsubstratabstand:
- Ein üblicher Bereich für den Abstand des Zielsubstrats beim Sputtern ist 5 bis 15 cm .
- Dieser Bereich ist für die meisten Standard-Sputteranwendungen geeignet und bietet ein ausgewogenes Verhältnis zwischen Abscheiderate und Schichtqualität.
- Der genaue Abstand muss jedoch unter Umständen an spezifische experimentelle oder industrielle Anforderungen angepasst werden.
-
Faktoren, die den optimalen Abstand beeinflussen:
- Sputtering-Verfahren:Verschiedene Sputtertechniken (z. B. DC, RF, Magnetron) können aufgrund von Unterschieden in der Ionenenergie und den Abscheidungsmechanismen unterschiedliche Abstände erfordern.
- Target- und Substratmaterialien:Die Masse und die Eigenschaften der Target- und Substratmaterialien beeinflussen die Sputterausbeute und das Partikelverhalten.
- Kammerdruck:Höhere Drücke können die mittlere freie Weglänge der Partikel verringern, so dass kürzere Abstände erforderlich sind, um die Abscheidungseffizienz zu erhalten.
- Sputtering Leistung:Höhere Leistungen können die Energie der gesputterten Partikel erhöhen, was möglicherweise größere Abstände zum Zielsubstrat ermöglicht, ohne die Schichtqualität zu beeinträchtigen.
-
Auswirkungen auf Abscheiderate und Schichtqualität:
- Ablagerungsrate:Ein kürzerer Abstand erhöht im Allgemeinen die Abscheiderate aufgrund geringerer Partikelstreuung und eines höheren Partikelflusses auf dem Substrat.
- Qualität des Films:Ein größerer Abstand kann die Gleichmäßigkeit des Films verbessern, da sich die Partikel gleichmäßiger über das Substrat verteilen, kann aber auch die Abscheidungseffizienz verringern.
-
Praktische Überlegungen zur Einrichtung der Anlage:
- Einheitlichkeit:Um eine gleichmäßige Schichtdicke zu erreichen, ist es wichtig, dass das Substrat parallel zur Zielfläche positioniert ist.
- Einstellbarkeit:Sputtersysteme sollten eine präzise Einstellung des Targetsubstratabstands ermöglichen, um unterschiedlichen Materialien und Prozessbedingungen gerecht zu werden.
- Überwachung:Die Echtzeit-Überwachung der Schichtdicke und -qualität hilft bei der Optimierung des Abstands während des Sputtering-Prozesses.
-
Anwendungsspezifische Anpassungen:
- Hochpräzise Beschichtungen:Für Anwendungen, die extrem gleichmäßige oder fehlerfreie Beschichtungen erfordern, muss der Abstand zum Zielsubstrat möglicherweise minimiert und sorgfältig kontrolliert werden.
- Großflächige Abscheidung:In industriellen Umgebungen können größere Abstände verwendet werden, um größere Substrate oder mehrere Substrate gleichzeitig zu beschichten, was jedoch eine Anpassung anderer Parameter (z. B. Leistung, Druck) erfordern kann, um die Qualität zu erhalten.
-
Experimentelle Optimierung:
- Der optimale Zielsubstratabstand wird für bestimmte Anwendungen oft experimentell ermittelt.
- Faktoren wie die gewünschte Schichtdicke, die Substratgröße und die Materialeigenschaften sollten den Optimierungsprozess leiten.
Zusammenfassend lässt sich sagen, dass der Abstand des Zielsubstrats beim Sputtern ein Schlüsselparameter ist, der sorgfältig kontrolliert werden muss, um eine hochwertige Dünnschichtabscheidung zu erreichen.Während im Allgemeinen ein Bereich von 5 bis 15 cm verwendet wird, sollte der genaue Abstand auf das jeweilige Sputterverfahren, die Materialien und die Anwendungsanforderungen abgestimmt werden.Ein angemessener Abstand gewährleistet eine gleichmäßige Abscheidung, minimiert Defekte und verbessert die Gesamtleistung des beschichteten Substrats.
Zusammenfassende Tabelle:
Schlüsselfaktor | Auswirkung auf das Zielsubstrat Abstand |
---|---|
Typische Reichweite | 5 bis 15 cm |
Sputtering-Methode | Gleichstrom-, Hochfrequenz- oder Magnetronsputtern kann eine Anpassung des Abstands für optimale Ionenenergie und Ausbeute erfordern. |
Target/Substrat-Materialien | Materialmasse und -eigenschaften beeinflussen die Sputterausbeute und das Partikelverhalten. |
Kammerdruck | Ein höherer Druck kann kürzere Abstände erfordern, um die Abscheidungseffizienz zu erhalten. |
Zerstäubungsleistung | Höhere Leistung ermöglicht größere Abstände ohne Beeinträchtigung der Schichtqualität. |
Abscheidungsrate | Kürzere Abstände erhöhen die Ablagerungsrate; längere Abstände verbessern die Gleichmäßigkeit. |
Anwendungsspezifische Erfordernisse | Hochpräzise Beschichtungen oder großflächige Abscheidungen können maßgeschneiderte Abstände erfordern. |
Benötigen Sie Hilfe bei der Optimierung Ihres Sputtering-Prozesses? Kontaktieren Sie noch heute unsere Experten für maßgeschneiderte Lösungen!