Die Temperatur von Sintereisen liegt in der Regel zwischen 900°C und 1.500°C, je nach gewünschter Dichte, Materialeigenschaften und Sinterverfahren.Sintern ist ein kritischer Prozess, bei dem Eisenpulver oder -partikel unter ihren Schmelzpunkt erhitzt werden, um sie zu einer festen Struktur zu verbinden.Die genaue Temperatur wird von Faktoren wie der Materialzusammensetzung, der Partikelgröße und dem Vorhandensein von Zusatzstoffen oder Bindemitteln beeinflusst.Höhere Temperaturen führen im Allgemeinen zu dichterem und festerem Sintereisen, aber der Prozess muss sorgfältig kontrolliert werden, um Defekte wie Verzug oder übermäßiges Kornwachstum zu vermeiden.Die Sinterumgebung (z. B. Luft, Vakuum oder Inertgas) und die Abkühlgeschwindigkeit spielen ebenfalls eine wichtige Rolle bei der Bestimmung der endgültigen Eigenschaften des Sintereisens.
Die wichtigsten Punkte erklärt:
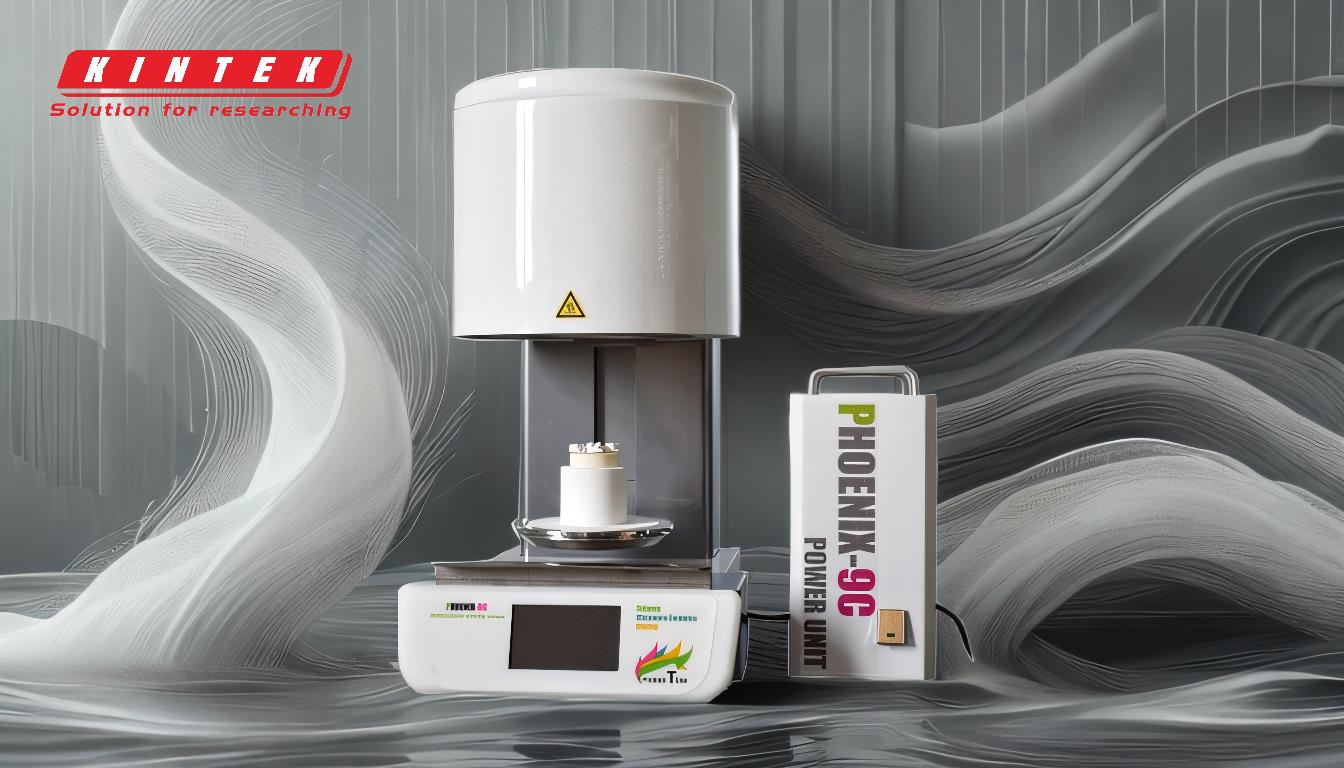
-
Temperaturbereich für Sintereisen:
- Sintereisen wird normalerweise bei Temperaturen zwischen 900°C und 1.500°C .
- Die genaue Temperatur hängt von der gewünschten Dichte, den Materialeigenschaften und dem Sinterverfahren ab.
- Höhere Temperaturen (näher an 1.500 °C) führen zu dichterem und festerem Sintereisen, da sie eine bessere Partikelbindung und geringere Porosität fördern.
-
Faktoren, die die Sintertemperatur beeinflussen:
- Materialzusammensetzung:Das Vorhandensein von Zusatzstoffen oder Bindemitteln kann die optimale Sintertemperatur verändern.
- Partikelgröße:Kleinere Partikel sintern aufgrund ihrer höheren Oberflächenenergie bei niedrigeren Temperaturen, was die Verdichtung fördert.
- Sinterumgebung:Die Atmosphäre (z. B. Luft, Vakuum oder Inertgas) beeinflusst die Sinterkinetik und die endgültigen Eigenschaften.So verhindert das Vakuumsintern beispielsweise die Oxidation und ermöglicht höhere Temperaturen.
- Aufheiz- und Abkühlraten:Kontrollierte Erwärmungs- und Abkühlungsraten sind entscheidend, um Defekte wie Verzug oder übermäßiges Kornwachstum zu vermeiden.
-
Parameter des Sinterprozesses:
- Temperatur-Rampenrate:Die Geschwindigkeit, mit der die Temperatur von 900°C auf die Sintertemperatur erhöht wird, ist entscheidend.Eine kontrollierte Anstiegsgeschwindigkeit gewährleistet eine gleichmäßige Erwärmung und minimiert die thermische Belastung.
- Haltezeit:Die Verweildauer bei der Sintertemperatur beeinflusst den Grad der Verdichtung und Bindung.
- Abkühlungsrate:Die langsame Abkühlung von der Sintertemperatur zurück auf etwa 900 °C trägt dazu bei, die gewünschte Mikrostruktur und die mechanischen Eigenschaften zu erreichen.
-
Einfluss der Sintertemperatur auf die Materialeigenschaften:
- Dichte:Höhere Sintertemperaturen führen zu dichterem Eisen, das oft nahe an der theoretischen Maximaldichte liegt.
- Festigkeit:Das Hochtemperatursintern erhöht die Zugfestigkeit, die Biegewechselfestigkeit und die Kerbschlagarbeit.
- Mikrogefüge:Die Temperatur beeinflusst die Korngröße und die Phasenumwandlungen, die sich wiederum auf die mechanischen Eigenschaften auswirken.
-
Sintertechniken und Ausrüstung:
- Ofen-Typen:Die Sinterung kann je nach Produktionsmaßstab und -anforderungen in Förderband-, Schub- oder Chargenöfen erfolgen.
- Kontrollierte Atmosphäre:Die Verwendung einer kontrollierten Atmosphäre (z. B. Vakuum oder Inertgas) ist unerlässlich, um Oxidation zu verhindern und eine gleichmäßige Sinterung zu erreichen.
- Schichtdicke und Geschwindigkeit:Beim Sintern in großem Maßstab werden die Schichtdicke (250-500 mm) und die Maschinengeschwindigkeit (1,5-4 m/min) kontrolliert, um eine gleichmäßige Sinterung zu gewährleisten.
-
Praktische Überlegungen für Sintereisen:
- Defekt-Prävention:Eine sorgfältige Kontrolle von Temperatur, Erwärmungsrate und Abkühlgeschwindigkeit ist notwendig, um Defekte wie Verzug, Risse oder übermäßiges Kornwachstum zu vermeiden.
- Optimierung:Das Sinterverfahren muss auf der Grundlage der spezifischen Anwendung und der gewünschten Eigenschaften des Sintereisens optimiert werden.
- Energie-Effizienz:Die Abstimmung von Temperatur und Prozessparametern kann die Energieeffizienz verbessern und die Produktionskosten senken.
Zusammenfassend lässt sich sagen, dass die Temperatur von Sintereisen ein kritischer Parameter ist, der sorgfältig kontrolliert werden muss, um die gewünschte Dichte, Festigkeit und Mikrostruktur zu erreichen.Der Sinterprozess umfasst eine Kombination aus Temperaturkontrolle, Atmosphärenmanagement und Prozessoptimierung, um hochwertiges Sintereisen für verschiedene industrielle Anwendungen herzustellen.
Zusammenfassende Tabelle:
Parameter | Einzelheiten |
---|---|
Temperaturbereich | 900°C bis 1.500°C |
Wichtige Einflussfaktoren | Materialzusammensetzung, Partikelgröße, Sinterumgebung, Abkühlgeschwindigkeit |
Auswirkungen auf die Eigenschaften | Höhere Temperaturen erhöhen die Dichte und Festigkeit und verringern die Porosität |
Ausrüstung zum Sintern | Bandförderer, Stoß- oder Chargenöfen mit kontrollierter Atmosphäre |
Vermeidung von Defekten | Kontrollierte Heiz-/Kühlraten und optimierte Prozessparameter |
Benötigen Sie Hilfe bei der Optimierung Ihres Sinterprozesses? Kontaktieren Sie noch heute unsere Experten für maßgeschneiderte Lösungen!