Die Temperatur zum Sintern von Keramik, insbesondere in Dentalanwendungen, liegt typischerweise zwischen 1200 °C und 1400 °C. Diese hohe Temperatur ist wichtig, um die Atomdiffusion über Partikelgrenzen hinweg zu erleichtern und es den Partikeln zu ermöglichen, miteinander zu verschmelzen, ohne den Schmelzpunkt des Materials zu erreichen. Der Prozess umfasst mehrere Phasen, darunter Pulvervorbereitung, Erhitzen, Partikelverschmelzung und Verfestigung. Bei Materialien wie Zirkonoxid liegt die Sintertemperatur oft über 1100 °C bis 1200 °C, wobei einige Öfen näher bei 1500 °C arbeiten, um die maximale Dichte zu erreichen. Die genaue Temperatur hängt von den Materialeigenschaften und dem gewünschten Ergebnis ab und gewährleistet optimale Dichte und strukturelle Integrität.
Wichtige Punkte erklärt:
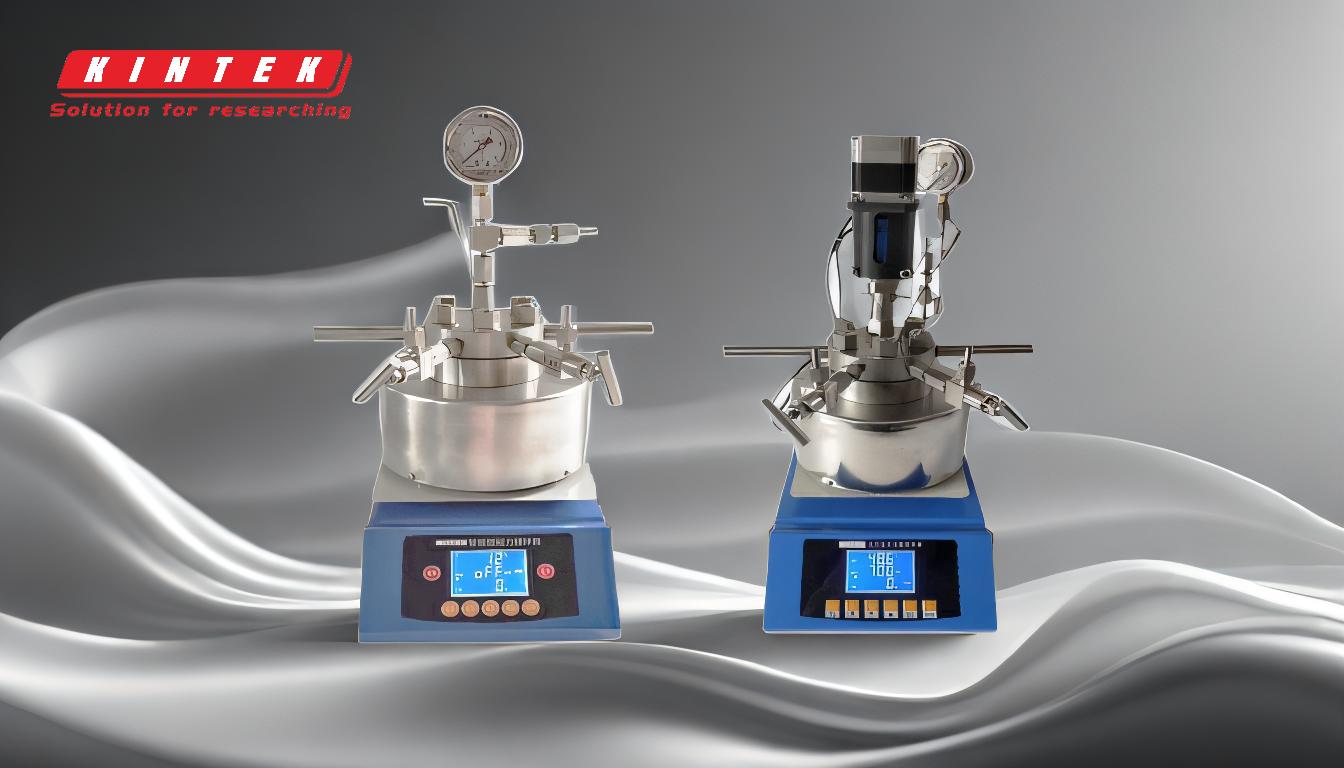
-
Temperaturbereich zum Sintern von Keramik:
- Der Sinterprozess erfordert typischerweise Temperaturen dazwischen 1200°C und 1400°C für Keramik, insbesondere im Dentalbereich.
- Dieser Bereich ist von entscheidender Bedeutung, da er die Diffusion von Atomen und die Verschmelzung von Partikeln ermöglicht, ohne dass das Material verflüssigt wird.
- Bei Zirkonoxid findet die Umwandlung von monoklinen in polytetragonale Kristallzustände statt 1100°C bis 1200°C , aber höhere Temperaturen (bis zu 1500°C ) werden häufig verwendet, um eine nahezu theoretische maximale Dichte zu erreichen.
-
Rolle der Temperatur beim Sintern:
- Die Temperatur ist ein Schlüsselfaktor beim Sintern, da sie hoch genug sein muss, um Atomdiffusion und Partikelbindung zu ermöglichen, aber unter dem Schmelzpunkt des Materials liegen muss, um eine Verflüssigung zu verhindern.
- Der Sinterofen muss eine präzise Temperaturkontrolle aufrechterhalten, um sicherzustellen, dass das Material die gewünschte Dichte und Struktureigenschaften erreicht.
-
Phasen des Sinterprozesses:
- Pulverzubereitung: Das Rohmaterial wird durch Methoden wie Kaltschweißen, 3D-Druck oder Pressen in eine kompakte Form gebracht.
- Erwärmung und Konsolidierung: Der Pressling wird bis knapp unter seinen Schmelzpunkt erhitzt, wodurch kristalline Mikrostrukturen aktiviert und die Partikelbindung eingeleitet wird.
- Partikelverschmelzung: Partikel verdichten und verschmelzen, ein Prozess, der durch Techniken wie Flüssigphasensintern (LPS) beschleunigt werden kann.
- Erstarrung: Das Material kühlt ab und verfestigt sich zu einer einheitlichen, dichten Struktur.
-
Materialspezifische Überlegungen:
- Bei Zirkonoxid ist die Sintertemperatur entscheidend für das Erreichen der gewünschten Kristallumwandlung und -dichte.
- Sinteröfen werden häufig bei höheren Temperaturen (z. B. 1500 °C) betrieben, um eine maximale Dichte zu gewährleisten, die bis zu erreichen kann 99 % des theoretischen Maximums .
-
Bedeutung einer präzisen Temperaturregelung:
- Sinteröfen müssen Temperaturen unter dem Schmelzpunkt des Materials halten, um eine Verflüssigung zu vermeiden und gleichzeitig ausreichend Wärme für die Partikelverschmelzung sicherzustellen.
- Diese Präzision ist entscheidend für die Erzielung der gewünschten mechanischen und strukturellen Eigenschaften im Endprodukt.
-
Anwendungen und Implikationen:
- In der Zahnmedizin wird Sintern zur Herstellung hochfester Keramikrestaurationen wie Kronen und Brücken eingesetzt.
- Die Möglichkeit, die Sintertemperatur zu kontrollieren, wirkt sich direkt auf die Qualität, Haltbarkeit und Leistung des Endprodukts aus.
Weitere Informationen zu Sinteröfen finden Sie in diesem ausführlichen Ratgeber: Sinterofen .
Übersichtstabelle:
Aspekt | Einzelheiten |
---|---|
Temperaturbereich | 1200°C–1400°C (bis zu 1500°C für Zirkonoxid) |
Schlüsselrolle der Temperatur | Ermöglicht Atomdiffusion und Partikelbindung ohne Verflüssigung |
Stadien des Sinterns | Pulveraufbereitung, Erhitzen, Partikelverschmelzung, Verfestigung |
Materialspezifische Faktoren | Zirkonoxid benötigt für die Kristallumwandlung 1100–1200 °C |
Präzision ist wichtig | Gewährleistet optimale Dichte, strukturelle Integrität und mechanische Eigenschaften |
Anwendungen | Zahnrestaurationen (Kronen, Brücken) und hochfeste Keramikkomponenten |
Benötigen Sie präzise Sinterlösungen für Ihre Keramik? Kontaktieren Sie noch heute unsere Experten um mehr zu erfahren!