Die Dicke dünner Schichten, die durch physikalische Gasphasenabscheidung (PVD) hergestellt werden, liegt in der Regel zwischen 0,00004 und 0,0002 Zoll (etwa 1 bis 5 Mikrometer).Diese Dicke wird von verschiedenen Faktoren beeinflusst, darunter die Abscheidungsmethode (z. B. Sputtern oder Aufdampfen), Prozessparameter wie Zykluszeit, angewandte Leistung und Materialeigenschaften.PVD ist eine vielseitige vakuumbasierte Abscheidungstechnik, mit der dünne Schichten auf Substraten wie Metallen, Keramik, Glas und Polymeren erzeugt werden können.Bei diesem Verfahren werden die Materialien von einer kondensierten Phase in eine Dampfphase und dann wieder in eine kondensierte Dünnschichtphase überführt.Um die gewünschte Dicke und Qualität zu erreichen, müssen Faktoren wie Abscheidetemperatur, Substratvorbereitung und Vakuumbedingungen genau gesteuert werden.
Die wichtigsten Punkte werden erklärt:
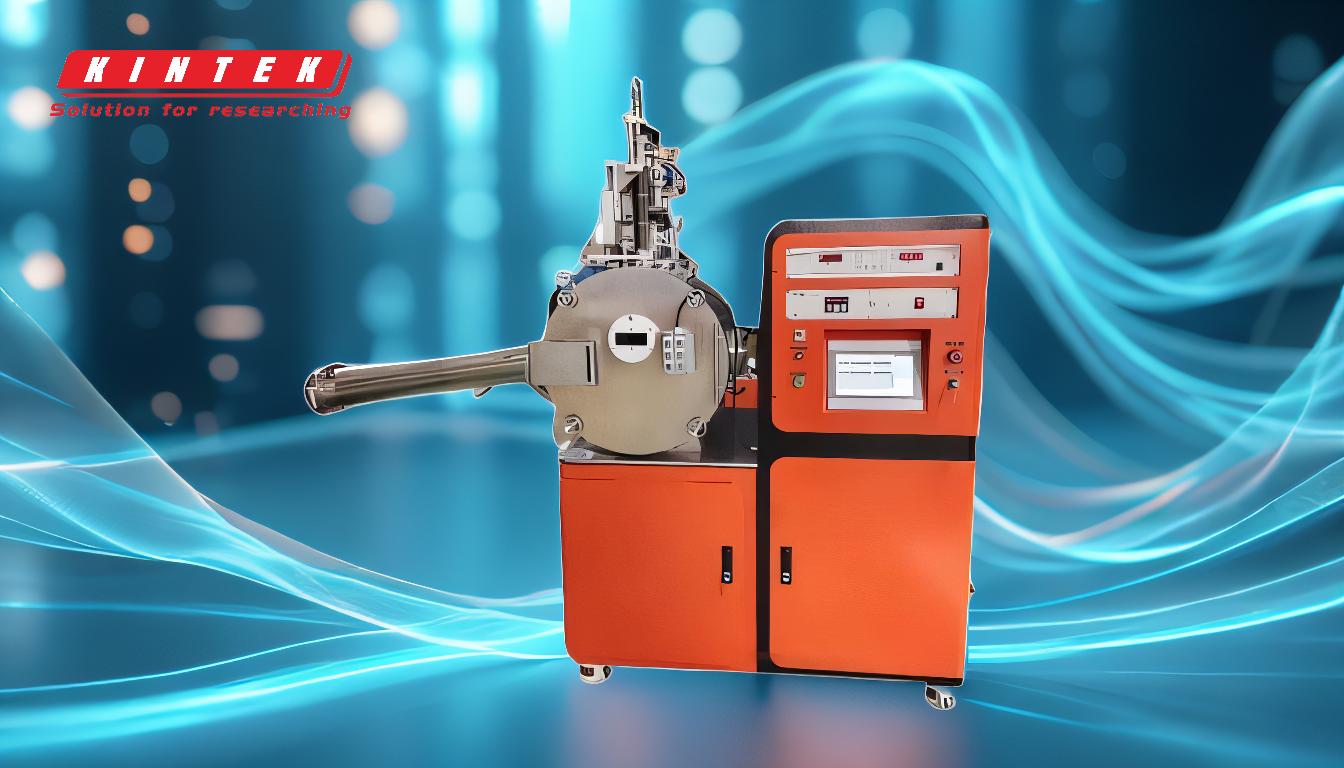
-
Typischer Dickenbereich von PVD-Beschichtungen:
- PVD-Beschichtungen haben im Allgemeinen eine Dicke von 0,00004 bis 0,0002 Zoll (ungefähr 1 bis 5 Mikrometer ).
- Dieser Bereich ist für Anwendungen geeignet, die enge Toleranzen und minimale Materialanhäufung.
- Die dünne Beschaffenheit von PVD-Beschichtungen stellt sicher, dass die Oberflächenbeschaffenheit des Substrats genau nachgebildet wird.
-
Faktoren, die die Dicke beeinflussen:
- Ablagerungsmethode:Die beiden gängigsten PVD-Verfahren, Sputtern und Verdampfung können je nach ihren spezifischen Prozessparametern unterschiedliche Dicken erzeugen.
- Zykluszeit:Längere Sputter- oder Verdampfungszyklen führen zu dickeren Schichten.
- Angewandte Leistung:Höhere Leistungen während des Sputterns erhöhen die Energie der Beschichtungspartikel, was zu einer schnelleren Abscheidung und potenziell dickeren Schichten führt.
- Materialeigenschaften:Die Masse und das Energieniveau der Beschichtungspartikel (von einigen zehn bis zu Tausenden von Elektronenvolt) wirken sich auf die Abscheiderate und die Enddicke aus.
- Vorbereitung des Substrats:Eine ordnungsgemäße Reinigung und Oberflächenbehandlung des Substrats gewährleistet eine gleichmäßige Abscheidung und gleichbleibende Dicke.
-
Prozessparameter und ihre Auswirkungen:
- Temperatur:PVD-Prozesse arbeiten normalerweise in einem Temperaturbereich von 320 bis 900 Grad Fahrenheit .Höhere Temperaturen können die Haftung und Gleichmäßigkeit verbessern, aber auch die Enddicke beeinflussen.
- Vakuum-Bedingungen:Die Restgaszusammensetzung und der Druck in der Vakuumkammer beeinflussen die Abscheiderate und die Schichtqualität.
- Sichtlinie:PVD ist eine Sichtlinie Verfahren, d. h. das Beschichtungsmaterial bewegt sich in einer geraden Linie von der Quelle zum Substrat.Diese Eigenschaft erfordert eine sorgfältige Positionierung des Substrats, um eine gleichmäßige Schichtdicke zu erreichen.
-
Vorteile von PVD für die Dünnschichtabscheidung:
- Umweltschonend:PVD-Verfahren kommen ohne schädliche Chemikalien aus, was sie zu einer nachhaltigen Wahl für die Dünnschichtproduktion macht.
- Hohe Reinheit:Die Vakuumumgebung gewährleistet, dass die Beschichtungen frei von Verunreinigungen sind, was zu hochreinen dünnen Schichten führt.
- Verbesserte Oberflächenqualität:PVD-Beschichtungen verbessern die Oberflächeneigenschaften von Substraten, einschließlich Härte, Verschleißfestigkeit und Korrosionsbeständigkeit.
-
Anwendungen von PVD-Dünnschichten:
- Industrielle Beschichtungen:PVD wird häufig zur Beschichtung von Werkzeugen, Formen und Bauteilen verwendet, um die Haltbarkeit und Leistung zu verbessern.
- Dekorative Beschichtungen:Die Fähigkeit, Oberflächenbeschaffenheiten nachzubilden, macht PVD ideal für dekorative Anwendungen auf Schmuck, Uhren und architektonischen Elementen.
- Elektronik:Durch PVD hergestellte Dünnschichten werden aufgrund ihrer präzisen Dickenkontrolle und hohen Qualität in Halbleitern, Solarzellen und optischen Geräten eingesetzt.
-
Vergleich mit anderen Abscheidetechniken:
- PVD bietet bessere Kontrolle über die Dicke im Vergleich zu einigen anderen Beschichtungsmethoden, wie z. B. der chemischen Gasphasenabscheidung (CVD), die zu dickeren und weniger gleichmäßigen Schichten führen kann.
- Anders als CVD erfordert PVD keine Wärmebehandlung nach der Abscheidung, wodurch der Prozess vereinfacht und die Produktionszeit verkürzt wird.
Wenn ein Einkäufer oder Ingenieur diese wichtigen Punkte kennt, kann er fundierte Entscheidungen über den Einsatz von PVD für bestimmte Anwendungen treffen und so optimale Leistung und Kosteneffizienz gewährleisten.
Zusammenfassende Tabelle:
Aspekt | Einzelheiten |
---|---|
Dickenbereich | 0,00004 bis 0,0002 Zoll (1 bis 5 Mikrometer) |
Abscheidungsmethoden | Sputtern, Verdampfen |
Wichtige Einflussfaktoren | Zykluszeit, angewandte Leistung, Materialeigenschaften, Substratvorbereitung |
Temperaturbereich | 320 bis 900 Grad Fahrenheit |
Anwendungen | Industrielle Beschichtungen, dekorative Veredelungen, Elektronik |
Vorteile | Umweltfreundlich, hohe Reinheit, verbesserte Oberflächenqualität |
Erzielen Sie präzise Dünnfilmbeschichtungen mit PVD- Kontaktieren Sie noch heute unsere Experten für maßgeschneiderte Lösungen!